Process Control Strategies for Reducing the Minimum Load of Fossil-Fired Plants
The post Process Control Strategies for Reducing the Minimum Load of Fossil-Fired Plants appeared first on POWER Magazine.
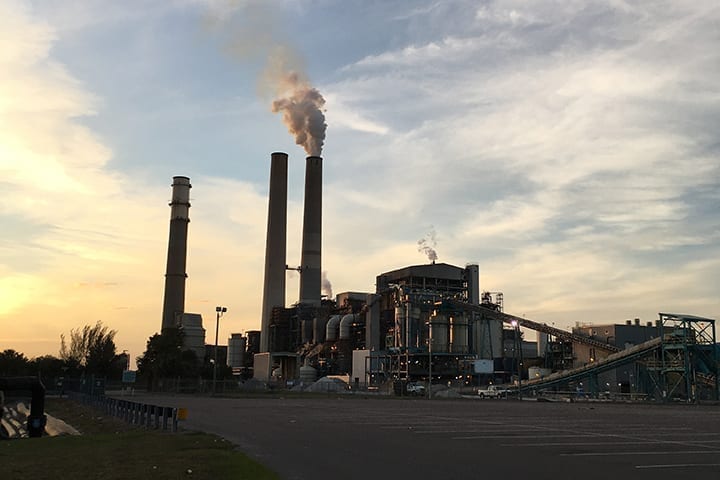
Recent Electric Power Research Institute (EPRI) research aims to better understand the potential of process control enhancements, such as load control, sliding pressure control, and steam temperature control, to improve low-load operation.
Current practices for reducing low-load operating limits in conventional thermal power plants generally center on changes to plant configuration, equipment, and operational practices, such as increasing gas exit temperature to enable selective catalytic reduction (SCR) systems and replacement of flame scanners to reduce false tripping. However, beyond these current practices, process control and automation strategies can potentially play an important role in reliably achieving low-load targets.
EPRI research is investigating current control and automation practices that large-scale coal-fired units can use to achieve low-load operation and to identify opportunities where controls can enable or support low-load operation. In one implementation of the research, EPRI assisted a utility in implementing process control and automation strategies to achieve and sustain reductions in the minimum load of a large-scale coal-fired plant in its fleet.
Low-Load OperationIn recent years, many large, conventional thermal power plants have begun operating over a wider range of loads due to the increasing capacity of non-load-following generation, such as renewables, connected to the grid. As a result, baseload coal-fired power plants have now become cycling plants and are likely to be temporarily shut down when load demand is low. An alternative is to keep these units online during low-demand periods by running them at minimum loads for extended periods.
Large thermal power plants can gain a competitive advantage by improving operational flexibility, and low-load operation can empower a plant to successfully participate in a competitive market. While low-load operation may not be ideal in terms of efficiency, performance, or reliability, it may be preferable to frequent shutdowns and startups.
The drivers to operate utility thermal power plants at low loads usually evolve as a compromise between the commercial imperative for profitability based on the costs associated with other options, such as on-off cycling operation, and the plant's minimum operating load. Motivation to reduce existing minimum operating load limits is an additional driver.
The targets for these reduced load limits are usually determined based on the design capability of the plant to operate safely and reliably at the revised limits, and the cost-effectiveness of their realization compared with other options, such as operating at existing higher minimum load limits or taking the unit out of service. Operating at reduced minimum loads is generally preferred for short durations (for example, daily load-following cycles) when load reduction can be reasonably achieved and sustained without unduly impacting process efficiency through the use of turbine bypass or costly ignition support fuels.
Current Practices to Improve Low-Load OperationEfforts to reduce low-load operating limits are generally centered on changes to plant configuration, equipment, and operational practices. In some cases, control adjustments are made to improve control stability, but these adjustments are typically limited in scope.
EPRI has actively conducted investigations and provided critical guidance for introducing and expanding these practices. Such practices include:
- Increasing gas exit temperature to enable an SCR system to remain in service at lower load by operating upper pulverizer or gas burner elevations (at times introducing constraints such as attemperator sprays reaching saturation temperature limits).
- Introducing revised SCR inlet temperature limits, with time-related graded limiting conditions based on ammonium bisulfate (ABS) formation test results and models.
- Upgrading of SCR catalysts to elements with lower minimum temperature limits.
- Modifications to SO absorber reagent supply systems to enable lower-flow operation at low unit load.
- Operating in turbine-follow (TF) mode at minimum load to reduce fuel under-firing and improve stability, forcing operation out of remote dispatch (automatic generation control [AGC]) mode.
- Replacing ignition fuel type (for example, oil to gas) to reduce cost of increased pulverizer stop-start operations, or to allow for more frequent operation with support ignition.
- Replacing flame scanners to reduce false tripping and initiation of ignition support.
In addition to these practices, process control and automation strategies have the potential to enable fossil plants to achieve low-load targets. Process controls can improve low-load process stability in normal modes of operation, allowing operating points to be optimized within process and plant constraints, and closer to limiting thresholds.
Implementation of process control schemes that improve efficiency can allow sustained low-load operation. Automation enhancements, such as automated sequence operations for pulverizers and feed pumps, provide opportunities to improve plant operations by making it possible to smoothly and repeatedly decrease load to the minimum and increase load again as required. Control and automation systems can also help sustain low-load operation though alarm systems, human-machine interfaces, and diagnostic systems that improve the effectiveness of the operator interface by focusing on process and plant constraints, and the risks to availability associated with low load.
Over the years, EPRI has conducted research to explore the opportunity for process control modifications to improve low-load operation. These modifications are based on several assumptions, including:
- A programmable distributed control system (DCS) is implemented with available spare capacity.
- Normal unit modes of control are implemented (for example, coordinated load control, boiler follow, or turbine follow).
- Monitoring, supervisory, and instrumentation systems are adequate for low-load operation.
The strategies under study by EPRI were implemented at a large coal-fired unit. The unit, which was constructed in 1979, is a subcritical coal-fired plant, rated for maximum continuous operation of approximately 447 MWgross. The initial minimum load during normal online operation was nominally 200 MWgross.
The EPRI project followed a systematic, sequential approach of identifying and testing appropriate site-specific process control modifications. The approach involved an initial desktop review and site visit to determine low-load targets, low-load benchmark testing, and detailed design and implementation of the logic modifications. The final six controls/automation modifications included:
- Inferred Overfire Air (OFA) Flow Signal Development and Substitution at Low Load. Instead of switching OFA flow to zero, an inferred signal was substituted, which provided a bumpless transition and eliminated this source of instability at low load.
- Superheater (SH) Steam Temperature Controls Tuning. These controls were re-tuned to give a faster response, with tuning parameters that automatically adjust over the full load range to a load of 150 MWgross.
- SH Outlet Temperature Controller Limiting. The SH outlet temperature controller's operating control range was widened to improve control range at low loads during startup.
- Boiler Feed Pump (BFP) Balancing. Automation of operations, such as BFP balancing, provided repeatable operations and predictable load ramping, thus alleviating operator workload as cycling frequency increases.
- Sliding-Pressure Control and Associated Modifications. Operation at reduced pressure offered improvements in unit efficiency at low load, reduced turbine inlet temperature variations during ramps, increased reheat steam temperature at low load, and decreased superheat-to-reheat steam differential temperatures at the high/intermediate-pressure turbine inlets.
- Drum Level Controller Adaptive Tuning. Adaptive tuning functions were implemented as functions of load and pressure to linearize the drum level control loop.
One of the modifications noted above is sliding-pressure operation. Sliding-pressure operation can potentially reduce minimum load by maintaining reheater (RH) temperature control and raising gas exit temperatures. Figure 1 shows four profile options for sliding-pressure operation.
![]() |
1. Sliding-pressure profile options (TV = Throttle valve and MCR = minimum continuous rating). Courtesy: Electric Power Research Institute (EPRI) |
The graphs show the following:
- The top left displays the most efficient option, with wide-open throttle valves and natural sliding pressure to 50% load. The mode has no frequency-regulation capability and requires operating in coordinated turbine-follow control mode (fuel controlling MW) for load control.
- The top right displays a typical profile for standard sliding-pressure operation in AGC and with a spinning MW reserve margin that reduces at low load.
- The option in the bottom left is similar to the top right, but with a fixed MW reserve margin. The throttle valves close in slightly as the load reduces.
- The bottom right displays sliding pressure only below 60% load. This provides fast ramping during normal operation, with slower ramping as pressure reduces by 40% to 60%. The slope of the pressure setpoint curve can be set as required to meet plant capability.
When a unit is operating in coordinated mode with the boiler controlling steam pressure and the turbine controlling MW load, any fuel change generates an integrating response to pressure (any imbalance between fuel input and MW output will result in steam pressure ramping up or down without stabilizing). Processes that respond this way tend to be less stable and can easily overshoot when the setpoint is ramped. As a result, implementing sliding pressure is often not considered.
A control approach known as a two degrees of freedom" (2-DOF) feedback/feedforward design is highly suitable in this application because the pressure setpoint is dynamically modeled to match the process's natural response. Additional fuel is calculated according to the pressure setpoint's rate of change to match the boiler energy storage as a function of pressure and the heat-release delay in the furnace. Figure 2 provides an outline of the 2-DOF design.
![]() |
2. Two degrees of freedom" (2-DOF) steam pressure controller outline with model-based pressure setpoint [PV = process variable, MV = manipulated variable, F(x) = function equation, d/dt = derivative calculation, PID = proportional, integral, derivative controller, and FF = feedforward]. Courtesy: EPRI |
The process control and automation modifications implemented on the case study unit helped enable the plant to achieve a new minimum load point of 150 MWgross (120 MWnet) in either fixed or sliding pressure, thus reducing its stable minimum load operations from 45% to 34% of rated load, extending the unit's load range for AGC operation, and improving control at low load. Additionally, the unit efficiency at minimum load was improved by more than 1%, and ramping from minimum loads was also improved.
The process control strategies will improve the stability and efficiency of the plant's low-load operations. In turn, reducing the plant's minimum load will allow the plant to improve its dispatch order to the grid and to more successfully participate in the competitive electricity market.
Following the successful test and operational results of the changes made on the initial unit, many of the controls tuning concepts are being implemented by plant controls staff on the other two units at the site. The results have been positive on those units as well. The implementation of the process control strategies at this plant is described in the EPRI report Process Control Strategies for Low Load Operation: Implementation (3002016325).
-Steven Seachman(sseachman@epri.com)is the program lead for the Process Control and Automation Program in the Generation Sector at the Electric Power Research Institute.
The post Process Control Strategies for Reducing the Minimum Load of Fossil-Fired Plants appeared first on POWER Magazine.