How NRG Energy Uses IIoT Technology to Optimize Asset Performance and Predict Failures
The post How NRG Energy Uses IIoT Technology to Optimize Asset Performance and Predict Failures appeared first on POWER Magazine.
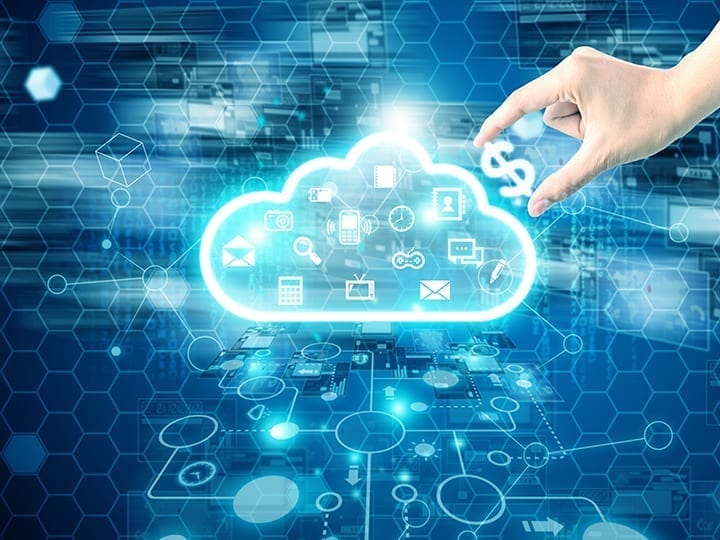
Industrial Internet of Things (IIoT) technology is changing how power plants operate. One generating station incorporated new wireless vibration sensors with data from its existing historian system to better identify and understand problems on a real-time basis.
NRG Energy is a leading power generator and retailer with 35 generating facilities producing 23 GW of power to help meet the needs of more than 3.7 million residential, small business, and commercial and industrial customers served through a diverse portfolio of retail brands. NRG has committed to cutting its carbon emissions in half by 2030, even as the company expects to continue growing.
NRG recognizes the role technology will play in this transformation and how Industrial Internet of Things (IIoT) devices can help improve efficiency, and optimize how power is produced and consumed. In a blog post on the company's website, NRG shared its vision of what IIoT connectivity can provide, which is, a real-time view of energy as it is generated and consumed, not just at a corporate level but at a utility and soon, perhaps, a grid level."
Several of NRG's generating plants are in Texas, which operates a competitive energy market through the Electric Reliability Council of Texas (ERCOT). ERCOT is the independent system operator (ISO) that controls about 90% of the electricity distribution in Texas. Unlike other ISO markets, which use longer-term forecasting, the prices in the ERCOT market are determined daily through an exchange, based on available capacity and demand.
The 3.7-GW W.A. Parish generating station, located about 25 miles southwest of Houston, is the largest power plant in the NRG fleet. These days, it needs to be available to respond to ever-changing load demand, because generating units designed to run at a steady baseload are now operating at variable loads, with some units even being stopped and restarted daily to meet demand at certain times of the year. Such flexible operation places new stresses on the equipment and makes failure detection more challenging. At W.A. Parish, IIoT sensors have been combined with process data to improve availability and reliability.
Continuous Improvement of the Asset Reliability ProgramEquipment reliability at NRG means the difference between meeting its power generation commitment or purchasing from competitors on the open market. NRG has an existing well-developed predictive maintenance (PdM) program, which includes infrared thermography, oil analysis, and vibration analysis, but the company sought to supplement its monthly walkaround data collection with more frequent readings under differing load conditions.
To better assess equipment condition, additional data collection was required, so the NRG team decided to add continuous wireless asset monitoring that would provide more frequent data and allow earlier detection of developing failures. Going wireless was desirable because wiring the sensors into the plant's distributed control system (DCS) would have made the program cost prohibitive.
The PdM team also recognized the benefit of combining asset condition data with historical process data from its OSIsoft PI System. The combination of the two systems was useful to both the PdM team and process engineering. The PdM team wanted to use process data to have a more comprehensive ability to detect failures. The process engineering team wanted to use the data to improve plant performance by understanding the impact of process variability on asset condition.
With their mutual interests in mind, the two groups decided to form a multi-disciplinary team to define the requirements and establish goals for the usage of continuous asset condition data. The requirements that they defined were:
- Cost effectiveness-wired systems were cost-prohibitive.
- Integrate with the PI System.
- Easy to deploy.
- Easy to use.
After considering various wireless systems, NRG selected Petasense's vibration motes and Asset Reliability & Optimization (ARO) system to monitor 13 critical pumps and motors, including steam- and motor-driven boiler feed pumps and condensate pumps, and a startup boiler feed pump that runs only during startup and shutdown. Continuous monitoring of these pumps provided consistency in the vibration readings, as several of the pumps operate at variable speeds and loads. The periodic nature of walkaround systems makes it difficult to take readings under consistent operating conditions. By including process data such as flow, speed, and load from PI in the analysis, the PdM team is able to more accurately determine an underlying failure.
The vibration motes collect vibration and temperature eight times per day, which is sent to Petasense's cloud-based software to provide on-demand alerts to the PdM team of developing problems. This allows for improved efficiency, as an alarm prompts examination. The ARO cloud provides a simple, trendable Asset Health Score, as well as detailed diagnostic tools needed to diagnose the underlying cause of problems.
The biggest benefit to the PdM team was peace of mind that comes with continuous data collection. During the first five months collecting and analyzing data, the PdM team achieved its goal of zero missed starts during the peak summer months. After five months, the units were taken offline to balance generating portfolio with demand.
Developing Greater Insights from Data CollectedThe team saw the frequent data collection as a way to improve plant performance. Each triaxial sensor provided multiple data points that could be brought in as tags to the PI Asset Framework. They uploaded all vibration and temperature data points collected from 29 sensors over a five-month summer run season.
With the combined historical asset condition and process data, the impact of process variation is visible on a single screen. For example, there is simultaneously visibility of the flowrate of water through a specific pump, and how it is impacting the vibration on that asset and overall power generated (Figure 1). This provides a visual and easy way to troubleshoot when vibration starts to increase-if there have been no process changes, they can determine that the asset may be developing a problem.
![]() |
1. This example shows data within the OSIsoft PI System that includes the combination of vibration and process data on a single screen. Courtesy: NRG Energy |
Another area that continuous asset condition data can improve NRG's PdM program is in determining whether a pump is running on its Best Efficiency Point (BEP). The BEP is defined as the flow at which the pump operates at the optimum efficiency for a given impeller diameter. When a pump is operating off its design curve, it will create problems such as premature bearing and seal wear, and cavitation.
As a pump is cycled up and down, it is often running off the design curve, meaning it is not moving enough, or moving too much, water. NRG can see by looking at the vibration during ramping between low and high loads whether the pump is off its design curve and modify operating parameters or alert operators to manage pump operation appropriately until the problem can be corrected.
Next StepsEvery summer run season comes with new challenges. NRG's PdM team will continue using wireless technology to provide more frequent readings and complement other systems. The more frequent nature of continuous wireless vibration data helps to provide insights that would be difficult to obtain with a walkaround program and provides confidence that there won't be any missed starts.
As NRG looks to IIoT technology to improve generating performance, the company is considering pushing live asset condition data to PI instead of batch data. This would allow closer monitoring and increase the value of collecting data-using data to move beyond failure prediction to operational improvement.
-Calvin Arnoldis predictive maintenancesupervisor at NRG,Mitch Levingsis an engineer at NRG, andJuli Iacuaniellois marketing director with Petasense.
The post How NRG Energy Uses IIoT Technology to Optimize Asset Performance and Predict Failures appeared first on POWER Magazine.