Vogtle 2 Installs World’s First Full Accident-Tolerant Fuel Assemblies
The world's first complete advanced nuclear fuel test assemblies containing accident-tolerant fuel (ATF) have been installed at Southern Co.'s Alvin W. Vogtle Electric Generating Plant's Unit 2 in Georgia.
Nuclear giant Framatome delivered four GAIA lead fuel assemblies containing enhanced ATF (EATF), including both pellets and cladding, to the plant owned by Georgia Power in January. Southern Nuclear, a Southern Co. subsidiary that operates the plant, installed the assemblies during the unit's spring refueling outage that began on March 10 and ended April 3.
According to John Williams, Southern Nuclear fuel and analysis director, installation of the ATF assemblies marks a significant advancement in the potential commercial deployment of ATF technology. "This innovative technology is expected to enhance the plant's already robust safety performance, as well as potentially lower plant operating costs," he said on April 5.
In a blog post, the Nuclear Energy Institute (NEI), the trade group that represents most nuclear generators in the U.S., noted the ATF concept also "offers a potential solution to a challenge posed by Southern Nuclear's Executive Vice President and Chief Nuclear Officer Danny Bost: to pursue an ATF concept that would increase safety, provide greater efficiency, reduce fuel costs and extend the fuel cycle at Vogtle from 18 to 24 months by the time Vogtle 3 and 4 come online."
"Framatome answered the call and delivered the product we were looking for in the timeframe that we needed it," said Jennifer Baker, Southern Nuclear's pressurized water reactor fuel engineering manager and the project lead for the Vogtle 2 fuel load. "Longer fuel cycles would ultimately be a win for the communities that our fleet is proud to serve by potentially lowering plant operating costs," said Baker.
Framatome, too, celebrated the milestone. Lionel Gaiffe, senior executive vice president at Framatome's Fuel Business Unit, applauded Southern Nuclear's "consistent support of EATF initiatives," noting the company was "pleased to deploy an economical advanced fuel technology that offers operators additional response time and greater operational flexibility."
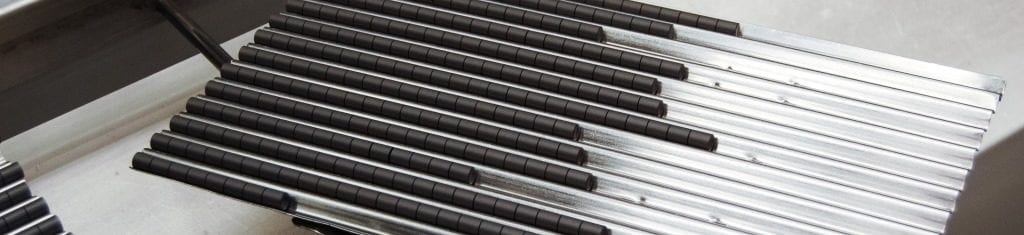
Chromia-enhanced fuel pellets have a small amount of Cr2O3, or chromia, added to the current industry standard uranium dioxide (UO2) powder. This addition changes some properties of the fuel pellets to improve performance under accident conditions. Courtesy: Framatome
Accident-Tolerant Fuel Is PromisingATF is an industry concept used to describe new technologies-in the form of new cladding and/or fuel pellet designs-that further enhance the safety and performance of nuclear materials. While ATF technologies have been under development since the early 2000s, they have received a marked boost in the wake of the Fukushima accident in March 2011 as the U.S. Department of Energy (DOE) aggressively implemented plans under its congressionally mandated EATF program to develop ATFs for existing light water reactors. The program today casts a wide net of collaboration that includes several U.S. utilities, universities, and the Electric Power Research Institute (EPRI).
The DOE has provided funding and technical backing for advanced ATF fuels concepts-including for fuel pellet and cladding materials. Concepts are under development by GE's Global Nuclear Fuel (GNF), Westinghouse, General Atomics, and Framatome. This January, for example, the DOE awarded GNF, Westinghouse, and Framatome $111.2 million through January 2021 to boost ATF development-with stiff requirements. During the first 14-month budget period, all three vendors must ensure an initial lead test assembly has been installed in a U.S. commercial power plant, and that prototypic pin segments have been installed in the Idaho National Laboratory's Advanced Test Reactor's (ATR) water loop.
If Congress approves it, the agency is planning to provide an additional $55.6 million to the three developers in fiscal year 2020 and $30 million in fiscal year 2021 to continue ATF development. With those funds, "the vendors will expand operation of ATF-related concepts in DOE facilities-INL ATR, INL Transient Reactor Test (TREAT) facility, and out-of-pile tests-and commercial reactors with prototypic segments and rods," the DOE said. "The companies would be expected to have agreed-upon licensing plans developed for future NRC approval for initial partial core loadings into commercial nuclear power plants during the mid-2020s."
(For more, see, "Accident-Tolerant Fuels Could Be a Boon for Nuclear Industry" inPOWER's April 2018 issue.)All three vendors appear to have made significant progress on their products. In March 2018, Southern Nuclear installed test ATF assemblies containing fuel segments made by GNF at the Edwin I. Hatch Nuclear Plant in southeastern Georgia. That test, which will assess iron-chromium-aluminum fuel cladding material known as "IronClad" and coated zirconium fuel cladding known as "ARMOR," is slated to end in March 2020.
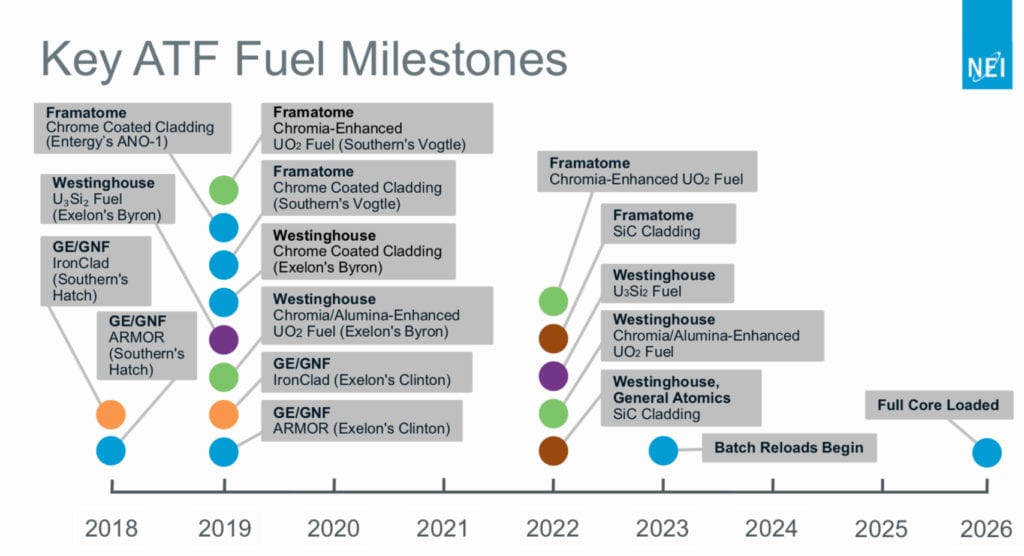
"ATF: An Industry Perspective," Regulatory Information Conference, Ben Holtzman, NEI, Feb. 15, 2019.
And this year, Westinghouse could test its uranium silicide fuel, chomia/alumina-enhanced fuel uranium dioxide fuel, and chrome-coated cladding at Exelon's Byron nuclear plant. GNF is also slated to test its IronClad and ARMOR products at Exelon's Clinton plant, and Framatome will test its chrome-coated cladding at Entergy's Arkansas One plant. The NEI suggests more milestones for silicon carbide cladding products being developed separately by Framatome and Westinghouse (in collaboration with General Atomics) could be announced in 2022.
Technical Triumph Through International CollaborationAt Vogtle 2, Southern Nuclear plans to test Framatome's EATF concept, which it helped developed under Framatome's PROtect program, for 18 months, until the next refueling outage. The assemblies feature Framatome's advanced chromium coating, which is added to its proprietary M5 zirconium alloy cladding. The combination "improves high-temperature oxidation resistance and reduces hydrogen generation during loss of cooling," the company explained. "The chromium coating also greatly reduces creep to maintain a coolable geometry and has mechanical properties that allow for more operator response time. Further, the innovative coating offers increased resistance to debris fretting during normal operations."
The assemblies also include chromic-enhanced fuel pellets, which "have a higher density, reduced fission gas release, and improved behavior during loss of cooling. Reduced Pellet Clad Interaction (PCI) also better supports power maneuvering," Framatome said.
Framatome, which fabricated the fuel assemblies at its fuel manufacturing facility in Richland, Washington, as part of a 2017 contract with Southern Nuclear, said it worked for several years with the DOE's EATF program, to "significantly improve" on its initial target to deploy the concept by 2022. The company is in tandem also expanding development efforts on its silicon carbide cladding concepts, it said.
Framatome also credits European partners, including France's Atomic Energy Commission, for initially exploring and identifying a suitable cladding coating process. Technology collaborators also include French utility EDF, which owns 75% of Framatome (Mitsubishi Heavy Industries owns 19.5%, and international engineering firm Assystem, the remaining 5%). Framatome also noted a series of research and development projects at Gisgen nuclear power plant in Switzerland helped develop new methodologies, irradiation capabilities, and equipment to support innovative fuel and cladding material characterization, which were applied to the EATF materials.
NEI: Decisions to Pursue ATFs Need to Be Made 'Urgently'As the NEI's director of fuel cycle programs, Nima Ashkeboussi, told POWER on April 5, installation of Framatome's ATF assemblies marks "an important milestone for the U.S. nuclear industry as we move a step closer to commercial deployment of ATF. Advanced fuels are designed to help our current fleet perform more efficiently and make our plants even more safe. By investing in these innovative fuel designs, the industry is further demonstrating our commitment to lead the country to a clean energy future."
ATFs offer so much promise that In December 2016, industry coalesced (under NEI's sponsorship) to form an ATF working group to assess its potential safety and economic benefits, and to determine how to accelerate licensing of products for earlier deployment. The ATF working group includes Exelon, TVA, Duke Energy, Southern, Dominion, APS, Xcel, GE Hitachi, Framatome, Westinghouse, Lightbridge, General Atomics, X Energy, Jensen Hughes, EPRI, and NEI.
The group later established a task force to focus on safety benefits. In a February 2019 technical report, "Safety and Economic Benefits of Accident Tolerant Fuel," the task force notes improved material response of ATF provides "additional margin during postulated accidents, operational transients, and normal operation; this increased margin reduces the likelihood of fuel failure."
Depending on their application, ATF products could also increase fuel cycle flexibility-by enabling an increase in allowable burnout and improving thermal margins-and optimize fuel loading and/or cycle length to minimize fuel costs. "Plants previously unable to economically transition to 24-month cycles may become able to do so with implementation of higher allowable burnup and higher enrichments. This will reduce the frequency of plant refueling outages, further reducing worker exposure and outage costs," it said. Increased fuel robustness could also improve a plant's ability to respond to changing conditions to accommodate variable generation, like wind and solar.
And, by improving resistance to mineral deposits on the fuel cladding, ATF products promise to accommodate more aggressive water chemistry, reducing inventory of minerals in the coolant, and crud buildup. Finally, and as significantly, "By reducing batch loading sizes or by extending cycle lengths, fewer assemblies would be used to produce the same amount of electricity. This reduces the amount of fuel that needs disposal and billions of dollars would be saved on the back end of the fuel cycle (i.e., spent fuel treatments)," it notes.
However, early and widespread adoption of ATF products "is predicated on an economic business case that overcomes the costs associated with a new fuel product being inserted into a reactor," the report warns.
The extensive analysis, changes in manufacturing processes, and readying concepts for regulatory scrutiny represent "significant investments." Economic benefits offered by new ATF concepts will also depend on how much the new fuel product will "support a wide range of operating conditions, and the ability to translate that wider range of allowable operating conditions into plant equipment and operating strategies that ensure safety and reduce operating costs," it notes.
If industry wants to reap the maximum benefits that ATF products could offer to the environment, consumers, and plant operators, "any decision to pursue ATF products will need to be made urgently," the report concludes.
"The future sustainability of the commercial light water reactor fleet depends on industry's ability to innovate at a pace which will allow the plants to remain economically competitive with other rapidly advancing energy technologies," it says.
-Sonal Patelis a POWER associate editor (spatel@powermag.com, @POWERmagazine.com)
Updated (April 6): Adds quotes and information from NEI
The post Vogtle 2 Installs World's First Full Accident-Tolerant Fuel Assemblies appeared first on POWER Magazine.