Welding Method 7 Approved, Fitness for Service Project Launched
The post Welding Method 7 Approved, Fitness for Service Project Launched appeared first on POWER Magazine.
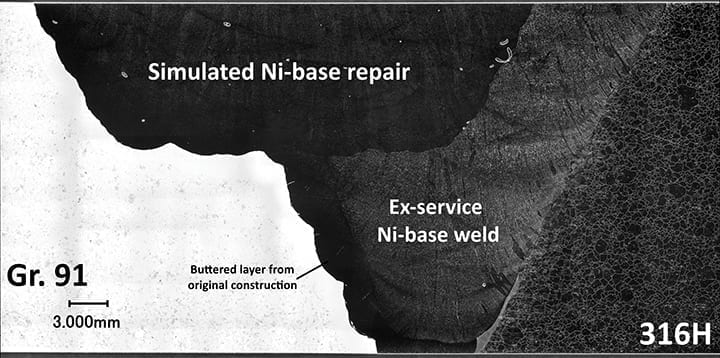
Welding Method 7 (WM7), which was supported by an extensive set of research experiments led by the Electric Power Research Institute (EPRI), was approved in March 2020 by the National Board Inspection Code (NBIC) for its 2021 edition. Going forward, development and approval of alternative repair methods like WM7 are key pillars in a larger emphasis on integrated life management, which must include options for run-repair-replace decision-making.
WM7 allows for dissimilar-metal weld repairs of Grade 91 steel without post-weld heat treatment (PWHT). A consistent challenge for industry is the specification and application of well-controlled field PWHT procedures. For materials like Grade 91 steel, when the essential variables are not understood and addressed, there is significant risk that heat treatment will introduce problems. WM7 will enable the entire power generation industry to routinely repair dissimilar-metal welds between Grade 91 steel and other materials inside a boiler or heat recovery steam generator (HRSG). Specific applications include joining of Grade 91 steel to an austenitic stainless steel or a low-alloy steel such as Grade 22 (P-Number 5A material).
In a related effort, EPRI recently launched a project called Fitness for Service for Critical Components in the Energy Industry." This project will establish a technically acceptable, workable framework for implementing relevant Fitness for Service (FFS) methods that consider the damage-, material-, and component-specific applications. The FFS project will enhance an already robust set of well-engineered guidance for repair and replace criteria, providing stakeholders with run options. This is critical since plants are operating under ever more complex modes, increasing problems while at the same time having fewer resources available for the repair or replacement of affected components.
Grade 91 SteelPower plant applications of creep strength enhanced ferritic (CSEF) steels have increased greatly over the last two decades. One of the most widely utilized CSEF steels is a 9% chromium steel widely known in the industry as T91, P91, or Grade 91.
Since the early 1990s, Grade 91 steel has been used in fossil power steam boilers, HRSGs, and piping systems (Figure 1). When properly processed, this alloy has enhanced properties, including high creep-rupture strength and fracture toughness, compared to traditional low-alloy steels. Higher strength makes Grade 91 attractive because of the potential for higher operating temperatures-up to 1,100F (593C)-and lower wall thickness, with excellent toughness significantly reducing the risk of fast fracture. Grade 91 is, therefore, suitable for use as a retrofit material in conventional subcritical power plants, for plants that will operate in cyclic mode, and as a pressure boundary material for advanced supercritical plants and HRSGs.
![]() |
1. Example of a simulated repair weld in a dissimilar-metal weld between Grade 91 and stainless steel 316H where the original weld deposit was made with multiple nickel (Ni)-base weld consumables. Note that the repair was made with Electric Power Research Institute (EPRI) P87 filler material. Courtesy: EPRI |
Service experience has shown a significant need for onsite weld repairs to Grade 91 steel components. Rather than simply rely on the use of procedures qualified for new construction for these repairs, research has been conducted over the last decade to establish the technology to support a well-engineered weld repair. These new approaches offer rapid, nonconventional welding procedures for minimum cost replacement and repair.
Critical Issues Related to Weld Repair of Grade 91 SteelA number of issues have driven the need to investigate alternative options for weld repair of Grade 91 steel. They include:
New Construction vs. In-service. Historically, the only allowable method for weld repair of Grade 91 steel has been dictated by the rules for new construction-use of a matching filler and mandatory PWHT. However, no relevant research establishes that these repair methods are technically appropriate for in-service components. Indeed, the perception that new construction approaches may be best completely ignores the practical challenges and risks to implementing the sometimes unfeasible or unwarranted restrictions imposed by new construction rules and requirements.
PWHT Issues. Field PWHT maintained within the allowable range of 1,350F to 1,450F (730C to 790C) has proven to be very challenging. Much evidence shows that poor heat treatment practice leads to significant over-temperature exposure. Research also indicates that any excursion above the allowable maximum dramatically reduces the long-term creep strength of Grade 91 steel and its weldments. For these reasons, EPRI published a position paper that provided evidence for modifying the minimum PWHT temperature for Grade 91 steel to 1,250F or 1,300F (675C or 705C) that appeared in the 2017 edition of the American Society of Mechanical Engineers Boiler and Pressure Vessel (ASME B&PV) Code Section I and in the NBIC Part 3 Supplement 8 (A Well-Engineered Approach for Establishing the Minimum Allowable Post-Weld Heat Treatment for Power Generation Applications of Grade 91 Steel [3002005350]).
In-service Failures. Many in-service failures of Grade 91 steel components have been documented (such as Service Experience with Grade 91 Components [1018151] and Service Experience with Creep Strength Enhanced Ferritic Steels in Power Plants in the Asia-Pacific Region [3002005089]). Explanations include poor design, poor operation, bad construction practices, metallurgical risk factors, and other causes. Regardless of the root cause for each documented failure, the number of documented failures highlights the need for validation of weld repair options that can be used for the range of Grade 91 steel components in service.
Inappropriate Repair Techniques. The technical details for best practice" regarding welding of low-alloy bainitic steels should not be applied directly to welding of tempered martensitic steel. Thus, repair techniques established for conventional" low-alloy steels are not directly relevant for repairs on Grade 91 steels.
EPRI Research on Well-Engineered Weld Repair ApproachesThese concerns led EPRI to conduct a comprehensive multi-year, state-of-the-knowledge research program to evaluate the integrity of well-engineered options for repair of Grade 91 steel components. Alternative weld repair approaches that do not mandate the use of PWHT provide end-users with added flexibility, reduced outage schedules, reduced cost, reduced risk of over-tempering, reduced risk of destroying the existing component, and reduced risk of ancillary damage due to localized PWHT and other potential downstream impacts.
EPRI's research program resulted, first, in development of Welding Method 6 (WM6), which allowed tube weld repairs of Grade 91 steel without PWHT. WM6 was approved by the NBIC in 2015. After only five years of code acceptance, multiple utilities have successfully applied WM6 to Grade 91 steel components-including Tennessee Valley Authority (TVA), American Electric Power (AEP), Prairie State Generating Co., Florida Power and Light, and Xcel Energy-and application of WM6 has been documented in thousands of repairs. WM6 was recently modified to permit the repair of attachment-to-tube configurations or to allow for local weld buildup in the event that the tube wall has been reduced by erosion or corrosion. These enhancements will appear in the 2021 edition.
Supplement 8 was first introduced to the NBIC Part 3 in the 2017 edition to permit repair options for thick-section, balance-of-plant components, including large-bore girth welds, small-bore penetrations, attachments, and other configurations that are not addressed in WM6. As an engineered repair option, Supplement 8 requires that, The organization performing the engineering evaluation shall have demonstrated experience with Grade 91 CSEF steels." To date, hundreds of repairs consistent with the language in Supplement 8 have been executed and documented throughout the power generation industry.
More recently, WM7 was developed to permit dissimilar-metal weld repair between Grade 91 steel boiler tubes and austenitic steels or low-alloy ferritic steels without PWHT (Figure 2). This development represents more than four years of sustained testing and parallel efforts within the NBIC.
![]() |
2. Example of a simulated repair weld in a dissimilar-metal weld between Grade 91 and Grade 22 steels where the original weld deposit was made with an American Welding Society (AWS) type -B3 consumable. Note that the repair was made with AWS type -B8 filler material. Courtesy: EPRI |
The method, similar to the original language for WM6 printed in 2015, will be limited to butt welds in tubing NPS 5 (Nominal Pipe Size, in.) DN 125 (Diameter Nominal, mm) or less in diameter and 1/2 in. (13 mm) or less in wall thickness and to non-pressure part welds for which the applicable rules of the original code of construction did not require notch toughness testing. WM7 will eventually permit a more comprehensive set of rules within Supplement 8 to allow for dissimilar-metal weld repair for balance-of-plant applications in NBIC's 2023 edition.
From a monetary perspective, the cost savings for utilities applying these alternative weld repair approaches include avoidance of PWHT (valued in the $10,000s to $100,000s cumulatively), delayed component replacement to budget years that allow potential replacements to be better accommodated (valued in the $100,000s), ability to bring critical power assets back to the grid rapidly (valued in the millions of dollars with regard to both reduced outage times and reduced purchase of power to meet current supply especially within high-demand months), and through elimination of potential component damage induced by mal-PWHT (valued in the millions of dollars). Overall, the direct cost savings demonstrated by innovative PWHT are easily in the $100,000s, while the indirect cost savings, which include both deferred and minimized impact, are well within the millions of dollars.
Need for Fitness for Service AssessmentsAnother current materials and repair issue in the energy industry involves Fitness for Service." Pressure-retaining systems and other high-energy" components in power plants may be at-risk to fracture. When these events occur, they can present serious safety hazards, including personnel injuries and fatalities, can lead to significant economic consequences, and should be assessed in terms of the risk to leak or break.
The failure of components generally gives rise to a number of generic concerns and questions. For example:
Why do cracks develop in components designed to conservative construction codes or standards?
Why do some of these cracks propagate rapidly, increasing the risk of catastrophic failure?
Will the method used to disposition damage ensure safe and reliable operation?
Can the confidence in run/repair/replace be increased for plants operating in flexible operating modes?
When weighing these questions, owners and operators should not assume that code rules governing the design and fabrication of components prevent such failures. This cautionary note is especially pertinent considering language in relevant new construction codes such as ASME B&PV Code. The preamble to the code reads: The objective of the rules is to afford reasonably certain protection of life and property, and to provide a margin for deterioration in service to give a reasonably long, safe period of usefulness."
However, most design codes provide no expectation regarding the timing" (that is, when damage will occur) and no knowledge of fracture mode (such as, how the component will fail). In addition, little consideration is given to the weakest links as part of a system" evaluation (for example, where damage will evolve first). As a result, most new construction codes are ineffective for post-construction activities. Moreover, there is an increasing realization that not all defects result in fracture. Thus, the need exists to allow components to run" with cracks, and to conduct assessments of in-service equipment, otherwise referred to frequently as a Fitness for Service (FFS) assessment.
While the need to conduct FFS assessments of critical systems has been recognized for more than 40 years, today's widely referenced approaches for assessing in-service deterioration are largely based on methods developed more than 30 years ago. Current FFS methodologies are simplified and biased to a focus on the implied damage mechanism. Such methods do not simultaneously address the specifics of operation and component geometry (local and system), or properly consider the mechanism(s) of crack initiation and growth. Moreover, little guidance exists for the relevance of inspection methods necessary to inform the FFS evaluation of cracked components. Lastly, FFS approaches do not provide guidance specific to the placement of sensors for future monitoring to generate useful inputs and/or to track component health.
A timeline of FFS projects-including both EPRI projects and European projects-indicates how projects to date have been limited to component program initiatives and to studies not related to the energy industry (Figure 3). In addition, significant advances have been made in recent years in metallurgical understanding of damage mechanisms, the extent of relevant data, and component assessment models based on finite element analysis. Thus, it is imperative for a modern FFS approach to incorporate the latest technology and current metallurgical knowledge.
![]() |
3. Timeline of EPRI and European Fitness for Service projects. Courtesy: EPRI |
The EPRI project called Fitness for Service for Critical Components in the Energy Industry" will establish a technically rigorous engineering framework for FFS of components operating under high-temperature conditions where degradation can be by fatigue, creep, corrosion, or an interaction of these mechanisms. The engineering framework will be customized to address Fitness for Service on a component- and damage-specific basis. The individual components to be studied will be agreed upon within the project. The stages of the project will include:
Establish a project review panel of technical experts.
Develop the necessary materials property data to underpin the FFS methodology. Data will include new, aged, and/or service-damaged conditions linked to the specifics of the component and damage mechanism.
State the requirements regarding installation of instrumentation, the acquisition of data linked to operating scenarios, and the analysis of the results to provide sensible inputs for engineering.
Provide basic guidance and limitations for commercially available inspection techniques to size the length, depth, and nature of present defects.
Recommend how modern computer methods should be used to reduce uncertainty in the local stress state of the component. In general, for high-temperature components, the relevant stress state will be determined by either an elastic plastic or an inelastic creep analysis.
Address where, when, and how the specific component will fail. This effort will include consideration of leak or break, and seek to ensure designs are damage-tolerant.
Transfer learnings into globally relevant codes and/or standards using simplified, conservative analyses that support the EPRI integrated life management approach.
The validated predictive capability resulting from this project will provide an essential engineering tool for FFS. Establishing key links between critical crack size and relevant material property data in a new, aged, or damaged condition will reduce the uncertainty in the assessment of component integrity when employing the recommended methods for FFS. If successful, this project will offer a simplified framework for FFS that can be incorporated into common post-construction codes or standards and reduce the uncertainties in the FFS inputs and acceptance process.
-John Siefert(jsiefert@epri.com) is program manager of the Materials and Repair Program;Jonathan Parker, PhD(jparker@epri.com) is senior technical executive in the Generation Sector; andKent Coleman(kcoleman@epri.com) is program manager of the Boiler Life and Availability Improvement Program-all at the Electric Power Research Institute.
The post Welding Method 7 Approved, Fitness for Service Project Launched appeared first on POWER Magazine.