From Foldable Phones to Stretchy Screens

Motorola demonstrated the very first handheld mobile phone almost a half century ago. It was the size of a brick and weighed half as much. That prototype spawned the first commercial mobile phone a decade later. It, too, was ungainly, but it allowed a person to walk around while sending and receiving phone calls, which at that point was a great novelty. Since then, mobile phones have acquired many other functions. They now have the ability to handle text messages, browse the Web, play music, take and display photos and videos, locate the owner on a map, and serve countless other uses-applications well beyond what anybody could have imagined when mobile phones were first introduced.
But smartphones, nimble as they are, have struggled to overcome one seemingly fundamental drawback: Their displays are small. Sure, some phones have been made larger than normal to provide more real estate for the display. But make the phone too big and it outgrows the owner's pocket, which is a nonstarter for many people.
The obvious solution is to have the display fold up like a wallet. For years, developing suitable technology for that has been one of our goals as researchers at Seoul National University. It's also been a goal for smartphone manufacturers, who just in the past year or two have been able to bring this technology to market.
Soon, phones with foldable screens will no doubt proliferate. You or someone in your family will probably have one, at which point you'll surely wonder: How in the world is it possible for the display to bend like that? We figured we'd explain what's behind that technology to you here so that you're ready when a phone with a large, bright, flexible display comes to a pocket near you-not to mention even more radical electronic devices that will be possible when their screens can stretch as well as bend.
Researchers have been seriously investigating how to make flexible displays for about two decades. But for years, they remained just that-research projects. In 2012, though, Bill Liu and some other Stanford engineering graduates set out to commercialize flexible displays by founding the Royole Corp. (which now has headquarters in both Fremont, Calif., and Shenzhen, China).

A Closed Book: In late 2018, Royole Corp. developed the first commercial smartphone with a bendable display, the FlexPai. It folds closed with the screen still visible on the outside.
In late 2018, Royole introduced the FlexPai, whose flexible display allows the device to unfold into something that resembles a tablet. The company demonstrated that this foldable display could withstand 200,000 bending cycles-and quite tight bends at that, with a radius of curvature of just 3 millimeters. But the FlexPai phone was more of a prototype than a mature product. A review published in The Verge, for example, called it charmingly awful."
Soon afterward, Samsung and Huawei, the world's two largest smartphone makers, began offering their own foldable models. Samsung Mobile officially announced its Galaxy Fold in February 2019. It features dual foldable displays that can be bent with a radius of curvature as small as 1 mm, allowing the phone to fold up with the display on the inside. Huawei announced its first foldable smartphone, the Mate X, later that month. The Mate X is about 11 mm thick when folded, and its display (like that of the FlexPai) is on the outside, meaning that the bending radius of the display is roughly 5 mm. And in February of this year, each company introduced a second foldable model: Samsung's Galaxy Z Flip and Huawei's Mate Xs/5G.
The most challenging part of engineering these phones was, of course, developing the display itself. The key was to reduce the thickness of the flexible display panel so as to minimize the bending stresses it has to endure when folded. The smartphone industry has just figured out how to do that, and panel suppliers such as Samsung Display and Beijing-based BOE Technology Group Co. are now mass-producing foldable displays.
Like those found in conventional smartphones, these are all active-matrix organic light-emitting-diode (AMOLED) displays. But instead of fabricating these AMOLEDs on a rigid glass substrate, as is normally done, these companies use a thin, flexible polymer. On top of that flexible substrate is the backplane-the layer containing the many thin-film transistors needed to control individual pixels. Those transistors incorporate a buffer layer that can prevent cracks from forming when the display is flexed.
Although flexible displays constructed along these lines are fast becoming more common for phones and other consumer products, the standards that apply to these displays, as well as language for describing their ability to bend, are still, you might say, taking shape. These displays can be at least broadly characterized according to the radius of curvature they can withstand when flexed: Conformable" refers to displays that don't bend all that tightly, rollable" refers to ones with intermediate levels of flexibility, and foldable" describes those that can accommodate a very small radius of curvature.
Because any material, be it a smartphone display or a steel plate, is in tension on the outside surface of a bend and in compression on the inside, the electronic components that make up a display must resist those stresses and the corresponding deformations they induce. And the easiest way to do that is by minimizing those shape-changing forces by bringing the outside surface of a flexed display closer to the inside surface, which is to say to make the device very thin.
To make the display as thin as possible, designers omit the protective film and polarizer that normally go on top, along with the adhesive applied between these layers. While removing those elements is not ideal, both the protective film and antireflection polarizer are optional components for AMOLED displays, which generate light internally rather than modifying the amount of light transmitted from an LED backlight, as in liquid-crystal displays.
Another difference between flexible and conventional displays has to do with the transparent conductive electrodes that sandwich the light-emitting organic materials that make the pixels shine. Normally, a layer of indium tin oxide (ITO) fills this role. But ITO is quite brittle under tension, making it a bad choice for flexible displays. To make matters worse, ITO tends to adhere poorly to flexible polymer substrates, causing it to buckle and delaminate when compressed.
Researchers battling this problem a decade ago found a few strategies for improving the adhesion between ITO and a flexible substrate. One is to treat the substrate with oxygen plasma before depositing the ITO electrode on top. Another is to insert a thin layer of metal (such as silver) between the electrode and the substrate. It also helps to place the top of the substrate in the exact middle of the layer cake that makes up the display. This arrangement puts the fragile interface with the ITO layer on the display's mechanical neutral plane, which experiences neither compression nor tension when flexed. Currently, the leading electronics companies that make foldable displays are using this strategy.
Even simpler, you can get rid of the ITO electrodes altogether. While that hasn't been done yet in commercial devices, this strategy is attractive for reasons having nothing to do with the desire for flexibility. You see, indium is both toxic and expensive, so you really don't want to use it if you don't have to. Fortunately, over the years researchers, including the two of us, have come up with several other materials that could function as transparent electrodes for flexible displays.
A flexible film that contains silver nanowires is probably the most promising candidate. These vanishingly tiny wires form a mesh that conducts electricity while remaining largely transparent. Such a layer can be prepared at low cost by applying a solution containing silver nanowires to the substrate in a manner similar to that of printing ink on newsprint.
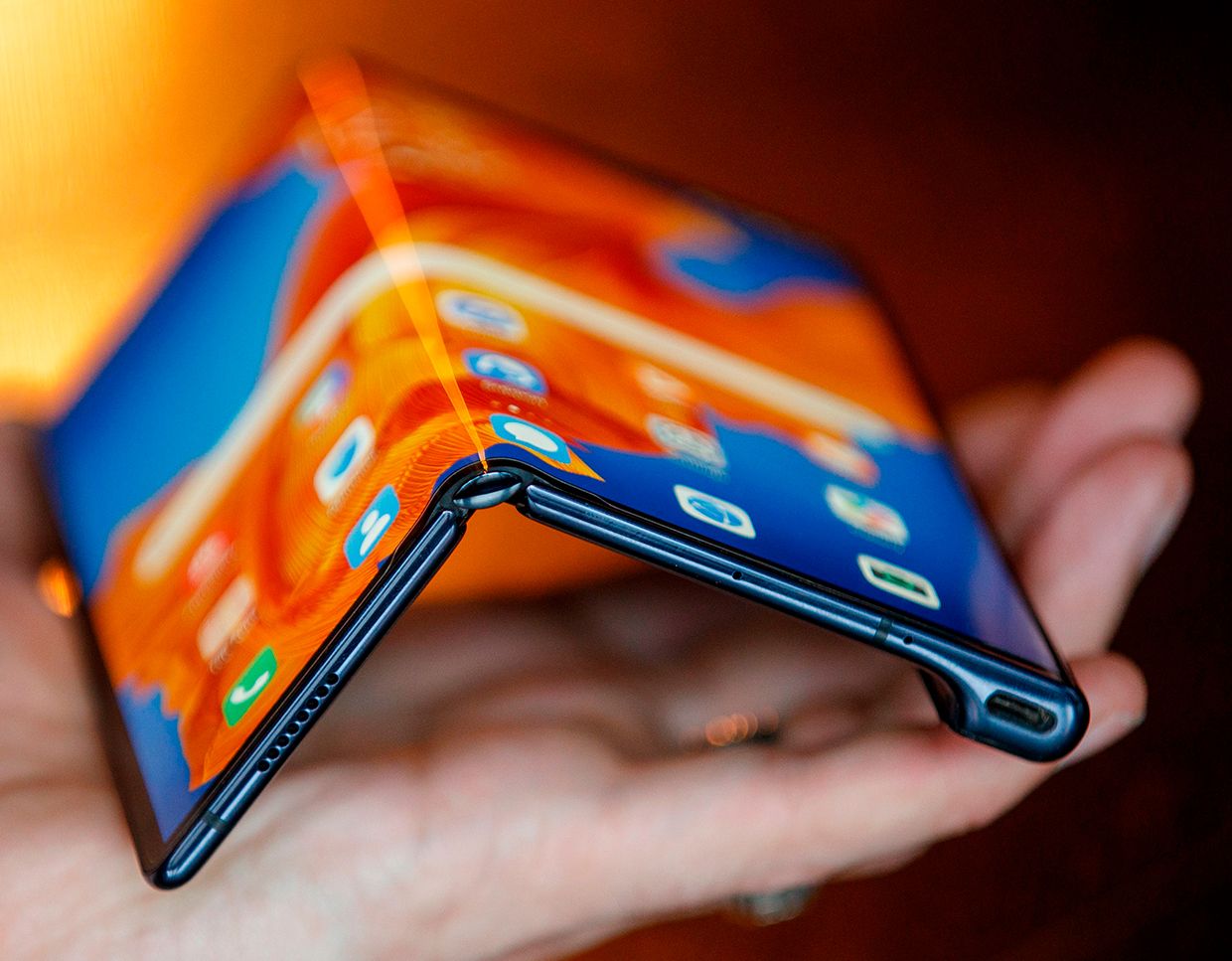
Most of the research on silver nanowires has been focused on finding ways to reduce the resistance of the junctions between individual wires. You can do that by adding certain other materials to the nanowire mesh, for example. Or you can physically treat the nanowire layer by heating it in an oven or by sending enough electricity through it to fuse the nanowire junctions through Joule heating. Or you can also treat it by hot-pressing it, subjecting it to a plasma, or irradiating it with a very bright flash to fuse the junctions. Which of these treatments is the best to use will depend in large part on the nature of the substrate onto which the nanowires are applied. A polymer substrate, such as polyethylene terephthalate (PET, the same material that many clear plastic food containers are made of), is prone to problematic amounts of deformation when heated. Polyimide is less sensitive to heat, but it has a yellowish color that can compromise the transparency of an electrode created in this way.
But metal nanowires aren't the only possible substitute for ITO when creating transparent conductive electrodes. Another one is graphene, a form of carbon in which the atoms are arranged in a two-dimensional honeycomb pattern. Graphene doesn't quite match ITO's superb conductivity and optical transparency, but it is better able to withstand bending than any other electrode material now being considered for flexible displays. And graphene's somewhat lackluster electrical conductivity can be improved by combining it with a conducting polymer or by doping it with small amounts of nitric acid or gold chloride.
Yet another possibility is to use a conductive polymer. The prime example is poly(3,4-ethylenedioxythiophene) polystyrene sulfonate-a mouthful that normally goes by the shorter name PEDOT:PSS. Such polymers can be dissolved in water, which allows thin, transparent electrodes to be easily fabricated by printing or spin coating (an industrial process akin to making spin art). The right chemical additives can significantly improve the ability of a film of this conductive polymer to bend or even stretch. Careful selection of additives can also boost the amount of light that displays emit for a given amount of current, making them brighter than displays fabricated using ITO electrodes.
Up to now, the organic LED displays used in mobile phones, computer monitors, and televisions have mainly been fabricated by putting the substrate under vacuum, evaporating whatever organic material you want to add to it, and then using metal masks to control where those substances are deposited. Think of it as a high-tech stenciling operation. Those metal masks with their very fine patterns are hard to fabricate, though, and much of the applied material is wasted, contributing to the high cost of large display panels.
An interesting alternative, however, has emerged for fabricating such displays: inkjet printing. For that, the organic material you want to apply is dissolved in a solvent and then jetted onto the substrate where it is needed to form the many pixels, followed by a subsequent heating step to drive off any solvent that remains. DuPont, Merck, Nissan Chemical Corp., and Sumitomo are pursuing this tactic, even though the efficiency and reliability of the resulting devices still remain far lower than needed. But if one day these companies succeed, the cost of display fabrication should diminish considerably.
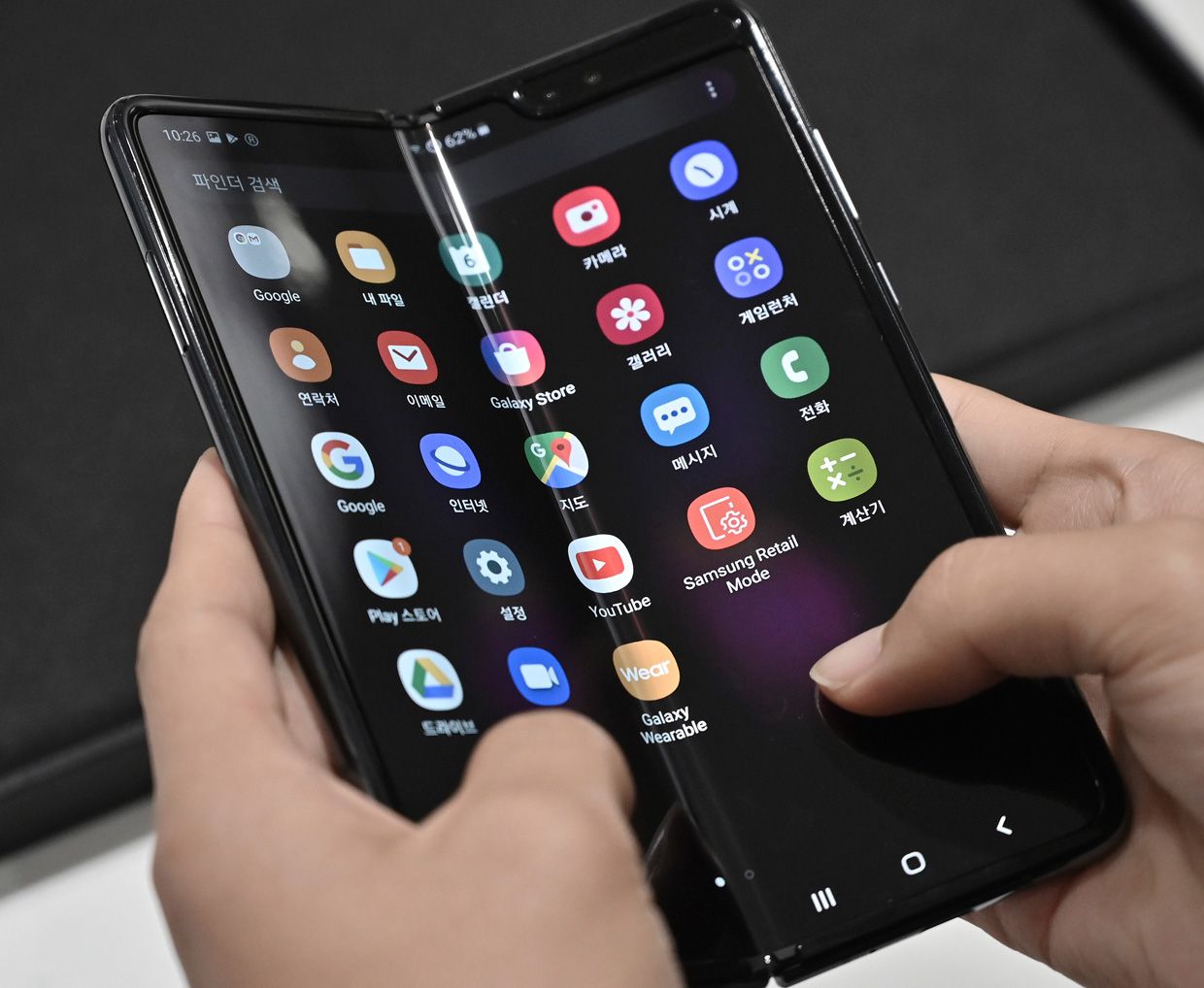
For makers of small displays for smartphones, an even higher priority than keeping costs down is reducing power consumption. Organic LEDs (OLEDs) are becoming less power hungry, but the more mature the OLED industry becomes, the more difficult it will be to further trim power consumption from its current value of around 6 milliwatts per square centimeter (about 40 mw per square inch). And the diminishing returns here are especially problematic for foldable phones, which boast displays that are much larger than normal. So it's probably a safe bet that your foldable phone, compact as it is, will have to contain an especially hefty battery, at least in the near term.
What's next for flexible displays after they allow our smartphones to fold? Given how much people seem glued to their phones now, we anticipate that in the not-so-distant future, people will start wearing displays that attach directly to the skin. They'll likely use these devices initially to visualize various kinds of biometric data, but other applications will no doubt emerge. And perhaps such wearable displays will one day be used just to make a high-tech fashion statement.
The materials used to produce such a display should, of course, be soft enough not to be bothersome when attached to the skin. What's more, they would have to be stretchable. Fabricating intrinsically stretchable conductors and semiconductors is an enormous challenge, though. So for several years researchers have been exploring the next-best thing: geometrically stretchable displays. These contain rigid but tiny electronic components attached to a stretchable substrate and connected by conductive pathways that can withstand the deformation that accompanies stretching.
More recently, though, there's been progress in developing intrinsically stretchable displays-ones in which the conductors and semiconductors as well as the substrate can all be stretched. Such displays require some novel materials, to be sure, but perhaps the greatest hurdle has been figuring out how to devise stretchable materials to encapsulate these devices and protect them from the damaging effects of moisture and oxygen. Our research team has recently made good progress in that regard, successfully developing air-stable, intrinsically stretchable light-emitting devices that do not require stretchable protective coatings. These devices can be stretched to almost twice their normal length without failing.
Today, only very crude prototypes of stretchable displays have been fabricated, ones that provide just a coarse grid of luminous elements. But industry's interest in stretchable displays is huge. This past June, South Korea's Ministry of Trade, Industry and Energy assigned LG Display to lead a consortium of industrial and academic researchers to develop stretchable displays.
With just a little imagination, you can envision what's coming down the road: athletes festooned with biometric displays attached to their arms or legs, smartphones we wear on the palms of our hands, displays that drape conformably over various curved surfaces. The people who are working hard now to develop such future displays will surely benefit from the many years of research that have already been done to create today's foldable displays for smartphones. Without doubt, the era for not just bendable but also stretchable electronics will soon be here.
This article appears in the November 2020 print issue as Displays That Bend and Stretch."
About the AuthorsHuanyu Zhou is studying for a doctorate at Seoul National University under the direction of Tae-Woo Lee, a professor of materials science and engineering there.