The Future of Moore's Law Is Inside This Willy Wonka Machine
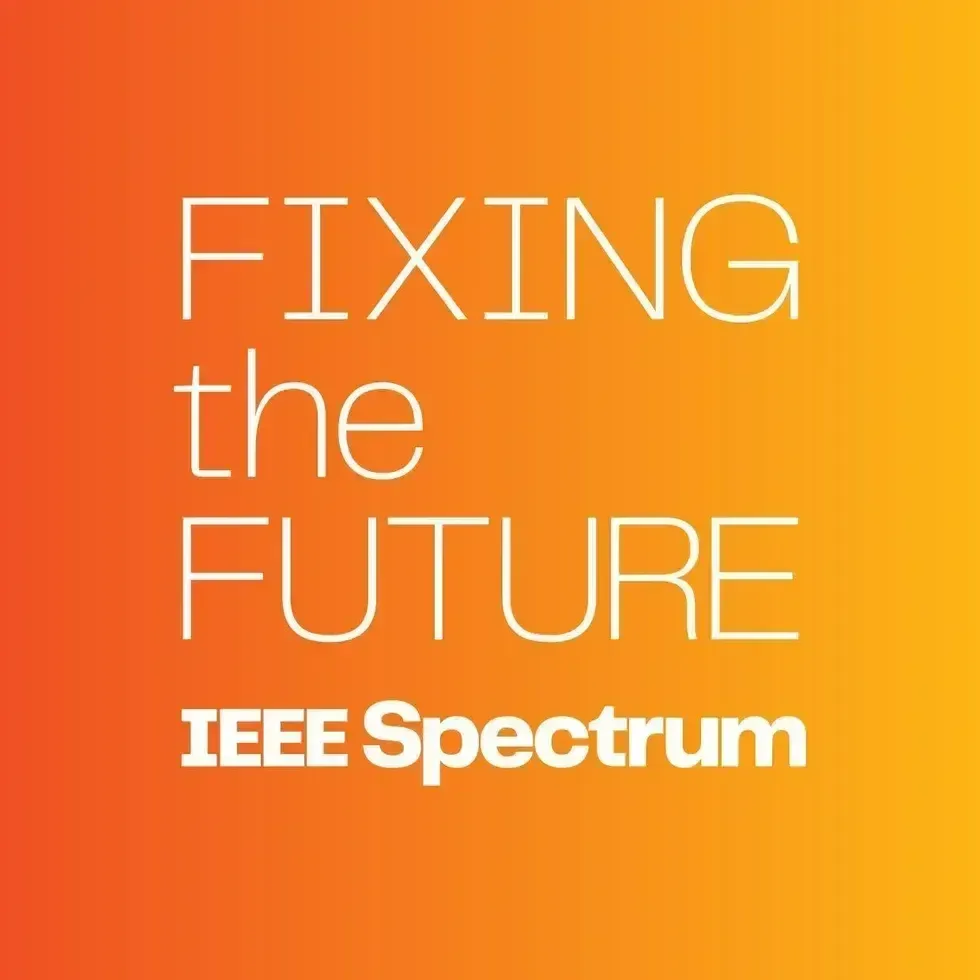
Transcript
Stephen Cass: Hello and welcome to Fixing the Future, an IEEE Spectrum podcast, where we look at concrete solutions to some big problems. I'm your host, Stephen Cass, a senior editor at IEEE Spectrum. And before we start, I just want to tell you that you can get the latest coverage from some of Spectrums most important beats, including AI, climate change, aynd robotics by signing up for one of our free newsletters. Just go to spectrum.ieee.org/newsletters to subscribe. Today, we're going to be talking about making tiny things even tinier so that we can cram ever more computing power onto silicon chips. And to do that, I'm talking with another Spectrumite, senior editor, Sam Moore, who covers a semiconductor beat for us like a field effect transistor covering a depletion layer. Sam, welcome to the show.
Samuel K. Moore: Thank you, Stephen. Great to be here.
Cass: So we'd often talk about Moore's law, no relation, on this show, and the current state of it and how we always seem to be talking about it's the end of Moore's law. And yet, it keeps going. So can you talk a little about what the current state is and these new ideas for pushing that boat further down the stream?
Moore: Sure thing. Yes, Moore's law is slowing down. That's a sort of definitive fact. It is getting harder and more expensive to make more transistors on a given area of silicon. But it is continuing, and there's a lot of effort to make that happen. Right now, we're sort of around the 200 million transistors per square millimeter range, and going to continue to keep trying to make that smaller. You hear a lot about sort of five-nanometer node, three-nanometer node, and stuff like that. You want to keep in mind that these names actually have nothing to do with the size of stuff on things. The five-nanometer node- sorry, the five-nanometer node chips generally have sort of their smallest distance between the wires is 20 to 25 nanometers. So it's all just a name. But they are going to continue to name new things and make new processes and make things even smaller.
Cass: So what do these names relate to at all then?
Moore: It's historical. There was a time when they actually meant something. That measurement, it's called the metal pitch. Basically, the distance between two wires used to actually be what they named things after, excuse me. But that kind of broke down in the late 90s or so. And so ever since then, it's just been sort of a name.
Cass: And what is it based on?
Moore: Sorry. So what is it based on now?
Cass: Yeah.
Moore: Oh, well, they kept cutting that distance in half and in half again. And then they just kind of continued using that sort of division for the name, even though it wasn't actually related to the size of things on the transistor.
Cass: It's just like a general, We are getting smaller kind of-"
Moore: Yeah, it's just kind of marketing. And there's so few companies who can actually do these really, really cutting-edge chips, so they could call them anything. And now they are. I mean, TSMC now calls its process N5. Intel is going to be- their next generation or the generation after that will be like A20. I think the A's for Angstrom.
Cass: So for you, the real measure, though, is that one you said earlier, which is how many million transistors you're going to get per square centimeter square.
Moore: Yeah. That's really what matters. It's just how many you can pack in.
Cass: So in the most recent issue of Spectrum, we had a fantastic feature that you edited called the Moore's Law Machine about some of these efforts to sort of keep Moore's law going with this fantastically elaborate device. And this was written by Jan van Schoot. So perhaps you could take me through this technology, which is called extreme ultraviolet, which sounds like a soda I might buy, but yeah.
Moore: Sorry. Well, they could have called it soft X-rays. But extreme ultraviolet is definitely cooler. So extreme ultraviolet lithography is how you make the- it's the main machine involved in the latest two generations of cutting-edge semiconductor chips. So without it, you wouldn't have your iPhone 12 through 15, I believe, the NVIDIA H100, that GPU that everybody's trying to get their hands on to do their AI. You wouldn't have at least one of the top 10 supercomputers and probably none of the next generation of them. This is the critical machine, and it is made by one company in the Netherlands. And it is fantastically complicated. Let me sort of tell you first what it does, and then I'm just going to give you some weird superlatives about it. What lithography is, is sort of, basically, you've got a pattern that you want to project onto the chip that will eventually make all the circuits and transistors and things like that. And with extreme ultraviolet lithography, you are using a wavelength of light that's only 13 and a half nanometers long. This is a huge jump from what was used in the previous generation, which was 193 nanometers, which was called deep ultraviolet. It's an enormous jump. It took more than 20 years of R&D to actually get to a machine that works and that is vaguely affordable. And when I say vaguely affordable, I really mean vaguely affordable. Each machine is more than $100 million. It's got 100,000 or more components in it. It consumes a megawatt of electricity just so it can deliver a couple of hundred watts of this extreme ultraviolet light onto the silicon wafer.
The thing weighs like 180 tons. I mean, it's massive. The current generation is like trailer size. I saw one of them being put together at a fab in upstate New York about five years ago. And it's so big everybody looks like an Oompa Loompa. I mean, very. If the Oompa Loompa's were the best in the world at what they did and the chocolate factory cost a billion dollars. It's just an amazing machine. And the next version of this machine, which is sort of what we're going to talk about today, is more than a third larger than today's. So it's just massive, complicated, super expensive, hard to get your hand on. And I want to tell you how they actually made it better.
Cass: So inside this giant trailer machine, there's some really crazy components, including how they actually make these soft X-ray/extreme ultraviolet blink beams. And it involves molten metal and a carbon dioxide laser.
Moore: Yeah, it is the most bananas process you can kind of think of. So you've got a vacuum chamber and a little- I don't know what to call it, but it's spitting tiny molten drops of tin. And they shoot across the vacuum chamber, and then you hit that tin with your 40 kilowatt laser. You blast it into a plasma. And then this plasma glows in all kinds of fantastic colors. But the optics collect the 13 and a half nanometers that you actually want to use and project it into the guts of the machine itself.
Cass: This really does sound very Wonka-ish.
Moore: Yeah, it feels like there should be an easier way to do this, but apparently, there isn't.
Cass: So these things have to be vacuum-sealed because this light gets absorbed by the air. And what are some of the other- why is this machine so big? Because it seems like you've got like a little tiny pattern. You've got little tiny chips, okay? These little tiny droplets. Why is it so big?
Moore: Well, a lot of it is actually the chamber containing the optics, which are just insanely precise. The mirrors are fantastically expensive. These aren't just ordinary mirrors. They're multiple layers of alternating exotic stuff in order to get this kind of light to reflect in the right direction with any efficiency because UV is absorbed by tons and tons of stuff, including air. And so a lot of it is just getting the light where it needs to go efficiently without disturbing any of the patterns that you actually want to project. And then there's a lot of it that's also just handling the wafers and handling the masks, which when they're actually sort of in position, they got to be handled at nanometer precision. So these are incredibly fine moving machines.
Cass: So one of the big challenges I think that Schoot talked about in the article was, Yes, you can set this up, and you can get the lasers going, the machine's going, but your throughput is going to be very, very, very low, uneconomical for the size of the machine unless you try a couple of other tricks on top of the, again, molten droplets being blasted by a very powerful carbon dioxide laser," which I know I'm hung up on, but tell me a little bit more about these other tricks.
Moore: Sure. Okay. So as you are a little hung up on- one of the biggest problems they had to solve just to get to the first generation was to make the tin explode in more brilliance so that you could get just that couple hundred watts of light because, the dimmer it is, the longer you have to expose the wafer. And so it's all about throughput. That problem is basically solved. But in order to continue Moore's law, you don't just want this. You've got this light, but you want to actually keep making smaller and smaller features with this light. To do that, there's three knobs that you can turn. One was the big knob of changing the wavelength, which makes sense. Smaller light, better resolution, totally straightforward. Two other knobs. One is kind of difficult to explain. It's a bunch of optical tricks that you can do, which might include as much as projecting two patterns serially to get one pattern at the end or just making things look weird so that they look less weird when they get to the silicon wafer. And I can talk more about that later.
But the knob that they are turning with this newest machine that is currently being built in Belgium right now is to increase the numerical aperture. That's sort of the angle of the light that you can operate within the optical system. Historically, they've turned all three knobs. Numerical aperture is one that actually gives you a really good return, historically. And so they really wanted to do this. They're right around 13.5 nanometer resolution now, but if they want to dip down below, they're going to have to do a high numerical aperture, extreme ultraviolet lithography. This causes a cascade of problems when you're designing the system. This machine is already fantastically complicated. But as with any optics, you tweak something here, it's going to have some other effect later on. So let me go through the cascade of the problems that they had to solve in order to make high NA extreme ultraviolet lithography.
Okay. So first, you want the numerical aperture increase at the wafer itself. That's where you'll get the resolution. But that means you also have to increase it at the mask. Now, the mask is where you store the pattern. So you bounce the light off the mask and goes through the optics, and then it lands on the silicon wafer, and that's your point. Here's the thing. So you got to bounce the light onto the wafer- sorry, onto the mask and then off of the mask. And here's where you have sort of a Ghostbusters moment. Those two streams can't cross. You think bad things will happen. It would be bad, I think, is the line, right? So you can't cross the streams. So that means you have to angle them away from each other, okay? But you can't angle them away from each other too much because these really specialized mirrors only work up to about 11 degrees. And in order to just- if you just wanted to do this without any adjustments, you'd need 18 degrees. So then they're like, Okay, well, now we've got to solve. We're going to need this angle. There's no getting around it." So the way they solved it was by increasing the demagnification, which I know sounds kind of increasing a D, but basically, it's shrinking stuff down a lot. They increased it by like eightfold or something like that.
So like, Okay, hey, problem solved." But not really because now your pattern on the wafer is really small. It's like a postage stamp instead of- not your pattern, sorry. The amount of wafer that you can project onto all at once, super small. It's like a postage stamp, and that means that you have to do more postage stamps, which means that you're-
Cass: Because these wafers are large.
Moore: Yeah, they are 300 millimeters across and so dinner plate size or so. And so if you can only do a little bit at a time, it's going to take you longer to do a wafer. And then it basically becomes so expensive, it's not even worth it. So they had to solve that problem by doing something kind of weird. It was sort of like kind of funhouse mirror effects. Basically, they increased the demagnification in only one direction. So they came up with these specialized mirrors that kind of would stretch things out [laughter] and shrink them. And it had weird effects. I mean, you actually have to make the mask stretched out. So the pattern that's on the mask is kind of this funhouse mirror version of what you want on the wafer. But amazingly, that actually does it. You still wind up with a little bit smaller than you'd like of a projection onto the wafer, but it's acceptable as long as you increase the acceleration of how fast things are moving through the machine. So what? Five problems to solve?
Cass: Yeah, I think so, yeah. Yeah. But this effect, it sounds a little bit like in the old days before we all had widescreen, flat-screen TVs, sometimes when you were trying to be showing like a cinema movie on a TV and suddenly, the aspect ratio would get really weird and distorted because they were having to squeeze in on one axis to make it all fit, especially when the credits would roll and would get all distorted in one direction. And that kind of reminds me of that. But these are big machines. And you've done some other reporting, though, on some of the sort of the side effects of handling these big machines, which is how to operate them in a more sort of environmentally friendly way. And that was the work of this company called, I think, Edwards in England. So can you tell me a little bit about that?
Moore: Yeah. So you remember how I said everything has to happen in a vacuum on the inside of this? Kind of sort of not. There is a very small sort of flow of- I mean, sorry. It seems like a small flow of hydrogen, but it's a really big machine, so it's actually 600 liters per minute. [laughter] But this hydrogen is there for a couple of reasons. Everything in there is super delicate. You don't want anything to get on the mirrors or on the mask or anything like that. But you are blasting molten tin in a chamber, and you have other chemicals that are involved in chip making and stuff like that, and you need to kind of sweep them away. And so that's what this hydrogen is for. And you think, Oh, hey, hydrogen. That's green." Not yet, actually. Most hydrogen is actually not made in any green process. It's actually made by a chemical reaction between water and methane, so not great. And 600 standard liters per minute is actually kind of a lot. What they're doing with it currently is they just burn it because you just get water, and all of the nasties that it's picked up just kind of falls out. And that's-
Cass: Kind of a smoke stack at the side with a flame on top, [laughter] and it's even more Willy Wonka. But yeah, okay. So they're just burning off the hydrogen.
Moore: Right. But that's super wasteful. So what Edwards worked on was a system that can recycle the hydrogen. It's actually pretty cool. It's like a reverse fuel cell kind of. The used hydrogen and the icky components that it's picked up along the way. Basically, go through one side, get ionized. Then an electric field sort of forces those protons through a proton exchange membrane. They come out of a membrane, excuse me. They come out the other side, recombine with electrons. You get pure hydrogen to go back into your process. And all the awful stuff stays on that to the other side. Yeah. So it works pretty good. They set one up at a nanoscience research organization called IMEC, which is kind of a key European research house. And it managed to recycle 70 to 80 percent of the hydrogen in their EUV machine. So now they just have to convince the big chip makers to adopt it as well.
Cass: So with all of these technologies- and I want to turn to sort of a competing technology in a moment, but for these technologies, how long do you think it'll be before we see chips in our smartphones and our computers made with this new technology?
Moore: Right. With a high NA EUV, things that are made in 2025 will probably start to- at least the chips themselves will be made in 2025. It takes months after that for them to be in systems, but that's probably in time for yet another NVIDIA GPU. So AI is driving a lot of the demand for particularly this most cutting edge. And so I'd expect to see it in sort of the generation of AI chips that are sort of made in 2025, 26. Also, Apple is always at the cutting edge. They always want the newest chip manufacturing techniques. So whatever iPhone [laughter] comes out in the latter half of the century will almost certainly involve this.
Cass: And that's actually a perfect segue because you mentioned NVIDIA there. And NVIDIA is looking at enabling another approach to squeezing things down and keeping Moore's law moving along, which is inverse lithography. So can you tell me a little bit about that? And why the fact that it's an AI company works out for well for them? Because they're a chip maker who happens to make like the AI chips.
Moore: Right. So let me sort of give us a little more context since you started. So NVIDIA, actually, they design the most in-demand AI chip in the world. Everybody wants their hands on an H100, which is just the current generation. The manufacturer of that chip, though, NVIDIA designs it. It's manufactured by TSMC, which frankly, kind of dominates the world of the most cutting-edge chips right now. So they work closely together now because NVIDIA is probably one of their biggest customers. So if you can kind of go back for a second, remember I told you about those three knobs you can turn to make lithography better, to make your precision and your resolution better. One of those knobs was this weird one called K1. It was sort of the process stuff that you can do. So what NVIDIA has done is it's made one of those process stuff that you can do much easier to compute. It's a technique called inverse lithography. And here's the thing. You might think that if you wanted to project, say, like a plus sign, something that was shaped like a plus sign onto a silicon wafer, on your mask, you'd put a plus, and then you'd get a smaller plus when it got to the silicon. And not the case. There's enough distortions and other just stuff that you have to worry about optically when you're dealing with this kind of operation below the wavelength of light that you're using, that you have to do things like add little sort of dog ears at the end of the plus sign to make it look like a plus when it gets there. Those things have had to be progressively more complicated as we've kind of driven Moore's law to its limits.
So now that plus sign would actually sort of look like- if you put it in a kaleidoscope and kind of turned it, it's just this massive weird stuff that you have to put on the mask in order to get your simple plus sign at the wafer. Now, those tricks are actually kind of really hard to do computationally. So it's the idea that like, Okay, if I want this plus on the wafer, what do I have to have on the mask?" And it's so computationally difficult that we're talking like weeks of just- we've got a massive computer, and it's going to just sit there for a couple of weeks and try to figure out what that shape should be. What NVIDIA has done is it's come up with a system that turned that two weeks into an overnight job. And the thing that was that it used to be- it used to be a job for CPUs. My guess is it was instructionally complicated enough that it was not sort of inherently of the parallel nature that GPUs were on. So NVIDIA did a lot of work and came up with algorithms that are just perfectly fitted to a GPU. And so, basically, they did in the work- sorry, what would have taken 40,000 CPUs they did with 500 GPUs and two weeks versus overnight, which is actually- that's huge. That eliminates a big bottleneck in getting your chip to market, for one thing. It allows you to use this really computationally expensive technique in more places rather than reserving it for the spots of the chip that were just really difficult.
And from the perspective of an environmental benefit, it's 5 megawatts of power in the computing system versus 35 megawatts, which is not insubstantial. So yeah, this is a thing that they- this computational lithography system, it's called cuLITHO. They introduced it, I think, in the early summer or late spring, and they've got Synopsis, one of the electronic design automation companies bought in. TSMC has been working on it with them. And of course, ASML, which makes the EUV machine in question. And all the other lithography machine equipment they're signed on as well. So it should really be making a difference both environmentally and in terms of getting chips done faster.
Cass: So just to wrap up, we've been talking about a lot of technologies that are actually very close to being deployed. Is there anything you're seeing in the lab that's further out that might help us like in the 2030s, basically?
Moore: There's no clear answer to whether there'll be sort of another wavelength of light that we use, and it seems kind of unlikely, actually. Even 13.5 nanometers is not that many atoms of material when you get down to it. So our ability to sort of shrink things down in two dimensions, it really is getting towards the end. And so transistor architecture is starting to go 3D. Or rather, in the lab, it's starting to go 3D. But this seems like the path that everyone has chosen. So now there's a new kind of transistor. I believe Samsung started using it in production last year, maybe TSMC this year. I might have those wrong, but they're both well into this new structure. It's called a nano sheet. And Intel is moving to it the end of 2024. And the thing about the nano sheet is that it's sort of conducive to making a second transistor right on top of it. So instead of trying to squeeze things together in two dimensions, we're going to start adding layers. In addition to just at the transistor level making it 3D, we've already got quite a lot of work going on right now and quite a lot of production chips that involve 3D packaging, which is just taking one chip and stacking it on top of another in order to kind of make a superchip. And that's happening now in production chips. So yeah, the future is three-dimensional.
Cass: Well, that was fantastic, Sam. Thank you so much for talking with us today.
Moore: It was a pleasure, Stephen, as always.
Cass: So today we were talking with Sam Moore, senior editor at IEEE Spectrum about extreme ultraviolet and other technologies to keep transistors getting ever smaller on computer chips. For IEEE Spectrum, I'm Stephen Cass, and I hope you see us next time on Fixing the Future.