Trial Operation of Innovative Horizontal Pelton Hydropower Turbine Underway in Austria
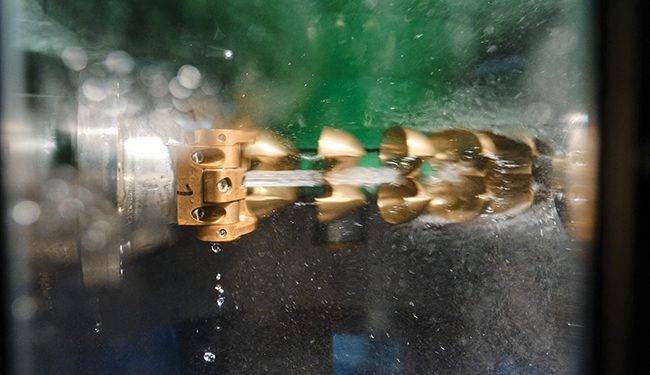
A pioneering horizontal, six-nozzle Pelton turbine developed by Voith Hydro at the 326-GWh Gerlos 1 pumped storage facility in the Ziller Valley, Austria, is setting new benchmarks for the 140-year-old technology.
The long-time German manufacturer of hydropower equipment in January said trial operation of the innovative Pelton wheel, which replaced the plant's four vertical Pelton turbines, has been running successfully" since November 2022.
Equipped with a nameplate capacity rating of 80 MW at 500 rpm (with a max head of 617 meters [m] and a maximum discharge of 16 m3/s), the newly developed turbine achieves an efficiency level that compares to vertical machines featuring the same number of nozzles and the same runner installed," Voith told POWER in February. That's proving significant for modernization efforts. At Gerlos, for example, a plant that has been running for nearly 75 years, more units could be replaced because also the size of the new machine is larger," the company noted.
Reinventing the Pelton WheelDeveloped by American inventor Lester Allan Pelton in the late 1870s to optimize energy production for Western mining operations using lower-volume mountain streams, the Pelton wheel is an impulse-type hydraulic turbine with a fairly simplistic design, which can be configured on a horizontal or a vertical axis. It essentially comprises a large circular disk with elliptical cup-shaped blades (buckets) mounted on a rotating shaft (rotor).
When a high-speed water jet from the penstock (a pipeline from the water reservoir) is injected through a nozzle, it hits on a Pelton wheel bucket, inducing an impulsive force that forces the turbine to rotate, and the rotating shaft runs a generator to produce power. So far, the horizontal-axis configuration has been limited to two injectors, while vertical-axis turbines can feature up to six injectors, which are typically mounted symmetrically around the wheel.
The Pelton turbine's working principle is well-suited to water sources with relatively high hydraulic heads at low flow rates. In contrast, the 1848-invented Francis turbine-the most commonly used hydraulic turbine-is a reaction-type turbine that operates with a partially submerged runner, where water reaches the wheel through a spiral conduit. The 1913-invented Kaplan turbine is an axial turbine with adjustable blades that, like boat propellers, rely on the flow of water to turn the blades (Figure 1).
![]() |
1. Types of hydraulic turbines. From left to right: Francis turbine, Pelton wheel, and Kaplan turbine. Courtesy: Enel Green Power |
Francis turbines are typically used for low- to medium-water heads (from up to 10 meters [m] to 400 m), while Kaplan turbines can perform optimally at small height differences but also with large variations in capacity (200 m3 per second and above). Pelton turbines are typically used for large height differences (from 300 m to 1,400 m) and less than 50 m3 per second of water capacity.
According to the American Society of Mechanical Engineers (ASME), the first operational Pelton wheel was installed at the Mayflower Mine in Nevada City in 1878, but it was dramatically scaled up in 1895 when a 30-foot-diameter wheel was installed at a gold mine in Grass Valley, California. Pelton's invention transformed the American West by replacing expensive, bulky steam engines at mining and construction sites with low-cost hydroelectric power. By the turn of the century, the age of hydroelectric power was flourishing," ASME notes.
Widespread uptake of the Pelton turbine was, in large part, spearheaded by Voith. From the beginning, the development of Pelton turbine technology has been synonymous with Voith," the company noted. Since the turn of the 20th century, Voith has supplied thousands of Pelton turbines, including large and powerful machines."
Sophisticated Modeling of a Highly Complex ProcessThe company says it has gradually refined Pelton technology using flow simulation, which has enabled realistic analysis of the Pelton turbine's unique flow characteristics. Today, designers have new insights into complex jet, bucket, and casing flow phenomena providing a solid basis for the development of new bucket profiles that result in improved performance," it said.
But while the company has showcased its development in a series of remarkable projects worldwide, its development, installation, and trial operation of the first horizontal, six-nozzle Pelton turbine marks a technological leap.
The breakthrough stems from an intensive study by German researchers to develop multi-nozzle horizontal Pelton units under the HP3+" initiative, a strategic development financed entirely by Voith to bolster hydropower modernization.
We see huge potential for the modernization of existing powerhouses," the company told POWER. Besides the development in our own state-of-the-art hydraulic laboratory in Germany, we also collaborated with independent external facilities." Still, the initiative is unique in the hydropower space. We do not know of any similar development by other companies so far," the company noted.
A key HP3+ challenge has been developing a suitable housing for multi-nozzle horizontal turbines that can withstand efficiency, aeration, and structural stresses, which are rooted mainly in how water circulates in the casing. Voith said its development of the innovative six-nozzle horizontal turbine was partly due to its newly developed ability to analyze housing flow (Figure 2).
![]() |
2. Impressions from the Pelton test rig at Voith Hydro's Brunnenmuhle Research and Development Center in Germany. Courtesy: Voith |
The interaction between the water jet and the buckets of the Pelton wheel is extremely short, often just a few milliseconds," Voith explained. This is why the flow simulation of Pelton turbines is by far the most complex and difficult of all hydraulic turbomachinery simulations," it noted.
The housing in a Pelton turbine needs to guide the water being discharged by the runner in such a way that it leaves the housing without backsplashing on the runner, because that would lower the efficiency," the company said. For two-jet machines, this is relatively simple because at two points along the circumference water is impinging on the jet. Therefore, only some guide vanes inside the housing are necessary. If more than two or three jets impinge on the runner, the amount of water per bucket width is dramatically increasing. Also, the positions at which the water is discharged by the runner are distributed all along the runner."
The new concept uses a circular or polygonal cover sheet around the runner that serves on one side as a guide vane for the discharging water and on the other side as a protection for the runner from back splashing water. The housing is more complex and larger. However, it provides a much higher power density than two-jet machines," Voith added.
A First Customer: VerbundAfter extensive tests and pilot programs, Voith bagged its first customer, Austrian utility Verbund. Verbund offered to demonstrate the technology at Gerlos 1, located at the southern end of the holiday resort village of Rohrberg in the Zillertal on the steep slope of the Rohrerberg. The plant, which was built in phases and completed in 1949, had four vertical Pelton turbines and was due for an upgrade.
![]() |
3. Voith Hydro deployed a heavy transport operation to get the 54-ton housing for its innovative six-nozzle horizontal Pelton turbine from its manufacturing facility in St. Poelten, Austria, to Verbund's Gerlos 1 plant site in the Ziller Valley in Tyrol. Verbund AG operates eight hydropower plants at five reservoirs in the scenic Zillertal Alps. Courtesy: Voith |
Among challenges Voith highlighted were getting the 54-ton turbine housing to the plant site (Figure 3). Apart from its weight, the dimensions of the unit were also impressive: just under nine meters long, more than six meters wide and over four meters high. This logistical masterstroke could be accomplished by means of a heavy transport operation taking an entire three nights," the company noted.
However, the triumph of demonstrating the turbine's operation has ushered in fresh potential for hydropower worldwide, Voith suggested. [T]he technology is of particular interest for upgrades of existing hydropower plants where single- or double-nozzle horizontal units are already installed," it noted. This is because the turbine can be replaced without major structural works, which significantly reduces civil costs and installation times."
The company also said enormous potential" exists to increase efficiency at hydropower plants equipped with Pelton turbines. The associated potential reduction in the number of turbines can likewise lower future maintenance costs. The new development is also a winning solution for new systems, as it requires less excavation and is more compact with a smaller footprint than conventional solutions. This is also associated with a shorter installation time, which substantially reduces the overall investment costs."
-Sonal Patelis a POWER senior associate editor (@sonalcpatel,@POWERmagazine).
The post Trial Operation of Innovative Horizontal Pelton Hydropower Turbine Underway in Austria appeared first on POWER Magazine.