Don’t Just Connect Your Plant—You Need to Model It, Experts Say
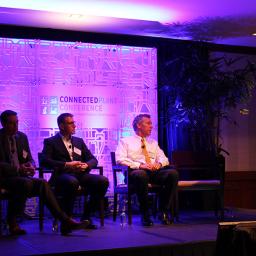
Remote and online monitoring of plant performance parameters is an important step toward a fully connected plant, but alone it's not enough to exploit the real value in the Industrial Internet of Things, speakers at POWER's inaugural Connected Plant Conference on February 15 in Dallas said.
Randy Bickford, president and CTO of software firm Expert Microsystems said modeling expected performance parameters is key. "The most accurate expected values give you the earliest and most accurate predictions of potential problems," he said. Without a good model, it's much harder to use plant data effectively. One problem with relying directly on sensor data is that many problems can display the same symptoms, making it hard to tell what's really going on. "With that model, you know when and where problems will occur."
Stefan Bungart, global head of digitalization, power generation services for Siemens Energy, noted that utilities that have embraced the possibilities of digitization have seen returns across their entire operations, from generation and distribution to trading, retail, and even headquarters overhead. Digitization can improve plant security, network security, and system integrity, he noted.
Clinton Carter, director of advanced monitoring and diagnostic services for Luminant Energy, described the firm's experience with its Performance Operations Center (POC), which monitors a comprehensive array of performance data across its fleet. Luminant saw returns on its investment immediately, as POC staff were able to spot a failing ventilation fan and direct plant workers to preventative maintenance that avoided an outage.
"On day one, we avoided a 48-hour derate that would have cost us $589,000," he said.
On another occasion, POC staff spotted elevated temperatures at a transformer as a result of a failing cooling system. Absent intervention, a catastrophic failure could have resulted in millions of dollars in damages.
Andrew Johnson, supervisor of Salt River Project's (SRP's) Performance Monitoring Center (PMC) in Arizona, reported similar benefits from the cooperative's embrace of advanced predictive analytics. The project began with one combined cycle plant in 2005, and SRP has since rolled it out across its entire fleet, expanding the range of data it gathers over time. The PMC is staffed by a crew of experienced plant supervisors who are able to give expert remote advice to plant workers. The results have more than justified the substantial investment.
"In 2016, the PMC managed 318 saves," Johnson said.
SRP plans to expand the PMC's capabilities through additional advanced modeling of performance and vibrational data.
-Thomas W. Overton, JD is a POWER associate editor (@thomas_overton, @POWERmagazine).
The post Don't Just Connect Your Plant-You Need to Model It, Experts Say appeared first on POWER Magazine.