The race to produce rare earth materials
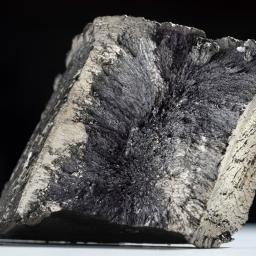
Abandoning fossil fuels and adopting lower-carbon technologies are our best options for warding off the accelerating threat of climate change. Access to rare earth elements, key ingredients in many of these technologies, will partly determine which countries will meet their goals for lowering emissions or increasing the proportion of electricity generated from non-fossil-fuel sources. But some nations, including the US, are increasingly worried about whether the supply of those elements will remain stable.
According to the International Energy Agency, demand for rare earth elements is expected to reach three to seven times current levels by 2040; demand for other critical minerals such as lithium may multiply 40-fold. Delivering on the 2016 Paris Agreement, under which signatory nations are obligated to reduce emissions to cap the global temperature increase, would require the global mineral supply to quadruple within the same time frame. At the current rate, supply is on track to merely double.
Obtaining rare earth elements begins with obtaining source materials, which can happen, broadly, in three ways: primary extraction, or mining directly from the earth; recovery from secondary sources, such as end-of-life electronics; and extraction from unconventional sources, including industrial wastes like coal ash and waste products from mines. But China so dominates the market-it controlled 60% of global production in 2021-that other countries are at a disadvantage. After China announced export restrictions in 2023 on gallium, germanium, and graphite, nations scrambled to find alternative sources in anticipation of future restrictions.
Primary extraction in the US is limited; only one active mine, the Mountain Pass Rare Earth Mine and Processing Facility in California, produces rare earth elements domestically. Opening new mines can take decades. As a result, scientists and companies alike are intent on increasing access and improving sustainability by exploring secondary or unconventional sources.
Finding critical materialsAll but one of the 17 rare earth elements appear on a 2022 list of 50 designated critical materials"-meaning they are economically important yet vulnerable to supply disruption. The 17, such as praseodymium (used in aircraft engines), gadolinium (used in MRI imaging), and neodymium (used in computer hard drives), include the lanthanide series"-the 15 elements with atomic numbers 57 to 71 near the bottom of the periodic table-as well as two chemically similar elements. The rare" in rare earth elements" refers not to the quantity available but rather to their wide dispersion-it's hard to find an economically meaningful quantity in a single location.
One unconventional source of rare earth elements is coal ash, the residual solid waste from burning coal at power plants. Historically, coal ash has often been mixed with water to form a slurry that is stored in ponds (also called surface impoundments). This ash, which contains elevated concentrations of rare earth elements, could be a significant domestic source of the materials in former US coal towns, which face challenges due to plant closures. There are more than 1,000 coal ash ponds across the US, mostly spread across the eastern part of the country. One of the largest facilities, Plant Barry in Mobile County, Alabama, contains more than 21 million tons of ash spread over 600 acres.
These ponds are not harmless; according to the US Environmental Protection Agency, improper management of them can compromise waterways, groundwater, drinking water, and air via contaminants such as mercury, cadmium, and arsenic. A document submitted by Earthjustice, a nonprofit environmental law organization, and Earthworks, a nonprofit focused on preventing the destructive impacts of oil, gas, and mineral extraction, responding to a 2023 request for information from the US Department of Energy, noted that 91% of power plants storing coal combustion residuals (CCRs) are polluting the underlying groundwater to levels that exceed federal drinking water standards." Ponds can also be destabilized during extreme weather events, and the resulting flood of contaminated material can destroy wildlife, damage property, and threaten community health and safety.
A startup, Rivalia Chemical, believes the health hazard posed by ash ponds can be addressed by repurposing ash to create a domestic supply of rare earth elements. Laura Stoy, the environmental engineer who founded Rivalia in 2021, says she is motivated by both environmental concerns and the potential for economic revitalization.
Stoy began developing Rivalia's flagship technology during graduate school at the Georgia Institute of Technology and is now working to scale it within the Chain Reaction Innovations program at the DOE's Argonne National Laboratory. In 2019, Georgia Tech supported the budding company in filing a patent (currently pending) for its technology, for which Rivalia holds an exclusive license.
That technology extracts rare earth elements from coal ash, leaving behind a solution rich in those elements and a residual solid containing iron and other metals. Through sequential steps of heating and cooling, rare earths are transferred into an ionic liquid-a salt in liquid state-via a proton-exchange mechanism. Acid-based reduction techniques and salt-based leaching can reduce the amount of iron in the final solution, after which rare earths must be further separated toproduce pure metals or oxides. Rivalia can sell primary outputs to companies that handle subsequent processing steps, manufacturers using rare earths, and sell residual solids to concrete producers. Stoy says Rivalia's efforts will produce materials that could be used for cleaner products and alternative energy sources. Furthermore, they could help reduce the carbon footprint of concrete production by repurposing the solid residue as a replacement for emission-heavy Portland cement-a major ingredient in concrete. (For more on this, see Climate's hardest problems".)
Rivalia prefers to work with existing waste products as opposed to coal that has not yet been burned. This approach is risky; extraction from unconventional sources can cost more than mining, given the low concentrations of rare earth elements and the greater initial concentration of toxic contaminants.
Still, Stoy says, this is a strategic move in light of the need to diversify supply. It's also an opportunity to make use of a widely available material with few alternative uses and significant economic value; the value of rare earth elements in US coal ash reserves was previously estimated at $4.3 billion (based on 2013 prices) and has likely grown since then. As a fairly new startup, the company is still in the R&D stage and is currently focused on reducing extraction costs.
I want to be one player in a big ecosystem where there's a lot of folks producing rare earths. That's the best outcome for everyone."
The race to produce rare earth elements domestically in the US is, at least partially, an attempt to figure out how to do so economically; however, companies are unlikely to get production costs low enough to be able to compete on price alone. Experts hope consumers will be willing to pay a premium, partly absorbing the increased costs.
Hopefully there is a market for a domestically produced material that's produced in an environmentally conscious manner and an ethical manner that's respectful of the workers producing the material," says Evan Granite, program manager for the carbon ore program at the DOE's Office of Fossil Energy and Carbon Management.
Regulators have started addressing the coal ash problem, so startups hoping to use the material will need to watch ongoing developments closely. The EPA began regulating the management of coal ash ponds in 2015 following destructive spills in 2008 and 2014. A recently proposed update to the 2015 rule mandates that older, inactive ponds that were previously exempt be covered or excavated.
Following the 2015 regulation, Earthjustice said that closing ponds by capping them in place is insufficient if they are within five feet of groundwater, and that in such cases only full excavation will prevent future damage. Either option-capping or excavation-would make coal ash harder to access for companies like Rivalia. Stoy says she considers this a reason to move decisively.
Stoy says she is wary of inadvertently creating new markets for coal by-products, which could jeopardize the country's clean-energy ambitions. Ironically, if utilities stopped using coal, Rivalia's source materials would eventually dry up. However, she isn't worried just yet-even in the absence of new production, the US now has 2 billion metric tons of ash, and many other countries seem likely to continue burning coal for the foreseeable future.
Handling all that ash will have to be done with care, says Lisa Evans, senior counsel in the clean-energy program at Earthjustice. Evans says that even for companies motivated by cleanup hopes, additional regulatory oversight is needed to ensure they dispose of by-products appropriately. What I've experienced in so many years of looking at how industries behave is that they don't do anything they're not required to do," she says, adding that the government should also ensure that communities receive adequate notice of nearby extraction activities.
Modernizing extractionAnother unconventional source of critical materials is tailings-the waste products of mines themselves. The EPA does not yet regulate mine tailings, even though they are similar to coal ash in the environmental risks they pose, says Evans of Earthjustice.
Phoenix Tailings is a Massachusetts-based startup extracting rare earth elements from mining sites. Two of Phoenix's founders, who grew up in communities affected by mining, say they are motivated by personal experience in addition to the growing demand for rare earth elements.
Besides the four rare earths used most commonly in magnets (neodymium, praseodymium, dysprosium, and terbium), Phoenix recovers battery metals, platinum group metals, low-carbon irons, and other materials in what it calls a portfolio approach" that improves economic viability. Like Rivalia, Phoenix repurposes residual materials into concrete and other aggregates. This, the company says, provides long-term storage for carbonaceous materials, reducing environmental impact by trapping them and preventing them from ending up in the water supply.
Phoenix works to modernize extraction, reducing the amount of energy, equipment, and funding required, says cofounder Anthony Balladon. You develop chemistries that are tuned for the rare earths, as opposed to trying to brute-force your way through them," he says.
After obtaining an oxide concentrate containing the rare earths, Phoenix uses separation techniques to draw out the desired end products. This is followed by reduction into final metal and alloy products using mixed-halide molten-salt electrolysis, resulting in 35% to 45% lower energy requirements. Chief technology officer Tomas Villalon says Phoenix's process reduces the amount of material inadvertently lost between processing steps and improves the purity of the final product. Phoenix's founders also highlight the sustainability of the company's process, which they say uses no hazardous materials and creates zero direct carbon emissions. The company is currently producing rare earth metals for commercial clients and expects to be producing over 3,000 tons per year of finished rare earth metals by 2026.
Villalon estimates that Phoenix will be busy for a long time: at least 10 billion tons of mine tailings are created each year from new activity.
Increased demand for magnetsSome companies target recycled materials rather than coal wastes as a source of recoverable rare earths. Noveon Magnetics-formerly Urban Mining-extracts critical materials from discarded commercial magnets (from motors or medical devices, for example, or from storage drives used by data centers) or those withdrawn from the supply chain because of manufacturing defects or obsolescence. From these materials, Noveon manufactures new sintered neodymium boron magnets, critical components of generators in wind turbines and motors in electric vehicles.
According to DOE projections, US demand for these rare earth magnets is set to more than quadruple by 2050. This is partly because of improved industrial technologies, says Noveon's chief commercial officer, Peter Afiuny. Industrial pumps, compressors, HVAC systems ... 50% of our electric consumption is being driven by those motors. If you're talking about getting to carbon neutral, you need to upgrade those systems and make them more efficient," he says.
There are fewer than 10 active magnet manufacturers outside China; Noveon is the only one in the US. Afiuny says it acquires all its materials domestically.
The company produces a new type of high-performance magnet, which it calls EcoFlux," using less material than conventional versions, says Afiuny. While it's hard for recycled magnets to perform as well as nonrecycled products, Afiuny says that Noveon has managed the feat by combining a proprietary technology that improves the composition and properties of magnetic materials with its patented Magnet-to-Magnet technology that can recycle up to 99.5% of input materials. He adds that Noveon has multiple customers and produces at commercial scale in its Texas facility. He says the company plans to produce 10,000 tons a year within five years.
These new magnets serve the same types of customers from which the materials were collected-such as companies using motors to power consumer electronics and medical or automotive products. The result is a loop of reuse.
Can these alternative sources replace existing imports? In a recent paper published in the National Academy of Engineering's magazine, The Bridge, DOE researchers estimate that for some critical materials such as germanium, coal ash can meet US demand for nearly 4,000 years, but for most materials, the supply will last for less than 20 years (and for nickel, for just a little more than one year).
Additional new sources are needed, says Granite: You're going to need many different waste materials and nontraditional sources to meet the long-term demand, because we project growing demands for many of these critical metals."
The researchers suggest that a much broader range of waste sources could be considered, including red mud," created during aluminum production, and produced waters," which result from oil production, as well as materials sourced from the ocean floor or even outer space.
A universal policy priorityBetween 2015 and 2021, the DOE awarded at least $27 million to projects related to extracting rare earth elements from both conventional and unconventional resources. In 2022 and 2023, the government announced at least $1 billion of funding available to support related work, including significant amounts from the Bipartisan Infrastructure Law. Other agencies have also announced support for companies working to help boost the nation's supply of critical materials, signaling a renewed sense of urgency for a longtime item on the policy agenda. Rivalia, Phoenix, and Noveon have all benefited from government support, suggesting that the government is willing to place bets on companies at varied sizes and stages of progress.
These funding allocations often reveal the priorities of the issuing administration; the focus under former president Donald Trump, for example, was independence from China, while the Biden administration's support for domestic production of rare earths seems more tied to its push for wider adoption of electric vehicles. Regardless of motivation, all parties seem aligned on the importance of rare earth elements.
It's something that's broadly supported in a bipartisan way," says Rivalia's Stoy. It's something that I think is very safe from a research funding perspective. The government is interested in this and is going to be funding it for a long time."
As the race to achieve self-sufficiency in rare earth elements and critical materials intensifies, the US is likely to further expand both the number of organizations involved and the diversity of potential sources.
Despite growing competition, Stoy says there's room for everyone. I want to be one player in a big ecosystem where there's a lot of folks producing rare earths," she says. That is the best outcome for everyone."
Mureji Fatundeis an academic and writer who explores how companies and consumers make decisions.