How Hydrogen Blends Will Impact HRSG Operation, Maintenance, and Performance
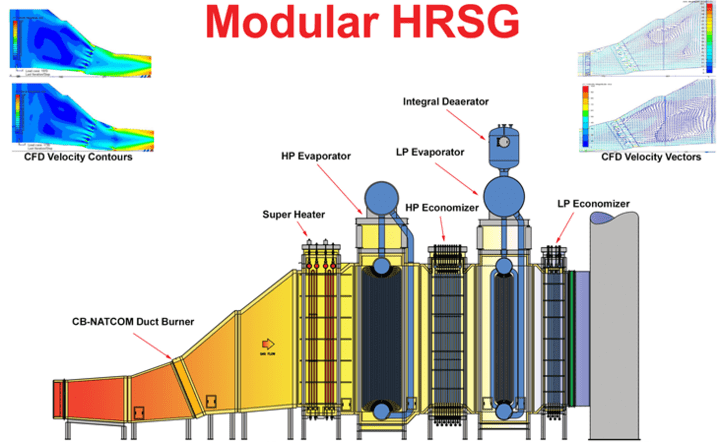
Environmental pressure is ramping up. Countries have issued targets to reduce or even eliminate the use of traditional fossil fuels in order to reduce emission of greenhouse gases such as CO2. Gas turbine original equipment manufacturers (OEMs) are responding by investing in hydrogen (H2) combustion. They are spending heavily on the development of combustors and other components that will enable gas turbines to operate with hydrogen blends. Some have issued roadmaps on how they will eventually operate their entire fleets with H2. This is seen as a key aspect of ongoing decarbonization efforts (Figure 1).
1. As more plants blend hydrogen with natural gas, HRSGs will have to be upgraded to cope. Source: Archie Robb
Natural gas generation with 30% hydrogen by volume delivers an 11% reduction in CO2," said Richard Saab, a sales manager at Siemens Energy.
While hydrogen-fired gas turbines are big news, a lot less attention is being paid to the impact of hydrogen on other areas of the gas-powered generation supply chain such as heat recovery steam generators (HRSGs). Yet, a great deal of the global gas turbine fleet operates in combined cycle mode with the turbines connected to HRSGs. Those HRSGs will have to deal with factors such as:
- Hydrogen has a higher flame temperature than natural gas.
- The water dewpoint of the flue gas increases when firing hydrogen.
- Colder parts of the HRSG in contact with flue gas will suffer from high levels of condensation.
- H2 combustion requires a higher volume of exhaust gas flow than natural gas.
- Hydrogen introduces additional safety concerns that must be dealt with.
Boiler makers have decades of experience in dealing with hydrogen," said Kevin Slepicka, vice president of HRSGs at HRSG manufacturer Rentech Boiler Systems. HRSGs present some additional challenges, but these are well within the capabilities of the vendor community."
HRSG BasicsHRSGs are high-efficiency heat exchangers that are used to extract heat from an exhaust gas stream to convert water into steam for use in combined cycle generation, or to produce steam for use in industrial processes. They consist of a complex arrangement of pipes with water flowing through them. When water exchanges heat with the hot gas, it is converted into steam. The primary components within the HRSG are the superheater, the evaporator, and the economizer (Figure 2). Duct burners are usually installed before the superheaters, while selective catalytic reduction (SCR) units are often deployed to reduce NOx levels.
2. The primary elements of the HRSG are the superheater, the evaporator, and the economizer. Courtesy: SoftInWay
There are major differences in temperature across the HRSG. The economizer temperature is much lower than the superheater section. Water fed into the economizer is preheated and passed to the evaporator to be converted into steam. As the name suggests, the superheater is used to superheat the steam to be fed to the steam turbine.
When hydrogen blends are introduced into HRSGs that were designed for natural gas combustion, certain factors must be appreciated. Hydrogen is a much lighter molecule than methane. It has a lower Btu value per unit of volume-natural gas has about five times the heating value per unit of volume, which means a far larger volume of hydrogen is needed for the combustion process. This impacts piping and metering stations that feed the turbine.
Hydrogen has a high mass related heating value of 51,600 Btu/pound, as well as a density that is eight times lower than methane," said Saab.
The higher flame temperature of hydrogen (roughly 4,000F versus 3,600F) means NOx becomes more of an issue. Burners, too, may need to be modified.
HRSG ModificationsBurner companies such as John Zink Hamworthy will usually determine the best size for fuel injectors used in hydrogen service. Minor modifications may be needed to HRSG duct burners depending on the amount of hydrogen being introduced. Separate hydrogen valve trains and firing elements will also need to be installed due to differences in heating value and supply pressure (Figure 3).
3. This plant is fired by refinery gas where the hydrogen in the fuel can range from about 30% to 80%, but is typically about 50%. The HRSG is coupled to a 22-MW gas turbine. Source: Archie Robb
The presence of hydrogen is likely to reduce performance; this must be compensated for with better burners and some design modifications," said Slepicka. As a result, HRSG duct burners are likely to be more expensive than those used in natural gas-based HRSGs."
Rentech has provided at least eight HRSGs to companies that want to burn hydrogen, primarily chemical plants that already have a ready supply on site. Some use it to produce more power, others for process steam.
One had dedicated injectors as the pressure was lower," said Slepicka. The other was able to use existing injectors."
He pointed out that the superheaters will run a little cooler due to all the water that condenses in the HRSG. This impacts heat transfer in the superheater. Hence, those driving a steam turbine may notice a performance hit compared to natural gas. This should be taken into account. If it is a new combined cycle plant, the steam turbine should be sized larger to generate the same amount of power as a 100% natural gas facility.
On the exhaust side, note that hydrogen requires a much higher volume of gas to be passed through the turbine. The HRSG, therefore, needs to be engineered to avoid exceeding the casing's design pressure. Higher pressure drop can also be a factor in derated performance.
Safety and Emissions ConcernsThe wider explosion range, lower ignition energy, and lightness of the hydrogen molecule compared to natural gas raises some safety concerns. Any unburned hydrogen will rise to the top of the HRSG and may collect in pockets. Modern HRSG designs generally leave little room for the collection of gas. However, purge cycles may be required to eliminate the risk of explosion. Any facility burning hydrogen should also install hydrogen detection technologies to catch the early signs of leakage.
Water and condensation are further issues. The water dewpoint rises when firing hydrogen. Therefore, cold parts of the HRSG in contact with exhaust gas will form condensation, especially in the back end of the HRSG. Designers should be aware of this phenomenon and ensure that drains and drying measures are implemented as needed.
As for emissions, the main worry is NOx. Early experience with hydrogen-based combustion and HRSGs indicates that NOx numbers will be higher due to the higher flame temperature of hydrogen. This will be negligible if hydrogen remains at 5% by volume of the overall fuel blend, said Slepicka. Above that, NOx will rise and mitigation steps will be needed.
SCR systems are already present in many HRSGs. Once the hot gases have moved through the HRSG and converted water to steam, they need to be mixed with ammonia before being released into the atmosphere to ensure emissions compliance.
Hydrogen's HRSG HistoryHydrogen, it turns out, is nothing new in packaged boilers and HRSGs. Packaged boilers have operated with some blend of hydrogen for decades. For example, Valero's Port Arthur refinery in Texas, which produces more than 100 million ft3/day of high-purity hydrogen, has added a combined cycle plant with a GE Frame 7EA 80-MW gas turbine. The HRSG is designed for supplemental duct firing up to 550,000 lb/hr and with a ramp rate of 60,000 lb/hr per minute. A steam methane reformer (SMR) hydrogen plant is integrated into the facility to provide additional steam. Exhaust from the gas turbines is used by the HRSG and the SMR. A 20-MW auto-extraction/backpressure steam turbine produces power and exports steam at two different pressures.
In the coming years, HRSGs will be required to run with hydrogen in increasing frequency," said Slepicka.
Retrofit or ReplaceNew HRSGs should always be designed to take into account the potential presence of hydrogen. Who wants to buy a HRSG and find out two years later than it requires extensive modification to tolerate hydrogen blends? Room for an SCR should be included as part of this. As emissions of NOx will go up as more hydrogen is added, space should be left in new HRSG designs where an SCR can be added in the future, if needed.
Those wanting to burn hydrogen in the future should set up the HRSG for it upfront," said Saab. Those that do receive a hydrogen-ready stamp, that can help with financing and will minimize costs. It is far more difficult to do afterwards."
But what about the hundreds of HRSGs that already exist? Some are decades old. To be able to operate with hydrogen blends, many will require substantial retrofitting to operate efficiently. Worst case scenario: it may be easier to replace an old HRSG with one specifically designed for hydrogen combustion. Particularly in light of the fact that gas turbine OEMs are intent on introducing more and more hydrogen into their turbines (with 100% being the ultimate goal), newer HRSGs should be specified to cope with hydrogen and older ones should be evaluated based on the best course between retrofit and replace.
Retrofitting an SCR into existing HRSGs would be extremely challenging," said Slepicka. If an older HRSG needs a lot of modification, it might be better to replace it. In any case, many of these units are nearing end of life."
-Archie Robb is a Southern California-based writer specializing in energy, technology, and business.
The post How Hydrogen Blends Will Impact HRSG Operation, Maintenance, and Performance appeared first on POWER Magazine.