The POWER Interview: Eaton Targets Skilled Labor Shortage With Hands-on Training
The post The POWER Interview: Eaton Targets Skilled Labor Shortage With Hands-on Training appeared first on POWER Magazine.
POWER in 2018 reported on the lasting impact that a dip in training programs has had on the utility workforce. In the 1980s, there were fewer training programs and the impact is still being felt today. There are fewer utility workers able to move into middle- and upper-management positions, contributing to a workforce gap as the large number of Baby Boomers retire.
Power management company Eaton recently announced a three-pronged investment in education, workforce training, and industry programs to help address this issue. To learn more, we recently spoke with Dan Carnovale, manager of the Eaton Experience Center in Pittsburgh.
POWER: Could you give a brief overview of your role at Eaton and the company's involvement across the power generation industry?
Carnovale: Electrical power is central to making our homes, businesses and infrastructure work and Eaton is a global power management company that helps our customers, including utilities, modernize the electric grid to support these needs. We provide the automation and control solutions, equipment and turnkey services expertise that is necessary for power generating facilities-no matter what energy resource they're tapping.
Education and training are also a part of Eaton's core values. To help our customers, we continue to invest in industry education, preparing a larger workforce to build and maintain electrical infrastructure.
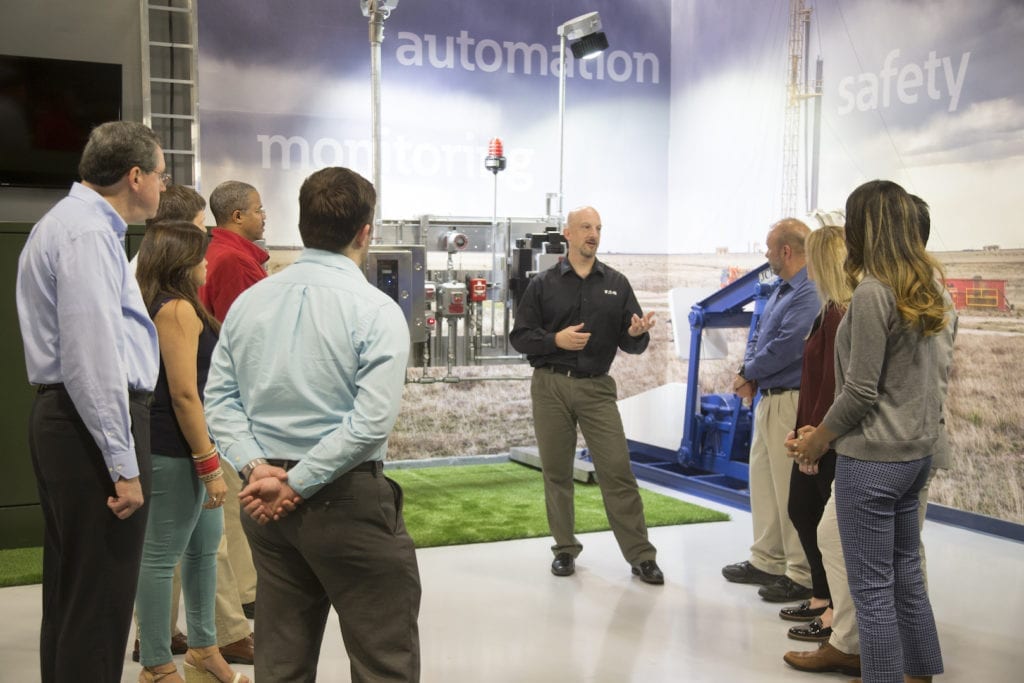
Eaton investments in industry training programs for the current and next generation workforce start at its Experience Centers in Pittsburgh and Houston, where Eaton provides training and certification programs in a hands-on lab environment designed for power industry professionals. Courtesy: Eaton Corp.
We have two Eaton Experience Centers within the U.S. I manage the Power Systems Experience Center in Pittsburgh, Pennsylvania, which is like a playground for the electrical industry. We provide a hands-on training environment at our Experience Centers (here in Pittsburgh and in Houston, Texas) in a full-scale demonstration and testing facility and help demystify the design, technology and installation practices of the power industry. For example, we provide:
- Live demonstrations of a full-scale microgrid system, showing how we're able to maintain power even if the local utility power is out.
- Interactive power quality courses, where we can both create and mitigate power quality problems for demonstration and testing purposes.
- Training on the latest arc flash safety guidelines and solutions.
More than 7,000 people come through our Experience Center in Pittsburgh each year and the vast majority of them are here for hands-on training. We provide courses for all knowledge levels-from STEM (science, technology, engineering, and math) programs for middle school children to experienced professionals. We are always working to create the next visual learning opportunity for our visitors so that they can understand how power works and how important it is in our lives. Over the years, I've developed and teach CEU-certified courses on power systems, energy management and power system analysis for our visitors.
POWER: From Eaton's perspective, what is the growing industrial skills gap and how is it impacting power generation?
Carnovale: Analysts indicate the current skills gap created by a steadily retiring workforce may leave an estimated 2.4 million industrial positions unfilled through 2028, with global productivity losses potentially reaching $2.5 trillion as a result. (Source: Deloitte) Filling this skills gap is a significant challenge for the industry and currently there is not enough new talent to fill the retirements on the horizon.
Power generation plants are currently under pressure to maximize energy generation, despite a workforce that is retiring at a record rate. Many power generation plants are using equipment that may be decades old, and near the end of its useful service life. And, the global energy landscape is changing thanks to rapid technology innovation and dramatic growth of renewable power resources and energy storage. This means the next generation of energy professionals must be familiar with technologies old and new-with the ability to operate, diagnose, repair and maintain systems installed decades ago in addition to designing and implementing next-level operations technologies.
Over the years, I've seen a real need for more training, for both new people coming into the industry and experienced professionals. The challenges new and incumbent workers face are often different. New professionals may have hundreds of classroom hours behind them, but little training on the actual equipment they're going to use or design in the field, while seasoned professionals can often benefit from training and hands-on experience on the latest (and always evolving) equipment as well as codes and standards. Education programs that provide critical skills training can help our customers take advantage of new solutions maximizing energy production, enhancing safety and productivity.
POWER: What is Eaton doing to address this challenge?
Carnovale: Eaton is targeting the power industry skills gap with long-term investments in education, training and industry programs for both the current and next-generation workforce. We're partnering with higher education institutions, industry organizations and providing our own training at our Experience Centers to prepare professionals for success in the power industry.
For students and young professionals, we're joining forces with colleges and universities to facilitate learning through real-world training programs. I think our work with the University of Pittsburgh is a great example of how we're partnering with universities to provide hands-on training in real-world environments. We've worked with the University of Pittsburgh for over a decade to develop new courses, certificate programs and research projects to help students speak the language of electrical power. Our dedication comes to life at Pitt's on-campus Electric Power Systems Lab training facility and extends to our most recent joint effort, the Energy Innovation Center lab, where students, faculty and industry organizations collaborate to move the industry forward. These labs foster research across a wide range of electric power areas, including energy efficiency, alternative energy systems and microgrids.
To support engineers, consultants and electricians throughout their careers, we've developed our own training programs and partnered with industry organizations. For example, Eaton provides expansive education programs, including:
- Hands-on training and information sessions at our Experience Centers and regional manufacturing facilities in the U.S. and around the world.
- Regular industry Tech Days and training courses where our experts provide critical training sessions on a range of technologies for CEUs and PDHs.
- Online training courses on arc flash safety, electrical maintenance programs and more.
- Customized training on a range of topics - from safety to maintenance to new technologies - that can help incumbent workers get up to speed on the latest codes and standards.
POWER: What specific training programs and educational environments have you established to support power industry professionals?
Carnovale: It's our goal to take the mystery out of electrical power systems. For power generation industry workforces, our long-term investments in education start at our own Eaton Experience Centers. We provide training and certification programs to support continuing education for experienced professionals and those new to the industry.
For example, electrical consultants play a vital role in the industry and it's essential for electrical system designers to understand the product lines, tools and services available to them. We offer a two-day Power Up Consultant Training seminar that guides early-career professionals through electrical design characteristics including power system design, system protection and coordination, and power quality.
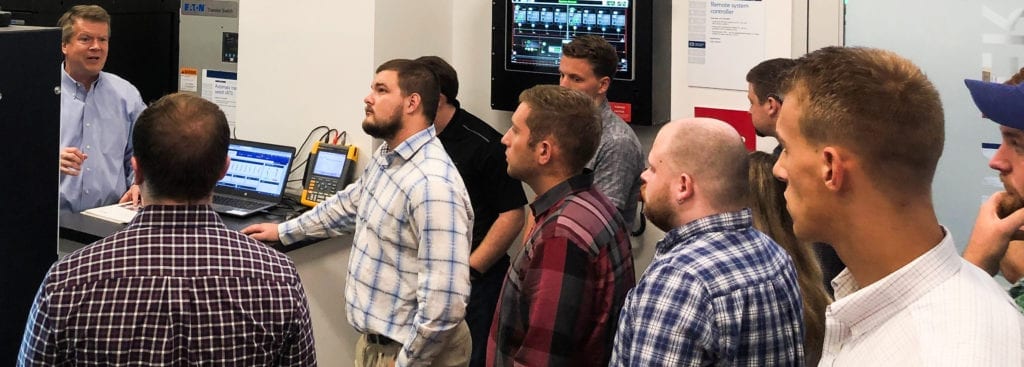
Targeted training programs like Eaton's Power UP program for consultants help early and mid-career professionals keep pace with codes and technology advancements. Courtesy: Eaton Corp.
We've also partnered with industry organizations like the electrical training ALLIANCE to provide the next generation of IBEW (International Brotherhood of Electrical Workers) electrical contractors with the education resources, innovative solutions and expertise they need. We provide many resources to the Joint Apprenticeship and Training Committees and contractors across the country.
POWER: How are real-world training environments helping prepare the next generation of electrical professionals?
Carnovale: At real-world training environments like our Experience Centers and the Electric Power Systems Lab at Pitt, students young and experienced can see and interact with the products and systems that they're going to encounter in actual plants today. These labs enable an immersive learning environment that focuses on providing first-hand experience.
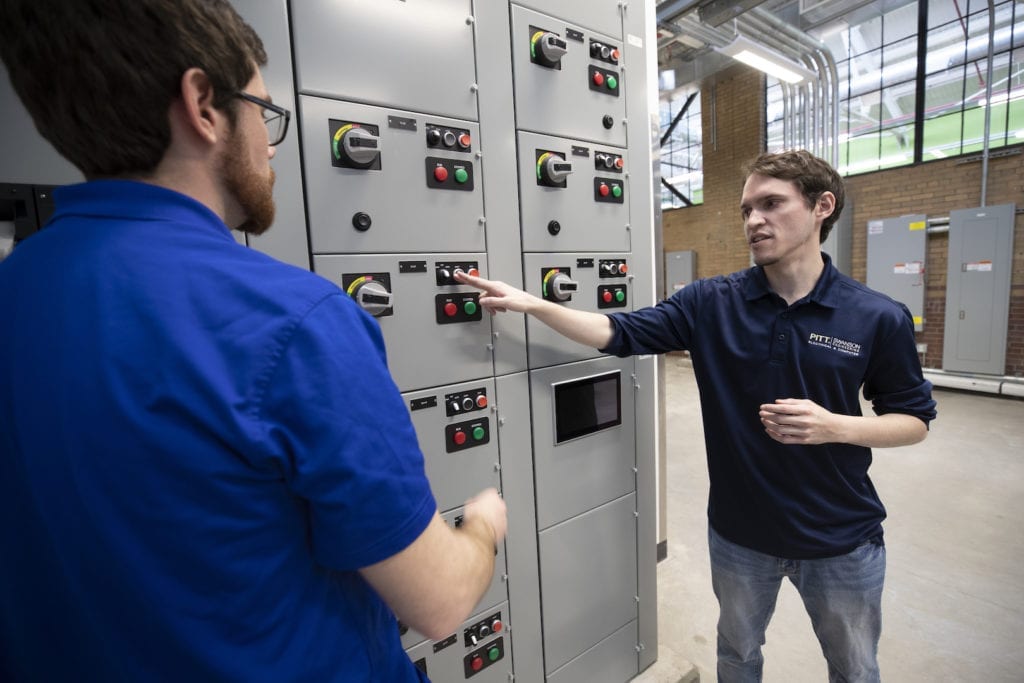
Investments in higher education, like Eaton's long-term collaboration with the University of Pittsburgh, prepare power industry engineers and professionals for the challenges ahead. Courtesy: Eaton Corp.
Real-life lab environments offer a safe and controlled environment to understand complex energy industry challenges, maintaining safety and helping professionals better understand new technologies and evolving codes and standards. Education and training programs like the ones offered at our Experience Centers are preparing professionals for success-providing the right facility, curriculum and equipment to train a workforce with advanced skills and competitiveness.
POWER: What advice would you provide for students hoping to prepare themselves for careers in power generation?
Carnovale: Because power is at the heart of what makes our homes, businesses, and infrastructure work, I think it's an exciting time to be part of the energy industry that fuels the world and makes an impact on people's lives every day. Engineers and electricians that choose the power field have a great outlook for employment for many years to come.
Analysts are estimating a shortage of qualified professionals, so you know that if you're studying to be part of this industry that there will be career opportunities for you. This landscape is rapidly changing due to advanced technology adoption by industry. Tomorrow's technicians will need to operate, diagnose, repair and maintain equipment installed over 40 years ago, while integrating cutting-edge technologies to make the grid safer, more reliable and more sustainable.
POWER: What resources are available for current industry professionals? Do you recommend any specific training programs or resources?
Carnovale: With access to advanced training, power professionals of every experience level are better prepared to help modernize the power grid and our electrical infrastructure. You can access our training programs, videos on power topics, and information about our Experience Centers at Eaton.com/Experience.
POWER: Where can our readers go to learn more? Is there anything else you'd like to add?
Carnovale: There's a critical need to build a bench of talent to address an aging workforce and skilled labor shortages. Eaton plays a vital role in educating the next generation of power industry professionals through wide-ranging and impactful collaborations with higher education institutions, industry partnerships and targeted training programs.
Readers can learn more about our initiatives and discover training and educational resources by visiting www.eaton.com/nextgeneducation. You can also reference our For Safety's Sake blog to gain new perspectives on the codes and standards that shape electrical safety across industry.
-POWER staff (@POWERmagazine).
The post The POWER Interview: Eaton Targets Skilled Labor Shortage With Hands-on Training appeared first on POWER Magazine.