Why Pump Energy Savings Should Matter to Utilities
The post Why Pump Energy Savings Should Matter to Utilities appeared first on POWER Magazine.
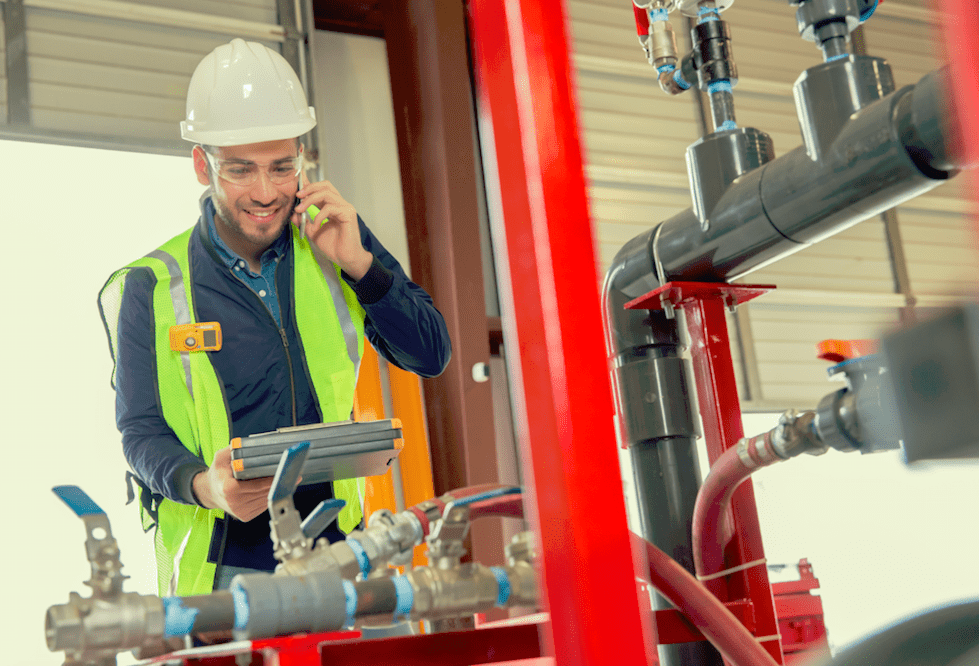
Utilities have a two-fold relationship with energy efficiency. On one side, public and private utilities gain from finding efficiencies in energy usage to reduce costs in their own operations-just like many other businesses. The U.S. Department of Energy's 2002 Motor Market Assessment established that pumping systems offer the greatest optimization potential of all types of fluid systems, offering savings up to 75% with an average net savings of 20.1%. Since then, technological advancements may have boosted the potential for energy savings even more.
On the other side, utilities are uniquely positioned to encourage energy savings among their customers through incentive programs. Now, the types of rebate initiatives associated with lighting can also be applied to pump systems utilized in clean water applications. So, how do utilities grow energy savings on both fronts? It takes a dual strategy that prioritizes optimization and energy efficiency on the operations side and building a comprehensive incentive program on the business side for their rate payers.
Enter the Energy Rating ProgramWhat if commercial builders, utilities and other fluids engineers could unlock 162.9 terawatt-hours of energy savings and subsequent cost savings of $14.6 billion? According to the Environmental Protection Agency's greenhouse gas equivalency calculator, that greenhouse savings would represent carbon sequestered by more than 1.9 billion tree seedlings grown for 10 years. It's equivalent to the CO2 emissions from more than 12.9 billion gallons of gas consumed, and a year's worth of electricity for more than 13 million homes. That potential lives in the pump systems that heat and cool buildings, generate power, run industrial plants, and irrigate farms. By re-evaluating current pump systems and implementing more energy-efficient solutions, companies can generate long-term savings without sacrificing reliability.
Energy and cost savings will vary depending on a variety of factors for different settings, but properly selecting pumps and ensuring they have an HI Energy Rating Label will increase the savings. For example, utilizing water pumps with an HI Energy Rating of 50, in a typical mid-sized commercial building using 20 pumps with an average 15-hp rating, you could expect to see a savings of 411,000 kWh per year, or $37,000 per year. In an industrial facility using 40 pumps with an average 15-hp rating, you could see a savings of over 1.3 million kWh per year, equating to an approximate savings of $117,000 per year.
Where Optimization Meets Energy EfficiencyThe Hydraulic Institute (HI) defines pump system optimization as follows:
The process of identifying, understanding and cost effectively eliminating unnecessary losses while reducing energy consumption and improving reliability in pumping systems, while meeting process requirements, minimizes the cost of ownership over the economic life of the pumping systems."
Getting there is a process that requires a few steps. For utilities to mine energy efficiencies while optimizing their clean water pump systems, they need to:
See the Bigger Picture. First, it is important to understand that all pumps are selected to meet system requirements-never the other way around. Once the application is determined, engineers can assess criteria, which varies greatly between different uses. For example, a condensate pump intended to pump saturated water will require different flow rates and design attributes than a cooling water pump. The energy consumption required for any system depends on the flow rate of the entire system including the pressure (head) and how often the pump(s) are operating.
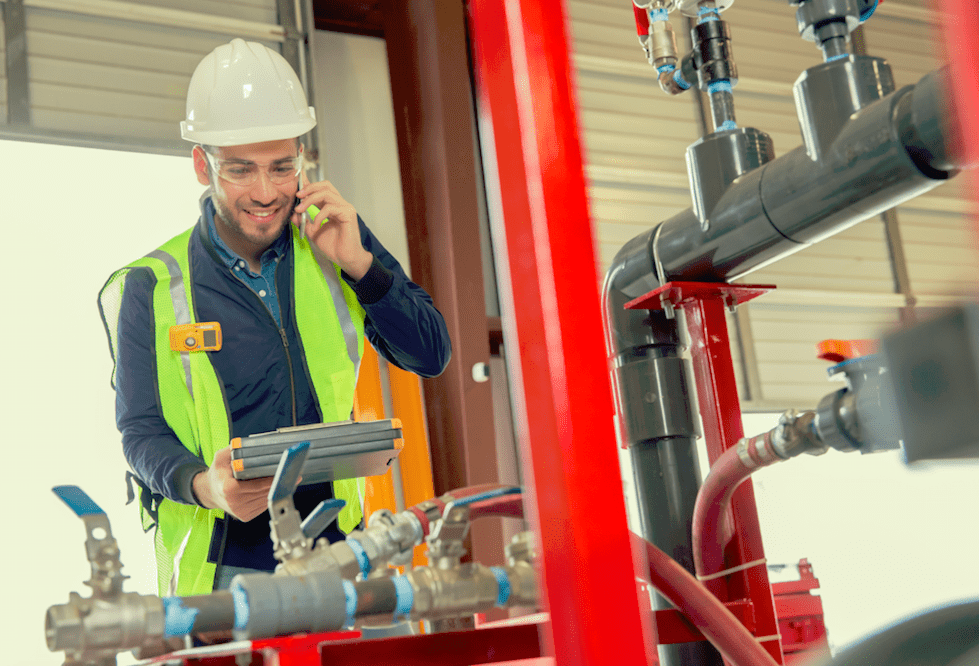
By reviewing the entire system and not just the individual pump, engineers and specifiers lay the foundation to select the right pump or system for the application and the proper control methodologies to manage the flow of energy and ensure reliability.
Build the Best Assessment. To achieve optimization in an existing pump system, it's important to start with an assessment. Proper assessments provide a host of results to justify costs for improvements to the system's design, control, operation, and maintenance. Improvements to pump systems for optimization can result in reduced system head (pressure), reduced system flow rate or operating time, more efficient equipment or controls, and/or improved installation, maintenance or operation procedures.
This assessment should be built in three levels. First, the paper audit begins with a pre-screening and gathering system information for pumping systems. This data draws from equipment information, control schemes, operating parameters, reliability issues, and performance curves. With this information, potential for energy savings can be quantified, and recommendations for level two or three assessments can be made.
Level two assessments entail physically measuring the system for a specific amount of time in order to provide a snapshot of how the system is operating. It is important to note, however, that a level two assessment will not be sufficient for systems with significant variable flow or pressure over time. Level three assessments include a longer-term system measurement to establish how the system operates over a period of time. This assessment documents how the system varies so that the complete picture can be seen. This type of assessment is accomplished with the use of in situ monitoring combined with any available historical site data.
Make Energy Efficiency Part of the Cost Assessment. A variety of factors for different settings can affect energy savings resulting in long-term potential for significant cost savings. Upfront costs can often deter specifiers from considering overall savings throughout a pump's lifecycle.
For a typical pumping system, 65% of the Total Cost of Ownership (TCO) is related to energy and maintenance, while the initial cost only accounts for 10%. For example, a double-casing between bearing multi-stage pump (BB5) will cost more than an axially split multistage pump (BB3), but the BB5 is designed for high reliability in high-pressure and temperature applications. Trying to reduce cost upfront by extending the pressure and temperature range of the BB3 pump could result in a much higher TCO due to maintenance costs. Enhancing the energy efficiency of pumps can also go a long way to save on utilities. To help identify the most efficient pump for the system requirements, the Hydraulic Institute (HI) offers an Energy Rating Program for select pump types below 200 horsepower.
Building an Assessment Team. It's also important to understand that collaboration is essential when undergoing pump system evaluations and assessments. Because of the complexity of such systems, the assessment team should be comprised of personnel from cross-functional backgrounds including:
- Host organization representative that has management support and overall responsibility and ownership
- Assessment engineer with broad pump system analysis competencies
- Specialists on system processes, operations and functions
- Specialists on the maintenance practices and history
- Specialists who can provide the team with cost data
There are certified professionals who can assist with this, known as a Pump Systems Assessment Professional (PSAP). These experts have completed HI's PSAP program, a certification program that sets the standard for the discipline of pump systems assessment and the use of pump system optimization techniques. Professionals with the PSAP certification have demonstrated that they have the requisite knowledge and experience to perform high-quality pump system assessments.
Identify Optimization Opportunities. To be accurate in the determination of energy consumption, the next step is to evaluate opportunities for efficiency gains in system flow, pressure/head, and pump, motor or drive efficiency, and operating time. In existing systems, the energy requirements can be measured over time as a benchmark to aid in identifying where energy consumption can be optimized.
The time period for this process may need to account for seasonal variations, so an entire year may be needed. In contrast, a batch process for a system's specific task (e.g., provide 100 gallons per minute [gpm] of water around a reactor to maintain 200 degrees Fahrenheit for one hour), will be a much shorter benchmark because the periodic operation is known and consistent.
Remember that Footprint Matters. Space availability and the pump system's footprint are an important factor in the selection process. Given the accessible space, a frame mounted (pump has its own bearing frame), close coupled (motor bearings carry pump loads), or inline pump may be appropriate based on the power and speed requirements. However, these options will not have an interchangeable footprint.
Think Smart. Consider utilizing smart pumps that integrate a Variable Frequency Drive (VFD), which have the pump performance programed in from the factory, instead of retrofitting with a separate VFD. Both solutions reduce the pump speed to meet a designed set point for greater efficiency and cost savings. However, the more conventional approach of installing a separate VFD requires the additional legwork of installing the VFD near the pump, installing instrumentation and connecting it, and programing the VFD, which can also create opportunities for error. Additionally, having the performance of the pump programed into the VFD allows control based on the VFD speed and power, without other external instrumentation.
Carefully Assess Flow Requirements and Fluid Properties. Fouling, corrosion and erosion of pumps and pipes over time can be attributed to biological, chemical, and abrasive factors, so understanding fluid properties can be critical to avoid failure or the need for continuous and costly maintenance. Additionally, fluid viscosity and temperature are also critical considerations in the pump selection process.
For example, positive displacement pumps are often used in the industrial and petrochemical sectors and in many applications with viscous product. These pumps come in many designs, but generally deliver consistent volume with every rotation of the shaft, efficiently handling viscous liquids and delivering a nearly consistent flow against low or very high pressures. A benefit is that adding a variable speed drive allows these pumps to be dialed into a very precise flow rate, or possibly have their flow extended to meet future system demands.
Forging an Energy Savings ProtocolUtilities-whether private or public-shouldn't stop their energy savings mission at their own facilities and operations. With the new U.S. Energy Conservation Standard for certain clean-water pumps in effect, utilities can encourage further energy savings with the creation of deemed incentive programs for the energy savings of pumps that exceed the industry baseline. This undertaking is made easier with HI's Energy Rating program. In 2020, HI launched its Utility Resources. This collection of tools and educational materials can drive the development and implementation of incentive programs that advance pump system energy savings.
Such programs can also help utilities meet regulatory goals and provide other value-adds to customers. HI's Utility Resources build upon the association's Energy Rating Program which underpins incentive programs by streamlining the way pump manufacturers and distributors communicate energy efficiency.
The toolbox includes the following:
For Program Design & Management:
- The Deemed Measure List and Technical Resource Manual (TRM) Workbook are housed in a single customizable Excel file tool providing one-stop-shops for pump energy savings calculations, measure identifiers, and all the necessary technical data.
- Subscription to the HI Energy Rating Database to inform qualified product lists.
- The Utility Program Design Memorandum provides technical background on pump efficiency programs and summarizes program strategies to consider when initiating new rebate programs.
- The FAQ & Lessons Learned summary outlines best practices and key learnings from past programs to help utilities promote the most efficient solutions, work with pump market actors, and develop effective marketing materials.
- The Efficient Pump Utility Program Database identifies existing utility programs that promote efficient pump systems and circulators so utilities and other users can gain inspiration from successful and efficient models.
- The Pump Systems Matter (PSM) Training Memorandum details how the trainings provided by HI's Pump Systems Matter (PSM) and Pump System Assessment Professional (PSAP) course and certifications can equip utilities professionals to better understand system nuances.
For Program Promotion:
- Pump System User Profiles help utilities professionals understand the motivations and challenges of pump system users to help them better target programs, marketing and rebates to customers.
- Key Messages utilities can use to articulate the value of energy savings and pump efficiency to various stake holders.
- Communications Tools, including flyers, promotional slides and other materials that can boost education and awareness of programs.
Amid the uncertainty created across the United States-and the world-it can feel like sustainability initiatives have taken a back seat. However, energy efficiency and cost savings are often intrinsically linked. Utilities remain uniquely positioned to gain energy efficiencies in their own operations while launching incentive programs that encourage other companies to seek more energy efficient clean water pump systems. Learn more at www.pumps.org/EnergyEfficiency.
-Matthew Derner is Manager, Business Development, Pump System Programs for the Hydraulic Institute. For more information on the Hydraulic Institute, visit www.pumps.org.
The post Why Pump Energy Savings Should Matter to Utilities appeared first on POWER Magazine.