Utilities and Industry Continue Learnings Around Benefits of Heat Rate Improvement
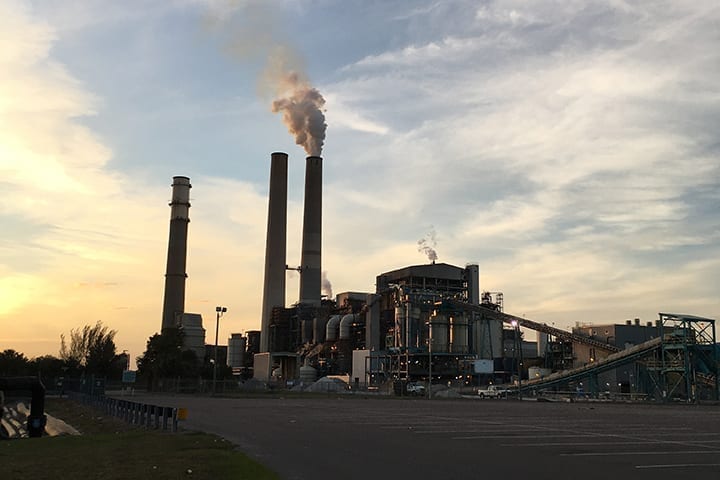
As the power industry moves toward net-zero carbon emission goals, heat rate improvement will continue to play a vital role. Heat rate improvements in a power plant improve air emissions and contribute to the overall reliability and life of the plant. Improvements to reduce air emissions are one-for-one, that is, a 2.5% heat rate improvement correlates with a 2.5% reduction in all air emissions, including carbon dioxide (CO2) and nitrogen oxide (NOx). Because the cost of fuel is 60% to 80% of the overall cost of producing electricity, improvements in heat rate can make a difference in the financial health of a power plant, power producing company, and the power industry.
The focus of EPRI's heat rate improvement projects is to improve operating plant heat rate, independent of the fuel fired. More recently, EPRI has sought to identify and quantify cost-effective heat rate solutions to operability and performance issues associated with baseload and flexible operations.
This article describes EPRI research efforts to discover and demonstrate heat rate improvements to reduce air emissions, fuel consumption, and production costs. It also discusses EPRI's Heat Rate Improvement Conference, first held in 1981, and now in its 40th year. This conference has not only provided a forum for utilities and researchers to discuss current needs and latest research advancements, it has also been a springboard to launch significant new research projects and industry interest groups.
Heat RateThe heat rate of a coal-fired power plant describes the amount of heat, typically in Btus, needed to generate one kilowatt-hour (kWh) of electricity. Accordingly, typical units for heat rate are Btu/kWh.
Heat rate is the heat energy input per unit of electrical energy output, or fuel consumption rate for specific levels of power plant output. Heat rate is also the inverse of plant efficiency. In this sense, it is comparable to a golf score: lower is better.
For each power plant, heat rate depends on the plant's design, its operating conditions, and its level of electric power output. In theory, 3,412 Btu of thermal energy is equivalent to 1 kWh of electric energy. For existing coal-fired power plants, heat rates are typically in the range of 9,000 Btu/kWh to 11,000 Btu/kWh. A plant with the industry average heat rate of 10,300 Btu/kWh is operating with an overall plant efficiency of about 33% (3,412 / 0.33 = 10,339).
The same follows for combined cycle power plants, but due to their design, the heat rates are lower. For existing gas-fired combined cycle power plants, heat rates are typically in the range of 7,000 Btu/kWh to 8,000 Btu/kWh. Note that a plant with the industry average heat rate of 7,400 Btu/kWh is operating with an overall plant efficiency of about 46% (3,412 / 0.46 = 7,400). While this is a vast improvement over coal-fired plants, improving heat rate still produces tangible results.
For example, at a typical 500-MW coal-fired plant operating at 40% capacity factor and firing $2.00/MMBtu bituminous coal, a 1% heat rate reduction will save about $360,000 in annual fuel costs.
500,000 kW x 10,300 Btu/kWh x 365 days/year x 24 hr/day x 40% x 1% x $2/MMBtu = $360,912 annual fuel cost savings
For example, at a typical 500-MW combined cycle plant operating at 60% capacity factor and firing $3.00/MMBtu natural gas, a 1% heat rate reduction will save about $580,000 in annual fuel costs.
500,000 kW x 7,400 Btu/kWh x 365 days/year x 24 hr/day x 60% x 1% x $3/MMbtu = $583,416 annual fuel cost savings
Heat rate improvement is also the first obvious step to reduce CO2 and all other emissions. It is commercially proven and is the most cost-effective and immediately available control process for lowering CO2.
Heat Rate ResearchEPRI's Generation sector provides information, processes, and technologies to improve the flexibility, reliability, performance, and efficiency of the existing fossil-fueled and renewable energy generating fleet. The research includes programs focused on asset management and optimization.
Capital and Maintenance Projects. In one research project, EPRI developed a methodology to assess the costs and benefits of potential maintenance improvements to coal-fired power plants, and refined the methodology to assess the net annual benefit of potential capital improvements to these plants. The assessment methodologies were then applied to a hypothetical 500-MW plant to calculate the benefits of potential capital improvements and maintenance projects, including the heat rate reduction benefit, reduction in auxiliary load, capacity increase, equivalent forced outage rate (EFOR) improvement, and emissions benefits.
The calculations were captured in two spreadsheets-one for capital projects and the other for maintenance projects. Inputs could be modified according to plant-specific circumstances, thus making it possible for individual utilities to use the methodology for scoping studies. The magnitude of the actual heat rate improvements were site specific, as were the drivers and economic benefits.
The capital improvements research identified 32 capital projects. For each project, the research identified the estimated capital cost, added operations and maintenance (O&M) cost per year, heat rate reduction (% and Btu/kWh), estimated auxiliary load benefit, capacity increase, EFOR improvement benefit, heat rate benefit, emissions benefit, added power sales benefits, and net annual benefit. At the time this project was completed and report written, the emissions benefit related only to NOx and sulfur dioxide (SO2), but the equations could easily be adapted to include CO2 and mercury.
Example projects included: turbine steam seal upgrades, turbine section replacements, intelligent sootblowing systems, automated boiler drains, coal drying systems, air heater baskets, and combustion optimization. There were a wide range of results. Not all projects generated net benefits with a positive payback. Heat rate reductions ranged from 0.10% to 2.50%. Project positive net benefits ranged from $30,000/year to $2.9 million/year. The research findings can be used by plant engineers and planners to develop a realistic case for making a specific capital investment.
The maintenance improvement research identified 25 maintenance projects and practices. For each, the spreadsheets identified the estimated initial maintenance cost, additional O&M costs per year, heat rate reduction (% and Btu/kWh), estimated auxiliary load benefit, capacity increase, EFOR improvement benefit, heat rate benefit, emissions benefit, added power sales benefits, maintenance annual benefit-cost ratio, useful life, and payback (years).
Example projects included: replacing feed pump turbine steam seals, repairing steam and water leaks, boiler chemical cleaning, repairing boiler air in-leakage, cleaning air preheater coils, repairing condensate pumps, and repairing flue gas desulfurization (FGD) systems. Similarly, there were a wide range of outcomes. Heat rate reductions ranged from 0.03% to 1.50%. Maintenance annual benefit-cost ratios ranged from about one to over 100.
Other examples include the following. A coal-fired power plant was preparing to switch to gas, but requested EPRI conduct a heat rate evaluation, which identified numerous actions to improve the plant's performance. After taking the recommended actions, the plant is still operating today. In another example, EPRI helped identify the cause of a cooling system problem, reducing an existing performance penalty by more than 50%, resulting in annual fuel cost savings of about $75,000.
These reductions lower production costs. In today's economic climate that can make the difference between continued operation or plant retirement. More recently, a similar compendium of actions was compiled for gas-fired combined cycle units.
Fleetwide Assessment Case Study. The most powerful use of the approach described above is to apply the method to an entire fleet, where a set of potential projects can be evaluated for a group of specific coal-fired units. Working with an electric utility, EPRI conducted a study to identify power plant efficiency improvements that could be implemented across all 12 coal-fired units in the utility's fleet to reduce CO2 emissions.
The study identified efficiency improvements organized by six major plant systems: boilers, turbines and generators, condensers, fans and motors, air quality control system precipitators, and balance of plant. In all, the study identified approximately 200 heat rate improvements, totaling a fleetwide emissions reduction of about 5%. Roughly 30 actions in the study created such large fuel savings that they could be conducted with a return on investment of less than three months.
Flexible Operation. Another EPRI study addressed the issue of improving energy efficiency during flexible operation. Flexible operation refers to the ability of a plant to operate at part load, load following, and cycling (on and off) modes in response to economic conditions and increased utilization of non-coal-based generation (such as renewables or gas). Operating conditions under flexible operation can result in reductions in plant efficiency and increased degradation and/or maintenance on components due to constant swings in operating temperature and pressure.
The study identified cost-effective capital modifications and adjustments to plant operating procedures to improve heat rate during cycling operation. The 10 upgrade options evaluated in the study included: sliding pressure operation; variable-speed drives for main cycle and auxiliary equipment; boiler draft system control schemes and operating philosophy; automated pulverizer controls and variations with mill design; optimum partial load operation of air quality control systems; feedwater heater drain system modifications for cycling; cooling system optimization; performance monitoring; reducing warm-up flow for idle boiler feed pumps; and minimizing flow, pressure, and temperature oscillations during cycling operation.
Heat Rate Improvement ConferenceThe 2022 EPRI Heat Rate Improvement Conference will be held February 7-9, 2022, in Charleston, South Carolina. The conference, the only formal gathering of its kind for power plant performance engineers, has been held biennially for more than 40 years.
It was initially born out of a collaboration with then Duke Power and the American Society of Mechanical Engineers (ASME). ASME volunteers hosted several sessions in early conferences. The meeting provided the ASME group with an opportunity to introduce new/revised performance test codes, and gave the industry a chance to provide feedback/input on those codes.
Over the course of its history, the conference has provided a forum to exchange knowledge and experience; identify major plant performance problems; and establish a clear understanding of priorities for additional research and development to improve power plant performance. Conference attendees have a unique opportunity to learn from the best minds in the field and to gain from their experience. The event has historically attracted a global audience of between 100 and 250 attendees. Initially the meeting had a coal plant emphasis, with some nuclear presentations; however, over the last decade, the focus has shifted to include gas. Topics may include new industry findings, unsolved plant performance problems, recent EPRI research, new techniques and hardware (from retractable turbine packing in the 1980s to advanced performance monitoring techniques in 2022).
Research Resulting from Conference ProceedingsA number of industry-leading research documents and interest groups have resulted from the conference.
ASME Performance Monitoring Guidelines for Power Plants. These guidelines include performance monitoring concepts, a description of various methods available, and the means for evaluating particular applications. The guidelines present performance monitoring essentials (including requirements, and potential benefits and tradeoffs), program implementation best practices, and case studies and diagnostic examples (Figure 1).
1. A controllable loss screen used as part of a performance monitoring dashboard. Courtesy: EPRI
EPRI Production Cost Optimization Project. The EPRI Production Cost Optimization (PCO) project assisted about 20 participating power companies in implementing or enhancing heat rate optimization programs to reduce production costs through sustainable performance improvements. The PCO assessment process consisted of benchmarking plant thermal performance and using historical plant data-along with an onsite performance appraisal-to identify potential areas for performance improvement. Overall performance improvements were significant, and ranged from 1% to 5%, with typical heat rate improvements of 2% to 4%.
EPRI Boiler Air In-leakage Projects. Boiler air in-leakage is a stealth thief of power plant performance. When occurring upstream of a steam generator's oxygen instruments, it can drive the furnace into a super-substoichiometric condition, potentially increasing damage to internal components, increasing unburned carbon, and potentially affecting ash sales, limiting NOx reduction levels, and decimating boiler performance.
The sources of boiler air in-leakage are difficult to identify. Nearly all components in power plants are covered with insulation, and many areas are difficult to access. While new lagging and insulation may prevent or reduce the amount of air leaking into the boiler, it also hides the holes that have formed underneath.
These projects were designed to evaluate the methods used to identify the sources of boiler air in-leakage. The projects involved 10 host sites and introduced new methods to the industry. The methods to detect and identify boiler air in-leakage sources included: smoke generated by multiple means, acoustics, infrared/thermal imaging (Figure 2), oxygen rise, external traverses, and remote visual observations.
2. Thermal image indicating boiler air in-leakage on a door between a plant economizer and air heater. Courtesy: EPRI
EPRI Combined Cycle Thermal Performance Interest Group. This group, the only one of its kind, promotes and facilitates an open information exchange among performance engineers, plant operations personnel, and others tasked with improving and monitoring combined cycle plant performance. The group has more than 20 utility company members and has been meeting since 2012. Meetings are held twice a year and permit attendees to learn of industry problems and advances through a network of technical peers.
-Sam Korellis is a technical executive at the Electric Power Research Institute (EPRI), where he leads research and development in heat rate improvement, heat exchangers, and cooling systems. He has managed the Heat Rate Improvement Conference since 2009. Prior to his efforts at EPRI, he worked for several power generating companies.
The post Utilities and Industry Continue Learnings Around Benefits of Heat Rate Improvement appeared first on POWER Magazine.