The Consumer Electronics Hall of Fame: Epson Stylus Color
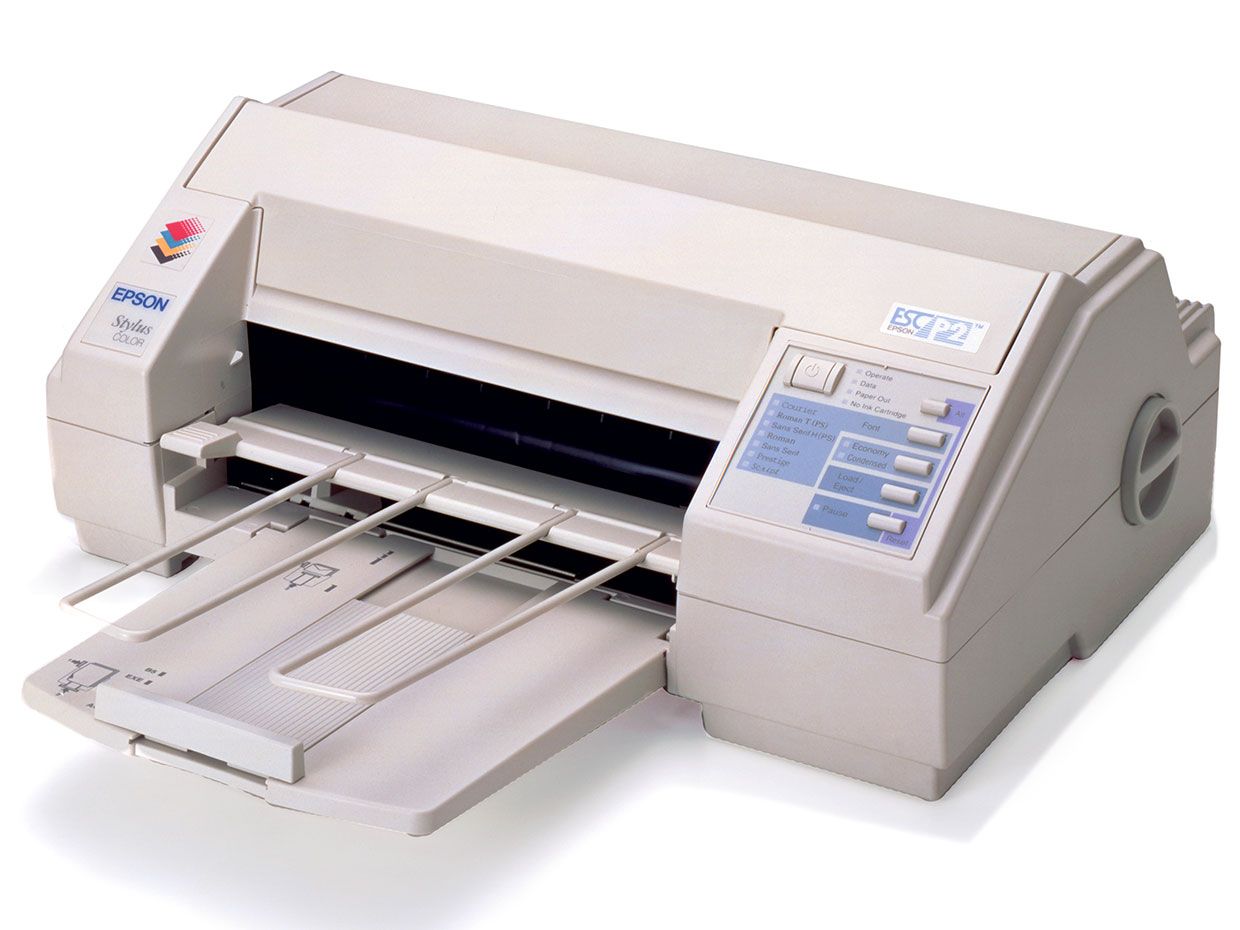

In technology, as in life, timing is everything. Case in point: Epson's Stylus Color, the world's first high-resolution color inkjet printer, a dazzling innovation that came along in 1994, at precisely the time it was needed. Digital cameras were starting to eclipse film, and millions of consumers were accumulating digital photographs, which they wanted to print at home.
The first inkjet patent was awarded in 1951, but it took three decades to improve the technology sufficiently to merit mass-market adoption. Manufacturers persisted for so long because they knew if the approach could be perfected, it held the promise of much more accurate printing. The perpetual problem was applying ink with precision. For a long time, it was a challenge to print anything that wouldn't immediately splotch and smear.
Seiko Epson has a good pedigree in the printer market. It had produced an early electronic printer in 1964, and introduced what was considered the first small digital printer, the EP-101, in 1968. At the time, the company was a Seiko subsidiary known as Shinshu Seiki. In the 1970s it started branding its printers with the Epson label, and then adopted the name as its corporate moniker in 1982. It sold mostly dot-matrix printers through the 1970s and early 1980s.
In 1984, Hewlett-Packard introduced the first inkjet printer, the ThinkJet, beating Epson to the market by a few months. Epson's response was the SQ-2000. Both were black-and-white printers.
The breakthrough for Epson was something it called Micro Piezo technology. In the mid-1980s, Epson was developing a novel printhead. It had a few dozen tiny reservoirs, each filled with black ink (later versions would add more reservoirs, for colored inks). Each reservoir had a minuscule nozzle with a valve. A plate capped each reservoir. The idea was to push on the plates, deforming them so that they pressed into the reservoirs. Well-controlled pressure squeezed microscopic drops of ink out of the nozzles and onto the paper.
What Epson needed was a precise means to push on the plates. It's not clear if Epson had the idea from the start to use piezoelectric elements with this printhead-the company told IEEE Spectrum no one associated with the development of its early inkjet printers still worked there. But there is no question that engineers in Epson's printer division were familiar with the technology.
To cut to the chase, at some point Epson engineers decided to use piezoelectric materials in the printheads as the squeezing mechanism. They put a piezoelectric crystal on the back of every plate capping each ink reservoir in the printhead they were developing. When voltage was applied to any individual crystal, it contracted, deforming the plate and pushing out a tiny amount of ink. Precise control of the voltage led to precise control of the deformations, in turn providing unprecedented control of the amount of ink Epson was able to emit for each dot.
That level of control led to another great advantage for Epson.
Other printers minimized smearing and blotting by using inks that had been formulated to be thicker than inks used in other types of printers. These inks were less viscous when cold but would flow well when heated. So the common approach was to use these inks in combination with a head that incorporated a heating element. The downside was that heating gradually degraded the printheads, meaning they would have to be replaced periodically.
A benefit of Epson's new printhead was that it could use almost any ink, including less expensive inks that were more viscous at room temperature. This was possible because the high degree of control meant that ink could be dispensed so sparingly that there wasn't enough of it to be smeared on the paper. Because Epson could use inks that did not need to be warmed, it could forgo having a heating element in its printheads. Epson's heads weren't subject to thermal degradation, and therefore lasted a long time.
That meant Epson could build a printer in which the printhead was permanent. The only thing that would need to be replaced would be the ink wells. The wells, or cartridges, could be simple, easy to produce, easy to replace, and cheap.
Epson's first printer with the Micro Piezo technology was the Stylus 800 (the MJ-500 in Japan), introduced in 1993. The Stylus 800 had 48 nozzles in a 4-by-12 configuration, and could print 360 dots per square inch (dpi).
The following year, Epson released its Stylus Color (P860A). The Micro Piezo technology printhead was refined for the Stylus Color; this one had 64 nozzles in a 16-by-4 configuration. It had a palette of 16 million colors. Epson had also developed new inks that dried very quickly, contributing to better printing control and better prints.
Photographs printed on the Stylus 800, with its 360 dpi, had decent resolution. But photos printed on the Stylus Color, which printed at 720 dpi, were obviously superior to anything any competing printer could produce.
Epson also boasted about a means of controlling the printhead precisely enough to almost eliminate a common problem with printers of the time, which was traces of ink, called horizontal banding, between lines of text. And to top it all off, the Stylus Color printed faster than other printers. Between the speed and the more economical inks, it was also considerably less costly to own and operate.
Bundled with drivers for both Windows and Macintosh computers, the Stylus Color was an immediate and major success. Epson said it sold some 300,000 units in Japan, where it carried the model number MJ-700V2C, a record then for a printer. The company says it had similar success in other markets around the world.
The beauty of inkjet printers is that their key component, the ink cartridge, is easy to produce and to work with. For that reason and others, inkjets are relatively inexpensive-roughly one-half the price of laser printers, the next most popular type today. The low price and high quality of the printing combine to make inkjets the best-selling type of printer to this day. Epson remains a significant force in the market with its still-unique Micro Piezo technology, which it has continued to refine. The company claims it can now apply droplets as small as 1.5 picoliters-a trillionth of a liter.
Back to Consumer Electronics Hall of Fame >> < Back to Consumer Electronics Hall of Fame