Power Industry Automated Scraper Strainers Filter Full Spectrum of Debris Sizes
The post Power Industry Automated Scraper Strainers Filter Full Spectrum of Debris Sizes appeared first on POWER Magazine.
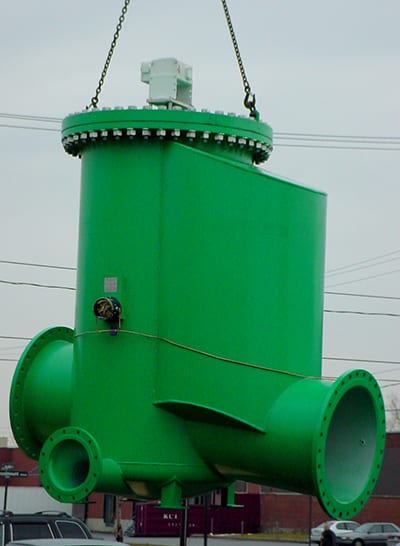
Unlike backwash systems, scraper strainers reliably resist clogging and fouling when faced with micron-sized particles, oversized solids, and high solids concentration.
The power generation industry often prefilters raw water from rivers, lakes, gulfs, and coastlines to remove organic, aquatic, and other solids for use as cooling water. Typically, with once-through systems, water circulates through pipes, absorbing system heat before it is returned to its original source.
Because the cooling water originates from bodies of water, it can be dirty, with considerable debris, weeds, and trash. Strainers are required to remove the waste from the cooling water before it goes into heat exchangers and cooling systems, and to prevent spray nozzles from clogging.
Insufficient removal of both large solids and small particulate (such as debris, dirt, and other suspended solids) as well as biofouling (including organic matter) from the water can cause serious problems. Plugging and fouling can cause unscheduled downtime, excessive maintenance, and costly premature replacement.
Traditionally, filters are designed to handle either smaller particulate or larger debris, but not both. The challenge is that natural bodies of water such as rivers and lakes are typically rife with both. Since power plants commonly draw cooling water from natural sources, their production often depends on reliable and efficient filtering of debris from the water to prevent excessive maintenance and downtime.
When a power plant was providing energy as a backup for a Kansas City power provider, the plant used river water for cooling, utilizing large basket strainers. The plant is now part of an energy solution partner with multiple district energy networks nationwide, and sought more efficient operation and maintenance from a downtown steam loop that produced chilled water.
District energy uses a centrally located facility, or facilities, to generate thermal energy-heat, hot water, or chilled water-for a number of nearby buildings. These resources are transported through underground pipes to meet the needs of communities, cities, and campuses-such as colleges, hospitals, airports, and office parks.
In order for them to provide condensing water for steam production as well as cooling water to the chillers and condensers, they take water from the Missouri River and put it through a once-through cooling system," said Keith Williams, PE, who was involved with the project and is a manufacturer's representative at Lenexa, Kansas-based Associated Equipment Sales, which represents North American manufacturers of heating, cooling, and hydronic equipment.
According to Williams, the river's fast flow along with high tide complicated the straining of river water for the plant. The Missouri River is the fastest river in North America, so high tide is when it is ripping everything off its banks: grass, weeds, twigs, and debris. All of that has to be filtered to keep from clogging the condenser tubes in the heat exchangers. We needed fine straining, but still had to pass very large debris, so, the [basket] strainers had to be cleaned out manually," said Williams.
Williams noted that the power plant's previous basket strainers required excessive maintenance. They had to clean the manual strainers every shift, three times a day during high tide, and it was a very dirty, disgusting job that no one wanted to do," he explained.
Although backwash strainers are often used in these circumstances, backwashing is not ideal for removing large solids from the perforated screen elements. The challenge is that the backwash arm must be quite close to the screen to function properly, and that prevents the passing of larger particles.
Most automatic strainers have a sweeping arm that uses differential pressure to suck the debris off the filter," said Williams. In order for it to have enough power [to do this], the gap has to be very tight to the filter, so you cannot pass large particles. The particle size is typically limited to about a half inch or three quarters of an inch."
When solids are bigger than the gap between the screen and the backwash arm, the solids remain in the vessel and have to be removed manually. In addition, biological film can adhere to the screen and create a cake that the backwash arm cannot remove. So, frequent cleaning is usually required by maintenance crews.
In this case, a basket strainer was used, but was continuously clogged during the river's high tide. Maintenance crews would clean one strainer and close it, open the other and clean it, etc. It was a never-ending process during high tide to keep the strainers clean, and keep the downtown chilled water loop functional," he said.
Originally, Williams was contacted as part of a plan to install new cooling towers. He instead advised that for this application, a more cost-effective solution was to install more efficient strainers.
I advised using an automatic scraper strainer from Acme Engineering that is capable of very fine straining while still passing very large debris," he said. It can strain to the micron level, yet can pass surprisingly large debris."
The automatic scraper strainer from Acme Engineering, a North American manufacturer of industrial self-cleaning strainers, is a motorized unit designed to continually remove both very large and very small suspended solids from cooling water. Cleaning is accomplished by a spring-loaded blade and brush system, managed by a fully automatic control system.
The four scraper brushes (Figure 1) rotate at 8 revolutions per minute, resulting in a cleaning rate of 32 times per minute. The scraper brushes get into wedge-wire slots and dislodge resistant particulates and solids. This approach enables the scraper strainers to resist clogging and fouling when faced with large solids and high solids concentration. It ensures a complete cleaning and is very effective against biofouling.
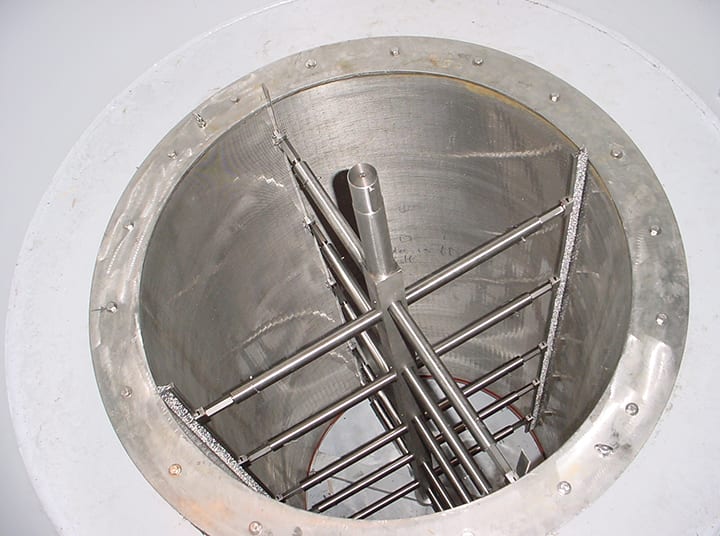
Blowdown occurs only at the end of the intermittent scraping cycle when a valve is opened for a few seconds to remove solids from the collector area. Liquid loss is well below 1% of total flow.
According to Williams, the scraper basket also allows the strainer to bypass extremely large particles and debris. There are very few manufacturers that can pass such large particles while straining out fine particles," said Williams.
The Acme automatic scraper strainer had to be customized to install on a 30-inch inlet and outlet with a 12-inch blowdown line for solids removal (Figure 2). Although industrial facilities with existing systems may be hesitant to replace under-performing backwash strainers due to the misperception that the installation modifications can be costly, firms like Acme can custom manufacture pressure vessels to fit within the existing piping arrangement, which minimizes installation costs. They can even deliver units with backwash arms, when needed.
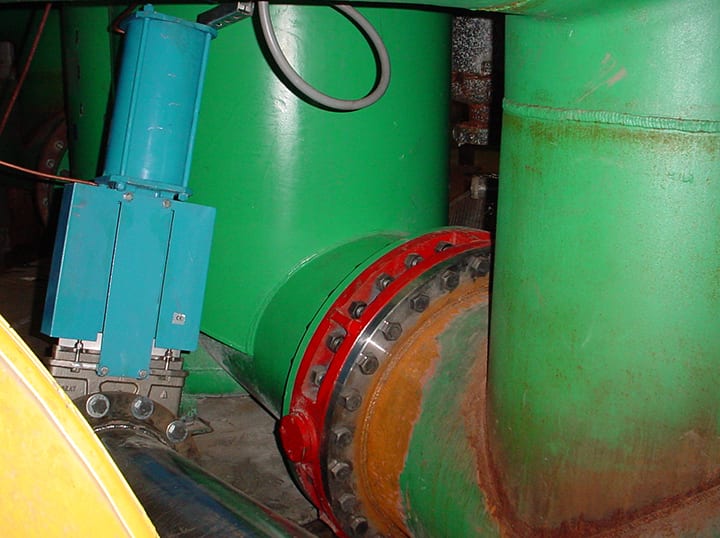
The line they wanted to install it in was at a 15-degree angle in a very tight space with a very short line, so we made a strainer where the inlet and outlet angled at 15 degrees," said Williams. This enabled them to just cut the pipe, install the flanges and the strainer, and be done. It was a custom vessel."
The facility's staff was impressed at how much the automatic scraper strainer simplified the maintenance of their strainer for cooling, despite the size range of river water debris it has to catch," he added. Now, they only open it for annual inspection and maintenance, and no one has to manually clean it anymore." According to Williams, the installation more than a decade ago is still fully functional, with only a basket replacement.
Recently, to accommodate the growth of the downtown loop, the facility began an expansion process, added Williams. Toward this effort, the facility has purchased two additional 30-inch strainers for the system and two 12-inch strainers for a raw water treatment system. The two new 30-inch strainers are the main strainers for the entire system. The two 12-inch strainers are raw water feed strainers that supply a portion of the plant that utilizes specialized water treatment.
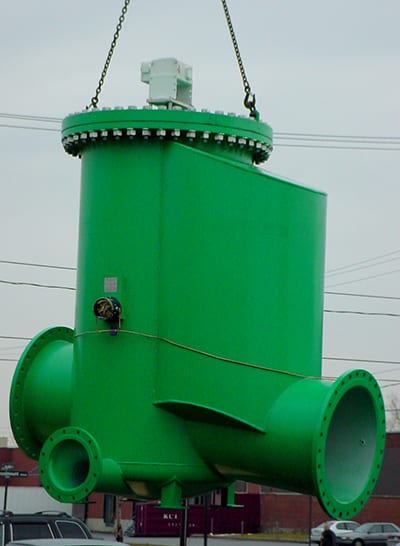
The plant is basically doubling the amount of cooling water coming in. With the added strainers, the intent is to prepare for future growth with potentially three times their previous capacity," Williams concluded.
-This article was contributed by Acme Engineering. Visit acmeprod.com to learn more about the company and its offerings.
The post Power Industry Automated Scraper Strainers Filter Full Spectrum of Debris Sizes appeared first on POWER Magazine.