GE Invests Heavily in Improving Gas Turbine Repair Processes and Combustor Performance
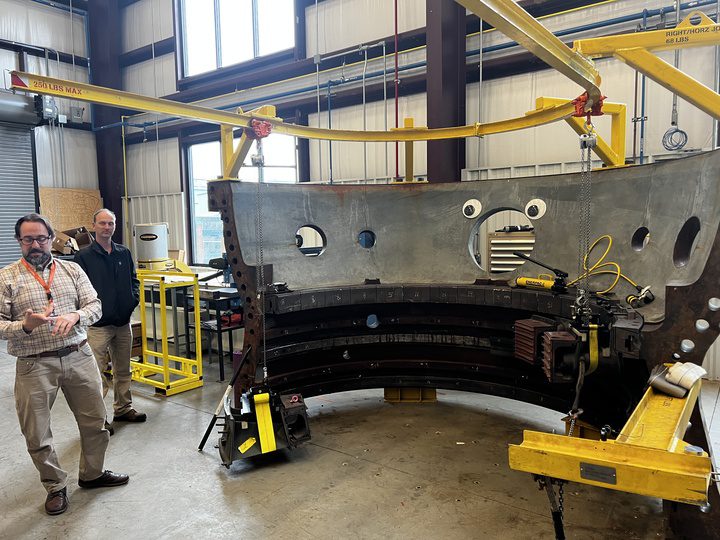
On the east side of Greenville, South Carolina, sits a 413-acre site with more than one and a half million square feet of manufacturing space and another 70,000 square feet of labs. This is one of the locations where GE Gas Power is working to improve gas turbine technology and repair processes, among other things.
GE's Greenville facility includes such things as a Gas Turbine Technology Center, Advanced Manufacturing Works Center, Repair Development Center (RDC), Combustion and Static Load Labs, an outage simulator, and at least seven different gas turbine test stands. More than 2,500 employees work at the site, and GE claims about 7,000 patents have been filed at the facility over the past 10 years.
POWER visited the site on April 26 to better understand some of its capabilities. The tour was conducted in conjunction with the Combustion Turbine Operations Technical Forum (CTOTF) Spring Conference being held at the Hyatt Regency in downtown Greenville.
The first stop on the tour was the outage simulator. As one of the largest original equipment manufacturers in the gas turbine industry, GE says it is continuously improving our methods and resources for the future of planned outages." To do that, the company is investing a lot of money in advanced robotics, automation, software, and smart tooling solutions, many of which are being developed in Greenville.
One of the examples on display at the outage simulator was a big orange box or BOB" (Figure 1). BOB includes a large touchscreen monitor and several industrial-rated tablets for use in the field. It also comes with high-tech networking components to ensure everything will connect seamlessly when taken to remote sites. The solution eliminates much of the paperwork that used to go along with an outage, and ensures all the procedures and documentation are instantly available at a worker's fingertips. Tracking progress and managing work utilizing these tools has never been easier or more efficient. GE already has dozens of these boxes in use at outages around the world.
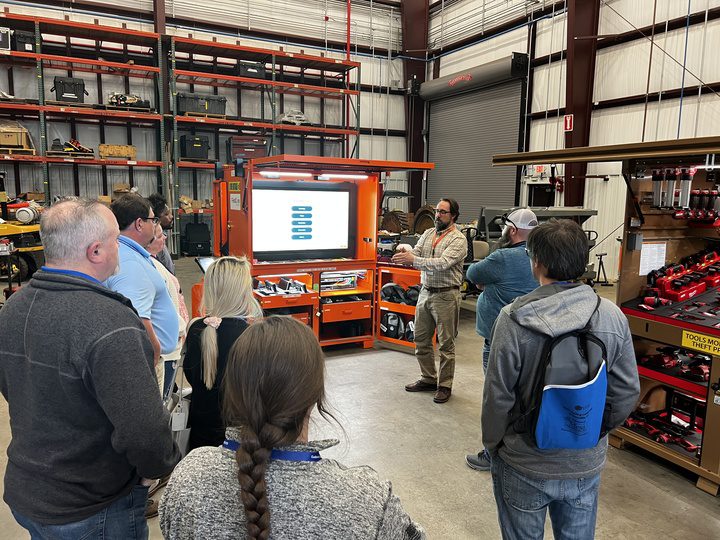
Other tools being developed at GE's outage simulator include systems to make gas turbine disassembly and reassembly safer and easier. Working with technicians and field support personnel from sites around the world, engineers have created various rigging and jacking systems (Figure 2) that eliminate some of the hammering and beating that many workers used to do to get stuck components apart after years of service. These new tools are designed to support heavy components at exactly the right point, keeping them balanced and pushing with hydraulics rather than physical manhandling.
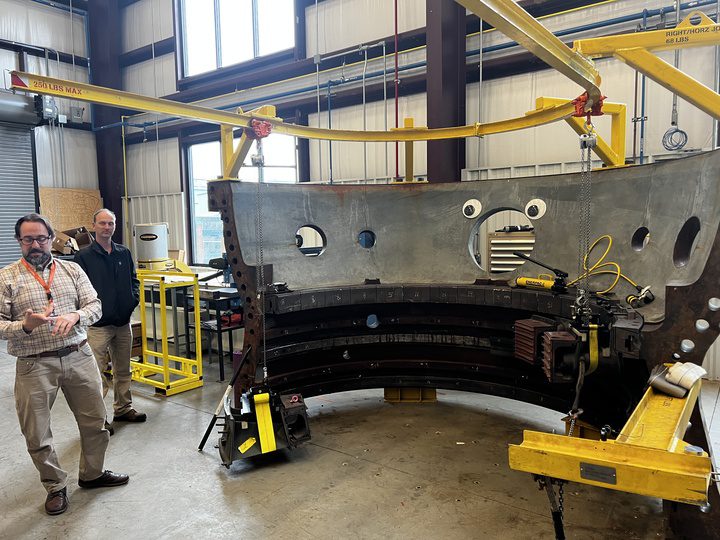
Meanwhile, the RDC's mission is to make GE Gas Power's repair and manufacturing facilities better at work they already do. Their team goes out and identifies and develops great new technology, then, industrializes it at full scale and pushes it out around the globe (Figure 3).
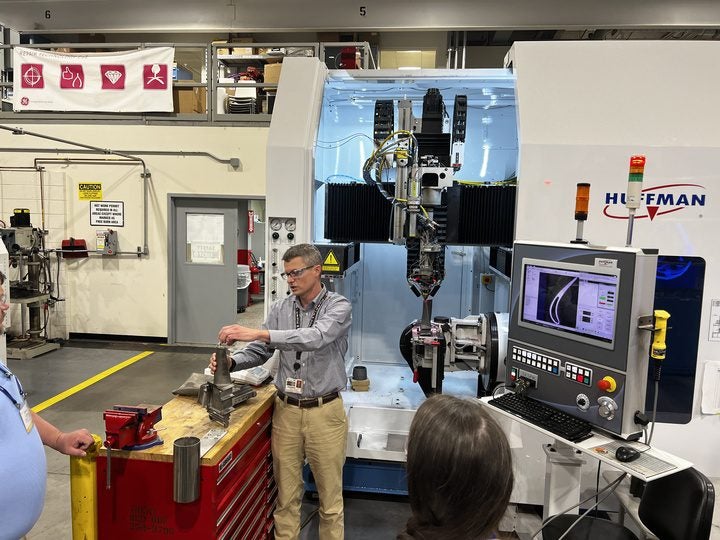
We want to make sure that we can get our service centers to have the most competitive cost and most competitive cycle that we can," explained Erick Baker, engineering manager at the RDC. This is a nonproduction space. This is a space where we can bring four different teams together within GE to try to make some mistakes, try out some ideas, get a few things wrong. Hopefully, at the end of the day, we get something to come out of here that's a robust, proven process, ready to be industrialized."
Baker said there are four teams that use the RDC space. The first team is those service shops and those manufacturing facilities, not just here in Greenville, but out around the world. Those are our customers," he said. They're providing inputs on the needs-inputs on the pain points-where we need to go work. As we develop a solution, they're providing inputs on how that's going to fit in their shop-what needs to change to make it work in the real world." Other groups involved include component engineering, process engineering, and design engineering.
The last stop on the Greenville tour was the combustion lab. Welcoming visitors in front of the lab sits the historic Belle Isle gas turbine, GE's first gas turbine unit delivered to Oklahoma Gas and Electric Co. in April 1949 (Figure 4). The Belle Isle unit allows visitors to see how much has changed in gas turbine technology over the years.
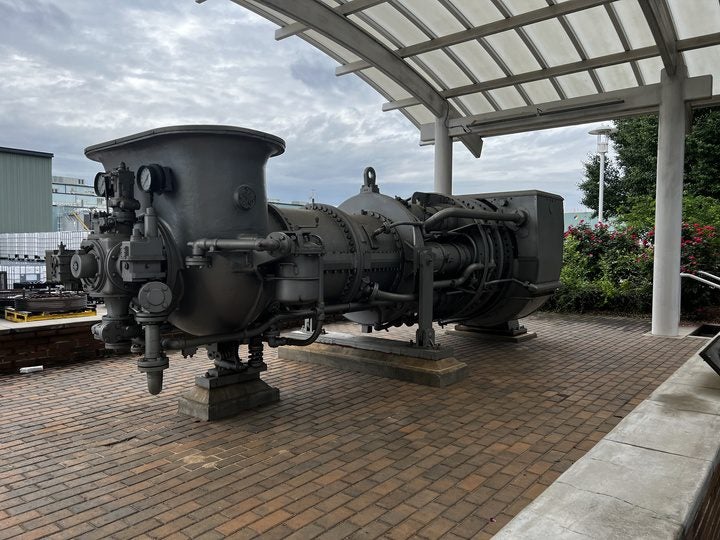
The combustor lab includes multiple bays for testing combustor technology and fuel blends. While no power is generated during the testing, combustors can be fired at maximum rates with exhaust cooled by water spray and directed to the facility's stack.
The lab has a variety of fuels available including both gaseous (including natural gas, propane, and hydrogen fuel blends) and liquid fuels (such as Jet-A and No. 2 fuel oil). Test cells are equipped with low- and high-speed data acquisition systems, interlocks for laser safety, optically accessible pressure vessels and combustor sections for comprehensive laser-based and optical diagnostic measurements. Various optical and laser-based diagnostic systems are available to characterize flow field properties including fuel/air mixing, flame heat release, gas temperature, and pollutant emissions.
The Greenville facility and its capabilities are impressive, showing how GE Gas Power is working to advance gas turbine technology, and maintenance and repair processes.
-Aaron Larson is POWER's executive editor (@AaronL_Power, @POWERmagazine).
The post GE Invests Heavily in Improving Gas Turbine Repair Processes and Combustor Performance appeared first on POWER Magazine.