Overcoming the Top Three Hurdles to Eliminate Flaring
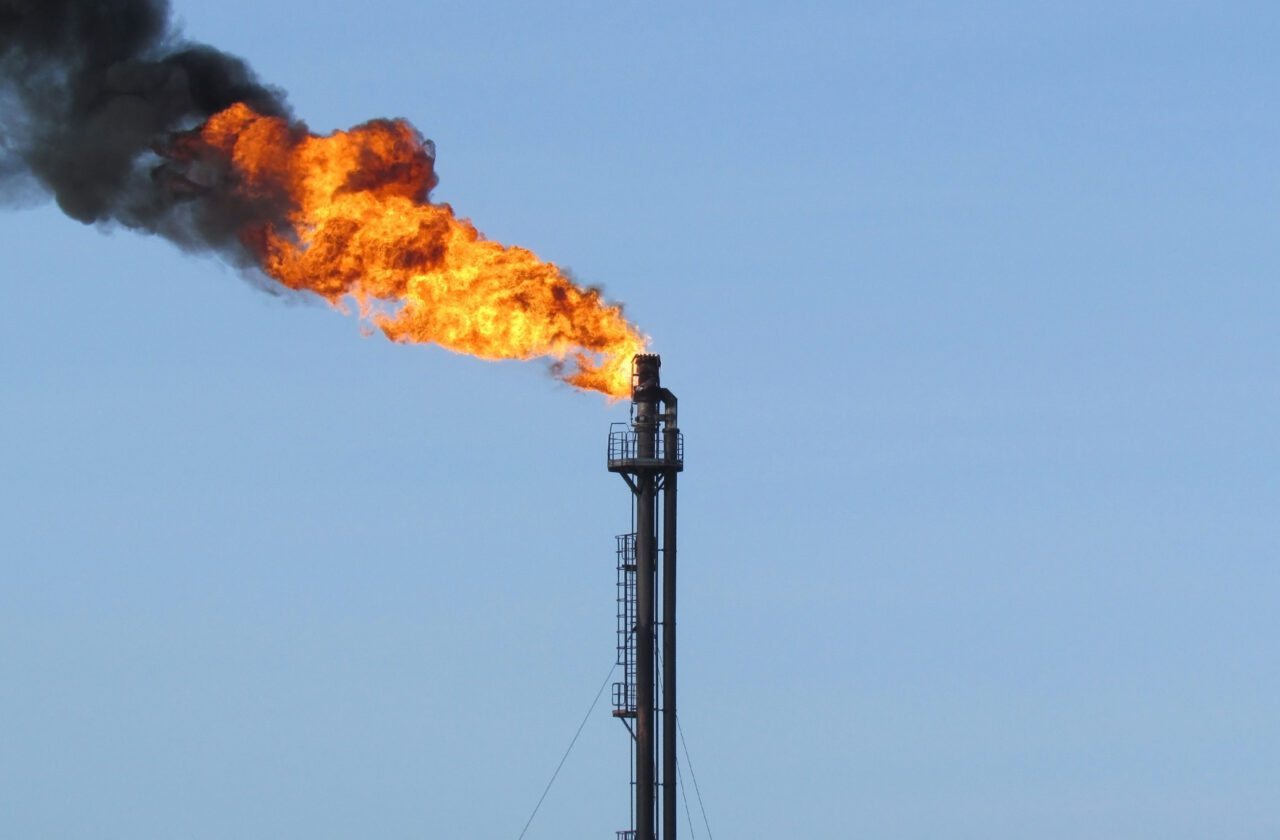
Despite exacting a heavy environmental and financial toll, routine flaring remains a persistent practice in the oil and gas sector. This gas could be captured and used for productive purposes, but a lot of it simply isn't. While flaring levels are down 5% from 2019, this is still a huge amount-142 billion m3/yr in fact. This wasted gas is the equivalent of 5,000 MW of power over 10 years, enough to power millions of homes.
At Aggreko, we live by the conviction that there is a technical solution for every flare. The real challenges are more prosaic, practical, and financial. With that in mind, here are the three most frequent hurdles we encounter with flare gas to power projects, along with how to solve them.
Geographic LocationThe most frequent objection to utilizing flare gas is that geographic constraints make it impractical or uneconomic. For example, imagine a production site located miles away from the nearest gathering pipeline. The associated petroleum gas (APG) is a by-product of the oil extraction, and something must be done with it to maintain production levels. Without takeaway infrastructure, or a way to use the gas onsite there and then, it's a waste product that must be flared.
Notice there are two key factors there: takeaway infrastructure and an onsite use. Those are the two variables in the whether-or-not-to-flare equation that seem fixed but can in fact be tweaked to avoid the need for routine flaring.
Let's take onsite use first. Remote oil and gas operations that are stranded from takeaway infrastructure are also often remote from power grid infrastructure and rely on onsite generators or turbines to power operations including artificial lift. Sometimes, these run on diesel, a fuel which must be transported to site at significant expense and is more carbon intensive than gas. The logical first step, then, is to use the produced APG to displace that liquid fuel, either entirely or partially-it's a practically free fuel source after all.
The trickier decisions come when there is still excess gas that can't be used this way. What to do then, if not flaring? The list of answers to this is really only limited by the extent of human ingenuity. For example, we have worked on projects where we built a full modular power station onsite, and then took it upon ourselves (on behalf of the local government) to build out the grid infrastructure to export the power. Alternatively, if you can't take the gas or power to end-users, you can bring the end-users to the gas and power. Bitcoin mining operations and data centers are easy operations to co-locate and are always looking for reliable sources of power.
If the gas is in excess to what is needed onsite, a virtual pipeline could be employed. The concept of virtual pipelines" has become more popular in recent years, with advances in midstream technology making it more practical to transport the captured gas by road either in a liquid or compressed state, negating the need for fixed, expensive infrastructure.
The thing in common with both approaches is that they require a solutions-oriented partner with significant engineering capability and experience. The oil and gas business is a commodity business with fortunes tied to the price of oil. But a commodity equipment provider is not what is required here-operators need a partner with the experience and engineering capability to put together a business case and back it up with technology.
Gas QualityAnother objection we frequently hear is that gas quality is often poor or inconsistent. There is truth to this. Too many conversations treat natural gas" as a homogenous substance, but like crude, it appears in all different grades and compositions. If you run poor quality gas through a generator not designed for it, you may quickly be facing power outages.
However, technology has improved on two fronts to solve this problem. On the one hand, modern gas generators are capable of running on a wider range of gases without compromising performance or durability. On the other, pre-treatment units have improved considerably in terms of capability and cost-effectiveness, and will continue to do so. Additionally, monitoring technology to measure the specification of the gas, and adjust the operations of the generators accordingly, can help to manage fluctuations in gas quality and composition over the lifetime of a well.
The technology is now available, and once again, it comes back to working with a solutions-oriented partner that can test the gas at the site, design a right-sized solution for the specific situation, and present a compelling business case to the operator.
Changing Production ProfilesIt isn't only quality of gas that can fluctuate over time, though, it's also volume, and this is the third hurdle to overcome. It is common for the gas production profile to change. That's not a problem if you're flaring, but if you've built a business case around powering operations or a data center, for example, then surely you need a bit more certainty that you will have enough (and not too much) to keep the lights on?
Again, the answer here is an intelligently designed, site-specific solution. Possible technologies could include buffer gas tanks to store excess gas in times of plenty for later use or utilizing virtual pipelines to bring in supplementary gas when required. Or it may be better to convert the excess gas to power and store in batteries instead, leveling out power peaks and troughs when needed. It may even be that a combination of the above is the best fit.
What is clear, however, is that there is no technical justification for routine flaring left, and the economic and practical justifications are shrinking by the day.
-Billy Morley is global head of Oil and Gas with Aggreko.
The post Overcoming the Top Three Hurdles to Eliminate Flaring appeared first on POWER Magazine.