Evolution and Continuation: How Distributed Control Systems Will Change and Adapt
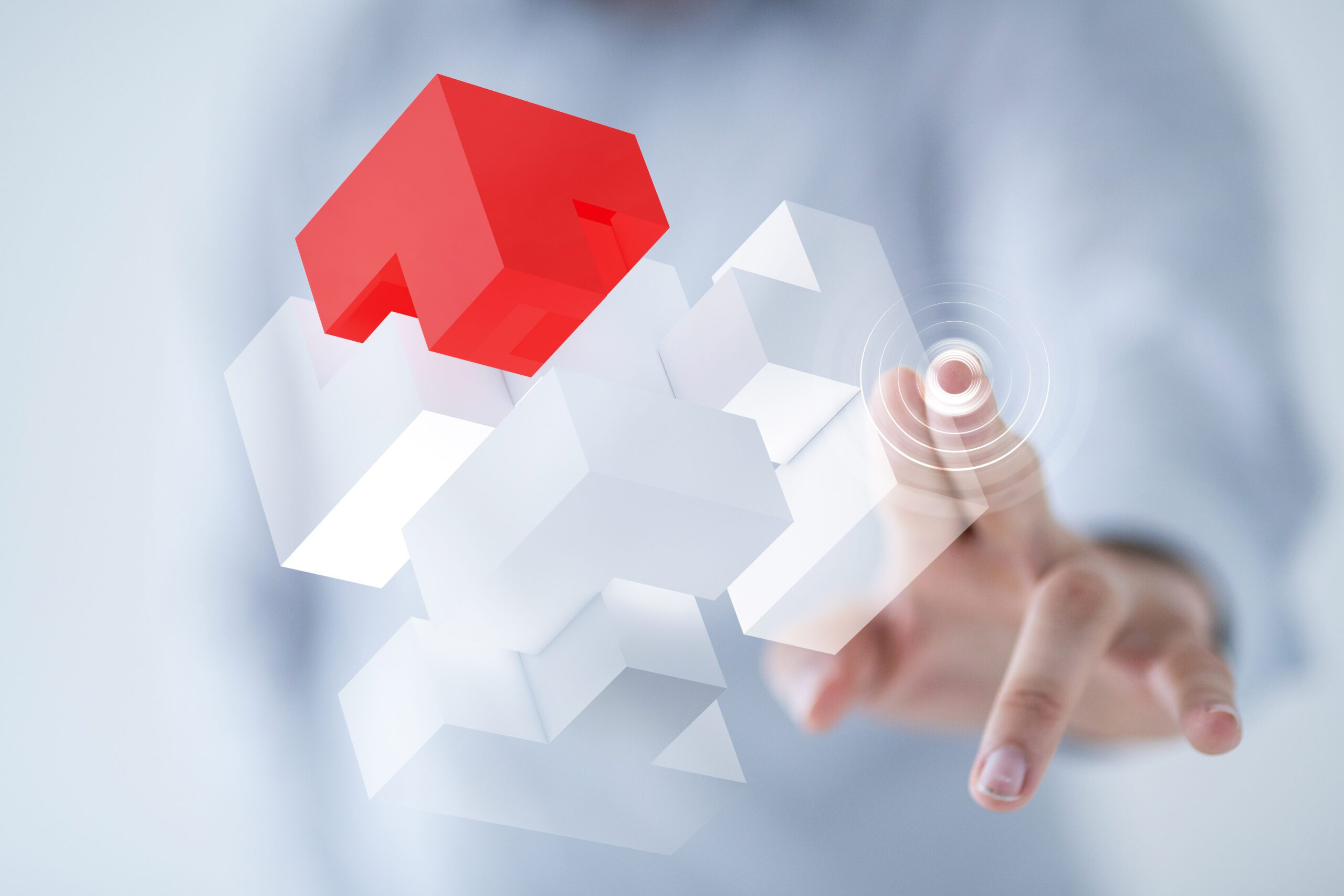
Are today's Distributed Control Systems ready for what tomorrow could bring? Johan Bjorklund of leading global technology company ABB believes they are. Here he looks at how the DCS is adapting to meet the changing demands of users.
Distributed Control Systems (DCS) have been around for nearly half a century. Of course, both industrial processes and the control systems that help to manage them have changed a lot since the 1970s.
COMMENTARY
It's still true that the core DCS aim is ensuring reliable, efficient, and safe performance of industrial processes. However, the underlying requirements have expanded as the demands of process industry companies-providing energy, power, water, metals, minerals, and chemicals-have become more varied and more complex.
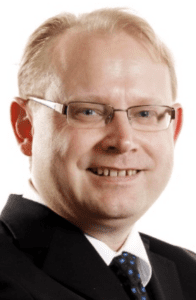
And there's another consideration that wasn't so high-profile in the early days of DCS: sustainability. Can control systems match the ambitions of industry to do a lot more, more efficiently, with less effect on the environment?
Thanks to digitalization, they can. In fact, the Digital DCS won't just help to boost productivity, collaboration, and operator engagement-it will play a role in helping companies achieve their net-zero targets.
New Functions, No DisruptionDistributed Control Systems are expensive and often mission critical. Simply replacing them every time a new industrial requirement or new function comes along would not be cost-effective or practical. Thus, control systems must both meet new user needs and incorporate new functions while continuing to deliver safe, secure and reliable operation.
The answer? Changing or upgrading elements of the process in a way that can improve the whole system without disrupting it and separating the core functions of the DCS from those that are less time or process critical. A modular approach, in other words.
Automation is both an enabler and a beneficiary of this approach, with all that implies in terms of new efficiencies, better use of staff and greater collaboration between people, systems and equipment.
Open and SecureBut how can we enable the expansion of the functions of the DCS without affecting the core control system itself? Among a number of approaches to this challenge, including the work of the Open Process Automation Forum (OPAF), and the industry wide Modular Automation effort, is the NAMUR open architecture (NOA) model. This effectively adds a layer to the Distributed Control System to allow the addition of extra functions.
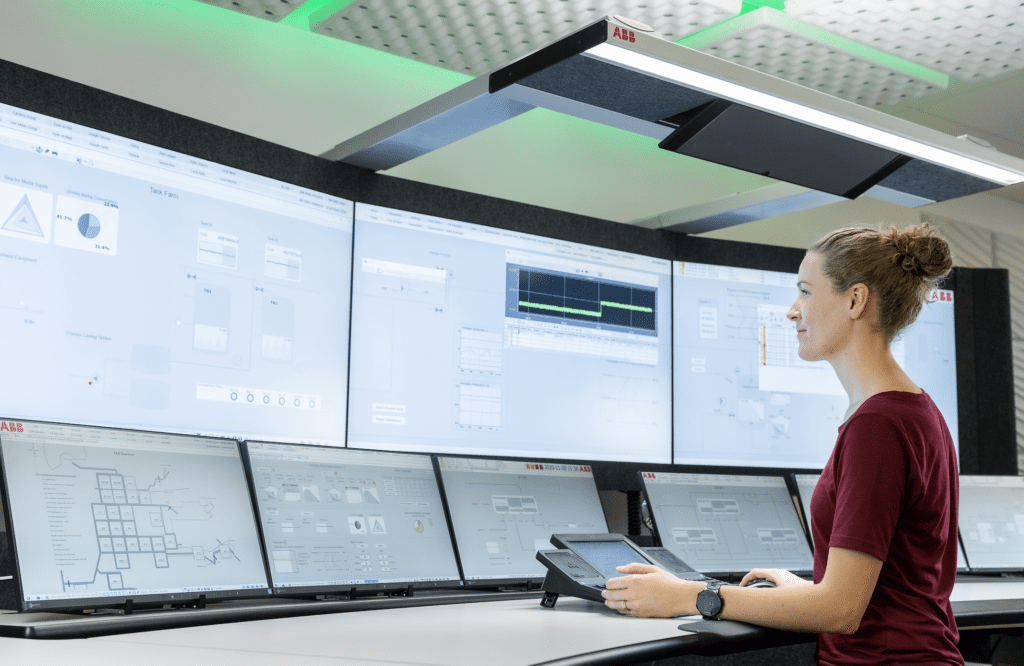
NOA provides an open and secure environment for integrating IT components from the field up to enterprise level, enabling operators to extend the capabilities of their control systems.
Among these extended capabilities are offerings not available even a few years ago, such as edge and cloud computing technology. Allying this technology with IIoT-enabled sensors makes it possible to collect and analyze huge quantities of data from numerous sources and share it between individuals, departments, or different sites.
The non-core control system functions will remain connected but separate, sitting in a digital environment that will allow users' systems to adapt more readily to changing needs. Furthermore, when existing applications can be moved to a virtualized, digitally native environment, advanced cybersecurity tools can be deployed.
Error-Proof the Early StagesOverlaying openness, interoperability and flexibility onto the secure control system core can also be useful at the deployment stage. Future iterations of the Process Automation System will simplify, accelerate and error-proof the automation engineering and project execution stages of the system lifecycle.
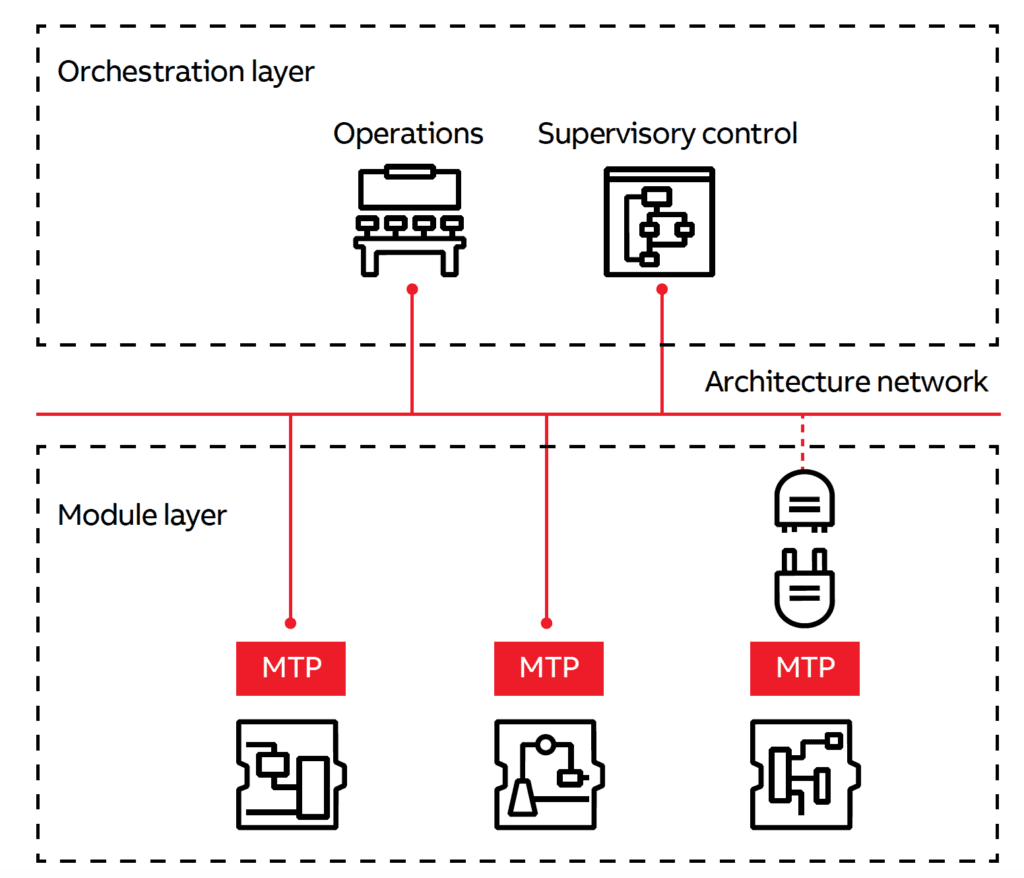
The need for operators to get new production units online faster means cutting down on the time needed to deploy DCS solutions. It also means using up fewer engineering resources. The separation of automation hardware and software engineering at the set-up stage is one way of achieving this.
ABB's Adaptive Execution approach enables multiple teams to carry out project tasks in parallel working from different locations or even in a virtualized cloud engineering environment. If multiple stages of work can be carried out simultaneously, savings of as much as 40 percent on project delivery can be achieved.
Other automation advances now come into play, notably pre-made and pre-tested automation software modules. Pre-configured with the elements required for the application and using the required interfaces needed to communicate with both other modules and the overall system, they will add to time savings.
Many lower-level project execution-related tasks could also be automated. The DCS solutions of the future could eliminate such tasks and thus enable engineers and technicians to operate at a higher level, allowing companies to get more from their engineering teams.
Use the Right Data-and Understand ItData presents another major opportunity. The average plant is estimated to use just 20 percent or less of the data it generates. Collecting and analyzing more data can produce more actionable insights. The digitalized DCS environment can use AI, ML, and edge computing to analyze data. Analyzing operational data at the point of production will improve asset management and predictive maintenance.
Sustainability-AI and ML-led data analysis can also support sustainability. There are many ways to check the performance of multiple emissions-monitoring instruments-and they're going to get more effective. What is the established performance model? What is the actual performance? What's the difference between the two? Can we demonstrate and report our compliance with environmental regulations? Using cloud-hosted continuous emissions data analytics is a way of answering all those questions.
SaaS, PaaS and More-Specifying and purchasing hardware based DCS systems has often been a slow, time-consuming process. But what if a new digital ecosystem meant models such as Software-as-a-Service (SaaS) and Platform-as-a-service (PaaS) could be employed? Users could even choose specific applications and services that they need for as long as they need them. Equally importantly, DCS purchasing, and implementation times could be slashed.
How Automated Can You Get?But there's an even greater prize on the horizon: minimized human intervention. This is an ideal driven by several factors: knowledge drain, labor shortages, or just the distance humans may need to travel to manage a problem with a DCS. These are costly considerations for operators. Can automation help?
Low-level processes are increasingly being handed over to highly automated processes, freeing up time, money and expertise. But humans still need to manage more complex and higher-level or unusual decisions and tasks. Can autonomous control systems reach this level in the process automation systems of the future?
AI will be the key to hardware and software that can learn, understand, and act autonomously. There will be some questions to answer such as how do we demonstrate to our satisfaction that a given technology can operate safely? Are the tasks involved suitable for automation? And what level of automation is required or feasible?
Virtual Support-In the FieldAI and machine-learning algorithms won't just enable automation or predictive maintenance. They will also support engineers in the field, helping them diagnose and solve problems using mobile devices. These devices will give them access to control systems data showing real-time process conditions. Or access to Augmented Reality (AR) tools so they can do repairs with the help of virtual instruction guides and manuals or share views of equipment or situations with remote subject matter experts.
Much more is coming. The separation of core and non-critical functions is an important development that will enhance the DCS and make it much better equipped to adapt to change. Digital technologies, in short, will make DCS architecture more open, more flexible and less prone to delays.
But much more is coming: intelligence that will bring a step change in how we manage DCS performance and ensure the sustainability of operations. AI, ML, data analysis and more will, in other words, drive up automation, efficiency and speed and drive down delay, maintenance time and harmful emissions.
-Johan Bjorklund is responsible for Product Line Management and Sales Enablement for Control System within ABB. He has international experience from being based in Sweden, Switzerland, Singapore, China and the United Arab Emirates for the past 25 years, holding roles from Product, Area Sales, Segment to General Management. For more about ABB's vision of the future of process automation, visit https://new.abb.com/control-systems.
The post Evolution and Continuation: How Distributed Control Systems Will Change and Adapt appeared first on POWER Magazine.