How One Fabrication Shop in Alabama Is Powering Through the Pandemic
The post How One Fabrication Shop in Alabama Is Powering Through the Pandemic appeared first on POWER Magazine.
Drive one hour south of Birmingham and you will find the not-so-small town of Tuscaloosa, Alabama, county population of more than 207,000. Known as the home of the University of Alabama, Tuscaloosa is rich in history, arts, young professionals, rooted families, and famous Southern hospitality. At the heart of this college town is a culture of trade workers and quality craftsmanship.
At the edge of downtown Tuscaloosa sits Dixie Mechanical Inc., a mechanical contractor with local roots and a national footprint. Dixie Mechanical serves as an industrial fabrication contractor on projects with the nation's largest engineering, procurement, and construction (EPC) firms. Since 2002, the fabrication shop (Figure 1), project managers, estimators, draftsmen, and the entire team have been providing quality craftsmanship and project management to clients working on some of the largest power, energy, oil, gas, and chemical construction projects that keep America running. These projects are essential to the nation's infrastructure.
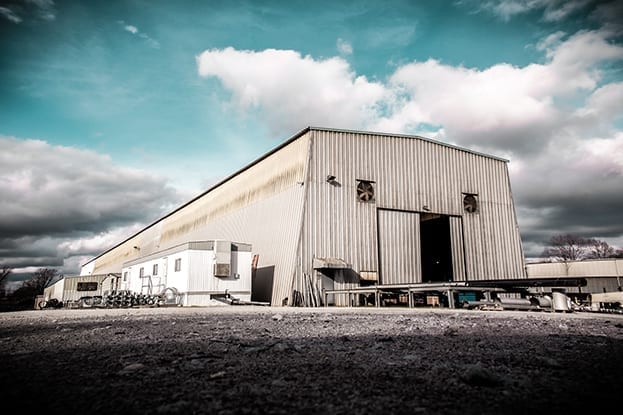
On March 16, 2020, the management team at Dixie Mechanical met to discuss the possible repercussions of the spreading novel coronavirus, COVID-19. The meeting was to prepare for possible scenarios that could affect the day-to-day operations of the company's services.
"How do we ensure that our operations continue as planned without unforeseen interruptions? That's what we wanted to prepare for," Doug Killough, Marketing and Sales manager with Dixie Mechanical, said. "If we are prepared, they wouldn't be 'unforeseen interruptions,' they would just be obstacles, and we can handle obstacles."
Dixie Mechanical is not alone. Almost every company or organization in the U.S. is dealing with hurdles and obstacles set in place by the global pandemic. It's how the company is navigating the course that is proving effective.
"We've implemented safety precautions recommended by the Centers for Disease Control and Prevention (CDC) and World Health Organization (WHO) for our employees that cannot work from home; for those that can, we've reinforced our communications and digital platforms to ensure working from home does not hinder our progress, productivity, and executions, and that we can all #PowerOnTogether," Killough said.
Dixie Mechanical's fabrication shop works like an assembly line. On one end of the shop is the receiving department. This end of the shop, the entrance, is where pipe spools enter the shop and are measured and cut to the exact specifications noted on isometric drawings (Figure 2). Moving down the line, the spools are tack-welded then passed down to the welders (Figure 3). The spools, valves, flanges, and countless other materials are welded and sent down the line for inspection. After passing inspection and being painted, if necessary, the spools are ready to be loaded for delivery to the client's project site.
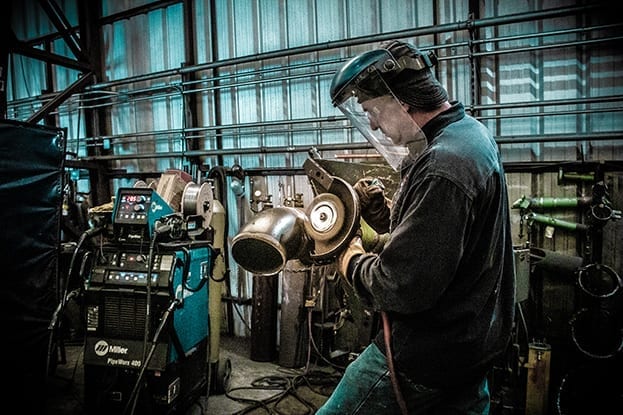
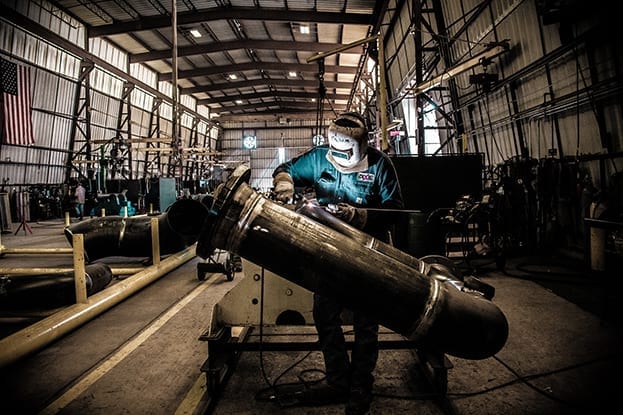
After COVID-19 impacted the workforce, Dixie Mechanical began operating under the recommendations from the CDC and WHO. The assembly line setup has ultimately been stretched. The space between each workstation in the shop has been evaluated and increased, if necessary, to meet the minimum 6-foot distance. Shop workers operate with Occupational Safety and Health Administration (OSHA)-standard PPE (personal protective equipment) regularly, so implementing PPE was not new territory-shop workers are required to wear PPE at all times when in the shop. Where the most significant adjustments were made was in social distancing and breaks.
The shop break room is where most shop workers (more than 50 employees) take their scheduled 15-minute breaks and 35-minute lunch break. Dixie Mechanical enforces break times and lunch time, so all shop workers are on one break at the same time. This causes issues with social distancing as more people are trying to use the same break room at the same time.
"We knew we couldn't let the entire shop crew squeeze into the break room at the same time, so we decided to enforce workstation lunches," Killough said. "All breaks and lunches are to be taken at individual workstations, which have already been measured to maintain the 6-foot rule."
Aside from social distancing, all employees in the shop and office are asked to hold each other accountable when practicing cleanliness and sanitation. Hand sanitizer and antibacterial wipes have been placed throughout the shop and offices to encourage clean workspaces.
Modern Processes Facilitate SafetyFortunately, today's technology allows for better communication and the ability to work from home. Dixie Mechanical's office staff, comprised of project managers, drafters, estimators, material coordinators, controllers, accounts payable, and more, have the option of working from home. A handful of employees are doing so while the others are taking advantage of fewer bodies in the workplace. Having some employees work from home allows those remaining in the office to implement the 6-foot rule with fewer complications.
For the past two years, Dixie Mechanical has been implementing its customized Microsoft Office 365 platform, utilizing tools such as Microsoft Teams, SharePoint, custom Flows, and OneDrive, to name a few. Each job or bid has its own secure SharePoint site that hosts working documents that can be manipulated simultaneously by multiple employees. Drawings, ongoing tasks, relevant information (such as deadlines and changes), and other details are available, allowing for more efficient execution. This has become a crucial aspect of daily operations during the COVID-19 pandemic, as it has allowed Dixie to meet deadlines and deliverables without any of unforeseen interruptions.
Dixie Mechanical's clients are essential businesses making Dixie essential as well. With that in mind, the team is utilizing these digital platforms and programs to work remotely. "Our clients expect the best, and we aren't going to let a few obstacles prevent us from keeping our promises," Killough affirmed. "If anything, we will use this to better understand the challenges that working remotely may present, and how we can continue improving our operations, execution, and project management to continue servicing our clients in the future. We are powering through."
Dixie Mechanical has taken the obstacles presented by the COVID-19 outbreak and used them as learning opportunities, to act as a stress-test for the company's digital infrastructure and as an opportunity to flex the company's collective muscles to deliver on promises to its clients. For more information on Dixie Mechanical or how it plans to #PowerOnTogether through the pandemic, contact Doug Killough (dkillough@dixiemechanical.com) or visit www.dixiemechanical.com/covid19.
-Edited by Aaron Larson, POWER's executive editor.
The post How One Fabrication Shop in Alabama Is Powering Through the Pandemic appeared first on POWER Magazine.