The Benefits of Synthetic Greases: Improved Efficiency, Reduced Maintenance
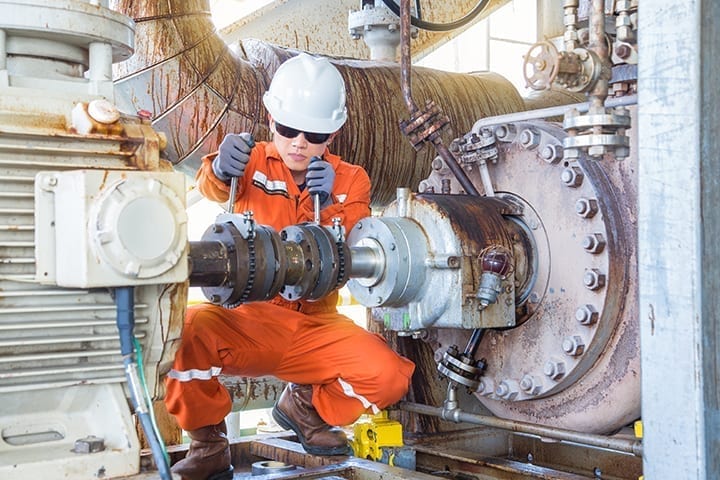
The optimal grease to use in power plant equipment is rarely contemplated by people other than truly dedicated operations and maintenance managers, and the workers on their teams who feel the pain when a piece of equipment breaks down due to inadequate lubrication. Yet, for those individuals, the choice of which grease to use in a bearing is an important decision. Selecting the right option could not only save energy, but also extend the maintenance interval and reduce the likelihood of equipment failure.
We spent a lot of years looking at: Can you make a difference from an efficiency perspective based on the product that you choose?' And the answer is, unequivocally, yes," Greg Morris, product application specialist for greases at Shell Americas, said as a guest on The POWER Podcast.
Morris suggested that synthetic greases are far superior to standard mineral-based formulations. How do you get to a place where you have longer service intervals-you touch the equipment less often," Morris asked. You can go to a synthetic," he said. That changes everything."
If an original equipment manufacturer recommended relubrication of a component every 1,500 hours using a mineral-grade grease, for example, you may be able to double that interval to 3,000 hours with a synthetic grease. Using synthetics, you've gained something," Morris said. You're gaining oxidative stability. A lot of times there's mechanical stability that comes along with that. And, you also have thicker film at higher temperatures."
Extending preventive maintenance intervals also reduces the risk of human error. The less often workers have to touch a piece of equipment, the fewer chances there are for personnel to make a mistake, such as lubricating with the wrong grease, for example. We don't have as many people working in the facility as we used to dedicated to doing just lubrication. So, you're doing more with fewer people," explained Morris. If you can reduce the tasks that those folks have to do to maintain reliability, then you're helping yourself out."
Efficiency gains can be significant. Morris said 8% to 12% improvements in efficiency are common when switching from mineral-based greases to synthetic greases. Where does that show up? It shows up in temperature in the bearing," Morris said. If you go from a mineral grade to a synthetic, you can see a drop in temperature in the bearing, and nothing else has changed-you haven't changed the load, you haven't changed the speed, you haven't done anything else-what you see is, the lubricant is having that much of an impact."
To hear the full interview, which includes a discussion about the National Lubricating Grease Institute's (NLGI's) certification process and Shell's Gadus S3 V220C 2 grease, which was recently certified as a High-Performance Multiuse (HPM) grease, in addition to its previously held GC-LB performance classification, making it the only NLGI dual-certified grease in the world, listen to The POWER Podcast. Click on the SoundCloud player below to listen in your browser now or use the following links to reach the show page on your favorite podcast platform:
The POWER Podcast 104. The Benefits of Synthetic Greases: Improved Efficiency, Reduced MaintenanceFor more power podcasts, visit The POWER Podcast archives.
-Aaron Larson is POWER's executive editor (@AaronL_Power, @POWERmagazine).
The post The Benefits of Synthetic Greases: Improved Efficiency, Reduced Maintenance appeared first on POWER Magazine.