How we transform to a fully decarbonized world
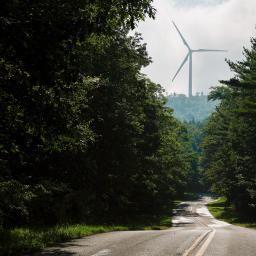
In 1856, Napoleon III commissioned a baby rattle for his newborn son, to be made from one of the most precious metals known at the time: light, silvery, and corrosion-resistant aluminum. Despite its abundance-it's the third most common element in Earth's crust-the metal wasn't isolated until 1824, and the complexity and cost of the process made the rattle a gift fit for a prince. It wasn't until 1886 that two young researchers, on opposite sides of the Atlantic, developed the method that is still used for refining aluminum commercially. The Hall-Heroult process is extraordinarily energy intensive: the chemically modified ore is dissolved into a high-temperature bath of molten minerals, and an electrical current is passed through it to separate the metallic aluminum. It's also intrinsically energy intensive: part of the reason the metal was isolated only relatively recently is because aluminum atoms bind so tightly to oxygen. No amount of clever engineering will change that physical reality. The astronomical growth in worldwide aluminum production over the last century was made possible by the build-out of the energy infrastructure necessary to power commercial refineries, and to do so in a way that was economically viable. In the US, that was facilitated by the massive hydroelectricity projects built by the federal government as part of Franklin D. Roosevelt's New Deal, closely followed by World War II and the immense mobilization of resources it entailed: aluminum was the material of choice for the thousands and thousands of aircraft that rolled off wartime assembly lines as fast as others were shot down. Within a century, the metal went from precious and rare to ubiquitous and literally disposable.
Just as much as technological breakthroughs, it's that availability of energy that has shaped our material world. The exponential rise in fossil-fuel usage over the past century and a half has powered novel, energy-intensive modes of extracting, processing, and consuming matter, at unprecedented scale. But now, the cumulative environmental, health, and social impacts-in economics terms, the negative externalities-of this approach have become unignorable. We can see them nearly everywhere we look, from the health effects of living near highways or oil refineries to the ever-growing issue of plastic, textile, and electronic waste.
We're accustomed to thinking about the energy transition as a way of solving the environmental problem of climate change. We need energy to meet human needs-for protection from the elements (whether as warmth or cooling), fuel for cooking, artificial light, social needs like mobility and communication, and more. Decarbonizing our energy systems means meeting these needs without burning fossil fuels and releasing greenhouse gases into the atmosphere. Largely as a result of public investment in clean-energy research and development, a world powered by electricity from abundant, renewable, nonpolluting sources is now within reach.
Just as much as technological breakthroughs, it's the availability of energy that has shaped our material world
What is much less appreciated is that this shift also has the potential to power a transformation in our relationship with matter and materials, enabling us to address the environmental problem of pollution and waste. That won't happen by accident, any more than the growth of these industries in the 20th century was an accident. In order to reach this future, we need to understand, research, invest in, and build it. Every joule of electricity that comes from fossil fuels means paying for what's burned to produce it. In fact, because of the inefficiency of thermal generation, it means paying for many more joules of heat.
Energy generation from renewable sources has capital and operating costs, of course, but minimal, incremental ones. That's because the input energy arrives as wind or sunlight, not as boxcars of coal. In the big picture, this means that in a fully decarbonized world, all energy will be closer to hydroelectricity in its economics: while it may never quite be too cheap to meter," it may indeed be too cheap to reliably generate a profit on an open energy market. This is a problem for investor-owned energy infrastructure, but it's potentially transformative for community-owned systems (including public utilities, nonprofit electricity cooperatives, or local microgrids), where cheaper and more abundant energy can power a just transition and a new economy.
Twentieth-century investments in energy infrastructure, like the New Deal's Rural Electrification Act of 1936 and its counterparts worldwide, formed the basis for the global industrial economy. If we can achieve a similar scale of commitment to renewable energy-prioritizing abundance and access over profit-it will lead to another jump in what's possible in the material world, where what was previously unthinkably expensive becomes quotidian reality. For example, just like refining aluminum, desalinating seawater is intrinsically energy intensive. But in a world with cheap, clean electricity, residents of coastal cities could get a reliable supply of drinking water from oceanside water treatment plants instead of contested freshwater sources.
Desalination is not the only energy-intensive process that would become viable. Aluminum, glass, and steel are among the most recycled materials in part because so much energy is needed to make them from their raw precursors that recovery is economically worthwhile. In contrast, plastics-in their near infinite variety-don't lend themselves to mechanical recycling except in a handful of cases. Effectively recycling plastics means breaking them down into their chemical building blocks, ready to be put together into new forms. And since most plastics will burn to produce heat, going in the opposite direction-reassembling those carbon atoms into new plastics-requires a significant input of energy. It's always been easier, cheaper, and more profitable to just dump the waste into landfills and make new plastics out of freshly extracted oil and gas. But if the energy came from inexpensive renewables, the whole economic equation of making plastics could change. Carbon dioxide could be pulled from the air and transformed into useful polymers using energy from the sun, with the waste plastic decomposed into raw materials so the process could begin again.
If this sounds familiar, it's because it's how plants work. But, just like Hall and Heroult's breakthrough for aluminum, new processes would require both energy and technological innovation. Decades of research have gone into creating new kinds of plastics from fossil fuels, and only a proportionally tiny amount into what happens to those plastics at the end of their lives. But now numerous companies, including Twelve, are building on new research to do just this kind of transformation, using renewably sourced energy to turn water and atmospheric carbon dioxide back into hydrocarbons, in the form of fuel and materials.
Prioritizing abundance and access over profit will lead to another jump in what's possible.
Finally, it's not just about plastic. If we succeed in building a world of even cheaper and more abundant energy but we again use it to supercharge extraction, consumption, and disposal, then we might solve" the pressing crisis around energy while worsening the multiple environmental crises posed by pollution. Instead, we can think about community-led investments in energy infrastructure as spinning up a new industrial system in which clean, inexpensive renewable energy makes it possible to recover a broad range of materials. That would cut out the enormous costs of primary extraction and disposal, including environmental depredation and geopolitical conflict.
Building momentum as fast as we can will limit the materials bill for the huge changes that decarbonization will entail, like replacing combustion-powered vehicles with their electric equivalents. This is already happening with companies like Ascend Elements, currently building a facility in Hopkinsville, Kentucky, to produce materials for new batteries from recycled lithium batteries. It's financed by more than half a billion dollars of recent private investment that builds on $480 million in Department of Energy grants, and the work is based on fundamental research that was supported by the National Science Foundation. As more and more clean, renewable energy comes online, we need to continue with policies that support research and development on the new technologies required to recover all kinds of materials-together with regulations that account for the true costs of extraction and disposal. This will facilitate not just an energy transition but also a matter transition, ensuring that the industrial sector aligns with the health of our planet.
Deb Chachra is a professor of engineering at Olin College of Engineering in Needham, Massachusetts, and the author of How Infrastructure Works: Inside the Systems That Shape Our World (Riverhead, 2023).