World-First Test Production of Fossil-Free Hydrogen-Reduced Sponge Iron Completed
The post World-First Test Production of Fossil-Free Hydrogen-Reduced Sponge Iron Completed appeared first on POWER Magazine.
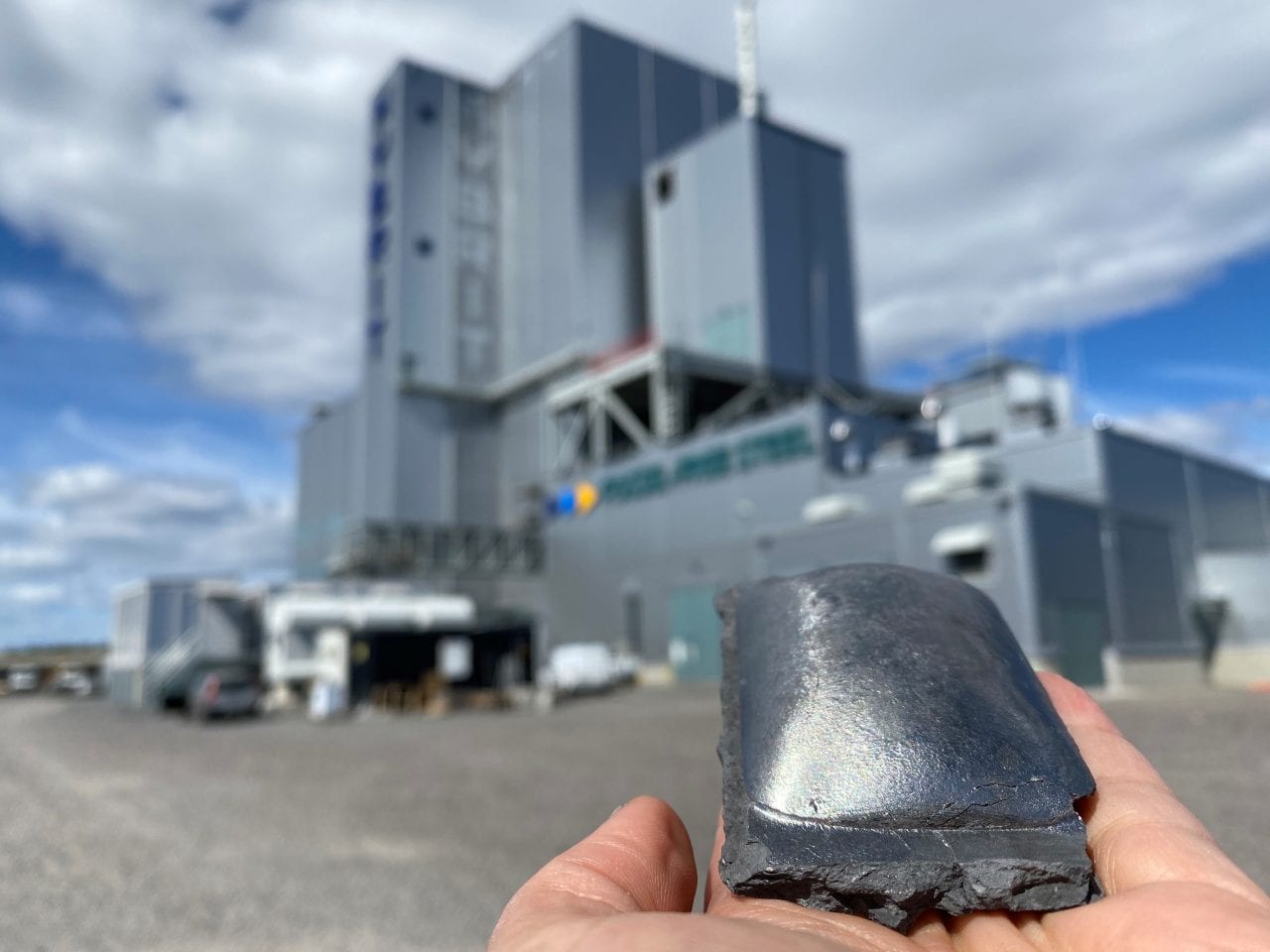
A pioneering pilot project in Lulea, Sweden, designed to produce fossil-free" steel has successfully completed test production of sponge iron, demonstrating it is possible to use hydrogen made with fossil-free power to reduce iron ore, instead of coal and coke.
Swedish energy company Vattenfall, mining company LKAB, and steel manufacturer SSAB-companies that are collaborating under the joint initiative, dubbed HYBRIT"-hailed the achievement as a technological breakthrough that is a decisive step on the road to fossil-free steel."
Production has been continuous and of good quality," the companies announced on June 21. Around 100 tonnes have been made so far."
As HYBRIT explains it, the ore-based steelmaking value chain starts at the iron ore mine, where the ore is processed in the form of pellets, or fines." At a steelmaking site, the iron ore is conventionally converted to metallic iron by reduction of the iron ore pellets with coke in a blast furnace. In the furnace, the iron oxide and carbon react to form carbon monoxide and carbon dioxide gases, as well as liquid metallic iron (which is further processed before being cast as semi-finished steel).
The HYBRIT system uses hydrogen-produced by electrolysis of water using fossil-free electricity-instead of coking coal, and releases water instead of carbon dioxide. Courtesy: HYBRIT
HYBRIT's process emulates another already existing, though less common, process called direct reduction." Most direct reduction processes use natural gas to replace coke as the main reductant to produce a solid sponge" iron. HYBRIT's process essentially uses hydrogen gas as the main reductant instead of natural gas.
However, HYBRIT's partners say their pilot plant's principal goal is to eliminate carbon dioxide emissions from the steelmaking process by using only fossil-free feedstock and fossil-free energy in all parts of the value chain. Steelmaking, the companies noted, currently generates about 7% of total global carbon dioxide emissions. Through HYBRIT-and with backing from the Swedish Energy Agency-SSAB, LKAB, and Vattenfall intend to create the most efficient value chain from the mine to steel, with the aim of being first to market, in 2026, with fossil-free steel at an industrial scale," they said.
The companies said the first industrial-scale production demonstration facility is already in planning in Gallivare, Sweden. At that facility, LKAB will explore converting its entire production to sponge iron. SSAB, which said it will be ready to deliver minor quantities of steel made using hydrogen-based reduction to customers," as early as this year, expects that in 2026, it will deliver fossil-free steel at a large scale."
HYBRIT fossil-free hydrogen reduced sponge iron. Courtesy: HYBRIT/Asa Backlin
As POWER has reported, test operations to make hydrogen-reduced sponge iron in the Lulea pilot plant began in August last year. They wrapped up on March 24. The process involved producing hydrogen through electrolysis of water with fossil-free electricity-mainly nuclear and renewable power. In May, HYBRIT's partners began building a pilot-scale hydrogen storage facility next door to the direct reduction pilot plant in Lulea.
The companies estimate fossil-free iron and steel production using HYBRIT technology will require about 15 TWh a year at SSAB's current production levels. Once completed, the conversion of LKAB's operations will require a total of around 55 TWh a year (including most of SSAB's requirement). This will require faster and more predictable permit processes to expand Sweden's power network and electricity production," they said.
Sweden's and Vattenfall's fossil-free electricity is a basic requirement for the low carbon footprint of hydrogen-reduced sponge iron," said Anna Borg, president and CEO at Vattenfall. The breakthrough that we can announce today shows in a very real way how electrification contributes to enabling a fossil-free life within a generation."
-Sonal Patelis a POWER senior associate editor (@sonalcpatel,@POWERmagazine).
The post World-First Test Production of Fossil-Free Hydrogen-Reduced Sponge Iron Completed appeared first on POWER Magazine.