A Japanese Project Demonstrates a Carbon Neutrality Pathway for Coal Power
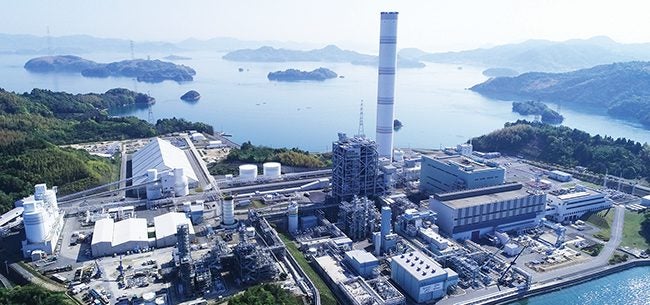
Osaki CoolGen Corp.'s complex three-phase demonstration project in Hiroshima Prefecture seeks to achieve highly efficient coal-fired power generation with near-zero emissions by integrating carbon capture-ready coal technology with a fuel cell.
When the Intergovernmental Panel on Climate Change (IPCC) amplified alarm bells about global warming in the early 1990s, executives at J-POWER took note. Since it was established in 1952 as a government-funded entity under Japan's Electric Power Development Promotion Law, J-POWER (which is still formally registered under the name Electric Power Development Co.") had burgeoned into one of Japan's largest power generators. But while it had amassed a substantial portfolio of coal-fired generation, most of it was fueled by imported coal. And though it predicted that coal power (along with nuclear) would continue a critical role in Japan's 21st-century energy mix, it was wary that growing environmental concerns and the volatility of future coal imports could pose significant hurdles to its coal assets. The company ultimately deduced that finding a way to cost-effectively and efficiently improve its coal utilization over the coming decades would need to be a top priority.
J-POWER jumped into action. In 1995, it launched a national project in collaboration with the Japanese government's New Energy Industrial Technology Development Organization (NEDO) to develop the Energy Application for Gas, Liquid, and Electricity (EAGLE) project. The project's key aim was to develop a Japanese-built oxygen-blown, entrained-flow coal gasifier that could be used for multiple applications, including power generation and the production of synthetic fuels, chemicals, and hydrogen. The EAGLE concept, however, went beyond just integrating the gasifier with gas and steam turbines in a conventional integrated gasification combined cycle (IGCC) configuration. It envisioned adding a fuel cell to the IGCC system to boost its efficiency beyond 50% while slashing its pollution emissions-effectively making it one of the world's first dedicated integrated gasification fuel cell combined cycle (IGFC) systems.
After conducting a feasibility study for the IGFC system, J-POWER and the government research agency in 2001 completed a 150-ton-per-day pilot plant at J-POWER's Wakamatsu Research Institute in Kitakyushu City. Starting in 2002, the pilot investigated gasification system shakedown, followed by overall plant performance testing, and then testing with different feedstocks, and later, carbon dioxide (CO2) separation and recovery. When the pilot showed promise, J-POWER in 2009 partnered with Chugoku Electric Power Co. to establish a new joint venture, Osaki CoolGen Corp.
Osaki CoolGen's main intent at the time was to scale up the EAGLE technology in a 166-MW demonstration test of the IGFC system at Chugoku's 2011-retired 250-MW Osaki Power Station on Osakikamijima Island, Hiroshima Prefecture. According to Chugoku Electric, the project's demonstration scope has since widened to address emerging challenges facing modern coal power, including a grasp on enduring flexibility and low-carbon attributes. Today, the Osaki CoolGen project's main aim is to achieve zero-emissions coal-fired power generation by combining the IGFC-the ultimate high-efficiency coal-fired power generation-with CO2 capture," Chugoku Electric said.
A Decade of Development and DemonstrationSince the Osaki CoolGen project officially kicked off in 2012, it has successfully wrapped up two of three key steps, and it anticipates completing the final step this year. In Step 1, which garnered funding from Japan's Ministry of Economy, Trade and Industry (METI), project partners kicked off construction of a 166-MW oxygen-blown IGCC demonstration plant in March 2013 and completed it in March 2017. The plant's oxygen-blown IGCC technology gasifies coal in J-POWER's proprietary gasifier using high-purity oxygen. It then generates power using a combined cycle that combines a syngas-burning gas turbine (1,300C-class) and a steam turbine that uses the exhaust heat from the gas turbine and the gasifier.
In the first step, we verified the basic performance, plant operability, reliability, and economic feasibility of a coal-fired power system that relies on the oxygen-blown IGCC technology," NEDO said in a statement. We achieved a net thermal efficiency of 40.8% [higher heating value-based (HHV)], the highest level of performance in the world for a 170,000 kW-class coal-fired plant, and obtained a prospect of achieving a net thermal efficiency of approximately 46% (HHV) at a commercial power plant using a 1,500C-level gas turbine (generation output 500,000 kW scale with a capacity of 2,000 to 3,000 tons of coal per day)," the agency added. Compared to the ultrasupercritical (USC) pulverized coal-fired power widely in use today, we believe this technology can cut the amount of CO2 emissions by about 15%."
According to Nobuhiro Misawa, executive director of Engineering at Osaki CoolGen Corp., the configuration of the IGCC demonstration facility is almost identical" to a commercial IGCC power plant, and it serves the same critical functions and priorities, including for safety. Safety is an important factor because the gas composition and process value are significantly different from a conventional [pulverized coal] plant," he noted during the Japan-Asia Carbon Capture, Utilization and Storage (CCUS) Forum 2021, held in October that year.
But as pivotally, test results confirmed a maximum load change rate of 16% per minute-a very high-low change rate, which was equal to natural gas combined cycle gas generation," noted Misawa. IGCC tests also confirmed stable operation at a net power output of 0 MW. Electric power is generated by combined cycle in both IGCC systems and natural gas combined cycle systems, and therefore the result proves that oxygen-blown gasification has a high-load change performance in terms of syngas production," Misawa explained. Utilizing these flexible features, IGCC commercial plants will be able to adjust to several power fluctuations caused by renewable energy, which will be further installed across Japan towards the future carbon neutrality."
Demonstrating a 90% Carbon Recovery RateDuring Step 2, which took place between 2016 and 2020, Osaki CoolGen added a CO2 separation and capture unit to the oxygen-blown IGCC. As there is a high concentration of carbon monoxide (CO) in the syngas, it can be efficiently separated and captured as CO2, making this generation technology optimal for CCUS," NEDO explained.
The carbon capture facilities consist of carbon capture units and a sour-shift catalyst pilot unit. Because syngas pressure for CO2 capture is high-it has about 3 megapascals-we selected a physical absorption method [that uses Dow's Selexol Max solvent] suited to high partial pressure CO2 gas," said Misawa. Osaki CoolGen conducted CO2 capture tests from December 2019 until 2021, when they were paused to allow for installation of the fuel cell equipment. Resumed earlier this year, capture tests involve a 17% slipstream of syngas with a capacity of about 400 tons of CO2 per day. Tests will evaluate capture costs using capital and operational expenditure data. So far, carbon capture performance has exceeded targets," Misawa said, including to demonstrate a CO2 recovery rate of 90% or more.
![]() |
1. Osaki CoolGen's carbon capture flow as joined with its integrated gasification combined cycle (IGCC) and integrated gasification fuel cell (IGFC) systems. Courtesy: Osaki CoolGen |
In the second step, syngas, after acid removal, is sent to the sweet shift reactor, where the CO is shifted to CO2 (Figure 1). The CO2 is then captured in the absorber and recovered by decompression in flush drums. The syngas, which has a high concentration of hydrogen, is returned to a gas turbine as a fuel," said Misawa. At this facility, 17% of total syngas is sent to CO2 capture unit in order to capture 15% of total CO2 volume emitted by the IGCC plant," he noted.
In addition, the company conducted long-term durability tests of the sour shift catalyst. This catalyst is newly developed and works at lower temperature than a standard catalyst. The amount of steam in the shift reactor can be reduced drastically, which results in avoiding energy loss in the CO2 capture process," he noted.
As part of the third step, Osaki CoolGen completed the integration of a 1.2-MW solid oxide fuel cell (SOFC) and began verification tests in April 2022. It plans to continue testing the system until the end of the year. Step 3 notably also involves construction of a CO2 liquefaction facility.
At the outlet of the gasifier, the syngas comprises 50% of CO and 20% of hydrogen. At the inlet of the shift reactor, steam is injected and the CO is converted to CO2 and hydrogen in the reactor. At the outlet of the reactor, the gas composition is 40% CO2 and 55% hydrogen," Misawa explained.
The CO 2 absorber captures the CO2; therefore, high-purity CO2 is obtained. On the other hand, the balance of the gas contains about 85% of hydrogen. While this hydrogen was used as a fuel for the gas turbine in the Step 2 test, in the Step 3 test, the hydrogen will be sent to the fuel cell to produce power," he said.
Osaki CoolGen plans to capture a portion of the CO2 to the liquefaction unit to produce food-grade purity CO2 of about five tons per day, he said. It will then be transported by truck to a commercial tomato greenhouse at the nearby Hibikinada Greenfarm.
The project has meanwhile prompted NEDO to establish a carbon recycling" research and development center at the nearby Osakikamijima town. The center will explore, among other areas, development of environmentally friendly concrete (developed by Chugoku Electric), selective synthesis technology for chemical products, a gas-to-lipids bio process, and bio-jet fuel made from microalgae.
-Sonal Patelis a POWER senior associate editor (@sonalcpatel,@POWERmagazine).
The post A Japanese Project Demonstrates a Carbon Neutrality Pathway for Coal Power appeared first on POWER Magazine.