Types of Coal and Fuel Blending Tips for Coal Power Plants
The post Types of Coal and Fuel Blending Tips for Coal Power Plants appeared first on POWER Magazine.
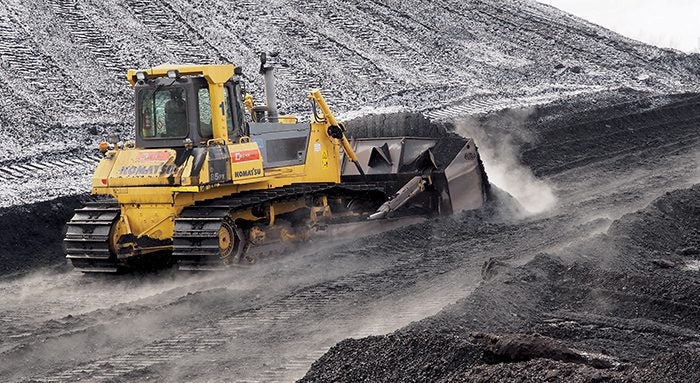
There are a handful of reasons why coal-fired power plant managers may want to blend fuel, but often the driving factor is economics. While the cost of the delivered coal is an important aspect, there could be adverse side effects that negate the savings, if the blending process is not done right.
The U.S. Geological Survey, the science agency for the U.S. Department of the Interior, categorizes coal into four major types or ranks. The ranks are lignite, subbituminous, bituminous, and anthracite. Rank refers to the step in the coalification process that buried plant matter is in as it changes into an ever denser, drier, more carbon-rich, and harder material.
Lignite, also known as brown coal, is the lowest grade with the least concentration of carbon. It generally has the lowest heating value and highest moisture content of all the major ranks. Next in order comes subbituminous and bituminous coal. These are black in color and gradually go from dull to a more shiny and smooth appearance as the rank increases. Anthracite, the highest rank of coal, is hard, brittle, and has a lustrous black appearance. It is often referred to as hard coal, and contains a high percentage of fixed carbon and a low percentage of volatile matter.
The U.S. Energy Information Administration (EIA) says bituminous coal, which has a heating value two to three times that of lignite, is the most common rank found in the U.S. It accounted for about 48% of U.S. coal production tonnage in 2019. Subbituminous coal-most of it from the Powder River Basin in Wyoming-was a close second, accounting for 44% of U.S. coal production in 2019, with lignite (8%) and anthracite (<1%) rounding out the list.
Why Blending Could Make Sense (and Why It May Not)Economics is what usually leads managers to investigate coal blending schemes. The EIA reported that the average annual sale prices of coal in 2019 from mines by main rank in dollars per short ton (2,000 pounds) were:
- Anthracite - $102.22
- Bituminous - $58.93
- Subbituminous - $14.01
- Lignite - $19.86
The cost of the physical coal is one part of the equation, but there are also other factors that must be considered. The cost of transportation to a power plant is often significant. It's not unusual for rail costs from the Powder River Basin to a coal-fired plant outside of Wyoming to exceed the price of the coal. Of course, therein lies one of the greatest potential opportunities. If a plant can cut transportation costs significantly by switching to a closer mine, for example, it could make a higher-ranking coal more economical and worth blending. In the end, the delivered cost per Btu is often most relevant.
Perhaps the single most important thing to contemplate is how the boiler will perform when a new coal is introduced. If a non-spec coal is being considered, there can be problems, even if a blended version of the fuel looks fine on paper. If the blended coal regularly causes upsets to plant operation, the result could be derates, boiler fouling, excessive emissions, or a variety of other trouble.
Decision-makers must not overlook the cost of blending either. Blending could require double handling of the coal, which is significant. Blending costs should be studied in depth because they could add $1 to $2 per ton, which quickly erodes potential savings.
Rod Hatt, owner of Coal Combustion Inc., gave an informative training session on the practicalities of coal blending during a Coal Users' Group webinar in 2020. Some of the details that follow were gleaned from his presentation. To learn more about the Coal Users' Group, visit: coalusersgroup.org. For more information on Coal Combustion Inc., visit: www.coalcombustion.com.
Methods of BlendingBlending coal can be done in several ways including at the mine, in shipping vessels, at the plant in the coal yard, or even in the boiler. It's important for managers to have a good understanding of how a plant's potential coal supplies are produced in order to ensure possible blending techniques will be implementable. Furthermore, the blending method chosen must create a homogeneous blend (Figure 1) rather than simply a mix; otherwise, plant operation will be adversely effected.
![]() |
1. A bridge-type bucket wheel reclaimer, equipped with a rake or an active scraper in case of poor flow properties, provides a good degree of homogenization. Using this type of equipment for coal blending is usually only practical at a mine. Source: Creative Commons / Bernard S. Jansen |
To better understand the difference between a mix and a blend, consider two jars of different colored sand, one black and one white. You could mix the two sands by alternately pouring a little of one and then the other into a new jar. However, what you'd end up with is layers of black and white sand. If coal were mixed in that fashion, those layers of different ranks will often result in the need for near-constant boiler operating adjustments. Instead, what you want to strive for in a blend is a sand that looks gray, which, when related to our coal blending scenario, provides much more consistent boiler operation.
To get a good blend, it is often best to add two coals to one belt and for that mixture to go through as many transfers as possible, such as through a crusher, tripper, or some other transfer station. It is also important to use a metering device or belt scale to ensure coal is proportioned properly. Having the most accurate measurements possible will help ensure the blend aimed for is the blend obtained.
At the Mine. Many mines blend coal as part of their normal production process (Figure 2). For example, they may blend coal from different seems within the mine in order to meet coal specifications that are required for a given plant. While there may be opportunities for plant managers to work with a mine to blend coal differently, that may not always be the case.
![]() |
2. A coal stacker is shown here at a mine in Australia. Blending from different seems is sometimes part of normal operations at a coal mine. Source: Creative Commons / Bernard S. Jansen |
In Shipping Vessels. For power plants that receive coal via barges or coal transport ships, it may be possible to blend coal as the vessel is being loaded. In this case, the best option, as mentioned earlier, is to add the two coals on the same belt as the vessel is being loaded so there are not layers of different coal in the cargo hold. The coal will be further blended as the vessel is unloaded, making this a very good way to obtain a homogeneous blend.
In the Coal Yard. Coal can be blended in the coal yard, but this is usually quite labor intensive, can add significant cost, and may not produce ideal results. Still, it is possible to receive different coals, stack them strategically when received, and blend them in the yard and during reclaim (Figure 3). Having enough space to properly accomplish the blending task is key.
![]() |
3. Blending fuel in the coal yard can be done, but workers need space to do it well. Source: Creative Commons / Petar Miloevic |
In the Boiler. Some plants have successfully blended different coals in the boiler. This can be done by feeding different fuels to the various pulverizers. For example, if a plant has six mills each with a dedicated silo, three silos could be filled with one coal and the other three filled with another coal, and the two coals would be blended as they were fed into the flame. In this case, however, it's important to ensure the air-to-fuel ratio and air balance are set correctly. Ideally, you want the Btu input from each pulverizer to be about the same. Therefore, if one coal has higher calorific value than the other, you may have to turn the coal flow down on pulverizers feeding the higher-ranking coal. In other words, try to adjust the coal flow so the calorific value fed from each mill is equal.
Consistency Is KeyWhen coal blends are analyzed on paper, it's often easy to find a blend that should work well in a plant's boiler. However, as has been mentioned before, having a consistent blend, rather than a poor mix, is vital to success.
My number one question when we start talking about blending is: Is it consistent? Has the fuel quality been properly blended so that the power plant is seeing a consistent blend?' " Hatt said.
When we do the economics, it always looks good on paper," said Hatt. But we're not really dealing with reality, because we're only using those average numbers for a fuel. We're not looking at the consistency or the spread of the data." If the various coals being used feed into the boiler in sporadic slugs, there could be trouble.
-Aaron Larsonis POWER's executive editor.
The post Types of Coal and Fuel Blending Tips for Coal Power Plants appeared first on POWER Magazine.