The POWER Interview: Optimizing Operations with IoT Technology
The post The POWER Interview: Optimizing Operations with IoT Technology appeared first on POWER Magazine.
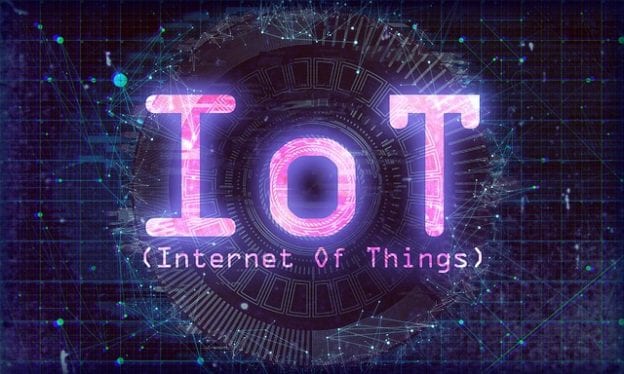
Some experts have predicted there will be as many as 50 billion connected devices in service by the end of this year. That number basically includes all of the equipment, sensors, and gadgets around the world that together make up the internet of things (IoT). But how are they all connected, what allows them to communicate with each other, and how do these systems benefit users?
To get an insider's perspective, POWER posed some questions about open-source technology to Akshay Patwal, strategic business manager with Siemens Energy. Patwal leads the development and commercialization of digital business transformation projects, using big data platforms and analytics, to create data-driven services. He has been pioneering the building of digitalization and big data-based framework by developing and implementing company-wide platforms, systems, and business processes to maximize the value of enterprise data, driving performance improvement, cost reduction, and revenue generation. He is an expert and thought-leader on data management, data analytics, and visualization technologies in the energy industry, so he obviously has a wealth of knowledge on the subject.
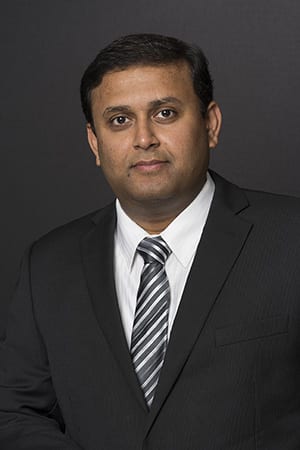
POWER: I understand Siemens' MindSphere is an open-IoT operating system. What does that mean?
Patwal: MindSphere in power generation is a cloud-based, open-IoT platform operating system developed by Siemens to connect all data, applications, and business models with power plant assets and processes. It provides an effective data management layer for IoT data acquisition, storage, integration, and validation, and this is supported by a strong analytical applications suite having a range of applications dealing with predictive maintenance, performance optimization, cybersecurity, and fleet monitoring and diagnostics.
The term IoT operating system" refers to an operating system designed to function within the constraints such as restrictions on memory, size, processing power, and more, relevant to IoT devices. It is considered open because it allows interfacing with products, assets, and processes from any vendor or customer.
It provides a wide range of options for connectivity with different vendor-agnostic devices, enterprise system protocols, industry applications, analytical packages, and user interfaces. It offers an innovative development environment, which utilizes Siemens Platform-as-a-Service (PaaS) with access to Amazon Web Services (AWS), Microsoft Azure, and Alibaba public cloud services. It connects physical assets to the digital world and offers industry applications for digital services for business models. The goal is to drive closed-loop innovation through development of digital twins for all assets and provide products and business models.
The features of MindSphere include secure connection of all assets with hardware and software solutions. It offers an environment for easy development, deployment, and testing with preconfigured solutions. There is a catalog-based approach for purchasing and distributing applications. This allows users to pick and choose applications, and get them customized to meet their individual requirements.
A broad spectrum of APIs [application programming interfaces] provides an easy way to connect and interact with varied applications. Being native cloud development, it provides consistent development and automated management experience across private, public, and hybrid cloud infrastructure. Enhanced data visualization and exploration capabilities provide an avenue for the generation of explored insights in data regarding asset health, performance, and behavior.
One of the impressive aspects about MindSphere is the existence of a store" with predefined packages having certain dedicated set of capabilities and services targeted toward achieving certain goals, which guides organizations at different levels in the digitalization maturity.
MindSphere allows development of robust IoT solutions with open PaaS with access to cloud infrastructure. It offers interface to a wide range of devices, assets, and enterprise systems from edge to cloud connectivity. Incorporating all possible industry solutions with advanced analytics, it offers closed-loop innovation and end-to-end decision-making with digital twins. All partners, vendors, and customers can easily create a partnership with the ecosystem to have access to industry solutions and services.
One of the unique aspects of the platform is the MindSphere Application Centers, which facilitate co-creation of digital business models and offerings to enhance business opportunities. It provides an interface for customers to operate and focus on their requirements to obtain solutions. Siemens offers excellent domain expertise and data analysis experience to focus on specific challenges in power generation. The company is customer-focused and reacts flexibly to customer requests. Discussions often lead to concrete customer offerings and references.
POWER: How is MindSphere different from other systems?
Patwal: Some of the features that separate MindSphere from competitors' systems are:
- Pre-Defined Applications. The platform offers pre-packaged applications depending on the digital maturity of the organization. It offers a low-barrier version called MindAccess for beginners with basic applications around asset connectivity, configuration, monitoring, and management. The Asset Manager provides a framework for users to build models of the entire industrial process by connecting assets and creating relevant data models. It can also incorporate configuration of entire fleets. The Fleet Manager performs monitoring, allows visualization, alerts of anomalies, provides insights, and creates business rules around them. The MindAccess IoT Value Plan offers permissions and roles to groups within organizations.
- Extensive Connectivity Options. There is provision for connectivity for a wide range of industrial assets from Siemens and other vendors. Siemens' family of MindConnect connectivity devices collects data from all relevant assets and sends it to the platform. In terms of software, MindConnect IoT Extension integration layer supports all possible protocols and enables any IoT-ready device from all vendors to connect to the platform. The API enables programming of connectivity agents for specific use cases.
- Creating and Selling IoT Apps. The platform houses an entire suite of third-party applications. It allows companies to develop their own subscription-based applications in MindSphere and sell them to customers via MindSphere Marketplace. They are allowed to set their own pricing, and receive incentives and resources for investing in MindSphere development as part of a partner program. The developers can also build apps in a local environment in any coding tool and upload them to the cloud using MindAccess DevOps Plan. This application development and implementation is enabled by the open-source Cloud Foundry application platform.
- Build IoT Apps with Low-Code Solution. The acquisition of Mendix with the low-code development platform has been integrated within MindSphere and has enabled coding amateurs to build apps for the platform. The platform offers a visual drag-and-drop interface along with the collaboration features and artificial intelligence (AI)-powered development environment.
- Easily Integration with ERP, MES, and SCADA Systems. The MindConnect integration tool in both on-premise and cloud-based offerings allows companies to send data to MindSphere from enterprise resource planning (ERP), manufacturing execution system (MES), and supervisory control and data acquisition (SCADA) systems using cloud-based adaptors and protocols. The tool possesses predefined integration configurations and graphical user interface (GUI) for mapping data values into the platform.
The growth of MindSphere has been tremendous and with the inclusion of AI, machine learning (ML), and augmented virtual reality (AVR) there will be further developments in this regard.
POWER: Can you provide specific examples of asset defect notifications customers have received and how that helped them?
Patwal: There are plenty of examples where MindSphere has played a key role in the early notifications and diagnostics concerning asset defects and health. Some examples relevant to the energy and utilities industry include:
- Scalable Plant-Wide Predictive Maintenance by Sensye. The challenge in this use case was that the visibility of machine-condition information was limited, and therefore, maintenance was conducted in a reactive way. As a result, 24% of manufacturing costs were attributed to unplanned downtime, with 90% of maintenance work performed during breakdowns. By monitoring asset health and providing early notifications of unplanned events, downtime was considerably reduced. This led to a reduction in maintenance costs by 40%, improved maintenance productivity by 55%, a 50% reduction in downtime, and improved downtime forecast accuracy by 85%.
- Real-Time Machine Monitoring and Analytics by Orange Business Services. The manufacturing plant floors use a host of software systems and machines, but without a clear way to gather data. The solutions were also outdated, home-grown, ineffective, cost-prohibitive, and cumbersome. The platform combined data sources, real-time calculations of key performance indicators (KPIs), and asset performance. A user-friendly interface and easy-to-configure formula editor, along with a customizable dashboard to provide real-time data collection and KPIs were created. The operational performance was optimized with real-time monitoring and analytics. Machine effectiveness and efficiency improved without raising costs using end-to-end solutions.
- Multisite Data Integration to Cloud and Asset Management by Quest. Existing asset management systems were limited to descriptive and diagnostic capabilities. Newer application-specific IoT applications were considered expensive and time-consuming to implement. The ready-to-deploy applications and solutions in the MindSphere platform accelerated time of implementation and reduced cost by implementing multisite asset management for effective decision-making and downtime reduction. This increased the asset availability due to predictive and prescriptive maintenance. It reduced operational costs, and enabled multisite asset monitoring and control, providing real-time access to asset health and status.
- Intelligent Water Metering by Sigfox Germany. The operating cost was very high, and service needed to be expanded with higher efficiency. The efficiency and sustainability of drinking water had to be managed along with the maintenance and monitoring of assets. The monitoring of the assets in the whole process led to detection and measurement of the smallest throughputs, attempted manipulation, leakage, and pipe breakage. Alerting was automated along with meter reading and billing being done based on actual consumption. It reduced maintenance frequency by remote monitoring and long battery life in monitors. It prevented fines and penalties for water over-consumption due to leaks and breakages. It also reduced the time and improved accuracy of invoicing.
- Adaptive Visual Inspection by Capgemini. This was a mobile, visual, quality inspection solution for the assembly lines. It analyzed real-time data and image processing, and used an AI algorithm to inspect the quality of assembled parts in production. The quality data associated with the images is processed into a time-series data. A workflow and dashboard quality inspection result guides the line managers to correct problems. It increased the quality outcomes of assembly line processes, thus improving productivity and workflows related to quality inspections during assembly.
- Asset Health Management by Tata Consultancy Services. There needed to be visibility into the real-time asset performance for critical parameters and relevant anomalies in the deployed assets. There was a huge cost associated with downtime due to reactive maintenance. The real-time monitoring of key parameters against defined threshold limits, alerting, and automated work order generation based on these threshold violations prevented machine failure. It reduced unplanned downtime and provided a proactive approach to maintenance. It also improved the response times and efficiency of the maintenance team using live asset data.
- AssetWise Operational Analytics by Bentley Systems. This system offered by Bentley does data acquisition, integration, advanced analytics, and visualization of KPIs to improve operations and maintenance, and prioritizes the maintenance and inspection activities to be performed on critical assets. The visualization of performance data, early detection and prediction of faults, and predictive maintenance recommendations resulted in improved decision-making and proactive maintenance to drive productivity and uptime.
- Smart Welding Management by LivNSense. Welding technology is critical to about 90% of durable goods and heavy machinery production and construction. There is lack of real-time monitoring, usage patterns, machine health and warranty tracking, and defect resolution was done in a manual and ad-hoc fashion. The smart welding solution provided monitoring and prediction into the system, and extracted insights into operations efficiency, downtime, and weld quality. A unique end-to-end solution including hardware gateway reduced equipment downtime, and maintenance and warranty costs. It improved weld quality and increased spare sales. It also optimized the skilled workforce training and productivity along with the tracking of location and maintenance records of machinery.
-Aaron Larson is POWER's executive editor (@AaronL_Power, @POWERmagazine).
The post The POWER Interview: Optimizing Operations with IoT Technology appeared first on POWER Magazine.