The POWER Interview: FREYR Leads Wave of New Battery Manufacturing
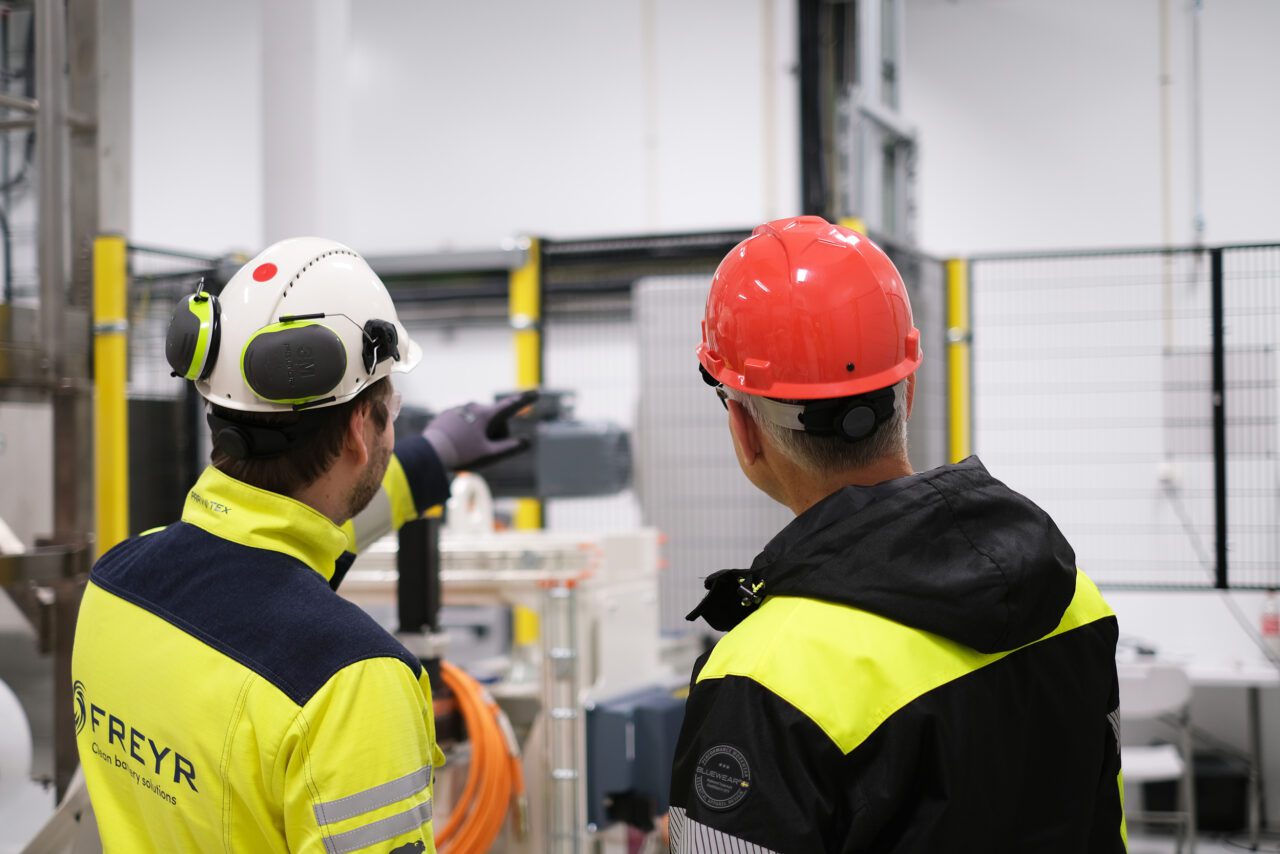
Growth in the energy storage market, including the transportation sector, has spurred a ramp-up in global battery manufacturing and investment in new technologies.
Passage of the Inflation Reduction Act (IRA) in the U.S. has brought a flurry of announcements from foreign companies eager to build manufacturing plants in America. FREYR, a Norway-based company, late last year announced it had purchased a site in Coweta County, Georgia, for its Giga America battery plant. The company at the time said it projected an initial capital spend of $1.7 billion for the project, which it said would create some 720 jobs in the region.
South Korea-based LG Energy Solution on March 24 said it will quadruple its initial budget for a battery manufacturing plant in Queen Creek, Arizona, saying the company will spend $5.5 billion for the project. LG said that the Arizona site would have two main facilities, one for building cylindrical batteries used in electric vehicles (EVs), and another for lithium-iron-phosphate pouch-type batteries for energy storage systems. LG also recently announced construction is underway for a battery-manufacturing project in Ohio in conjunction with Honda.
The U.S. Department of Energy (DOE) recently said it expects U.S. battery production will increase 20-fold by 2030 compared to 2021 levels. A wave of new planned electric vehicle battery plants will increase North America's battery manufacturing capacity from 55 Gigawatt-hours per year in 2021 to nearly 1,000 GWh/year by 2030," the agency said. The DOE in a news release noted, To optimize supply chain logistics, many battery plants will be co-located with automotive plants. Most of the planned projects in the United States are concentrated along a north-south band from Michigan to Alabama. Based on current plans, Kentucky, Tennessee, Georgia, and Michigan will see the highest growth in battery manufacturing capacity."
Korea's Samsung SDI, meanwhile, has announced plans for multiple U.S. projects, including a $2.5 billion facility in Indiana in partnership with Stellantis, a multi-national automotive manufacturing group.
FREYR's Georgia factory will likely be a model for that company as well as for other U.S. battery manufacturing facilities. Tom Jensen, the company's co-founder and CEO, said the Georgia site underscores FREYR's ambition to develop a very strong and near-term operational footprint in the United States. Expanding into the U.S. has been a foundational aspect of FREYR's long-term strategy from our inception, and with the recent passage of the Inflation Reduction Act, we expect U.S. demand for ESS, passenger EV and other electric mobility applications to grow rapidly over the next decade."
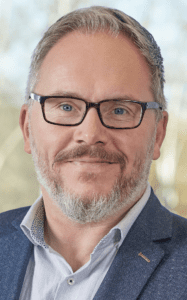
FREYR is supporting its expansion plans with the opening of a Customer Qualification Plant, or CQP, in Norway. The facility, in Mo i Rana in northern Norway, came online March 28. The CQP is energized by hydropower as part a long-term agreement with Statkraft from that company's Rana hydropower facility.
The factory features a demonstration production line, built at the actual physical size of a normal production line in commercial operation. That will allow creation of sample sales for customers, and provide the capability to test different materials in the manufacturing process.
The building also serves as a training facility for FREYR. That will enable the company's workers to know the challenges that could be part of the operation of the company's planned commercial giga factories such as the one in Georgia.
The Chapter One opening ceremony at the CQP is a major milestone for FREYR, which inaugurates the global launch of one industrial-scale production line of the 24M Technologies SemiSolid production platform at GWh scale," said Jensen, who added that the company has planned an investor-focused event at the CQP this summer to demonstrate automated production of clean, next-generation batteries with this ground-breaking technology."
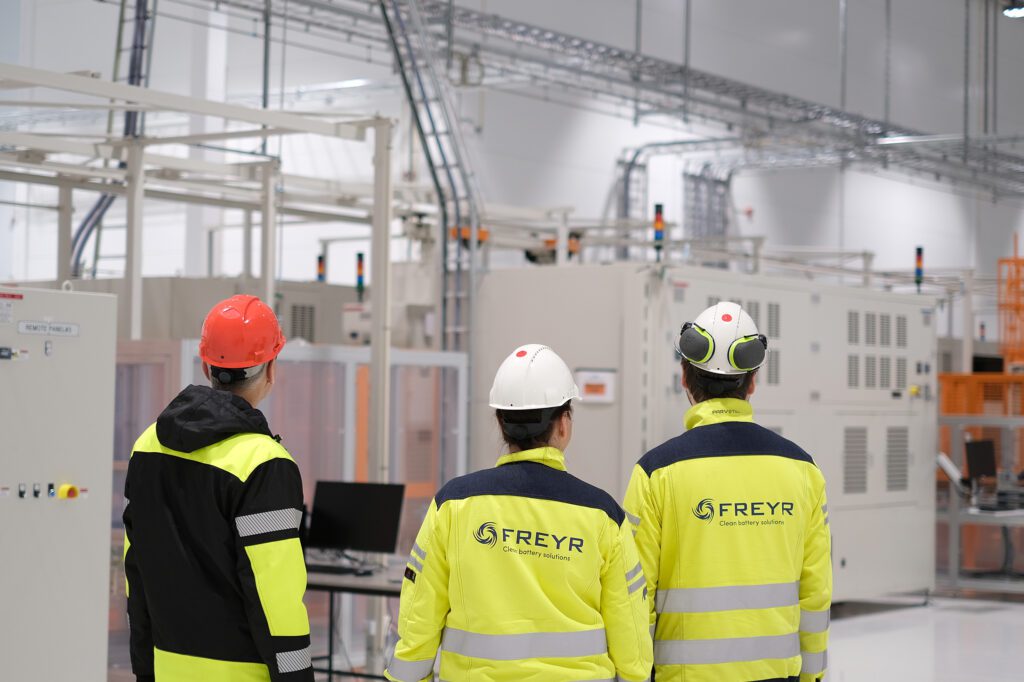
FREYR also has announced potential development of industrial-scale battery cell production in Vaasa, Finland, as well as the U.S. The company has said it intends to install 50 GWh of battery cell capacity by 2025, 100 GWh annual capacity by 2028, and 200 GWh of annual capacity by 2030.
The company on Tuesday also announced it has begun discussions on a potential strategic coalition with Glencore Plc, Caterpillar, Siemens AG, and Nidec Corp. to pursue the scale up of sustainable battery solutions across Europe, North America, and beyond."
We are exceedingly pleased to announce the emergence of this new global strategic coalition with four premier global industrial and energy companies," said Jensen. This announcement represents an important first step for FREYR and our four potential global partners as we launch this commercial initiative. Ultimately, FREYR's vision for this coalition is to accelerate the energy transition across key sectors by scaling up clean battery production from FREYR's gigafactories under development, and to incubate and develop innovative technology solutions together."
Jensen, as part of the company's celebration of today's CQP opening, answered questions from POWER about the facility and the company's plans to expand its battery manufacturing and provide innovative technology for the energy storage and e-mobility sector.
POWER: What was behind the decision to open a manufacturing facility powered by hydro? What stands out with this CQP?
Jensen: FREYR Battery aims to provide industrial-scale clean battery solutions to reduce global emissions. Our mission is to produce green battery cells to accelerate the decarbonization of energy and transportation systems globally. One of the reasons to choose Mo i Rana in northern Norway is the availability of abundant and low-cost renewable energy. In May 2022 we signed an agreement with Statkraft, Europe's largest producer of renewable energy, to secure [a] supply of renewable power under globally competitive terms for our operations in Mo i Rana.
We decided early to build the CQP as a full industrial-scale production line at GWh scale, as a world first for the SemiSolid technology platform. Our ambition is then to install eight of these in Giga Arctic in Mo i Rana and to replicate this in Giga America across the Atlantic. Having an actual industrial-scale production line in the CQP will allow us to shorten the time it will take to reach targeted yield and uptime in our subsequent gigafactories.
POWER: How does your technology differ from other battery manufacturers?
Jensen: We have chosen a U.S. technology licensing partner in the MIT-spinoff 24M Technologies Inc. The start of operations at the CQP will inaugurate the global launch of one industrial-scale production line of the 24M SemiSolid production platform at GWh scale. The battery cell design itself is improved through providing substantially larger and thicker electrodes, which implies that we have fewer repeating layers in the cell and therefore increase the amount of energy-carrying material per battery cell, lowering the bill of material costs per KWh. The larger physical structure also provides for significant system-level cost savings as we need fewer modules, packs and Battery Management System-related costs at the final product/system level.
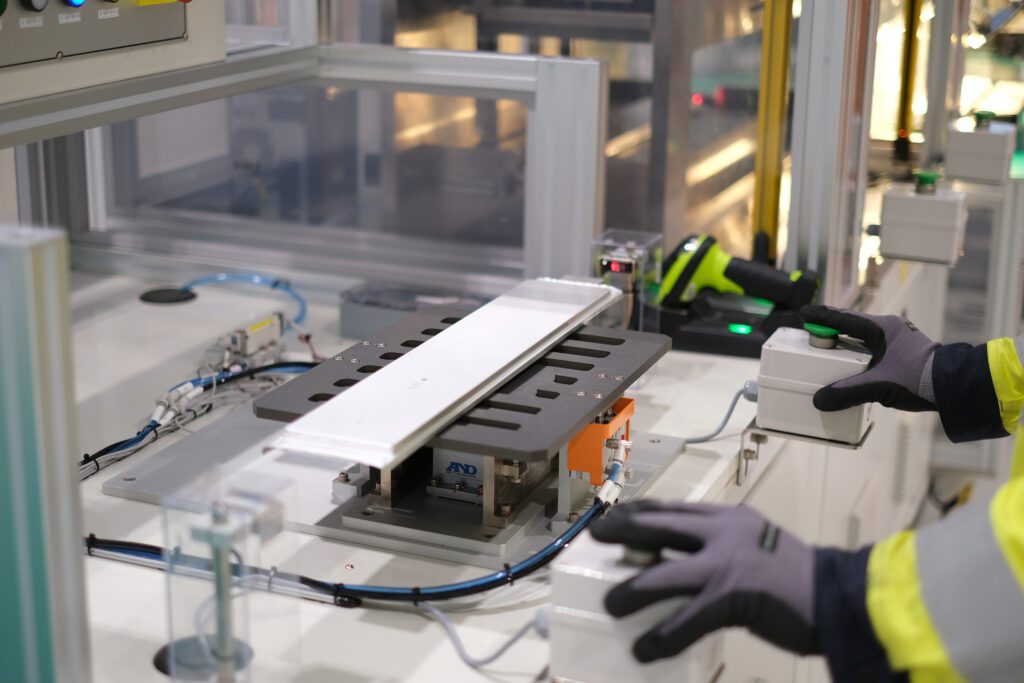
The production process is also dramatically simplified and fundamentally improved, and we project that the technology enables substantially lower capex, lower energy consumption, less space, and up to three times as many batteries produced per employee when produced at GWh scale.
POWER: How does the Georgia manufacturing plant support your position among global battery manufacturers?
Jensen: FREYR has created real option value with parallel project development in Norway and the U.S. catalyzed by CQP and [the] IRA. We are evaluating multiple options to fast-track the start of production at Giga America, targeting start-up in 2025. We are considering different roadmaps that will give us a shorter time to market and competitive products, to capture IRA benefits and the growing ESS [energy storage system] opportunity. Our customers value that we can provide products from multiple geographies. The U.S. is also the fastest-growing ESS market in the world, which is a market segment we have a core focus on.
POWER: Can you provide details about the engineering behind the 24M technology?
Jensen: The SemiSolid platform is a significantly simpler production process, reducing the number of production process steps in half. In short, this technology produces larger and thicker electrodes, which implies producing final battery products that are much more adapted to the end products it is now being used for such as vehicles and energy storage containers. The fundamental change in the technology is that the electrolyte is used as the binder and solvent upfront in the production process, eliminating the need for expensive and space-consuming solvent recovery and drying process steps.
POWER: How are you able to reduce production costs while delivering higher energy density per volumetric unit?
Jensen: 24M's SemiSolid production platform produces products that are fit for the purpose batteries are now being used for, and it will offer superior cost and performance when produced at GWh scale. With a simplified production process, we project to reduce capex per installed GWh unit significantly, reduce the energy consumption, and triple productivity per employee through further automation and digitalization. At the final product level we also see that the physically larger products could reduce total costs significantly by reducing the number of repeating structures at the system level.
POWER: Is your group challenged by supply chain issues? If so, why, and if not, how are you able to avoid them?
Jensen: Our general strategy is to develop a network of global suppliers, but we are targeting regional and decarbonized supply chains. We want to minimize the logistics chains to make it as cost-efficient and carbon-efficient as possible, but at the same time maintain the global flexibility to be resilient. This means that a major share of the raw materials we need in Europe will be supplied from Europe, and for U.S. from North America, but there will of course be some cross-continental supply, also including Asia. We have so far been able to secure all raw materials we need, and a major part of the volatility in the underlying raw material costs is covered through pass-through mechanisms in our offtake contracts.
POWER: What are the biggest issues today for the global battery manufacturing market?
Jensen: FREYR is moving as fast as we can to decarbonize energy and transportation systems globally. This is a growing industry as demand is increasing fast, and to be able to produce all the batteries needed, there will be a need for more of everything. To be able to meet demand, the world will need to install seven times more battery capacity in the next seven years if we are going to stay within the reasonable climate boundaries. The main challenge thus facing the battery industry is to be able to scale up fast, which requires huge amounts of capital and competence in record-breaking time to ensure high-quality products with impeccable safety and sustainability standards.
-Darrell Proctor is a senior associate editor for POWER (@POWERmagazine).
The post The POWER Interview: FREYR Leads Wave of New Battery Manufacturing appeared first on POWER Magazine.