Coal Plant Conversion to Non-Recyclable Plastic Waste Combustion Advances
The post Coal Plant Conversion to Non-Recyclable Plastic Waste Combustion Advances appeared first on POWER Magazine.
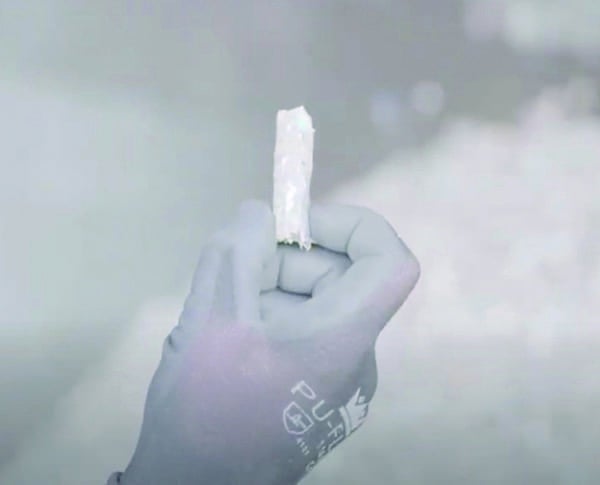
A hundred metric tons of innovative fuel pellets derived entirely from biogenic and plastic waste material-which would otherwise be bound for a landfill-have been successfully produced, marking a technological leap toward large-scale combustion testing at a coal plant in the UK.
It's a big step for SIMEC Atlantis Energy, a UK-based diversified sustainable energy developer, which has been working to convert the 220-MW coal-fired Uskmouth Power Station in Newport, South Wales, to combust non-recyclable waste for power generation by 2021. The milestone, which it marked this March, provides further confidence that the energy pellets developed as a high calorific value, low cost alternative to coal are able to be produced in commercial quantities and can be milled using industry standard designs," it said. However, it's also remarkable considering how ambitious the proposal is and how quickly the company has arrived to this point.
![]() |
5. The Uskmouth coal-to-waste conversion project is designed to use sustainable fuel pellets that are composed of 50% high-energy non-recyclable plastic and 50% biogenic material, like paper and cardboard. After pellets are received from a pelleting facility, they are fed into mills, where they are pulverized and then combusted. Courtesy: SIMEC Atlantis Energy |
As SIMEC Atlantis Energy CEO Timothy Cornelius notes in financial filings, Uskmouth was built in 1959 as a project designed to use the Welsh region's abundant local coal supply. A successful conversion at Uskmouth could form the blueprint for other power stations destined to be decommissioned, providing instead an extended period of valuable service in compliance with up-to-date emissions regulations and with materially lower levels of CO 2 emissions," he noted. This project is expected to help the transition of the local economy and workforce in Newport from a historic reliance on coal to a new, sustainable future, while at the same time providing an economically viable alternative to landfill of waste and addressing the issue of non-recyclable plastics." The waste the project (Figure 5) could convert into power over its lifetime would require a landfill the size of London to a depth of 73 meters or would fill more than 46,000 Olympic swimming pools," the company claims.
Cornelius noted the company acquired Uskmouth only two years ago, in June 2018, as part of a merger between SIMEC Energy, a subsidiary of London-headquartered manufacturing and engineering business group GFG Alliance, and Atlantis Resources Ltd., a company which is better known for its majority stake in MeyGen, the world's largest tidal stream project (and a POWER Top Plant in 2018). Along with initiating front-end engineering design (FEED) work for the conversion project in November 2018, SIMEC Atlantis Energy also formed a 50:50 joint venture with Dutch recycling group N+P Group BV to produce end-of-waste energy pellets, which essentially comprise equal proportions of waste biogenic material, such as paper and cardboard, and other forms of waste, such as plastic. As Cornelius noted, securing this fuel supply was crucial.
Unlike traditional waste incinerators, the primary purpose of the Uskmouth power station is the generation and sale of electricity, rather than the disposal of waste and the receipt of the associated fees from the producers of that waste," he said. Rather than charging fees for waste disposal, the Uskmouth power station will buy fuel pellets, which are created from waste streams that are carefully processed to ensure strict adherence to an agreed specification and high calorific value relative to raw waste. This is economically viable because of the high fuel quality and high efficiency of power station conversion, coupled with a low fuel price."
By March 2019, the company had completed the return to service and plant readiness review, and only a month later, it reported it had completed pilot-scale fuel production runs and milling. In April 2019, it also successfully completed combustion tests of the waste pellets, confirming a 100% solid recovered fuel (SRF) flame stability. Then, in October 2019, it revealed that its fuel supplier Simec Subcoal Fuels, formed from the N+P Group joint venture, would assemble a dedicated industrial-scale pilot production line for supply of the test fuel at its existing pelleting facility in the Netherlands. And in another significant step, it also brought on board Mitsubishi Hitachi Power Systems Europe GmbH (MHPS Europe), awarding it a contract to carry out the design and development of the combustion system for the Uskmouth project. The contract covers large-scale milling trials, which were completed in Germany this March.
The next stage now entails final large-scale combustion trials at a 24-MW MHPS test facility in Nagasaki, Japan. If these efforts result in a final validation of the fuel specification, and the mill and burner designs, SIMEC Atlantis will award the major engineering, procurement, and construction contract for the supply of a full combustion system. In documents published in early March, the company said construction could begin later this year, and it expects commercial operations to commence in 2021. Thereafter, it plans to sell power from the 220-MW (with the potential to be expanded by 70 MW) facility through two 20-year power purchase agreements (PPAs) with GFG Alliance companies.
-Sonal Patelis a POWER senior associate editor.
The post Coal Plant Conversion to Non-Recyclable Plastic Waste Combustion Advances appeared first on POWER Magazine.