GM Opens Up a New Front in Its Battle With Tesla: Batteries

In April of 1966, a shiny white Chevrolet Impala became the first car off the assembly line of a new General Motors plant in Lordstown, Ohio. It was the glorious start of what became a checkered history for the area. This blue-collar town survived an infamous labor strike in 1972, the Chapter 11 bankruptcy of GM in 2009, and a string of unmemorable small cars-including the Chevy Vega and Cavalier-before emerging as a symbol of industrial rebirth with the production of the Chevy Cruze in 2010.
But things soon went to hell again, and GM shuttered the plant in 2019. Even then, the pain wasn't over. The plant became a political football for President Trump, who urged local residents not to sell their homes, because of jobs he promised to restore. He later rebuked GM for not building COVID-19 ventilators in a factory it no longer owned. (By that time, GM had sold the mothballed plant to Lordstown Motors Corp., a long-shot electric-truck startup.)
Now, nine-lives Lordstown is getting another chance to play a significant role in the automotive future. Whether it succeeds hinges on the biggest multibillion-dollar question in the global auto industry: Can GM, or any legacy automaker for that matter, transform itself into a true rival to Tesla, whose electric cars-and sky-high stock price-dominate the EV space? To do that, it'll need better, stronger, more-affordable batteries. That's where GM's Ultium project comes in.
Honoring its own promise to bring jobs back to northeast Ohio, GM, in partnership with South Korea's LG Chem, has begun building a US $2.3 billion battery factory in Lordstown. This joint venture, called Ultium Cells, will have the capacity to produce at least 30 gigawatt-hours of batteries each year-50 percent more than can emerge from Tesla's Gigafactory in Nevada. Huge as it is, that investment is just a small fraction of the $20 billion that GM will be pouring into electric and autonomous cars by 2025, en route to the all-electric future" touted by the company's CEO, Mary Barra.
GM's plan calls for building 1 million EVs a year by mid-decade, for both U.S. and Chinese customers. The first Ultium-powered model, expected to be out late in 2021, will be a GMC Hummer pickup, reborn as an EV with up to 1,000 horsepower. Once the symbol of unrepentant gas-guzzling, the Hummer should now pass muster at any Silicon Valley cocktail party with its electric power train and zero tailpipe emissions.
This electric Hummer will roll out of a revamped $2.2 billion EV plant in Detroit-the vanguard for 20 new electric models bearing the marques of Chevrolet, Cadillac, and Buick by 2023. Slated also for production is the Cruise Origin, a self-driving, ride-sharing EV from GM's autonomous-car subsidiary. And all of them will, of course, need battery packs.
The sprawling Lordstown battery plant, which will be big enough to encompass 30 football fields, is where GM aims to churn out 250 million Ultium cells a year by 2025. Those will be large-format pouch cells, a marked departure from the cylindrical-can cells Tesla and Panasonic produce for use in EVs.
Tesla originally packed 8,256 of its cylindrical 18650" cells (18 millimeters in diameter and 65 mm long) into the 100 kilowatt-hour versions of the Model S sedan and Model X SUV. These were only mildly reworked versions of the same Panasonic batteries found in many laptops-indeed, using off-the-shelf batteries was key to Tesla's startup strategy. Yet the batteries have proven reliable in their new role, holding up well for many charge-discharge cycles.
Video: Raymond DeRamo/Bug Eye Drone
To supply the latest Model 3 and Model Y, Tesla's Gigafactory began producing the more energy-dense 2170" cell, which has 46 percent more volume than an 18650 but is still barely larger than an AA battery. A Model 3 with a 75-kWh battery holds 4,416 of these cells.
In September, Tesla announced plans to move eventually to a larger, 4680" cell, which will hold five times as much energy as the 2170 cell it will replace. GM is taking a bigger leap in that direction: Its large-format cells each contain about 20 times the energy of Tesla's 2170 cell.
Each of GM's large-format cells includes a stack of planar electrodes, which are immersed in a polymer electrolyte and wrapped in an aluminum-polymer pouch. Those cells can be stacked vertically or horizontally within scalable modules. A pack containing from 6 to 24 modules will provide between 50 and 200 kWh, depending on the vehicle. The 200-kWh version will become the largest available for any production EV, with double the storage of Tesla's biggest pack.
GM's 200-kWh pack contains two stacks of modules wired in series for a total of 800 volts, allowing 350-kilowatt fast charging, enough to extend range by something like 160 kilometers (100 miles) in just 10 minutes. That matches the Porsche Taycan's industry-topping charge speeds. Single-stack, 400-V packs will permit charging at a still-robust rate of 200 kW. (The majority of Tesla's Superchargers are limited to 150 kW.) And whatever the configuration, GM will be tracking the performance of its battery modules with a cloud-based monitoring system [see EV Phone Home," below].
How much better are these upcoming batteries and the ingenious architecture that supports them, which GM calls BEV3, compared with GM's existing BEV2 models?
Consider the 2020 Bolt hatchback, built on the BEV2 platform. In my recent week-long test, the Bolt proved its ability to squeeze 417 km (259 miles) of range from a modest 66-kWh pack, up from 383 km in the previous version. That is similar to the 354 km of range for a standard Tesla Model 3 with a 50-kWh pack. But Tesla can manage 531 km from its longest-range Model 3, with 75 kWh aboard-and 647 km from its thriftiest Model S with 100 kWh of energy storage. GM had work to do to match or beat those statistics.
Tim Grewe, GM's global director of electrification and battery systems, says that Ultium 1.0 batteries offer 60 percent more energy density than those found in the Bolt. And that's just the start. The Bolt had a great lithium-ion chemistry, but we had to take it to the next level," Grewe says.
Doing so demanded a proprietary nickel cobalt manganese aluminum chemistry, one that reduces by 70 percent the amount of cobalt normally required, which is important because cobalt is the priciest element used in batteries and is often mined under inhumane conditions. Tesla is on a similar track toward low-cobalt cathodes for the cells destined for future Model 3 production in China. Rather than being cylindrical, those cells will be prismatic. But they will be packaged in aluminum housings instead of the laminate pouches used for GM's cells. Both designs aim to maximize energy content in a given space, though pouch cells lead the industry at the moment, with 90 to 95 percent packaging efficiency.
Grewe describes the cathode in a lithium-ion cell as a parking garage" for electric ions. The problem is that the cathode's oxide structure begins to break down after thousands of charge-discharge cycles. Doping the cathode with aluminum can help avoid degradation, as does adding certain kinds of cladding to the structure, while also boosting thermal stability, so all the parking spaces stay open," Grewe says. He affirms that such measures put the industry's much-discussed million-mile battery" squarely in sight, a battery that will be especially valuable for the upcoming autonomous Cruise Origin EV.

Those Ultium 1.0 batteries are key to the forthcoming Hummer EV, the high-end version of which generates a shocking 1,000 horsepower from a trio of electric motors. This Hummer should combine a 3-second rip from 0 to 60 miles per hour (0 to 97 km per hour) with commando-worthy off-road skills-and still travel about 640 km (400 miles) on a charge.
GM says even its smallest and most-affordable new EVs will have ranges of at least 482 km (300 miles), despite having packs as small as 50 kWh, about 25 percent less energy than the current Bolt. If you're not getting at least 300 miles from a new EV architecture, you're doing something wrong," says Andy Oury, GM's lead engineer for high-voltage battery packs.
It's not all about range and performance, though. Price is key. Because battery packs are so expensive, legacy automakers continue to lose thousands of dollars on every EV they sell. Even Tesla's minuscule profits have mainly come from selling emissions credits to rival automakers, not from selling cars.
GM is confident that the Ultium program will drive cell costs below $100/kWh, long the holy grail of battery development, hastening the day when EVs achieve price parity with fossil-fueled cars. But that's still a ways off: Prices for Li-ion cells may have fallen by 87 percent since 2010, according to analysts at BloombergNEF, but remained a daunting $156/kWh in 2019.
We haven't seen the bottom of the cost curve," Grewe says. Company executives estimate that battery costs are dropping 4 percent per year on average, with energy density rising by roughly the same amount. And GM has boldly announced that it will turn a profit on every Ultium-powered EV it sells.
Even as GM races to bring these new EVs to showrooms, the company is developing ways to produce even better batteries, some that contain zero cobalt and zero nickel. Much better performance could also be in store. At GM's EV Week in March-where reporters were offered sneak peeks of 11 upcoming EVs-the company showed a working prototype of a lithium-metal cell, built at its Tech Center in suburban Detroit. That lithium-metal battery could provide nearly double the energy density of Ultium 1.0 cells-boosting driving range to 800 or more kilometers-if it could be made to perform reliably in the real world, which is still a big if.
Better batteries alone can't guarantee success for GM or any other automaker looking to transition its fleet to electricity. They'll also need to produce cars that people really want, in everything from design to technology.
The Chevrolet Bolt was a solid first step in that direction for GM back in 2016. But the Bolt never really caught on, arriving just as the United States was fleeing small cars for SUVs. So GM will reverse the Bolt's self-effacing, Birkenstock approach with the decidedly in-your-face Hummer pickup (followed by the SUV), aimed at the same Silicon Valley Bro crowd that's gone wild for Tesla's prototype Cybertruck. GM plans to follow the Hummer with nearly 20 all-electric stablemates, including the Cadillac Lyriq SUV, a Caddy sedan, Chevrolet Silverado pickup, and crossovers from Chevy and Buick.
Tesla delivered about 367,000 cars in 2019, whereas GM sells 9 million around the world in a good year. But if you consider just electric vehicles, the tables turn: In the United States, GM sold just 16,400 Bolts in the last year, as Tesla raked in 223,000 enthusiastic customers for its all-electric lineup. GM must leverage its global scale and manufacturing know-how, if it intends to become a serious rival to Tesla.
To start, GM plans to simplify. Its full range of BEV3 offerings, from hulking all-wheel-drive pickups to perky front-drive crossovers, can be built with just 19 combinations of batteries and drivetrains. That compares with 550 combinations for GM's internal-combustion portfolio.
The jigsaw commonalities of BEV3, paired with Ultium battery modules, will drive down cost and complexity, Oury says. The packs incorporate a load-bearing, crash-worthy structure, cooling, a high-current circuit, and electronic sensors-all in an elegant, space-saving design.
To give one example of how simplicity matters, previous GM packs had fiendishly complex cooling systems, some that grew out of hydrogen-fuel-cell development. Pricey, one-off components hogged space, such as the 150 cooling fins used in GM's now discontinued Chevy Volt, a plug-in hybrid. At scale, that's millions of parts that couldn't be used on any other GM model, Oury said: For even 100,000 vehicles, that's 15 million fins per year, gone."
In contrast, the Ultium battery modules integrate their own thermal management, so each module brings along its own scalable cooling," Oury says. An aluminum plate with thermally conductive adhesive connects cells to a high-strength steel cold plate." Pouch cells are wrapped like a taco" to eliminate lower flanges, saving both cost and mass.
The single-height battery packs in most EVs require design compromises, Oury says. But GM can work around the usual constraints by being able to orient cells horizontally or vertically. That allows power-packed, double-stacked modules for beefy trucks, or slim, vertically oriented modules that boost range for lower-roofed cars without stealing passenger space.
Some Ultium-equipped EVs will squeeze 22 kWh below the rear-seat footwell alone, more than the plug-in Chevy Volt held in its entire pack. We call it a multiheight battery pack, and it's unique in the industry for these large-format cells," Oury says of the seating-friendly arrangement.
GM's $20 billion move to develop a giga-topping factory, unrivaled pack storage, and a line of 400-mile SUVs and pickups surely has Tesla's attention. But that competition might well be seen as a good thing, given the company's stated mission to spur the transition to sustainable energy. If so, Mr. Musk should be very happy this holiday season: GM has given him the gift of a serious rival. Batteries included.
EV Phone Home: GM will monitor its battery modules wirelessly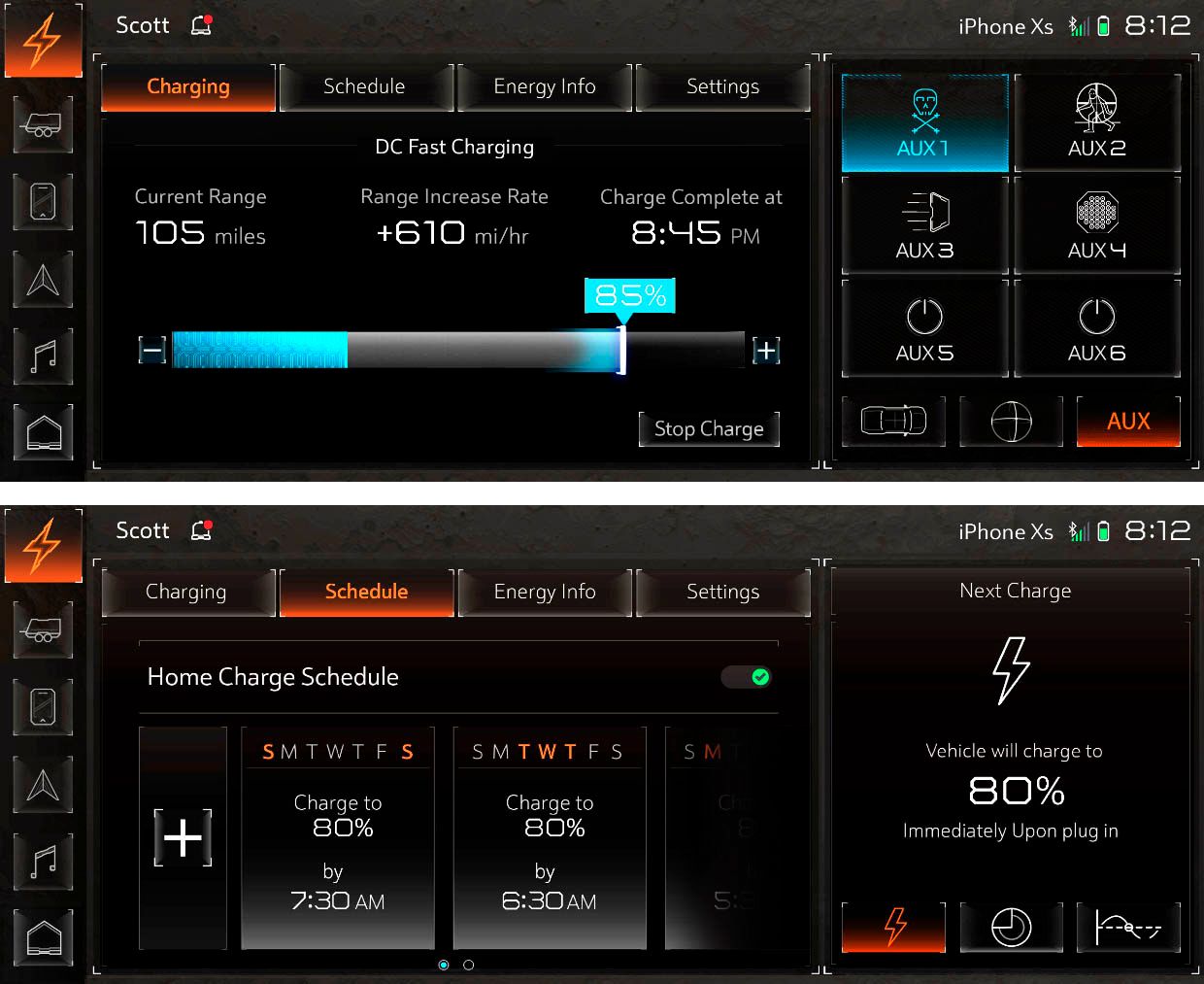
When a smartphone or laptop dies, what do people do? Some may have a new battery installed, but most take it as an excuse to purchase a new device.
It won't work that way for cars: The battery must last the life of the vehicle. To that end, General Motors has developed a wireless, networked battery-management system, the world's first for any EV.
Fiona Meyer-Teruel, GM's lead engineer for battery-system electronics, explains how the system-developed with Analog Devices-works. Instead of a tangle of wiring carrying signals to and from battery modules, circuit boards in each module will use integrated RF antennas and a 2.4-gigahertz wireless protocol (similar to Bluetooth, but using less power) to exchange measurements of cell voltages and other data with an internal battery-management computer. That computer in turn shares data wirelessly with a cloud-based system GM maintains. The upshot is thoroughgoing monitoring of all its batteries, from the factory floor to when they are zipping around the highways of the world.
And when these batteries reach the end of automotive life-spans, they can be reconfigured for grid storage or other uses. You can easily [repurpose] the batteries for a second life, when they're down to, say, 70 percent performance," Meyer-Teruel says.
Tim Grewe, GM's director of global electrification and battery systems, says the company's cloud-based system stores metadata from each cell. But owners will be able to opt for more-extensive monitoring if they choose.
That granular data can improve performance and drive down costs, teasing out tiny nuances between battery batches, suppliers, or performance in varying regions and climates. It's not that we're getting bad batteries, but there's a lot of small variations," Grewe says. We can run the data: Was that electrolyte a little different, was the processing of that electrode coating a little different? Now, no matter where it is, in the factory, assembling the car, or down the line, we have a record of cloud-based data and machine learning to draw upon."
This article appears in the December 2020 print issue as GM Bets Big on Batteries."
About the AuthorLawrence Ulrich, an award-winning automobile journalist, regularly writes about cars for many magazines, including IEEE Spectrum.