Power Plant Decommissioning Tips to Save Time, Money, and Hassle
The post Power Plant Decommissioning Tips to Save Time, Money, and Hassle appeared first on POWER Magazine.
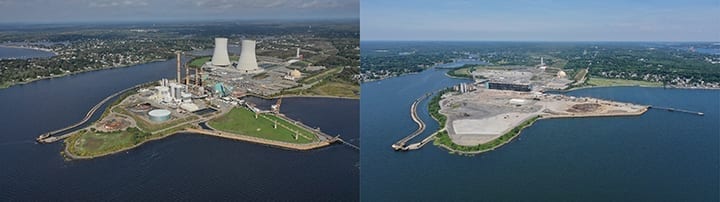
All power plants have a finite useful life. Thus, there will come a time at every facility when the unit must be retired and the decommissioning process undertaken. Decisions must be made on who will do the work, how long to allot for the job, and what to do with the site in the end. Fear not, however, there are best practices your company can follow to ensure everything goes smoothly.
When you talk to decommissioning experts, the most important message that seems to come out of the conversations is that companies need to have a clear vision for the final outcome before they start the decommissioning process. Begin with the end in mind," Jeff Kopp, managing director of Utility Consulting with 1898 & Co., part of Burns & McDonnell, said, borrowing a quote from the late self-help author Stephen R. Covey.
Randall Jostes, CEO of Environmental Liability Transfer Inc. (ELT), a comprehensive environmental liability assumption company that acquires retired facilities (Figure 1), handles the decommissioning activities, and repurposes the sites, agreed. We start with the reuse in mind. In other words, we have internal land planners that look at the market-look at the infrastructure of the site-to determine its highest and best future use," he said.
![]() |
1. In December 2018, Environmental Liability Transfer Inc. (ELT) assumed the environmental liabilities at the retired 1,600-MW coal-fired Brayton Point Power Station in Somerset, Massachusetts. Today, the site is being transformed into a world-class logistical port and support center, which will be capable of component manufacturing, staging, operations, and maintenance for offshore wind and other related sectors. The image on the left was taken Oct. 9, 2019, and the image on the right was taken July 27, 2020. Courtesy: ELT |
By understanding and planning for the future use in the beginning, mistakes, such as placing an impoundment in an area that might impede development, can be avoided. In some cases, it can also allow structures to be saved and utilized, rather than just scraping a site clean.
We start with our development concept upfront, and then everything we do is designed to get the site ready for that purpose," Jostes told POWER.
Risk ManagementIt's never too early to start planning," said Kopp, suggesting that much of the initial preparation should be predicated on risk. You've got to look at the individual plant and what level of risk it has," he said. Some of these older coal plants that have been operating for a long time have environmental risks, such as asbestos and PCBs [polychlorinated biphenyls], where I think you've got to carry a higher level of contingency because there's just a lot more unknowns and a lot greater likelihood that you're going to run into some cost overruns."
Commercially speaking, one of the key considerations is understanding risk in the context of various contract structures and designing the decommissioning project to balance risk and expenditure," said Erin Carroll, senior vice president and managing director of PowerAdvocate's Client Services team, a group that helps companies better manage costs through supply chain spending. For example, lump sum contracts are popular. How are owners evaluating lump sum prices compared to the obligations of the owner? Conversely, in a target price contract, how is risk shared and aligned with the contractor's incentives to drive savings?"
This leads to perhaps the biggest decision that owners must make, whether to self-perform or outsource the project (see sidebar). Jostes suggested a company such as ELT can speed up the decommissioning process, reduce the overall cost, eliminate much of the risk, and relieve the stress that comes with self-performing the work.
Decommissioning Experience Could Benefit Nuclear Plant Owners In the 1940s, the Oak Ridge Gaseous Diffusion Plant was built in unprecedented secrecy as part of the Manhattan Project. Its purpose was to provide enriched uranium for the world's first atomic bomb, and it expanded operations during the Cold War, producing enriched uranium for defense and commercial purposes. Uranium enrichment operations were halted at the site in 1985, and the plant was officially closed in 1987. During the next decade, as cleanup became the main focus at the site, it was renamed East Tennessee Technology Park (ETTP) to reflect the U.S. Department of Energy's (DOE's) ambition of transforming it into a multi-use industrial park. Recent efforts have also focused on establishing the site as a national park and conservation area. The DOE's goal is to complete the cleanup this year, marking the first time an entire enrichment complex has been cleaned and demolished. UCOR, an Amentum-led partnership with Jacobs, has been the prime cleanup contractor for ETTP since 2011. Kenneth Rueter, president and CEO of UCOR, suggested the lessons learned at ETTP are also important for the power industry. In many ways, UCOR has provided a model for commercial nuclear plant decommissioning in an even more hazardous environment," he told POWER. Cleanup at ETTP included the demolition of five massive uranium enrichment buildings, as well as hundreds of facilities that supported research and operations at the site. The largest of these facilities was the K-25 Building, a U-shaped, mile-long building that was the largest building in the world when it was constructed. Since large-scale cleanup operations began nearly 15 years ago, more than 13 million square feet of facilities have been demolished. Many of these facilities were contaminated and in dilapidated condition. Some of the site operations also contaminated underlying soil, which forced cleanup crews to remove approximately 30,000 truckloads of soil. To date, almost 1,300 acres have been transferred for economic development with another 600 slated for transfer in the years ahead. More than 3,000 acres have been placed in a conservation easement for recreational use, and another 100 acres have been designated for historic preservation. Our ability to safely decommission nuclear facilities and dispose of waste without harm to the public or environment is directly related to the future of nuclear power generation in the United States and across the world. That is because the public and lawmakers need to have confidence that our industry has the ability to do that," Rueter said. Learn more about the project, and the challenges UCOR faced, online at powermag.com (see The POWER Interview: Cleaning Up a Radiologically Contaminated Site"). |
It's a matter of putting a compelling economic equation in front of these utilities, showing them that our process is economically superior. And it's quicker. And it's guaranteed," Jostes said. He noted that many of the communities affected by a plant closing have lost jobs and are looking for redevelopment. We have all of that in-house," he said. Instead of going out to market, the utility really is getting everything that is required to decommission, reposition, and redevelop the site in one company."
For example, when an owner self-performs a decommissioning project, it often must engage with and solicit bids from a number of specialists, such as demolition companies, asbestos abatement remediation companies, real estate development companies, machine and equipment liquidation companies, and more. That's a lot of work, and there are a lot of different profit centers that are all looking to take a cut. With a firm like ELT, that's all done in-house, and therefore, Jostes said his company can put forth better economic terms that can get the project completed faster. We think we expedite the development of these types of facilities by about 24 months," he said.
Evaluate your internal capabilities to manage this work. The risk is different than operating a plant, or even an onsite capital project, so make sure you have a team-both internal and the combination of external resources-that can manage this type of project and these types of risks," PowerAdvocate's Carroll said.
Keeping Decommissioning Costs DownIf an owner chooses to self-perform, it must assemble a skilled team of people to do the job right. The internal expertise that you need includes staff with good project management experience," Kopp said. This-coupled with bringing in outside assistance where needed-will allow the team to plan for all tasks anticipated. The number one thing is planning and data gathering early, making sure that you've got all the appropriate data for potential contractors. Detailed information will provide the potential demolition contractors with information to get the tightest bids you can possibly get."
Transparency is one of the best practices for keeping an eye on both schedule and costs, and robust data management enables transparency," explained Carroll. By employing data strategies that drive transparency into granular, real-time, and market-based costs, project managers can take proactive steps to control estimates as they become actuals, address schedule issues, and track market factors that may be escalating overall project costs."
It's hard to overemphasize the importance of speed, because time really is money. While projects must be completed carefully and no one should compromise on safety, performing work efficiently, using qualified contractors, can save time and reduce costs. When people try to do these projects piecemeal, and they try to break them out, it results in a lot of inefficiencies and potentially a lot of higher costs," said Kopp.
For example, one owner believed some plant equipment had value for reuse on the secondary market that was higher than scrap value, so they chose to spend time advertising, waiting for bids to come in, reviewing options, and selecting winners. Then, time had to be given for the buyer to deploy a crew to the site to remove the equipment. The work was carried out with little concern for the as-left condition because, after all, the site was being demolished, but the end result was more difficulty for the demolition company, driving up its costs. In the end, scrapping the equipment would have been the more cost-effective option.
In another case, an owner chose to extend a project over a five-year period, rather than completing it straight through from beginning to end. The reasoning was that this would break up the cost over a longer time period. However, it also meant mobilizing and demobilizing crews each year, which was a significant cost. Meanwhile, personnel sometimes changed and even those that didn't had to get reacquainted with the site and the then-current status before work could resume in earnest. The net result was a greatly increased overall cost for the project.
Our view is that managing the data that is generated over the course of the project-from the Class 5 estimate [an early-stage estimate generally prepared based on very limited information] through the final project filing-will facilitate more timely and impactful decisions. Without accurate data, project planning and control software will fail to deliver useful insights for project managers. Priority one is setting a strong data foundation for the project," said Carroll.
-Aaron Larson is POWER's executive editor.
The post Power Plant Decommissioning Tips to Save Time, Money, and Hassle appeared first on POWER Magazine.