The POWER Interview: What Drove the Gas Turbine Technology Leap at GE Over the Past 70 Years
On July 29, 1949, at 2:15 p.m., General Electric's (GE's) first gas turbine at the Belle Isle Station in Oklahoma City began delivering power to Oklahoma Gas and Electric Co.'s distribution system. The 3.5-MW GE Frame 3 machine reportedly had an efficiency of about 17%.
Since the Belle Isle machine (Figure 1) started up seventy years ago, gas power technology has seen a leap in capability, and that can be attributed to several factors. In an exclusive interview with POWER recently, GE Power Chief Technology Officer John Lammas, who is also vice president of Generation Technology, noted GE's machines are pushing toward an efficiency of 64% today, and he outlined what has prompted the evolution.
Among GE Power's many notable developments are leaps in materials and tools, engineering and manufacturing, and cross-cutting knowledge and technology the division shares with GE's Aviation business, as well as Alstom, a company-now owned by GE-that developed a distinct line of gas power technology. New digital capabilities and recent breakthroughs continue to fuel GE Power's technology future, and more developments are forthcoming in the company's aeroderivative and heavy-duty gas turbine lines, he said.
[For an interactive look at the history of GE's gas turbine technology, see, "A Brief History of GE Gas Turbines."]
POWER: How long have you been involved with the gas turbine industry?
John Lammas, GE Power CTO: I actually started straight out of high school with Rolls-Royce Aviation in the UK. So, I started working straight out of high school as an apprentice on gas turbine engines-that would have been in 1978. I was an undergraduate apprentice with them, got a degree in engineering in the UK, and then I joined GE aircraft engines in 1985, worked on many of the engines, including the GE90. I moved to what was GE Energy at the time in 2005 as the chief engineer for GE Energy. And basically, I've worked my whole career in gas turbines-aviation gas turbines, industrial gas turbines.
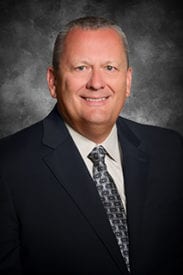
John Lammas, GE Power CTO
POWER: Throughout the long history of gas turbines, there have been many improvements. Is there one specific development that you would highlight as pivotal?
Lammas: Well, if you go back far enough, the gas turbine was originally designed in the Second World War, and it came to fruition in the Second World War as an aviation application. GE was the developer of the jet engine in the U.S. So, that was one of the pivotal times. Another, obviously, is the Belle Isle machine. For the original application, it was derived from a jet engine, and it was going to be used in transportation-it was actually going to be used in a train. And the next extension of that was to use it for power generation. The Belle Isle machine was a 3-MW machine that went into service in 1949-70 years ago. Using a gas turbine for power generation is certainly one of those pivotal moments.
You know, obviously, those machines were relatively inefficient at the time. I think the application of combined cycle, where we started to regain the lost energy-energy from the exhaust-and create steam. The first application of that for GE was in 1967. I think that was another pivotal moment.
The applications of some of the other aviation machines, such as the CF6, where we generated the LM2500, and again, that initially went into transportation applications, powering ships. But shortly afterward, in 1969, that became, again, a power generation application of an aircraft machine directly to power generation.
Those are the early ones. Another one, I think, is the F-class machine. The F-class was really one of GE's developments-and that was taking the existing machines, and looking at them, and knowing there was a need for a larger, more-efficient machine. And I think that's happened more than a couple of times in our history. The first F-class machines went into service in the early 1980s.
The first F-class went into service in 1990, but they went into service prior to that. The larger, higher-efficiency machines were certainly a step, and that certainly created a whole generation of new machines. I would also say, even though the original steam-cooled H machine from GE was a development, again, taking the firing temperature up to 2,600-plus. And that really in itself started a new generation of machines, which we successfully followed up with our HA-class machines in the last few years.
So, you know, I think there are certain steps in it, and I think early on its the derivation of machines from aircraft technology to industrial use, the development of combined cycle, then the successive development of the F-class and the H-class machines.
POWER: How did the H-class evolve?
Lammas: The development of the steam-cooled machine was actually in the late 1990s. The first of those went into service with Baglan Bay, which was our original 9H, and that was in 2003. We were the first to bring steam-cooling to industrial gas turbines, and some of our competitors followed with steam-cooling as well. But during that time, the development of air-cooling certainly advanced to the point that we could achieve the same sorts of firing temperatures with air-cooled machines that we didn't need steam cooling. And that's where the HA-the air-cooled Hs-were developed. But I think without the original H machines, the whole later class of HAs, really were a result of a move to these larger, more-efficient machines. [It was] a very similar step from the E-class to the F-class, as from the F- to the H-class.
POWER: Along with gas turbine technology, GE has been at the forefront for gas power pollution solutions. How did that suite of technologies evolve?
Lammas: There's been a series of new developments. I think the development of dry-low-NOx [DLN] combustion that was incorporated into our F-class machines was certainly one of the big steps in combustion technologies, allowing us to fire at higher temperatures with low emissions. That was certainly one of the big steps, the development of DLN combustion systems. Since then, we've incorporated additional features and continued to develop the DLN systems. On our HAs, we do what we call axial fuel staging, which is sort of a two-stage combustion system. And then if you go beyond that, we've now developed the next generation of combustion systems that are going to be in the 9HA.08. We call that internally the micro-mixer. So successively, we've developed lower-NOx systems. And also, these systems give us the ability to burn hydrogen at high percentages, which, with the future, the potential use of hydrogen in our machines can be a big advantage.
POWER: Many of these developments have been driven by market needs. In the 1950s, for example, gas turbines were mostly used for peaking duty, and after the Northeast blackout of 1965, black start became an important feature. What kind of market drivers is GE looking at today as it develops new gas turbine technology? What does the market want?
Lammas: Yes, market needs have definitely driven the developments that we've made. A year ago, we announced an LM6000, where we've incorporated batteries into it. And there, it was that as soon as there is a need on the grid, you can actually deliver power from the batteries and it then transitions into the gas turbine itself. So, there's an example of where we're bringing battery technology together with our aeroderivative technology to give that instant response that is now being demanded in places like California.
[In] all of our machines, we see the need for additional flexibility. This can be with respect to the ability to start the machines and get power on the grid, and also with things like fuel and variation in fuel. We had a great demonstration recently. We've put one of our HAs into a smelting facility. There was a machine that went out, and we showed our machine could drop basically from 120 MW to 0 and back to 120 MW-and we did that in 12 seconds, and that was actually demonstrated. So, the ability to have these machines working with grids that are potentially becoming a little more unstable based on the penetration of renewables is, I think, something that we're really seeing.
But if you look at the future, high efficiency is obviously always going to be a driver. We want these machines to be extremely reliable, obviously. How they fit in with future power-the penetration of solar and wind-is very important. We see, around the world, demands for different fuels as well. And having the capability to use a wide variety of fuels in our machines is becoming an increasingly important thing. But we see gas as being very complementary to the future mix of energy sources. And having a machine that is complementary is one of those things we're really looking at.
POWER: GE acquired Alstom's power business in 2015, but both companies have long legacies of technology development. How are you blending the two cultures-the two distinct technology families-in research and development today?
Lammas: You know, this has been an interesting exercise over the last few years since the acquisition of Alstom. We obviously looked at the portfolio of generators, steam turbines, and gas turbines, and I think in different areas, there are slightly different approaches. We obviously looked at the portfolio of gas turbines, and there were some gas turbines like the [GT13E2], which fit very well where there was a gap in the portfolio. If you look at the other machines, such as the 24 and 26, we're not going to continue producing new machines in those categories. But we're now looking at how do we use technology from the GE portfolio, and particularly from the HA portfolio, to improve those machines.
Relatively recently, in the last few months, we announced a major upgrade to the GT26, which is called the GT26 high efficiency (GT26 HE), where we've taken compressor technology and upgraded the compressor, and then heat, cooling, and materials technology into the turbine. And that's been a major improvement in both efficiency and output for that machine. So, there's an example where we're bringing the HA technology into a legacy machine.
On steam turbines, we've taken a somewhat different approach in that we've got technologies from GE and a whole family of last-stage blades, and technology in sealing, and different features to eliminate or to reduce costs, and we've brought the best of both together into a sort of hybrid family of steam turbines going forward. On the generator side, we compared products and asked: 'Which products are the best fit?' And we rationalized the portfolio in that way.
But what is really interesting is when you look at the design standards, the design practices that are used across the business. A lot of those are developed based on experience and knowledge, and we're looking at them very critically and bringing them together into one set of design rules for future products. And in some cases, you can find that maybe, based on history, there are different ways of looking at issues-and that enables us potentially to make a better family of future engines. So, as we move forward, we're really consolidating our design practices across the board, and they will be the ones that will be applied in the future, bringing the best technology from both companies.
POWER: GE in 2017 introduced a 65-MW aeroderivative gas turbine (the LM9000). Are you looking to continue to increase the capacity of these machines? What are you doing in terms of aeroderivative gas turbine development?
Lammas: This is actually interesting, having actually worked in the aviation business on some of these machines and then coming to the power business, I've worked on them in both places. We have a family of machines-the LM2500 and LM6000-that are really derived from the CF6 family of engines, and we continue to develop those. There's what's called the LM6000-PF+, which is the latest of the 6000s that we're currently working on, that will be a product we're shipping to our customers later this year. We are developing improved power turbines to go on the LM2500 machine. So again, continued development of that machine.
And currently our Aviation business is working on an aeroderivative version of the [1995-debuted] G90, which would be the next generation of aviation machines that are brought to the power generation business. So, we continue across the portfolio there. Largely, we benefit from the fact that the volume and production in Aviation can bring the cost of the product down through volume to a point where it is really a better fit in the power generation business. There's usually a lag between a new aviation machine being developed for an application in the power generation space.
POWER: Over the course of history, which specific technology developments do you think have been the most integral to the translation of technology from aviation to power generation?
Lammas: Fundamentally, I share a team between myself and Aviation that developed the aerodynamic tools, the heat transfer tools that we use across the full folio. So, " I think those tools are really applicable to both businesses directly. If you think about how you make gas turbines more efficient, it comes from component efficiencies-which is really aerodynamics. Over the years, we've run multiple aerodynamic tests that we've put and incorporated those lessons into our tools, which we now apply in both businesses.
[Also], the development of better materials. Obviously, continually, we want to run combustion and turbines hotter, and the development of materials tends to be led by our Aviation business. And then those materials become widely used in our power business. But there's also been examples where we've worked on materials that are now going into Aviation.
A good example of that is ceramic matrix composite, which we actually produce parts and run in industrial machines, and now those materials are going into production machines like the LEAP-X [a 2008-launched revolutionary turbofan engine concept] where they're using that machine for their trials. And Aviation actually uses some of the work and the experience we developed in the power industry to apply those materials into Aviation. We believe in the future, if the use of those materials increases, potentially the price of those materials drops, they will be sort of the next generation of materials that we'll be bringing back to the power industry. So, there's a lot of backwards and forwards, and a lot of sharing of common heat transfer, aerodynamics, materials technology between us.
Recently, we could add additive [manufacturing] to that as well. Obviously, smaller parts, additive, and the desire to drop weight makes them very applicable to Aviation, but we're also starting to see more use of them within our power generation machines, another area we work closely together on.
POWER: Since the first power generating gas turbine was put online 80 years ago, engineering and manufacturing have evolved dramatically. What changes do you think have been the most notable?
Lammas: Obviously, my career extends back long enough that when I started working on a drawing board as a gas turbine designer-and that really wasn't that long ago, it certainly wasn't 1939-but if you look at the engineering side, we started 2D calculations, and if you go into the late 1970s and early 1980s, the use of finite element methods started to be developed. Certainly, structurally, they were applied first. We went from 2D to 3D analytical methods that allowed us to design the development of computational fluid dynamics [CFD] and the application of that initially to aerodynamics and now to combustion. The ability to go from unsteady calculations in CFD in combustion, the ability to model the machine and enhance making it has just come leaps and bounds.
I think if you look at the manufacturing side, a lot of it is around the development of materials themselves, the ability to do investment cast, the development of single-crystal materials, where we actually grow turbine airfoils and we eliminate ground boundaries. So, all of those manufacturing techniques are really changing the game for us with respect to the capability.
Obviously, the latest revolution that's really only started up upon us is the incorporation of additive. One thing I would say as well is, going back to the previous comment, that a lot of movement in GE particularly between Aviation and Power, with respect to people. And I think that is another way that we've brought aviation technology to power and power to aviation as well.
We have a gentleman, Don Brandt, who used to be in my position at GE probably 25 years ago. He's retired-in his late 80s now. He was the father of the F-class machine. We brought him back, and we showed him the HA machine here in the factory. He's looking at it-at a machine that has twice the output in megawatts of machines he was working on. And when you think about it, from his machine to the one now, with 10% better in combined cycle efficiency. The machines he worked on were maybe 52% to 53%, and our latest machine that we're starting to test today-which is the one he came to see-it will exceed 64% efficiency. So, if you think of that from one generation to the next, the changes have just been incredible. The firing temperatures have gone up, probably in his day from 2,300F to 2,400F to exceeding 2,800F now, so, 500 degrees. So, for him to come and stand there and look at the machine, he was in awe. And that's just from one generation to the next.
-Sonal Patel is a POWER senior associate editor (@sonalcpatel, @POWERmagazine)
The post The POWER Interview: What Drove the Gas Turbine Technology Leap at GE Over the Past 70 Years appeared first on POWER Magazine.