This inside-out design solves most of the rotary engine’s problems
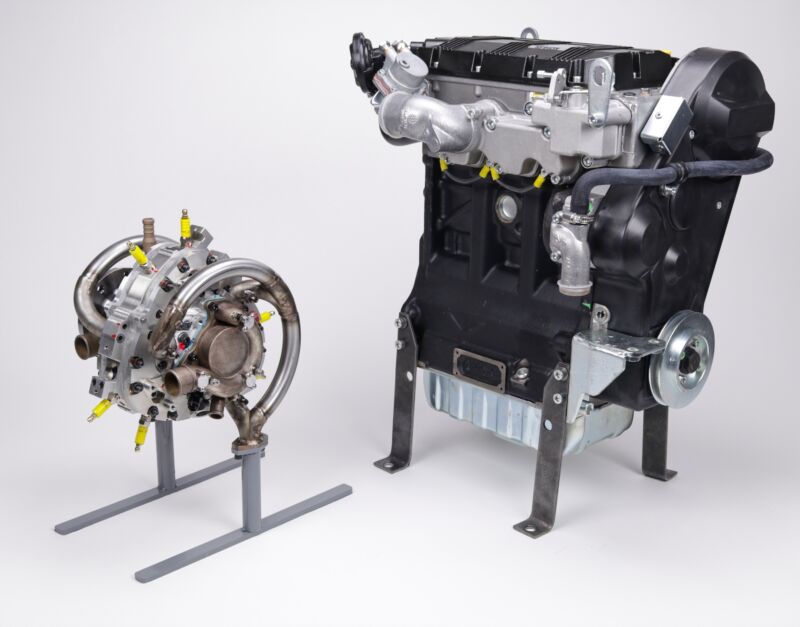
Enlarge / On the left, LiqudPiston's High Efficiency Hybrid Cycle engine, on the right, a 25 hp Kohler KDW1003 diesel engine. (credit: LiquidPiston)
Rotary engines have an aura of cool. In games of Top Trumps, the V12 might have been king, but a rotary was a joker, a wild card. A lack of mainstream success no doubt contributes; there are reasons they were never commonplace, including their oil-burning apex seals, which created emissions and fuel-consumption headaches.
LiquidPiston thinks it has those problems solved, however, and in the process, it created a new internal combustion engine that's small and efficient. It has demonstrated its tech on the bench and in a go-kart, but also in uncrewed aerial vehicles for the US military.
While little about the rotary engine merits the word, in a "traditional" Wankel rotary, a triangle-shaped rotor turns within a chamber during its combustion cycle. Apex seals are fitted at the apices of the rotor, but they need constant lubrication with oil, plenty of which burns during combustion. So, a Wankel engine needs constant oil top-ups while dealing with the products of that burnt oil. And those apex seals wear down.