Gas Power Outlook: Gas Turbines Will Play a Vital Role in Decarbonization
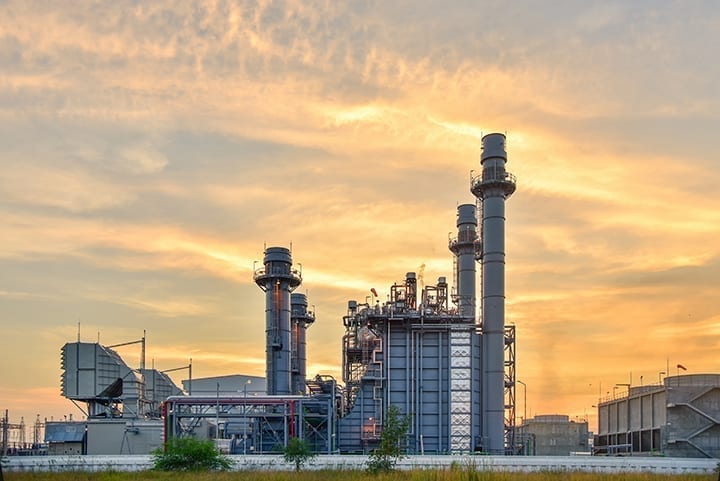
Natural gas-fired power generation has seen its ups and downs over the past couple of decades. In some cases, highly efficient combined cycle units were taken offline because they just weren't needed. But the future looks bright. As coal-fired plants are retired, gas-fired plants will often be needed to take their place.
COMMENTARY
On a cold and dreary October day in 2013, I paid a visit to the Ulrich Hartmann Combined Cycle Power Plant in Ingolstadt, Germany. At that time, the plant was owned by E.ON and in commercial operation since 2011. Based on Siemens Energy's SGT5-8000H gas turbine, the plant was the first one to break the 60% net LHV (lower heating value) efficiency barrier. On the day of my visit, at 10C ambient temperature, the monitors in the operator room indicated 540 MW net output at 60.3% efficiency.
Several years later, when I was writing my book on gas turbine combined cycles (CRC Press, 2019), the plant, now owned by Uniper and renamed Irsching Unit 4, was in cold standby," that is, one step removed from being completely mothballed." (Even at the time when I visited the power plant in the fall of 2013, the plant was averaging only one-fifth of its planned capacity.) Apparently, the generation from coal and renewables (mostly wind from what I could see) was such that there was really not much need for power from a plant (even a world-record-holding one at that!) burning very expensive natural gas imported from Russia.
Today, Irsching Unit 4 is fully operational and running in support of the wind generation and at baseload as needed (except for a 32-hour period in January due to a leak). According to information received by Industrial Info Resources Inc. (IIR), in spite of the ongoing conflict in Ukraine, the plant has enough gas to operate at least until the end of the year.
When I was driving from Aachen to Frankfurt in late November last year, I passed by a coal-fired power station going (apparently) full blast with the plumes from the two natural draft cooling towers covering the sky. On the other side of the Autobahn, a few lonely wind turbines with their slowly turning blades highlighted the contrast in Germany's generation portfolio (see Figure 1 depicting the situation last November). With an aggregated carbon footprint of 554 grams of CO2 equivalents per kWh in November 2022, Germany was one of the worst polluters in Europe. (One day in January, while writing this article, the number went over 800!) So much for the vaunted Energiewende.
![]() |
1. Germany's carbon intensity and electricity production in November 2022. Source: electricitymaps.com |
In terms of emerging technologies in the gas power realm (read: gas turbines), I do not have anything new to add to those ably covered in an earlier POWER article (see Gas Turbine Technology Advances That Could Boost Their Future Relevance" in the October 2021 issue). I would also like to draw readers' attention to a National Academies report, Advanced Technologies for Gas Turbines (2020), which is publicly available. (I was one of the contributors.)
At the end of the day, for a technology that started in earnest in the 1930s with the pioneering work of Dr. Hans von Ohain and Sir Frank Whittle, to expect proverbial eye-popping" advances is naive. In the last three decades, the admirable increase in gas turbine combined cycle (GTCC) efficiency from the low 50s (percent LHV) to above 60% can be attributed almost exclusively to the increase in turbine inlet temperatures (TITs) from 1,300C to 1,700C, which, of course, was primarily driven by advances made in metallurgy, manufacturing (such as single-crystal super-alloy hot-gas-path components, including stator vanes and rotor blades), and cooling techniques.
In early 2023, the goal post is set at 65% net GTCC efficiency, which, at least based on the published ISO baseload rating claims of major original equipment manufacturers (OEMs), is not too far ahead. The next target-70%-will require new tricks, including a change in the underlying Brayton cycle. In the past, attempts to do just that, including through external (steam) cooling of the hot gas path and reheat combustion, failed to make a big dent in performance. Although proven in the field, both attempts fizzled commercially due to complex designs with unfavorable operability and installed (and maintenance) cost implications. On paper, both technologies can make a significant contribution to cover the five percentage points from 65% to 70%. However, it is quite unlikely that the OEMs will dust off either technology. (Note that sequential combustion" gas turbines are still being offered by two OEMs and steam cooling of stationary parts is still a feature in one OEM's product line.)
The only other cycle modification that can really lead to an appreciable efficiency uptick is constant volume combustion." (Note that the conventional gas turbine Brayton cycle is an ideal proxy for constant pressure combustion.") To date, the best possible approximation of this ideal is detonation combustion (as opposed to the deflagration variant in modern dry-low-NOx [DLN] combustors). Pulsed detonation combustion has been on the table since the 1950s primarily for aircraft propulsion applications.
Currently, the research and development (R&D, Figure 2) focus is on rotating detonation combustion (RDC). In layman's terms, detonation combustion results in an increase in cycle temperature and pressure. This reduces the parasitic power consumption of the compressor and increases the net shaft output of the gas turbine for the same amount of fuel burn. While extremely difficult to fit into an aircraft gas turbine jet engine, RDC is readily implementable in a stationary machine. The efficiency impact can be significant, somewhere between one and two percentage points in GTCC.
![]() |
2. Gas turbine (GT) evolution chart. (Turbine inlet temperature [TIT] values are introductory/nominal-real values are probably closer to 1,700C after 2020.) Source: S. Can Gulen |
Even without the introduction of a new (or old) trick in the basic gas turbine cycle, incremental improvements in efficiency can be expected. Going much beyond the present state-of-the-art-1,700C TIT-is highly dependent on the availability of advanced materials (including ceramic composites). Additive manufacturing (commonly known as 3D printing) can contribute by enabling implementation of advanced film cooling (approaching the effusion cooling ideal) of the hot-gas-path components. Regardless of what will be claimed by the OEMs in the next decade, clearly at 60% net LHV or higher field-clocked performance today, GTCC will be the dominant thermal technology for electric power generation. In fact, with 400+ MW (approaching 600 MW!) in simple cycle in 60 Hz (50 Hz), one can simply replace many coal-fired power plants (some in the low 30s in net LHV efficiency) with one gas-fired machine (40+% net LHV efficiency) and achieve a significant reduction in CO2 emissions at minimal cost. (Future retrofit options for GTCC with or without post-combustion carbon capture [PCC] makes the proposal even more attractive.)
Hydrogen and Gas TurbinesReplacing coal-fired generation with gas turbines, in simple or combined cycle, is a slam-dunk. The incontrovertible proof of that is the transition from coal to natural gas in the U.S. in the last decade. A hydrogen economy, at least with respect to gas turbines running fully on H2, however, is a mirage. The problem is not whether gas turbines can burn H2 fuel or not-they can and they do-the problem is to find, or, more aptly, to produce enough green" H2 to make a meaningful impact on CO2 emissions.
From U.S. Energy Information Administration (EIA) Form 923 data from 2020, the most efficient GTCC plant in the country (Okeechobee Clean Energy Center) generated about 9,500 GWh by burning roughly 60 million MMBtu higher heating value (HHV) natural gas fuel for an impressive 59.4% (LHV) effective efficiency (translating to roughly 3.2 million metric tons of CO2). Assuming it were possible to utilize the entire U.S. wind curtailment in 2020-13,000 GWh-in a polymer electrolyte membrane (PEM) electrolyzer to make H 2 and burn it as fuel at the Okeechobee plant, one could meet only 50% of its fuel need for a reduction of 50% in its CO2 emissions. Retrofitting the same plant with 90% PCC using chemical absorption technology with a generic amine-based solvent would do much better than this at a much smaller cost (and complexity).
Green hydrogen is only green, if and only if, the renewable energy resource in its production is surplus, that is, curtailed wind or solar energy. Dedicating a primary energy resource, including nuclear energy, exclusively to H2 production by diverting it from direct electric power generation can only be green if the power grid in question is fully green to begin with. This is the case only in a few places in the world. Otherwise, each MW diverted to H 2 production will be made up by the existing grid with its particular CO2 emissions footprint (see Should We Really Use Renewable Electricity to Make Green Hydrogen? Not Always" in the January 2023 issue of POWER).
Blue hydrogen produced by gasification of biomass or coal (with carbon capture) is a good way to make use of otherwise unpalatable feedstocks. The technology is already available. The main hurdle is installed and operating cost of the production plant. There is an ongoing Department of Energy-funded front-end engineering design (FEED) study to investigate the feasibility of this route to blue H2 via gasification of biomass (corn stover pellets) and Powder River Basin (PRB) coal.
Coal gasification for blue methane production (with carbon capture) can also be a viable alternative to burning coal directly for electric power generation. The Great Plains Synfuels Plant in Beulah, North Dakota, has been in operation producing synthetic natural gas from lignite for more than three decades. Carbon dioxide generated by the process is piped to Canada for enhanced oil recovery.
Other Innovative TechnologyOne intriguing technology to generate electric power using natural gas is the semi-closed oxy-combustion gas turbine with supercritical CO2 as the working fluid. The underlying thermodynamic cycle is the Allam-Fetvedt cycle developed by NET Power. The combustion of natural gas with O2 generates a gas containing mostly H2O and CO2. Capturing CO2 is simply a matter of cooling the exhaust gas downstream of the turbine in a heat exchanger and condensing the H2O out of the mixture.
The combustion process (and the turbine) was demonstrated at a 50-MW (thermal) test facility in La Porte, Texas. A 300-MW commercial project has been announced by NET Power and its technology partners with a projected commercial operation date in 2026. The transition from pilot to commercial scale (a scale-up by a factor of roughly 10 to 15) in a few years is certainly a bold step. From an efficiency perspective (including the cryogenic oxygen plant), the projected performance, at least for the introductory units, is comparable to that of an advanced class GTCC with PCC, which is likely to be less onerous in capital expenditure.
Depending on its availability, H2 can certainly be blended with natural gas to be piped over long distances or on-site on a case-by-case basis. Be advised that to achieve 50% reduction in CO2 emissions (by mass), H2 content of the fuel gas should be more than 75% (by volume). This is small comfort, notwithstanding the fact that modern DLN combustors are not yet there but eventually will be fully hydrogen capable, supposedly by 2030.
Co-locating small units capable of burning 100% H2 with green H2 production and storage to support large wind or solar farms seems to be the best bet for the future of smart use of gas turbines with hydrogen. In this case, one could easily substitute gas-fired reciprocating engines for small industrial and aeroderivative gas turbines. Reciprocating internal combustion engines (RICEs), essentially automotive engines on steroids, can achieve high efficiencies (such as high 40s in net LHV, which is a direct result of constant-volume explosive combustion in the cylinders) and they are ideally suited to capacity firming of intermittent renewable resources. While not yet there, RICE manufacturers are also engaged in extensive R&D to make their machines fully hydrogen capable in the near future.
Energy storage is one area where gas turbines can make a strong contribution to decarbonization of the electricity sector-with or without green H2. The obvious candidate is compressed air energy storage (CAES), a field-proven technology eminently suitable to long-duration energy storage (LDES). Even so, one has to be aware that the last CAES plant (one of the only two in the world) went into commercial operation in the early 1990s (McIntosh, Alabama). It is difficult to predict when and where the third one will be built but it would not be surprising to see that happen sometime in the next decade. There are adiabatic variants of CAES (such as no combustion of natural gas or another fuel) proposed by technology startups, including cryogenic or liquid air energy storage systems. One can also add to the list thermal heat pump energy storage technologies (such as Malta Inc.'s thermo-electric energy storage system) making use of closed cycle gas turbines.
There is no denying that natural gas has received its share of bad publicity in the fight against global greenhouse gas emissions. While superior to coal in terms of criteria pollutant and CO2 emissions, on a wellhead to the plant stack basis with leaks (and flaring) being factored in, natural gas has (understandably) very few friends in the climate-conscious public. Combined with high prices (except in the U.S. with the shale gas fracking boon), this put a brake on new gas-fired plant construction in Europe and the U.S. in the last decade. Industry forecasters such as IIR and Forecast International (FI) expect this trend to change in the next decade.
According to Britt Burt of IIR, and confirmed by Carter Palmer of FI, it is unlikely that the revival will be on the scale of what we saw during the 2012-2020 timeframe when over 102 GW of new natural gas-fired capacity reached commercial operation. Based on IIR's market tracking, 25 GW of new natural gas-fired capacity is expected to be added in the U.S. between 2023 and 2033. This is well short of the 75 GW of coal-fired capacity scheduled to retire over that timeframe.
FI sees sales of machines over 250 MW as the major driver in the gas turbine market (Figure 3). The situation in Europe is subject to some degree of uncertainty, especially in countries dependent on natural gas from Russia. It also remains to be seen if liquefied natural gas (LNG) exports from the U.S. to Europe will make natural gas-fired generation attractive again.
![]() |
3. Projected gas turbine electric power generation. Courtesy: Forecast International |
IIR has identified 156 natural gas-fired projects in Europe in various stages of development scheduled to kickoff through this decade. If all of these were to be built, it would represent more than 155 GW of natural gas-fired capacity. However, not all of them are expected to move forward. Outside the U.S., IIR foresees most project development activity in the UK, Italy, Poland, Greece, Germany, and Belgium in Europe. Significant natural gas-fired power development is also expected in Southeast Asia, the Middle East and North Africa (MENA), and parts of Latin America such as Brazil and Mexico.
If anything, what we have experienced in the first two decades of the 21st century should make us wary of making projections of any kind. Early on, natural gas was extremely expensive and the GTCC power plants built for baseload only a few years earlier were running at low capacity factors. Almost out of the blue, the shale gas boon happened, and natural gas became almost cheaper than coal. Then, the OEMs started introducing their advanced class gas turbines at a rapid pace with ever-increasing efficiencies. Natural gas replaced coal in the U.S. generation portfolio at a quite dramatic pace.
A change in the administration led to attempts to resuscitate coal, but to no avail-basic economics and environmental consciousness were too convincing to reverse the trend. Then, COVID-19 crashed the scene, and the world economy slowed down dramatically. While recovering from the pandemic-induced economic distress, the war in Ukraine brought home the realization that having access to reliable energy is a vital component of modern life.
The energy transition cannot be dictated by politicians driven by public perceptions. Untimely closures of nuclear power plants and efficient GTCCs like Irsching had already forced Germany to burn coal in order to keep the populace warm. While I don't know the exact rating of the coal-fired plant I drove by in November, it's likely that one Siemens SGT5-9000HL gas turbine (rated at nearly 600 MW with >43% net LHV ISO baseload) could match its output at higher efficiency and a fraction of the CO2 emissions.
To paraphrase the popular misquote attributed to Mark Twain, the reports of gas turbine technology's twilight are greatly exaggerated. As FI's Palmer noted, COVID-19 hit all industries to some degree and gas turbine production suffered; however, this was an anomaly rather than some cyclic drop in production that plagues most industries. With recovery from the pandemic realized, the modern world's thirst for more power will not disappear. Unused turbine capacity will be turned back on (such as Irsching Unit 4, mentioned in the beginning), and coal plants will continue to be converted to gas turbine use.
There is no doubt that worldwide deployment of wind and solar facilities will continue at an increasing pace. It is highly likely that eventually nuclear power will make a strong comeback. Still, even if the aforementioned embellishments to the basic technology do not materialize, gas turbines in simple and combined cycle will play a vital role in decarbonization of the electricity sector simply by replacing coal-fired power plants and supporting renewable energy resources for capacity firming and/or emergency backup in partnership with LDES. As long as we accept the fact that the world population and economic growth cannot be arrested (or turned back), there is no other way.
-S. Can Gulen is an American Society of Mechanical Engineers (ASME) fellow with Bechtel Infrastructure and Power Inc.
The post Gas Power Outlook: Gas Turbines Will Play a Vital Role in Decarbonization appeared first on POWER Magazine.