Toshiba’s Light Sensor Paves the Way for Cheap Lidar
The introduction of fully autonomous cars has slowed to a crawl. Nevertheless, the introduction of technologies such as rearview cameras and automatic self-parking systems are helping the auto industry make incremental progress towards Level 4 autonomy while boosting driver-assist features along the way.
To that end, Toshiba has developed a compact, highly efficient silicon photo-multiplier (SiPM) that enables non-coaxial Lidar to employ off-the-shelf camera lenses to lower costs and help bring about solid-state, high-resolution Lidar.
Automotive Lidar (light detecting and ranging) typically uses spinning lasers to scan a vehicle's environment 360 degrees by bouncing laser pulses off surrounding objects and measuring the return time for the reflected light to calculate their distances and shapes. The resulting point-cloud map can be used in combination with still images, radar data and GPS to create a virtual 3D map of the area the vehicle is traveling through.
However, high-end Lidar systems can be expensive, costing $80,000 or more, though cheaper versions are also available. The current leader in the field is Velodyne, whose lasers mechanically rotate in a tower mounted atop of a vehicle's roof.
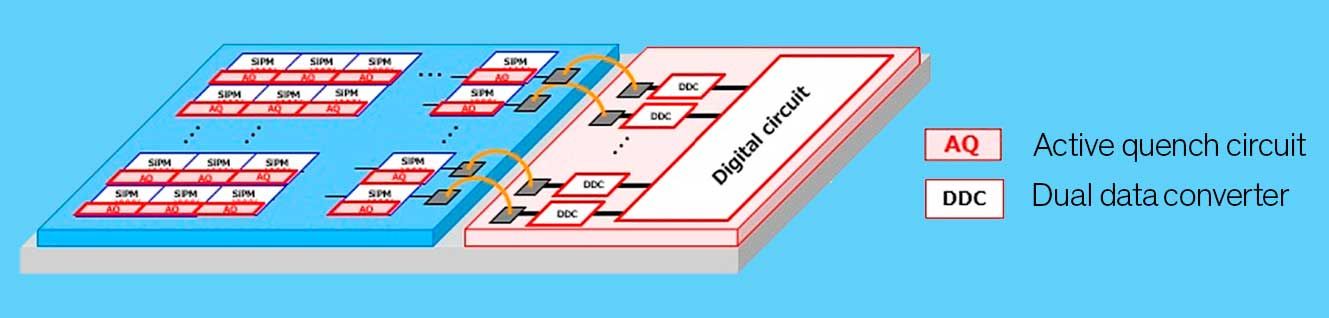
Solid-state Lidar systems have been announced in the past several years but have yet to challenge the mechanical variety. Now, Toshiba hopes to advance their cause with its SiPM: a solid-state light sensor employing single-photon avalanche diode (SPAD) technology. The Toshiba SiPM contains multiple SPADs, each controlled by an active quenching circuit (AQC). When an SPAD detects a photon, the SPAD cathode voltage is reduced but the AQC resets and reboots the SPAD voltage to the initial value.
Typical SiPM recovery time is 10 to 20 nanoseconds," says Tuan Thanh Ta, Toshiba's project leader for the technology. We've made it 2 to 4 times faster by using this forced or active quenching method."
The increased efficiency means Toshiba has been able to use far fewer light sensing cells-down from 48 to just 2-to produce a device measuring 25 m x 90 m, much smaller, the company says, than standard devices measuring 100 m x 100 m. The small size of these sensors has allowed Toshiba to create a dense two-dimensional array for high sensitivity, a requisite for long-range scanning.
But such high-resolution data would require impractically large multichannel readout circuitry that comprises separate analog-to-digital converters (ADC) for long distances scanning, and time-to-digital converters (TDC) for short distances. Toshiba has overcome this problem by realizing both ADC and TDC functions in a single circuit. The result is an 80 percent reduction in size (down to 50 m by 60 m) over conventional dual data converter chips.
Our field trials using the SiPM with a prototype Lidar demonstrated the system's effectiveness up to a distance of 200 meters while maintaining high resolution-which is necessary for Level 4 autonomous driving," says Ta, who hails from Vietnam. This is roughly quadruple the capability of solid-state Lidar currently on the market."
Factors like detection range are important, especially in high-speed environments like highways," says Michael Milford, an interdisciplinary researcher and Deputy Director, Queensland University of Technology (QUT) Center for Robotics in Australia. So I can see that these [Toshiba trial results] are important properties when it comes to commercial relevance."
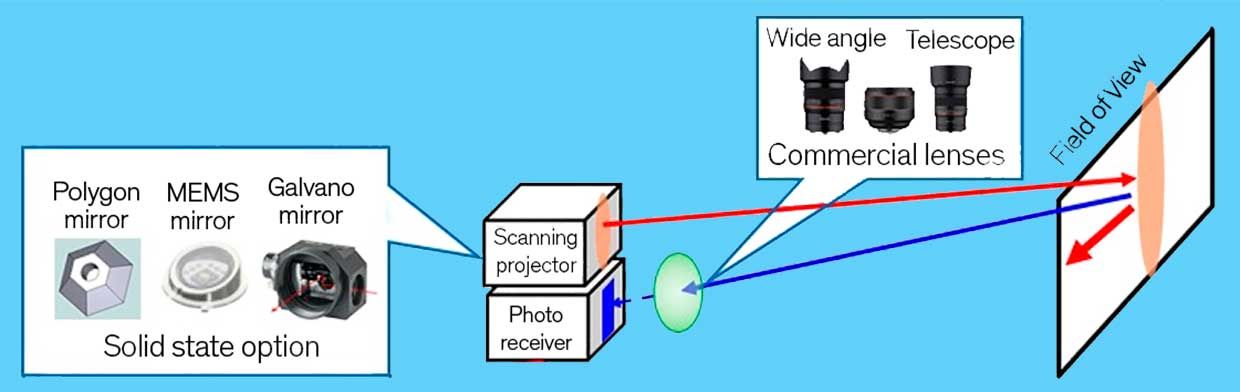
And as Toshiba's SiPM employs a two-dimensional array-unlike the one-dimensional photon receivers used in coaxial Lidar systems-Ta points out its 2D aspect ratio corresponds to that of light sensors used in commercial cameras. Consequently, off-the-shelf standard, telephoto and wide-angle lenses can be used for specific applications, helping to further reduce costs.
By comparison, coaxial Lidar use the same optical path for sending and receiving the light source, and so require a costly customized lens to transmit and then collect the received light and send it to the 1D photon receivers, Ta explains.
But as Milford points out, If Level 4+ on-road autonomous driving becomes a reality, it's unlikely we'll have a wide range of solutions and sensor configurations. So this flexibility [of Toshiba's sensor] is perhaps more relevant for other domains like drones, and off-road autonomous vehicles, where there is more variability, and use of existing hardware is more important."
Meanwhile, Toshiba is working to improve the performance quality of its SiPM. We aim to introduce practical applications in fiscal 2022," says Akihide Sai, a Senior Research Scientist at Toshiba overseeing the SiPM project. Though he declines to answer whether Toshiba is working with automakers or will produce its own solid-state Lidar system, he says Toshiba will make the SiPM device available to other companies.
He adds, We also see it being used in applications such as automated navigation of drones and in robots used for infrastructure monitoring, as well as in applications used in factory automation."
But QUT's Milford makes this telling point. Many of the advances in autonomous vehicle technology and sensing, especially with regards to cost, bulk, and power usage, will become most relevant only when the overall challenge of Level 4+ driving is solved. They aren't themselves the critical missing pieces for enabling this to happen."