Mechanical Seals and Bearing Isolator Solutions for Tidal Energy Equipment Protection
The post Mechanical Seals and Bearing Isolator Solutions for Tidal Energy Equipment Protection appeared first on POWER Magazine.
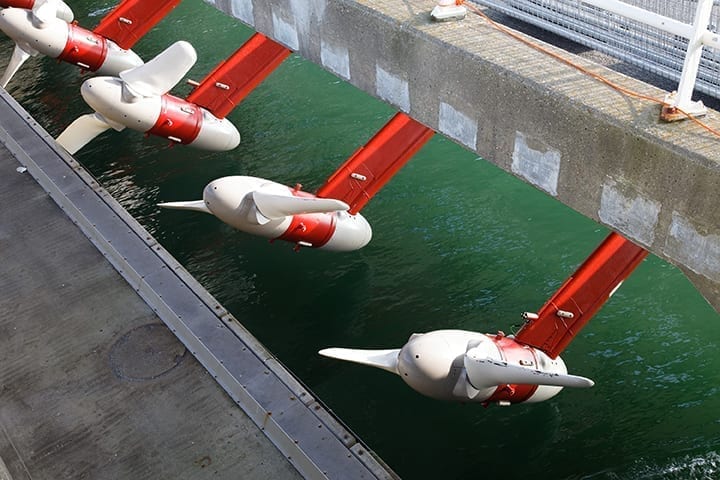
As clean-power technologies become more mainstream, offshore and river-based energy generating systems are beginning to come into their own in terms of proven performance. While the sea and rivers are widely available resources, they do come with a unique set of equipment protection and sealing challenges. The sealing solutions should be robust, safe, and effective-able to handle the difficulties of the environment, life-cycle requirements, and inaccessibility for maintenance.
Turbine Gearbox Sealing and ProtectionEffective equipment sealing is necessary for successful deployment of tidal turbines, such as the design shown in Figure 1. Within the turbine, the gearbox lubrication must be retained while moisture and contaminants must be excluded.
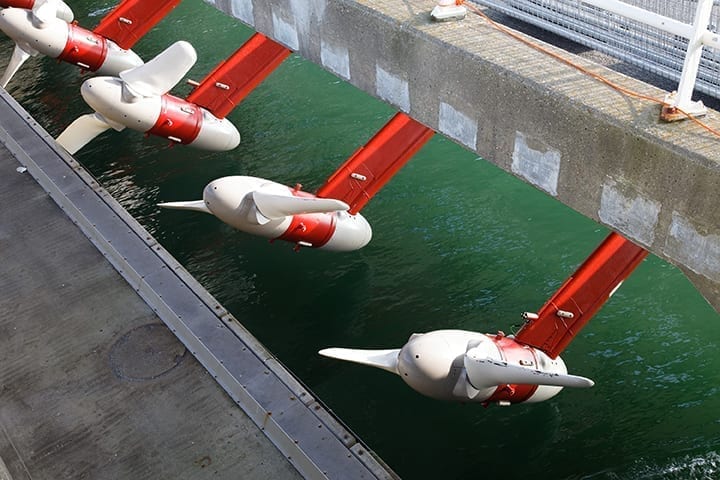
Traditionally, such rotational sealing applications would utilize lip seals at the gearbox boundaries, which are reasonable solutions in many pieces of equipment. However, oil seals must contact the rotating shaft to provide an effective seal, and even when operated in a well-lubricated environment, the lip seal will have a finite life. Oil seals require eventual replacement, and when used in a submerged marine environment, an oil seal replacement could come with a hefty price tag.
Bearing isolator technology offers a non-contact seal that will provide both ingress and egress protection for the life of the equipment, with zero wear to the seal or the shaft. Bearing isolators feature a labyrinth path to exclude dust and moisture to an Ingress Protection (IP) Rating of 66, while eliminating a contacting wear surface on the rotating shaft. The Garlock Guardian bearing isolator is one example of this technology, comprised of 3 components, the stator, rotor, and unitizing element (Figure 2).
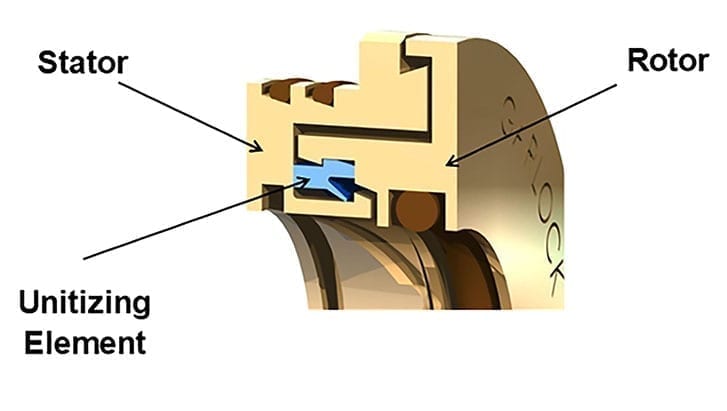
The rotor uses an incorporated O-ring to create the static seal on the shaft. The rotor and O-ring both turn with the shaft, removing any relative movement between them and, most importantly, eliminating shaft wear.
Unique to Garlock Guardian bearing isolators, the rotor and the stator are separated by a unitizing element. The unitizing element is made from polytetrafluoroethylene (PTFE) for its low friction and chemical inertness. The unitizing element maintains the spacing between the rotor and stator during installation and prevents metal-to-metal contact between the two parts during operation. Keeping the rotor and stator from interacting with each other eliminates the potential for the seal to generate contamination through internal metal-to-metal contact.
The stator is retained within the equipment bore by patented Cam-Lock O-ring grooves, which allow for installation by hand while providing excellent seal retention without damaging or galling the mating equipment. This non-contact seal technology allows the bearing isolator to have a truly infinite life. There are no wear components within the seal design, removing the need for costly routine maintenance.
Bearing isolator technology is scalable in size, with applications ranging from 1/2-inch thru 24-inch diameter shafts. Bearing isolators are rated for surface speeds of up to 12,000 feet per minute and can absorb radial misalignment of up to 0.2 inch. Bearing isolators are available in several materials, including bronze, stainless steel, and Hastelloy, for compatibility in challenging environments.
When using a traditional bearing isolator design, the fluid level within the gearbox must be maintained below the bottom of the shaft as noted in Figure 3. Within some gearbox designs, the oil level or behavior of the oil under running conditions can result in high splash or even a flooded seal condition. In such applications, an advanced design of bearing isolator can meet the need. The Flood-Gard bearing isolator is an example of such technology.
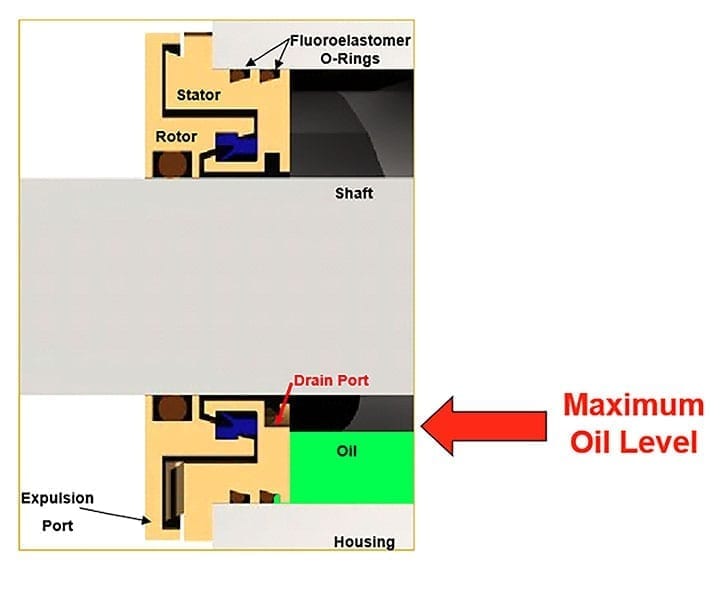
Designed for applications and gear boxes where the internal lubrication level is higher than the bottom of the shaft, or where extreme splash conditions exist, the Flood-Gard (Figure 4) combines the benefits of a bearing isolator with a traditional oil seal. The Flood-Gard provides the exceptional ingress protection of a bearing isolator, while also creating an ideal running surface for the internal oil seal. Available in standard sizes from 1- to 6-inch shaft diameters, the Flood-Gard provides consistent, reliable sealing for the most challenging of applications.
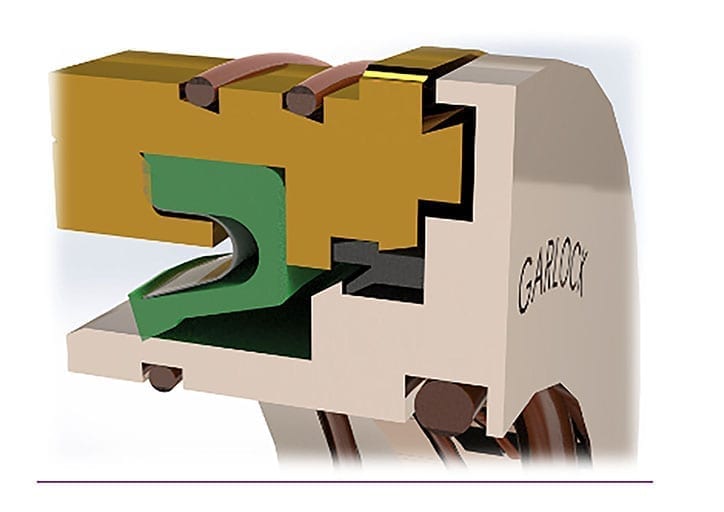
Due to the unique location and operation of tidal turbines, external shaft seals must be able to withstand several application challenges. Pressure differential, radial and angular misalignment, as well as corrosion and contamination all need to be managed in underwater environments. Initially developed for usage with shipboard propeller shafts, the Syntron double-face mechanical seal (Figure 5) has proven to be the ideal mechanical shaft seal solution for seawater pressure boundaries.
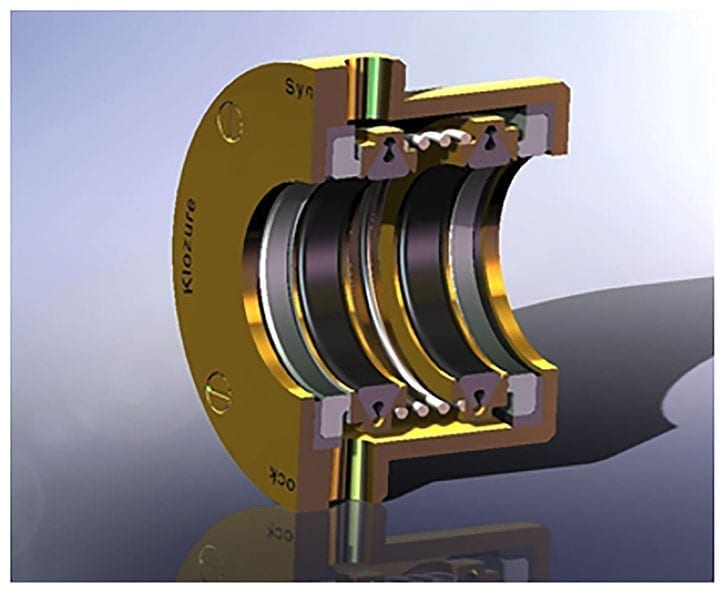
The Syntron mechanical seal is a cartridge-style seal that contains two opposing carbon and bronze sealing faces. These faces are loaded with an internally captured coil spring (or springs), allowing for continued sealing performance as the faces wear over time during normal operation.
The rotary faces and the spring(s) are affixed to the shaft with two drive rings. The drive rings create the static seal at the shaft outer diameter and translate the rotational force to the rotary seal faces. Similar to bearing isolators, no wear is imparted to the shaft. The stationary faces are captured within the seal housing by two molded rubber seats, creating the static seal on the stationary side.
In use, the seal housing is filled with a lubricating oil and capped. When submerged, the pressure across the faces equalizes, therefore no external contaminates are driven across the sealing faces. This allows for extremely long life with essentially zero leakage.
The seal housing is manufactured from machined bronze, eliminating the corrosion concern that is inherent in operating in marine environments. The combination of materials, construction, and operating parameters make the Syntron mechanical seal a uniquely well-suited solution for the challenging environment associated with equipment operating offshore. As an additional benefit, the Syntron is a cartridge-style seal, and completely rebuildable. This allows for easy repair and replacement as needed, while minimizing the total cost of ownership.
The Syntron mechanical seal is rated to 150 psi differential pressure and up to an operating temperature of 400F. While the default materials are bronze, carbon, and nitrile rubber, the seals can be manufactured with nearly any elastomer and housing material. Neoprene, silicone, and fluoroelastomers (FKM) are common elastomer offerings, while 316 stainless steel and Hastelloy are available choices for the seal housing and internal components.
In addition, the seal can be configured to act as a fluid coupling. Flow through the housing is communicated through vented spring guides to the shaft diameter. When paired with a hollow shaft, this allows cooling fluid to be transmitted through the shaft core to bearings located further down the shaft. This is a common solution used in annealing fan designs.
Consider Long-Term CostsThe necessity and the growth of clean-energy technologies continues to present unique equipment protection and sealing challenges. By leveraging both new sealing technology and mature proven solutions, matching them with carefully chosen materials and benefits, successful and cost-effective solutions can be configured. When evaluating these challenging environments, the life, performance, and maintenance cost must all be accounted for. Often, the total cost of ownership can be proven to be lowest when using a more initially expensive sealing solution like a bearing isolator in favor of an oil seal.
-This article was contributed by Garlock.
The post Mechanical Seals and Bearing Isolator Solutions for Tidal Energy Equipment Protection appeared first on POWER Magazine.