To be more useful, robots need to become lazier
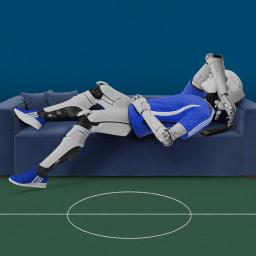
Robots perceive the world around them very differently from the way humans do.
When we walk down the street, we know what we need to pay attention to-passing cars, potential dangers, obstacles in our way-and what we don't, like pedestrians walking in the distance. Robots, on the other hand, treat all the information they receive about their surroundings with equal importance. Driverless cars, for example, have to continuously analyze data about things around them whether or not they are relevant. This keeps drivers and pedestrians safe, but it draws on a lot of energy and computing power. What if there's a way to cut that down by teaching robots what they should prioritize and what they can safely ignore?
That's the principle underpinning lazy robotics," a field of study championed by Rene van de Molengraft, a professor at Eindhoven University of Technology in the Netherlands. He believes that teaching all kinds of robots to be lazier" with their data could help pave the way for machines that are better at interacting with things in their real-world environments, including humans. Essentially, the more efficient a robot can be with information, the better.
Van de Molengraft's lazy robotics is just one approach researchers and robotics companies are now taking as they train their robots to complete actions successfully, flexibly, and in the most efficient manner possible.
Teaching them to be smarter when they sift through the data they gather and then de-prioritize anything that's safe to overlook will help make them safer and more reliable-a long-standing goal of the robotics community.
Simplifying tasks in this way is necessary if robots are to become more widely adopted, says Van de Molengraft, because their current energy usage won't scale-it would be prohibitively expensive and harmful to the environment. I think that the best robot is a lazy robot," he says. They should be lazy by default, just like we are."
Learning to be lazierVan de Molengraft has hit upon a fun way to test these efforts out: teaching robots to play soccer. He recently led his university's autonomous robot soccer team, Tech United, to victory at RoboCup, an annual international robotics and AI competition that tests robots' skills on the soccer field. Soccer is a tough challenge for robots, because both scoring and blocking goals require quick, controlled movements, strategic decision-making, and coordination.
Learning to focus and tune out distractions around them, much as the best human soccer players do, will make them not only more energy efficient (especially for robots powered by batteries) but more likely to make smarter decisions in dynamic, fast-moving situations.
Tech United's robots used several lazy" tactics to give them an edge over their opponents during the RoboCup. One approach involved creating a world model" of a soccer pitch that identifies and maps out its layout and line markings-things that remain the same throughout the game. This frees the battery-powered robots from constantly scanning their surroundings, which would waste precious power. Each robot also shares what its camera is capturing with its four teammates, creating a broader view of the pitch to help keep track of the fast-moving ball.
Previously, the robots needed a precise, pre-coded trajectory to move around the pitch. Now Van de Molengraft and his team are experimenting with having them choose their own paths to a specified destination. This saves the energy needed to track a specific journey and helps the robots cope with obstacles they may encounter along the way.
The group also successfully taught the squad to execute penetrating passes"-where a robot shoots toward an open region in the field and communicates to the best-positioned member of its team to receive it-and skills such as receiving or passing the ball within configurations such as triangles. Giving the robots access to world models built using data from the surrounding environment allows them to execute their skills anywhere on the pitch, instead of just in specific spots.
Beyond the soccer pitchWhile soccer is a fun way to test how successful these robotics methods are, other researchers are also working on the problem of efficiency-and dealing with much higher stakes.
Making robots that work in warehouses better at prioritizing different data inputs is essential to ensuring that they can operate safely around humans and be relied upon to complete tasks, for example. If the machines can't manage this, companies could end up with a delayed shipment, damaged goods, an injured human worker-or worse, says Chris Walti, the former head of Tesla's robotics division.
Walti left the company to set up his own firm after witnessing how challenging it was to get robots to simply move materials around. His startup, Mytra, designs fully autonomous machines that use computer vision and an AI reinforcement-learning system to give them awareness of other robots closest to them, and to help them reason and collaborate to complete tasks (like moving a broken pallet) in much more computationally efficient ways.
The majority of mobile robots in warehouses today are controlled by a single central brain" that dictates the paths they follow, meaning a robot has to wait for instructions before it can do anything. Not only is this approach difficult to scale, but it consumes a lot of central computing power and requires very dependable communication links.
Mytra believes it's hit upon a significantly more efficient approach, which acknowledges that individual robots don't really need to know what hundreds of other robots are doing on the other side of the warehouse. Its machine-learning system cuts down on this unnecessary data, and the computing power it would take to process it, by simulating the optimal route each robot can take through the warehouse to perform its task. This enables them to act much more autonomously.
In the context of soccer, being efficient allows you to score more goals. In the context of manufacturing, being efficient is even more important because it means a system operates more reliably," he says. By providing robots with the ability to to act and think autonomously and efficiently, you're also optimizing the efficiency and the reliability of the broader operation."
While simplifying the types of information that robots need to process is a major challenge, inroads are being made, says Daniel Polani, a professor from the University of Hertfordshire in the UK who specializes in replicating biological processes in artificial systems. He's also a fan of the RoboCup challenge-in fact, he leads his university's Bold Hearts robot soccer team, which made it to the second round of this year's RoboCup's humanoid league.
Organisms try not to process information that they don't need to because that processing is very expensive, in terms of metabolic energy," he says. Polani is interested in applying these lessons from biology to the vast networks that power robots to make them more efficient with their information. Reducing the amount of information a robot is allowed to process will just make it weaker depending on the nature of the task it's been given, he says. Instead, they should learn to use the data they have in more intelligent ways.
Simplifying softwareAmazon, which has more than 750,000 robots, the largest such fleet in the world, is also interested in using AI to help them make smarter, safer, and more efficient decisions. Amazon's robots mostly fall into two categories: mobile robots that move stock, and robotic arms designed to handle objects. The AI systems that power these machines collect millions of data points every day to help train them to complete their tasks. For example, they must learn which item to grasp and move from a pile, or how to safely avoid human warehouse workers. These processes require a lot of computing power, which the new techniques can help minimize.
Generally, robotic arms and similar manipulation" robots use machine learning to figure out how to identify objects, for example. Then they follow hard-coded rules or algorithms to decide how to act. With generative AI, these same robots can predict the outcome of an action before even attempting it, so they can choose the action most likely to succeed or determine the best possible approach to grasping an object that needs to be moved.
These learning systems are much more scalable than traditional methods of training robots, and the combination of generative AI and massive data sets helps streamline the sequencing of a task and cut out layers of unnecessary analysis. That's where the savings in computing power come in. We can simplify the software by asking the models to do more," says Michael Wolf, a principal scientist at Amazon Robotics. We are entering a phase where we're fundamentally rethinking how we build autonomy for our robotic systems."
Achieving more by doing lessThis year's RoboCup competition may be over, but Van de Molengraft isn't resting on his laurels after his team's resounding success. There's still a lot of computational activities going on in each of the robots that are not per se necessary at each moment in time," he says. He's already starting work on new ways to make his robotic team even lazier to gain an edge on its rivals next year.
Although current robots are still nowhere near able to match the energy efficiency of humans, he's optimistic that researchers will continue to make headway and that we'll start to see a lot more lazy robots that are better at their jobs. But it won't happen overnight. Increasing our robots' awareness and understanding so that they can better perform their tasks, be it football or any other task in basically any domain in human-built environments-that's a continuous work in progress," he says.