This Inside-Out Motor for EVs Is Power Dense and (Finally) Practical
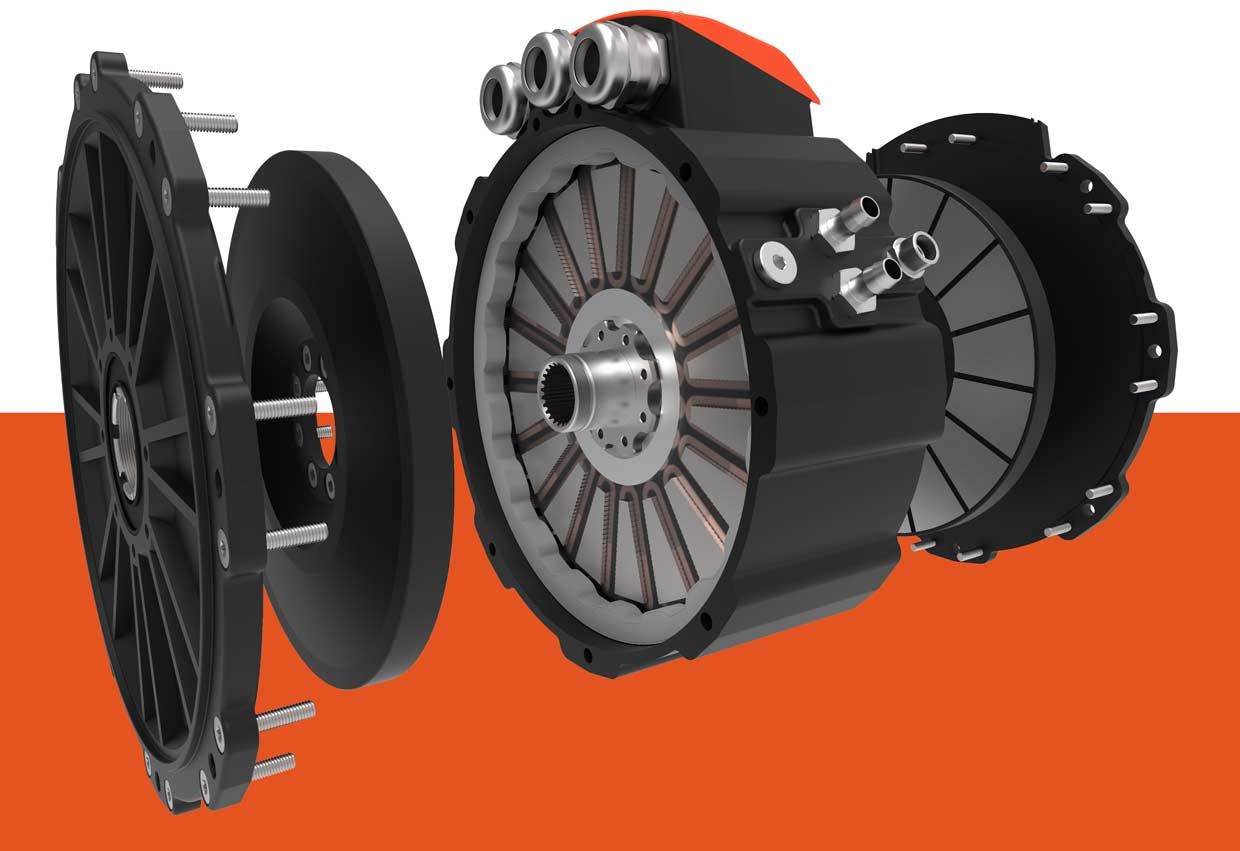
The world is electrifying fast. Manufacturing processes, cars, trucks, motorcycles, and now airplanes are making the move to electrons that Edison predicted more than a century ago. And they are all doing so for much the same reasons: quieter operation, reduced maintenance requirements, better performance and efficiency, and a more flexible use of energy sources.
At the heart of this great process of electrification stands the electric machine, filling either the role of a generator, for turning mechanical energy into electricity, or that of a motor, for doing the opposite.
For a long time, electric machines have hewed to a standard design, which has had the advantage of being very easy to manufacture. However, our startup, Magnax, based in Belgium, has taken another design that in theory can wring much more power and torque from a given mass and has made it commercially practical. We believe this new design can supplant the old one in many applications, notably in electric vehicles, in which it is now being tested.
One of our designs has a peak power density of around 15 kilowatts per kilogram. Compare that with today's motors, such as the one in the all-electric BMW i3, which delivers a peak power density of 3 kW/kg-or just one-fifth as much. And the Magnax machine is also more efficient.
We believe that we can scale the design to whatever size carmakers (and other customers) may demand. If so, then there is every reason to believe that this design will push aside the traditional one. If it does, it will help to improve performance, save on energy and overall operating costs, and reduce carbon emissions for a better world.
The concept of an electric machine is simple. You start with a housing, which is called a stator because it remains stationary. Then you add a rotor, which spins, usually inside the stator but sometimes outside, an idea we'll discuss later. When the machine is functioning as a motor, the magnetic fields of the stator and the rotor interact: Strategically placed magnets around the circumference of the rotor and stator repel or attract each other in a sequence to sustain the rotor's spin and create torque. In this way, the machine converts electrical energy to mechanical energy. When the machine functions as a generator, the process operates in reverse.
Such a rotating machine today generally uses permanent magnets rather than electromagnets in the rotor and is thus called a permanent-magnet synchronous machine (PMSM). When operating as a motor, it passes alternating current to structures in the stator known as teeth. The result is a rotating magnetic field in the stator that acts on the permanent magnets of the rotor, spinning it.
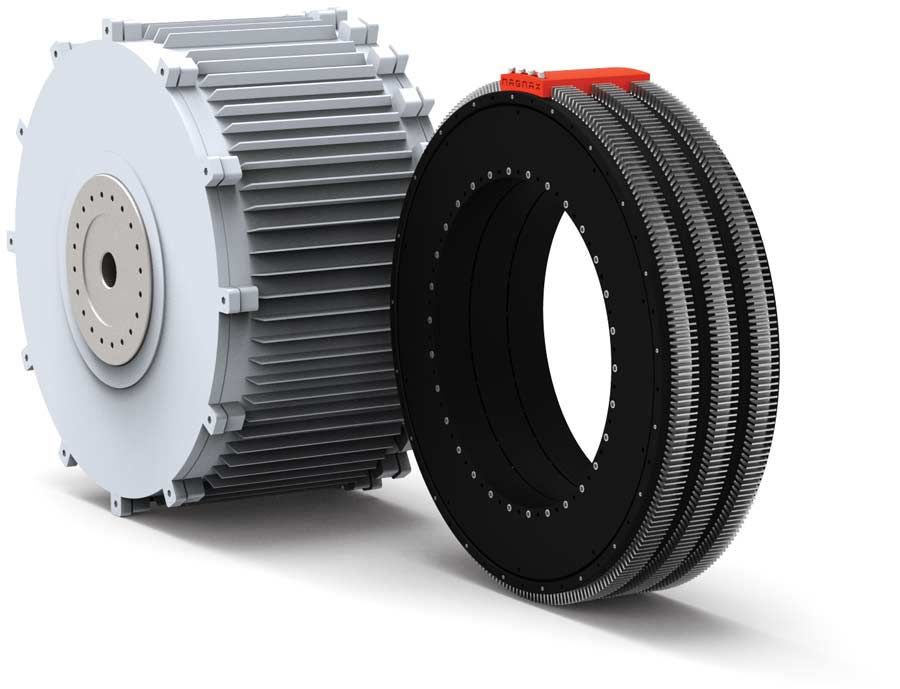
The big advantage here is that permanent magnets don't need energy to create a magnetic field. That makes this design more efficient and more powerful for a given weight and volume than a machine that uses electromagnets in the rotor.
There are many compelling reasons why PMSMs began to dominate in the 1980s, but the most important one was the development of a much more powerful breed of permanent magnet, based on neodymium. Nevertheless, because there was no change in the overall layout of the machine, the new magnet could provide only an incremental improvement. To further reduce the weight, size, and cost of the machine, the electromagnetic interaction had to be fundamentally rethought. That's what we've done. We call our product a yokeless axial-flux permanent-magnet machine.
It's a mouthful, and we'll explain it in a moment. First, though, it's important to understand that people already knew that the axial-flux topology had intrinsic advantages. It's just that there seemed to be no way to exploit those advantages commercially, mainly because a design based on them would be hard to mass-produce using automated procedures.
Before we could begin designing our motor, we had to overcome a fundamental problem: There was no commercially available software that could accurately and simultaneously model the electromagnetic and thermodynamic properties of an axial-flux motor. However, Peter Sergeant and Hendrik Vansompel of Ghent University, in Belgium, have been working on this problem since 2008. Their efforts, combined with several years of R&D and prototyping by Magnax, led to our design and our manufacturing methods.
A traditional, radial-flux machine puts the rotor inside the stator. Here the stator consists of a supporting part, called the yoke, which is fitted with teeth that contain electromagnet coils. The teeth thus function as magnetic poles. As the rotor turns, its own poles transmit flux every time they sweep past a stator tooth, and the stator carries the flux elsewhere-closing what's called the flux loop. The flux is routed from the rotor's permanent magnet through the air gap and the stator teeth, taking a 180-degree bend through the yoke and back to another magnet. Meanwhile, of course, the interaction between the permanent magnets and the rotating electromagnetic field in the stator teeth keeps the rotor spinning.
For highest efficiency, the design should minimize the distance-the air gap-between the rotor and the stator teeth, because air transports magnetic flux poorly.
Our axial-flux machine turns that traditional arrangement inside out. It uses not one but two rotors, on either side of the stator, bracketing it. In this arrangement, the stator merely functions as the bearer of the electromagnetic teeth, not as the support-or yoke-for the rotor. In other words, it creates the possibility of a stator that is yokeless-hence the inclusion of this word in the name.
Eliminating the yoke-basically a steel cylinder that composes about two-thirds of the stator iron-saves an enormous amount of weight. As a result, yokelessness more than doubles the machine's power density, compared with that of the older, yoked axial motors, and quadruples it compared with that of a traditional motor (like the one in the BMW i3). It also improves efficiency by reducing a bane of electric machines: iron loss.
Iron loss is mainly the result of two phenomena. First, there is the energy consumed when alternating current repeatedly magnetizes and demagnetizes cores in the stator-a process called hysteresis loss. Second are the losses to eddy currents, which are created by the varying magnetic flux through the cores.

Wide and Thin: This large prototype shows the flat shape of the axial-flux design.
There are other reasons why the design is so power dense. In this design, the magnetic flux goes from the permanent magnets on the first rotor disk, through the stator core to the permanent magnets on the second rotor disk-a relatively short and straight path.
Thanks to that unidirectionality, Magnax can further decrease the flux losses in the iron by 85 percent by using a material that's perfect for conducting flux in one direction only-grain-oriented steel. Such steel couldn't go into a traditional, radial-flux motor or generator because such machines route the flux from the rotor through the stator and back to the rotor-a multidirectional route. Magnax closely collaborated with Thyssenkrupp Electrical Steel on the design of the laminated grain-oriented cores.
Other advantages: In our yokeless axial-flux design the stator needs only about 60 percent as much copper and the rotor needs about 80 percent as much magnetic material than would a radial-flux motor of comparable power and torque.
In theory, all of these advantages make possible a relatively inexpensive and lightweight machine that delivers a lot of torque. But actually building such a machine meant facing down several serious engineering challenges.
The most obvious involve finding ways to replace the traditional functions of a yoke. In a conventional motor, the yoke holds the stator teeth in place and provides a thermal path for transporting the heat from the coils to the motor casing. It also serves as a path that closes the loop along which the magnetic flux flows when returning to its original source.
First, Magnax had to solve the mechanical challenges. Because there is no yoke to connect the individual stator teeth, another solution had to be found to create a stator with sufficient strength and stiffness to hold the teeth firmly in place even as they are wrenched by powerful electromagnetic forces.
Next came the thermal challenges. Because the windings are buried deep inside the stator and between the two rotor discs, the heat they generate can be hard to disperse. Better cooling lets you increase a machine's nominal power-that is, the actual mechanical power it puts out. Older axial-flux concepts-those that use a yoke-cool the coils by integrating a cooling channel in the yoke. However, that arrangement makes the heat flow through the yoke, and iron is not particularly good at transporting heat. Because the Magnax design has no yoke, we needed to find another way to directly cool the coils.
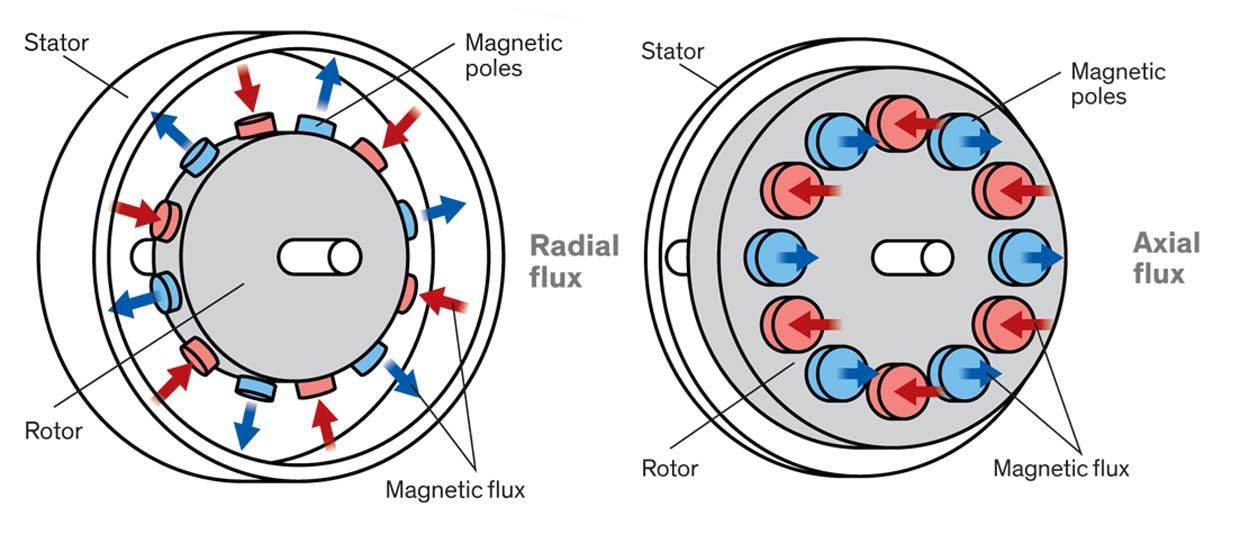
Manufacturing was yet another challenge. Existing axial-flux machines have always been hard to manufacture because the stator and the windings are complex. That's why until now such machines generally didn't lend themselves to automated production. These challenges translate to higher cost and very poor scaling, which can be seen in most of the axial-flux designs that are now commercially available.
Yokeless concepts, however, have a simpler winding scheme, which saves on labor. So cooling emerged as one of the biggest challenges. YASA, in England, another developer of yokeless axial-flux motors, has a manufacturable motor concept; the company uses oil cooling and is building its own factory for volume production in the United Kingdom. Magnax's design uses a different, and more flexible, cooling scheme.
Magnax has one that can use a number of coolants, notably air, water-glycol, and oil. Air cooling is preferred for use in drones and in two- and three-wheel electric vehicles (popular in India, for instance). It's also good in big machines, such as wind-turbine generators. Liquid cooling is better for maximum power densities, in combination with gearboxes. Thus, it is often used in automotive applications.
We start by laminating aluminum or copper heat sinks in close thermal contact with the windings. The heat sinks transport the heat to the outer perimeter, where it can be carried away by cooling fins or a water-cooling jacket. This not only gives the machine a much higher capacity to evacuate heat, making it possible to produce greater nominal torque and power, it also allows for a very stiff and completely solid stator construction. That means that the machine can handle a lot of torque and still last for a long time.



At the moment, our focus is on custom motor designs for automotive original-equipment manufacturers and their suppliers. Because axial-flux motors have a short axial length, they can help keep the power train short. That proves useful to automakers that integrate the motor, the transmission, and the electronics into an electric vehicle's axle, an assembly called an eAxle. These motors are also very useful in a hybrid design, where the combination of an engine and an electric drive system usually leaves little room for the motor.
Our design is also suited for in-wheel applications, where the motor goes right inside the wheel assembly. That configuration has many advantages-for instance, you can help to steer the car by varying the torque at each wheel, a trick known as torque vectoring. However, putting the motor in the wheel increases the unsprung mass-the part of a car that's between the suspension and the road-and that can make the ride bumpier. Every gram of weight saved on an in-wheel motor is therefore golden.
A European carmaker is now track-testing an in-wheel car concept that uses four Magnax motors, all made in the "outrunner" configuration. That's where the spinning part of the motor is on the outside (rather than on the inside, on a shaft), making the machine ideal for integration inside the very tight spaces within a wheel assembly. Here, too, the result is a power density that's twice as high as a conventional motor's, with higher efficiency to boot.
Although most car designs don't put motors right inside the wheels, many do use more than one motor in the vehicle. In fact, any car that uses multiple motors will benefit particularly from our product. The more motors you carry, the more important it is that they be light and compact. We have calculated that the absence of a yoke and its associated iron losses can increase the range an EV could travel by 7 percent in a car with a single motor and up to 20 percent in a car with two motors. Imagine the further effects on the battery, which is the most expensive part of an EV.
The main challenge now is to bring the concept into series production; Magnax will organize this together with production partners. We have invested a lot of time in the design for manufacturing our machines. As a result, we can prove that our machines can be produced. This capability, together with the savings we can realize on materials, makes our concept competitive on price-a key point for graduating from the niche markets to the original-equipment manufacturers.
The assembly line we are building will be capable of producing motors of several diameters. We plan to begin producing 25,000 motors per year by 2022 and to scale to hundreds of thousands later on.

Over the past two years we've had inquiries from hundreds of companies that are interested in motors of widely varying diameters for use in electric motorcycles, trucks, and other EV applications. In addition, we still receive requests from makers of wind turbines and industrial equipment. These particular markets are not our highest priority, but the widespread demand shows that our technology has what many companies need: compactness, power, and efficiency.
Our design can cut costs substantially in a high-volume business-for instance, the production in China of millions of motors of between 1 and 10 kW. When producing in large quantities, what counts is limiting the cost of the raw materials, which as we've shown is significantly lower than for traditional motors.
Tens, even hundreds of millions of electric motors were sold in 2017, for a total of some US $97 billion. Their average efficiency remains below 90 percent.
In tests at the University of Ghent on the first prototype, our yokeless axial-flux motor reached efficiencies from 91 to 96 percent. And that was just the prototype.
Motors and motor systems account for approximately 53 percent of global electricity consumption. We estimate that improving the efficiency of all the world's motors by just 1 percent would reduce the motors' power consumption by 94.5 terawatt-hours and shrink their carbon dioxide footprint by the equivalent of 60 million metric tons.
If yokeless axial-flux machines replaced only a fraction of the older machines, we would save our customers some money and make the planet more livable while we're at it.
This article appears in the October 2019 print issue as "Turning the Electric Motor Inside Out."
About the AuthorsDaan Moreels is a cofounder of Magnax, in Kortrijk, Belgium, and Peter Leijnen is the company's founder.