Water, Heat, Metal: A Crucial and Difficult Dance
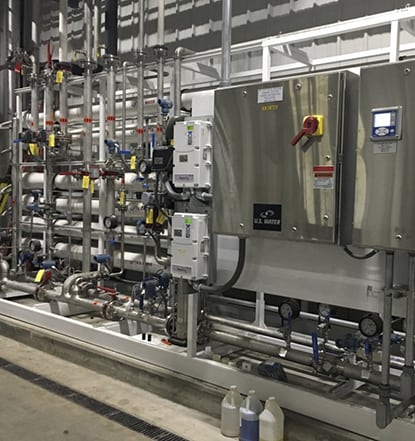
Proper water chemistry has always been important for dependable steam plant operation, but it may be even more critical today due to changes in operating routines and increased plant cycling. Failure not only affects plant reliability, but also personnel safety.
Water, heat, metal-all fundamental elements in steam electric power plants. The first of these is water, which some have called the lifeblood of steam power. And all three must interact properly for both plant performance and plant safety. That's been a priority for many years.
For steam plants," legendary water chemist Otakar Jonas (1933-2009), PhD, PE, and founder of Jonas Inc., wrote in POWER magazine more than 20 years ago, there is perhaps no more important O&M [operations and maintenance] fundamental than the production and maintenance of high-purity water-whether you are running a 30-year-old coal-fired plant, a nuclear station, or an advanced combined cycle."
Jonas laid out the effects of neglecting proper water chemistry as follows:
- Erosion/corrosion of carbon steel piping and other components.
- Boiler tube failures (Figure 1).
- Deaerator weld cracking.
- Pitting, corrosion fatigue, and stress corrosion cracking of low-pressure turbine blades and blade attachments.
- Copper deposition in high-pressure turbine blades, causing loss of megawatts.
- Solid particle corrosion.
![]() |
1. There are three main boiler tube failure mechanisms: waterside, fireside, and general. It's always important to understand the cause of failure. If water chemistry was a factor, corrections must be made to prevent future problems. Source: POWER |
Is that still the case? Yes," said Brad Burns, who manages the Electric Power Research Institute's (EPRI's) boiler and turbine steam and cycle chemistry program (Program 226). Maybe even more important."
Burns told POWER that the changing face of the electric generating market, including the increased spread of renewable generation, and the rise of use of heat recovery steam generators in combined cycle gas plants, has complicated water chemistry control. Fossil plants must cycle more often, he said, and often run at lower loads than they were designed for. They may have to come offline for short periods and then come back into service quickly to follow load. These circumstances add complications to chemistry control."
Additionally, many older fossil units are facing retirement; yet, they need to run reliably and economically until their demise. Outages due to corrosion impacts, which can be expensive to remedy and take plants out of service, makes chemistry even more important."
A third factor is that utilities faced with reduced and less predictable loads, and an impetus to get the plants to their retirement dates, often don't have the resources they once did. Many don't have onsite personnel formally trained in chemistry."
Another factor is that plant management is often under financial pressure to cut costs as once-dependable revenues become less reliable. Utilities are having to do more with less," Burns said. That can mean reduced attention to water chemistry control and less understanding of the warnings that come from monitoring indicators. Without proper training, operators may overlook problems until subsequent damage presents itself.
Alex Filar of Fossil Consulting Services Inc. said, Poor water chemistry control can lead to deleterious effects on equipment uptime, plant budgets, and most importantly personnel safety."
The Special Case of Nuclear Plant Water Chemistry While nuclear plants, which are steam plants, have the usual issues with water chemistry, they have an additional chemistry issue: radiation. A standard description of the issue says, The intense radiation inside the core of an operating nuclear reactor produces several chemical effects on the reactor coolant itself and on substances dissolved in the coolant." The Association for Materials Protection and Performance, a newly created organization representing two previous groups for the paint and coatings industries, recently said, Nuclear and conventional plants have many components in common: the boiler, steam drum, turbine, condenser, and feedwater heaters. In nuclear plants, however, most of these components, with the possible exception of the condenser, are made of austenitic SS [stainless steel], or some other nickel-chromium-iron alloy to minimize corrosion products. Low corrosion is desired, because if corrosion products become radioactive by transport through the reactor core, they constitute a radiation hazard to personnel when deposited again in areas remote from the core. In addition, when a water system surrounds the core, whether to generate steam directly or indirectly, specific problems arise from irradiated water." In the 1980s in nuclear reactors, the combination of usual water chemistry issues and radiation produced an outbreak of what the scientists describe as intergranular stress corrosion cracking," with the usual acronym of IGSCC, predictably pronounced igscoc." A technical report in 2012 summarized the understanding of IGSCC, which was first observed in small bore piping using sensitized 304 stainless steel fairly soon after BWRs [boiling water reactors] started operation. Laboratory studies showed that impurities increased IGSCC rates, and in fact water quality in BWRs gradually improved in the early 1980s. However, the same studies found IGSCC in high-purity oxygenated water typical of good BWR operations." The IGSCC issue also plagued pressurized water reactors. Since then, the industry has largely understood the issue, and adopted practices to identify and deal with the special chemistry requirements facing nuclear plants. |
One of the driving events that focused industry attention on water chemistry (see sidebar) in steam plants came in late 1986, when a corroded pipe elbow in a secondary feedwater pipe at the Surry nuclear plant in Virginia burst (Figure 2). The pressurized water flashed to steam, killing four and taking the plant out of service for an extended period.
![]() |
2. An artist rendering of the 18-inch-diameter pipe elbow that failed at the Surry nuclear plant on Dec. 9, 1986, killing four workers, is shown on the left. The elbow positioned on a flat surface after removal showing the relationship of fractured sections is on the right. Source: U.S. Nuclear Regulatory Commission |
A 2018 paper from the German energy company Uniper Energy, a spin-off from the giant utility EON, outlined the threats that poor water chemistry represents for steam plants. The problems include: flow-accelerated corrosion, hydrogen damage, acid phosphate corrosion, caustic corrosion, waterside deposits, corrosion fatigue, pitting, overheating, and stress corrosion cracking."
The EPRI ApproachEPRI has long published guidelines for water chemistry control. According to EPRI's Burns, the research institute is now focused on scientifically validating those guidelines, largely originally formed by consensus among the scientists. My research program is trying to take a scientific approach to validate [the guidelines]," he said.
We now have the technology to really get down" to the basic chemical and physical confirmations of the EPRI advice. That includes understanding when does active corrosion begin," Burns said. That should give operators more confidence that their instruments are not giving false positives.
A second approach in EPRI's water chemistry program is training plant operators, who may not have enough knowledge and experience to respond quickly to chemistry problems. One of the gaps," he said, is that operators don't have all this chemistry stuff memorized and have less experience" with water chemistry.
So, EPRI is offering practical exercises" for plant operators. These are not the traditional utility training approach, which has been to take operators off-shift and put them in a classroom for eight hours, inundating them with material that they may find hard to digest and retain. The new approach is short, repeated, and interactive sessions, at half an hour or less, to provide information to them and help them walk through validation" of the signals they are getting from their instrumentation. These are done more frequently and for shorter periods."
Another aspect of EPRI's approach to water chemistry is applying cyber tools to develop smart chemistry alarms. In 2018, Ohio-based giant utility holding company American Electric Power (AEP) used EPRI research to install smart chemistry alarms in two large power plants-the Lawrenceburg Power 1,096-MW combined cycle gas plant in Indiana and the 1,300-MW supercritical coal-fired Mountaineer Power Plant in West Virginia.
AEP Chemical Engineering Manager Doug Hubbard said, To reduce the amount of time equipment on the cycle sees contamination when it occurs-thus reducing the risk of long-term damage-an operator needs to recognize the contamination is real and what actions need to be taken. The smart alarm system determines for the operator if the contamination is real and immediately provides the operator the actions to be taken; thus reducing the amount of time cycle equipment is exposed to the contamination event. This reduces the risk of long-term damage to equipment."
Film-forming Chemical ProductsOne controversial element of water chemistry control is film-forming chemicals." These are chemicals, some based on amines (ammonia-based) and others on proprietary formulas, that are designed to form a barrier between the plant's metal components and the water, preventing or slowing corrosion. They have potential, as they may prevent outages and shutdowns, which can be very costly once flow water is stopped or slowed and dissolved oxygen concentrations increase.
An example is Nalco Water's POWERFILM 10000 product. The company, an Ecolab subsidiary, claims, When a boiler system shuts down, it cools, drawing a vacuum. Air and non-condensable gases enter the steam cycle. The combination of heat, moisture and oxygen drive a powerful corrosion mechanism. POWERFILM 10000 was designed to protect these systems. It shields the base metal of the boiler system from oxygen attack, resulting in significant improvement in corrosion protection during cyclic operations and unit outages. This helps reduce startup time from unit outages, protects boiler system assets and improves system availability."
So far, the performance record is mixed. Robert Barthlomew, PE, an engineer with the Baltimore water chemistry consulting and laboratory services company Sheppard T. Powell Associates, told POWER that the new and proprietary filming products have worked for some companies, but not for others. He added, It's not cheap stuff."
EPRI's Burns told POWER that film-forming products have been around for more than 20 years. They treat while online to reduce corrosion while offline. We've seen some good results, we've seen some not so good results, where the extra costs are not economic."
In 2016, an EPRI assessment found, Film-forming product treatments are being considered as a new method of improving power plant corrosion control. However, these new treatments have limited data describing their impact on corrosion processes. The effects of factors such as temperature, water chemistry, and tubing alloy on a filming product's corrosion mitigation are largely unexplored."
-Kennedy Maizeis a veteran energy journalist and long-time contributor to POWER magazine.
The post Water, Heat, Metal: A Crucial and Difficult Dance appeared first on POWER Magazine.