The Human Side of Digital Adoption
The post The Human Side of Digital Adoption appeared first on POWER Magazine.
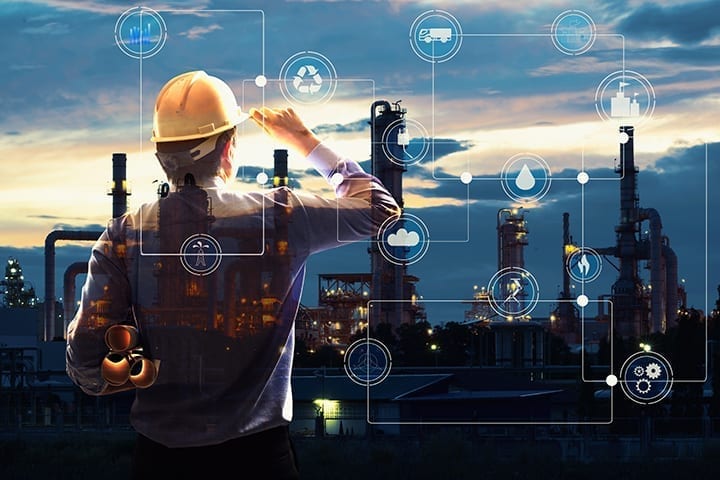
A pervading theme at the ongoing 5th annual Connected Plant Conference has been to explore the human side of digital adoption. Attendees have so far heard from several experts who are deeply involved in the future of the power plant workforce.
Steven Ford, Compliance and Support manager at Southern Co.'s Plant Barry, in his presentation during a session on Tuesday outlined one underlying problem starkly: Plant workers will almost always prefer familiarity, which makes technology adoption-no matter how promising it may be-difficult to achieve. You've got to be able to understand the vision for where this technology fits inside your organization," he advised. Secondly, you've got to be able to share that vision with a purpose." And third, you have to step back and assess your organization" to begin to identify the jobs of tomorrow and the people who can do them passionately. Passionate people build things so much faster," he noted. They believe in the vision, and they don't see a hurdle as a stopping point. They see a hurdle as a learning opportunity."
Ford illustrated his points with an array of historical examples. The light bulb, he noted, was invented before the grid-and it took education to envision the enormity of its application, he said. On the other hand, despite costs and constraints related to the first electric vehicles, the folks that bought them and used them were passionate about their expansion.
Stephen Kwan, director of Product Management for Power Generation/Grid at Beyond Limits, in his presentation noted that many power plant engineers and operators have worked 30 years or more acquiring a wealth of information. But that domain expertise" has been difficult to capture in a repeatable way. To aid plant decision-making by future generations, Beyond Limits is working on cognitive systems that embed human knowledge, he said. These systems represent wisdom in a variety of forms, educated from domain knowledge and experience," but they can also reason through general classes of problems, including those not limited to specific use-cases.
You can think of it as a cognitive AI [artificial intelligence] solution framework. You take various inputs, and we implement AI on top of the traditional data science, then we incorporate human reasoning on top of that. Then, we'll provide outputs including suggested operational setpoint and also action," Kwan explained. So, in effect, what we have is a digital twin of the physical space model-with the later AI on top-that can take into account trade-offs in various combinations."
Finally, Matt Buck, senior technical leader at the Electric Power Research Institute, pointed both to adaptability and knowledge loss as concerns afflicting the power industry, which is seeing a rapid transformation. When I think about this, and I go back to my days as an operator at a coal plant, it was still the old, pneumatic controls and the old hand-piston grips, the vertical gauges," he said. Now, all of a sudden, we have infinite control of valves, pumps, motors. We can see temperature, pressure changes instantly," he said.
However, even though modern power plant workers tend to be younger and have more digital experience, getting digital work programs to stick has been difficult for utilities, Buck said. Multiple surveys have said that up to 40% of the field workers' time is spent either managing paper or looking for information. So, if you get rid of the paper aspect, and you put the information at their fingertips, then you got 40% more efficient work," he said. But to make that happen, you've got to have a bold enterprise," he said. It will take an evolving interaction of personnel and technology. The utility of the future cannot be built alone by workers of the past unless they are agile learners who can untether themselves from traditional ways and embrace new technologies," Buck said. Current employees must be complemented by new talent such as data scientists, engineers, and analysts."
During another session on Monday, Marco Sanchez, vice president and head of Intelligent Solutions at Mitsubishi Power, a major power generation equipment supplier, outlined his company's efforts to improve reliability, sustainability, and resiliency through improved power plant operations.
A 500-MW power plant, regardless of who's making the best turbine, the best steam turbine, the best boiler, you're looking at 50 to 60 trips per year" stemming from balance-of-plant systems, Sanchez said. To resolve this issue by improving component performance, Mitsubishi Power invested in T-Point 2, a gas turbine validation facility that has an ultramodern, real-world grid-powering arrangement.
The most innovative feature of the T-Point 2 plant is the integration of Mitsubishi Power's TOMONI technology, a customizable suite of user-driven digital power plant solutions fueled by cutting-edge analytics and Mitsubishi's vast experience. It turns a mountain of big data into valuable actionable insights that can increase power plant efficiency and profitability, said Sanchez. With TOMONI, T-Point 2 is poised to become the world's first autonomous combined cycle power plant.
While T-Point 2 is currently validating the next JAC model, a gas turbine with an air-cooled combustor, as well as the building blocks to an autonomous power system, the plant has begun using TOMONI Voice, an Alexa-like intelligent voice assistant. Mitsubishi Power says it is also using TOMONI Voice elsewhere in Japan, as well as with select power plant owners" in the Americas. TOMONI Voice leverages artificial intelligence tools to streamline access to essential data, Sanchez explained.
Sanchez demonstrated TOMONI Voice for attendees. First, he asked the tablet-like device, What is the autonomous power plant?" The device responded: The autonomous power plant will be the world's largest energy system that integrates energy storage and advanced power generation technology together."
To demonstrate the device's designed use to help power plant operators quickly access equipment documentation, Sanchez then asked the device to call up specific parameters for a lube oil system. The device responded that it had found the information, as well as other related material for the same system."
Sanchez said TOMONI Voice's other capabilities will allow Mitsubishi Power to communicate with its customers, including to provide options for online troubleshooting. This is not there to replace your control system," he said. It's a digital assistant to help your operation teams minimize alarms, specifically eliminate maintenance, and eliminate trips. Why? Because we want to maximize the sustainability and the resiliency of these energy systems."
-Sonal Patelis a POWER senior associate editor.
The post The Human Side of Digital Adoption appeared first on POWER Magazine.