Inline Oil Condition Analysis on Power Generation Engines
The post Inline Oil Condition Analysis on Power Generation Engines appeared first on POWER Magazine.
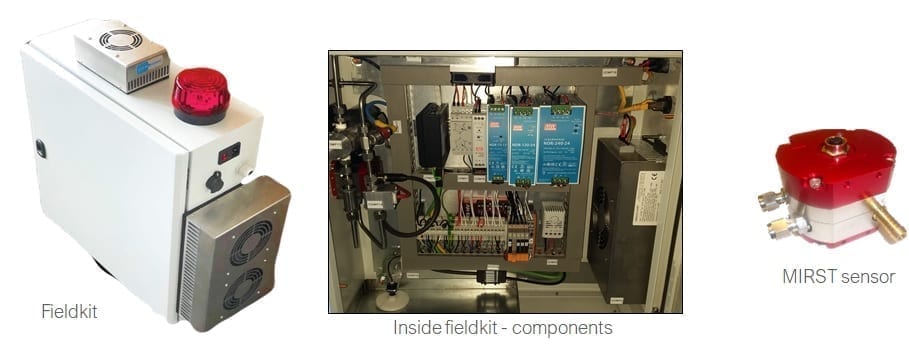
Oil and lubricants play a critical role in the operation of natural gas and biogas power generation engines, for example, in combined cycle (CC) and combined heat and power (CHP) plants. The oil condition gives valuable insight in the running status of the engine and many critical failures can be flagged.
Benefits of Real-time MonitoringConventionally, plant engineers operating and maintaining high-value assets, such as gas engines for power generation, rely on taking oil samples periodically and sending them to a laboratory for analysis. That whole supply chain is very laborious, but more importantly, it introduces a large time lag in the reporting of the oil condition that is lubricating critical parts of the system.
With real-time monitoring (Figure 1) of the oil condition, engineers and operators can have more intimate knowledge of their high-value power generation engine. The cost of ownership vastly decreases by having faster reaction time to failures or trends, by having effective maintenance and service planning, and allowing the plant engineers to extend oil change intervals and minimize engine downtime. Having real-time data also allows data merging with other equipment sensors to gain further insight for engine optimization.
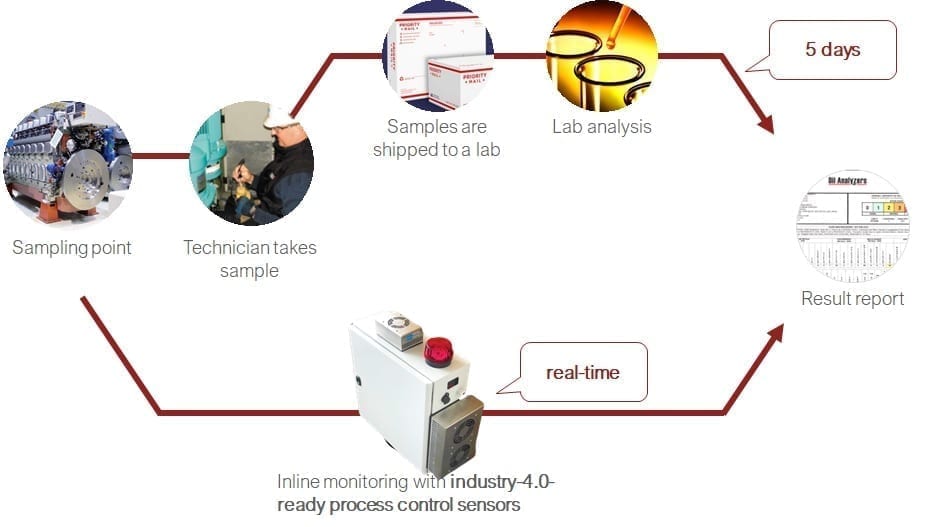
Spectrolytic's inline oil condition monitoring system, also known as the Fieldkit, allows seamless inline installation. The kit installation is plug and play, and can be carried out remotely with the support of Spectrolytic's field service engineers.
Housed inside the Fieldkit, the MIRS8-T oil condition sensor is an innovative inline mid-infrared (MIR) spectrometer that extracts the relevant oil condition information from chemical changes in the oil's infrared absorbance signature. The analytical method is identical to the one used in oil laboratories and provides very accurate quantitative data.
The Fieldkit (Figure 2) is designed with safety in mind and contains many safety features that ensure the Fieldkit itself is not the cause of any downtime. The Fieldkit can be integrated into the main oil flow of the engine or in a bypass flow from the oil sump or oil tank. If required for the application, the Fieldkit can be configured to include particle, viscosity, or other sensors that can provide additional information.
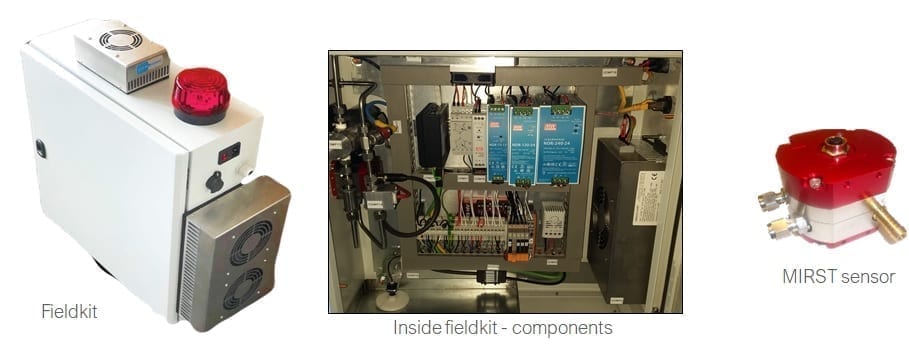
The MIRS8-T oil condition sensor located inside the Fieldkit can be customized depending on the oil formulation chemistry. The standard sensor configuration works well with most gas engine oils that are comprised of Group 1-3 base oils and a range of additives (dispersants, bases, anti-oxidation, anti-corrosion, etc.). There are also customized configurations that work well with synthetic oil bases.
Within the sensor itself, there are a number of discrete payload channels that can directly monitor parameters such as oxidation, nitration, sulfation, water, additive depletion, and soot. The results correlate well to the American Society for Testing and Materials (ASTM) E2412 standards. Other parameters such as Total Acid Number (TAN), Total Base Number (TBN), viscosity, and initial pH (ipH) can be derived from historical oil analysis data using Spectrolytic's proprietary chemometric modeling software. From one sensor the plant engineer obtains a host of oil condition parameters to fully understand the state of the oil condition in real time.
Data ManagementAs the power sector moves more and more toward the realm of Industry 4.0, it's critical that plant asset users have access to the full data stream at the touch of a button. The data stream, which consists of oil condition parameters, temperature, pressure, flowrate, etc., can be transmitted in a variety of customized options.
For example, the data stream can be set up to integrate directly into an on-site control system by using RS232 or CANopen interfaces. For complete remote access capability, the data stream can be transmitted to a cloud service. Depending on the location and infrastructure, there are a variety of transmission options, such as ethernet, LTE, or satellite communication.
From the cloud web portal (Figure 3), the user can access the process control charts from all the sensors to get a complete picture of the oil condition. The user can define and set the limits for each parameter to flag any trends or step changes in the behavior of the oil condition.
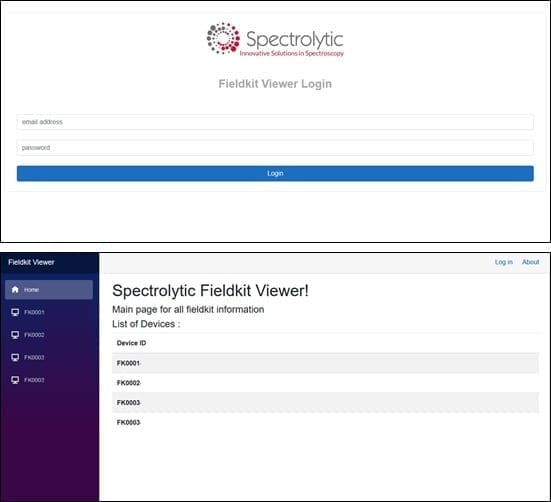
The inline oil condition monitoring system can also be used in a variety of plant equipment such as turbines (steam, gas, or hydro) for power generation, large gas compressors in plants and hospitals, and miniaturized for mobile systems, such as engines on heavy vehicles including excavators, diggers, and large trucks.
-Neil Conway is applications manager with Spectrolytic.
The post Inline Oil Condition Analysis on Power Generation Engines appeared first on POWER Magazine.