3-D Printed Gas Turbine Technology Marks ‘Game Changing’ Milestone
The world's first 3-D printed burner for an industrial gas turbine has been in operation for one year with no reported issues.
Siemens, which installed the burner for the 32.8-MW SGT-7000 gas turbine at E.ON's combined cycle power plant in Philippsthal in the German state of Hessen said on September 19 that it has been operating for more than 8,000 hours, and that "the results are impressive."
Three-dimensional printing-also called "additive manufacturing"-for power plant components is a process that builds parts layer-by-layer from sliced computer-aided design models to form solid objects. Siemens, which has researched additive manufacturing processes since 1989, says the technology could revolutionize the development and production of components.
"For example, it can be difficult for conventional manufacturing technologies to produce more efficient or low-emission turbines with higher temperature tolerances," it said. "3-D printing now makes it possible to produce almost any structure imaginable. The process allows turbine components like gas turbine blades and vanes to be cooled through complex internal ducts, which improves their efficiency."
(For more, see "3-D Printing: The Future of Manufacturing and Maintenance" in POWER's May 2017 issue.)
Siemens began investing in metal 3-D printing in 2008 and developed a technology specifically for power generation. In 2012, the company installed the first EOS M280 SLM printer and adapted it for burner repairs. In 2013, the first 3-D-printed burner tips and swirlers were installed in commercial gas turbines, and in 2016, Siemens acquired Materials Solutions in the UK, a leading company in the field of additive manufacturing.
In 2017, the company produced the first burners using selective laser melting technology under its intelligent burner manufacturing (IBUMA) program in Finsping, Sweden. "Each burner head is manufactured in one piece compared to traditional methods that required 13 individual parts and 18 welds," Siemens noted. "Design improvements, such as the pilot-gas feed being part of the burner head instead of the outside fuel pipe, allow the operating temperature to be kept lower, thus contributing to a longer operational lifespan of the components and, ultimately, the gas turbines," it said.
Last year, Siemens' 3-D-Experts also designed and printed the world's first gas turbine blades and validated them under full-load engine conditions, at 13,000 revolutions per minute and temperatures beyond 1,250C.
"As an energy service provider, precision and consistency are an absolute requirement for us," said Niklas Lange, project manager at E.ON Energy Projects. "Additive manufacturing not only delivers this, but in our experience it can even improve performance compared with older models."
For Siemens, the achievement's significance cannot be underscored enough. "These early results from the IBUMA burner with E.ON validate our belief that this technology is a game-changer. We appreciate E.ON's active participation and commitment to driving innovation and look forward to our continued close collaboration," said Vladimir Navrotsky, chief technology officer for Siemens Power Generation Services, Distributed Generation.
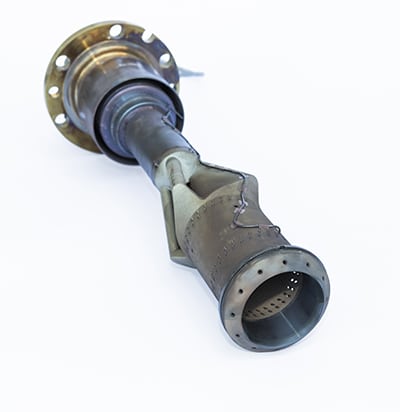
Pictured is Siemens' 3-D printed gas burner for the SGT-700 gas turbine operating at E.ON's combined cycle power plant in Philippsthal, Germany. Courtesy: Siemens
To keep its installed base competitive, GE Power is also investing in additive manufacturing. In July, the company unveiled the first upgrade with additive manufactured components for GT13E2 gas turbines. The new MXL2 with additive manufactured performance (AMP) upgrade "could not be manufactured with conventional methods and marks the first-of-its-kind solution with the injection of components manufactured by additive technologies," said Scott Strazik, president and CEO of GE's Power Services business. GE said the new technology can help gas plant power producers save up to $2 million in fuel annually, and open up additional revenues of up to $3 million annually in new power capacity.
The MXL2 with AMP includes two components produced by GE's Additive Manufacturing Works teams in Birr, Switzerland, and Greenville, South Carolina: the first-stage turbine vanes and heat shields. The technology promises to elevate the output and efficiency of existing GT13E2 gas turbines by reducing component cooling requirements by up to 25% and increasing output up to 21 MW in combined cycle configuration (which comes out to an efficiency improvement of up to 1.6% in combined cycle configuration), GE said.
GE's upgrade will be demonstrated by Vattenfall Europe Wirme AG at its Heizkraftwerk Berlin-Mitte power plant in Berlin, Germany. Vattenfall installed four different 3-D printed components at the plant in 2015.
-Sonal Patel is a POWER associate editor (@sonalcpatel, @POWERmagazine)
The post 3-D Printed Gas Turbine Technology Marks 'Game Changing' Milestone appeared first on POWER Magazine.