Could Dispute Resolution Boards Keep Combined Cycle Projects on Schedule?
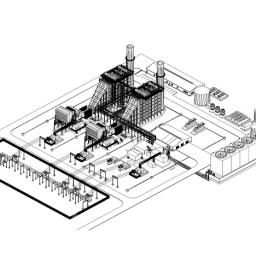
Owners and contractors can run into contractual disputes during combined cycle construction projects. Often, the disagreements snowball into lawsuits, which create a lot of activity in attorney offices, but can actually stop activity at the construction site. Engineers and laborers frequently end up taking off their hard hats and setting down their welding torches to take up claim and counterclaim tools instead.
Dispute Resolution BoardsTo prevent these work stoppages, the combined cycle industry could borrow the transportation industry's common practice of incorporating a dispute resolution board into project contracts.
For decades, complex construction projects in the transportation industry have used dispute resolution boards to successfully settle disputes rapidly onsite, rather than painstakingly in a future arbitration or courtroom hearing. Transportation engineers tell us that a key to their success is that the dispute resolution board comprises unbiased business managers trained to speak the language of construction, rather than attorneys trained to speak "legalese."
To understand how a dispute resolution board could help combined cycle projects stay on schedule, let's look at the guidelines followed by the transportation industry. The following are the seven guidelines for the dispute resolution board of the Florida Department of Transportation:
- The dispute resolution board comprises three members-one is appointed by the project owner, one by the contractor, and one is mutually agreeable to both.
- Board members cannot be representatives or employees of any of the project participants and must be completely impartial.
- Board members cannot be attorneys.
- The chairman of the board is the sole point of contact between the board and the project participants. Individual board members cannot communicate with any employees of the owner or the contractor.
- The board meets on a regular basis throughout the project, typically monthly at the start of construction but that can change to quarterly as the project moves forward. Regular meetings are held onsite to keep the board up-to-date on general site conditions and construction progress. Each meeting's agenda addresses any then-current disputes, which can be submitted by either the owner or the contractor. Prior to the meeting, both parties can provide documents to the chairman of the board to support their contentions. Both parties are entitled to see all submitted documents. After each meeting, the board privately discusses the disputes and makes a determination.
- The determination, which is based on the majority opinion of the board and is communicated promptly to the parties by the chairman, is only a recommendation and an explanation of the board's rationale. It is not legally binding.
- The cost of forming and operating the board is split between the owner and the contractor. For most projects, this cost is quite affordable, typically representing only 0.05% to 0.25% of contract value.
A study of U.S. construction projects over the past 30 years conducted by the Dispute Resolution Board Foundation-a non-profit organization dedicated to promoting the resolution of legal disputes-found that a dispute resolution board was employed in more than 2,400 highway, bridge, and tunnel projects. In contrast, the study concluded that only one combined cycle power project employed a dispute resolution board: the 674-MW Salem Harbor project in Boston, Mass, owned by Footprint Power Corp.
What's the Problem?Why have so few combined cycle projects employed a dispute resolution board? Perhaps it's simply because power producers in the regulated era grew accustomed to resolving their disputes in front of a public utility commission (PUC). In other words, power producers were relying on the PUC to be their defacto dispute resolution board. Or perhaps it's because the power industry doesn't have as much experience as the transportation industry in using contractors.
Deregulated power producers have been relying on engineering, procurement, and construction (EPC) contractors only since the 1980s. In contrast, the transportation industry has relied on contractors dating all the way back to the interstate highway program in the 1950s.
One power industry contracts expert suggested yet another reason that so few combined cycle projects employed a dispute resolution board. The 20-year industry veteran told us confidentially that a dispute resolution board sounds similar to an arbitration panel, and that those panels have a reputation in the power business as "a lawyerly bunch of bureaucrats deciding how to split the baby, instead of equitably settling the issue."
If that's true, then it explains why a proposal to increase our industry's use of dispute resolution boards at the 2017 workshop, "Combined-cycle capital projects: Managing risk in outages and new construction," was greeted with a deafening silence by the crowd of EPC contractors, project owners, and insurance carriers. Despite the negative response, we believe that dispute resolution boards deserve more consideration!
We hope you'll participate in the next industry debate on the topic when the HRSG User's Group conducts its 2018 workshop, "The Future of HRSG O&M, Design, Commissioning and New Projects." The workshop is open to all industry participants, so please join us February 12-14, 2018, at the Hilton Americas-Houston, and tell us what you think of dispute resolution boards, whether your opinion is good, bad, or undecided. For more conference information and to register, visit: www.hrsgusers.org/conference.
-Rob Swanekamp, PE is executive director of HRSG User's Group Inc. and Peter Weeks, PE is power industry consultant for McCartan Weeks Services LLC.
The post Could Dispute Resolution Boards Keep Combined Cycle Projects on Schedule? appeared first on POWER Magazine.