New steel process is faster, lower cost, higher quality, uses 5-10 times less energy and enables new thinner sheets
by noreply@blogger.com (brian wang) from NextBigFuture.com on (#2G7P8)
Advances in production technology and materials science, particularly for new types of high-tech steel, mean that an old concept called "twin-roll" is being taken up successfully. An alternative system that casts liquid steel directly onto a single horizontally moving belt is also being tried. Both techniques could cut energy consumption-one of the biggest costs in steelmaking-by around 80%. Other savings in operating and capital costs are also possible. If these new processes prove themselves, steelmaking could once again be transformed.
The Castrip process uses up to 90% less energy to process liquid steel into hot rolled steel sheets. In addition, the Castrip process will reduce greenhouse gas emissions by up to 80%. The Castrip(R) technology offers considerable savings in capital outlay, completion and delivery times and energy costs.
In sheet steels, thinner is more valuable. Thickness of as-cast product from the Castrip(R) process is less than conventional hot rolled products. With the single stand in-line hot rolling mill, ultra-thin products of less than 1.0 mm can be produced. The long-term goal is to produce ultra-thin cast strip as thin as 0.7 mm (0.028"). It is interesting to note that as the cast thickness is reduced, the productivity of the process actually increases.
Because the Castrip process operates best when making thin products at high casting speeds, exciting opportunities are now being created for new sheet steel product categories. The potential exists for the Castrip product to be used in many applications that were not previously possible for hot rolled material. Several market segments that could initially benefit include structural decking, purlins and light-gauge steel framing, as well as tubular goods and structural applications such as racking.
Due to its thinness, the Castrip product can also be used as a direct replacement for cold rolled material in many applications. Short term plans include the production of galvanized products directly from the caster without the need for further cold rolling.
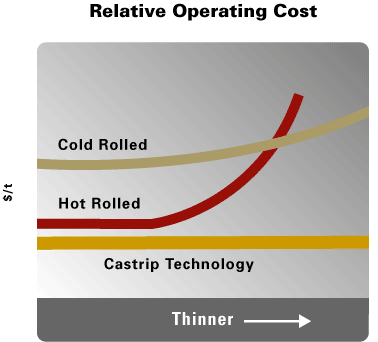
The Castrip(R) process is a major technological breakthrough for producing flat-rolled, carbon and stainless steel sheets at very thin gauges. The process is based on Sir Henry Bessemer's 1857 concept of twin roll casting, which has proven very difficult to bring to commercial reality...until now. Castrip technology allows steel makers to produce thin flat-rolled products in far fewer process steps, saving money on both capital outlay and operating expenses. And by casting steel at or near its final dimensions, tremendous savings of time and energy can be achieved.
Process Fundamentals
The twin roll casting process shown in Figure 1 uses two copper water-cooled, counter-rotating rolls. A refractory core nozzle (not shown) is positioned between the rolls to distribute molten steel into the melt pool. Side dams are positioned at each end of the rolls to contain the melt pool (also not shown).
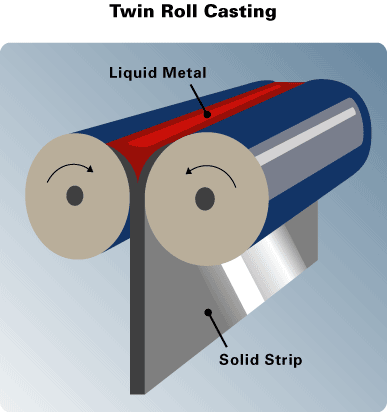
Starting at the first point of contact between the rolls and the molten steel, solidification begins and continues as the rolls rotate downwards. Two individual steel shells are formed, one on each roll. The shells form one continuous sheet when they are brought together at the roll nip or kissing point. This steel strip is guided through pinch rolls and a hot rolling stand, where it is reduced to the desired dimensions, typically between 0.7 and 2.0 mm. (See Figure 2 for a complete diagram of the Castrip process. The typical layout of a Castrip plant is illustrated in Figure 3.) Water-spray cooling reduces the steel from its rolling temperature to a temperature suitable for coiling.
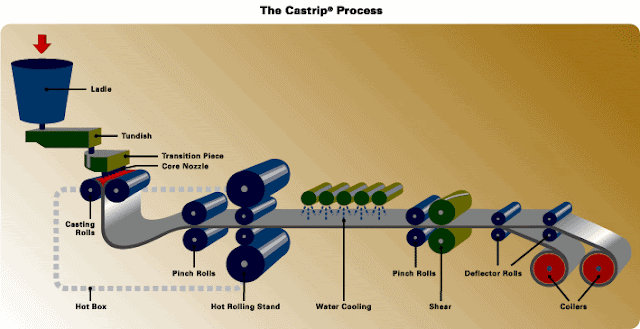
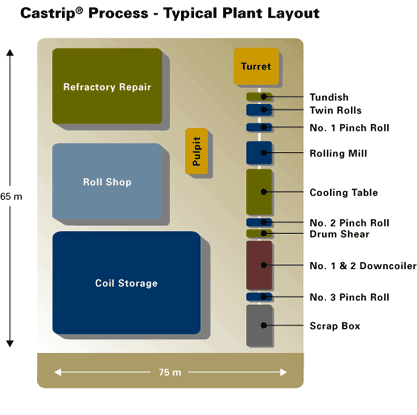
Process-to-Process Comparison
The Castrip(R) process represents a step-change over conventional thin slab casting of steel products in almost every aspect of operations - in fact, most characteristics are an order of magnitude different from comparable values from slab casting. The solidification event is completed in a shorter amount of time, the casting speed is much faster, heat fluxes are tremendously higher and the product is thinner.
Unlike slab casting, the Castrip process does not utilize any form of lubrication between the roll surface and the molten steel. Further, oscillation of the mold is not used and intimate contact is maintained between the solidifying shell and the roll. This allows for greater heat transfer, which dramatically reduces the solidification time to just 0.15 seconds, compared with 1070 seconds for conventional casting.
The new techniques are particularly good for making higher-value, specialist steels, says Claire Davis, a steel expert with the Warwick Manufacturing Group at the University of Warwick in Britain. Ms Davis and her team are developing new high-tech steels especially for belt casting, including advanced low-density steels that are stronger, lighter and more flexible than conventional steel.
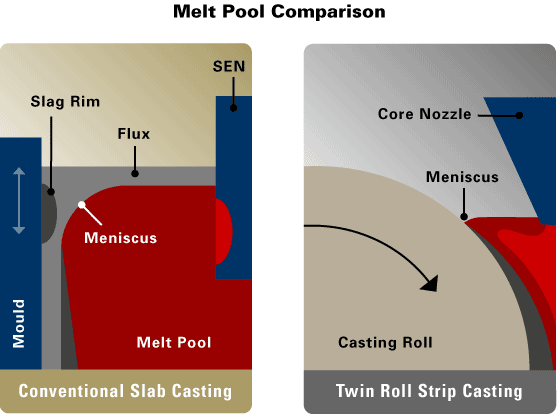
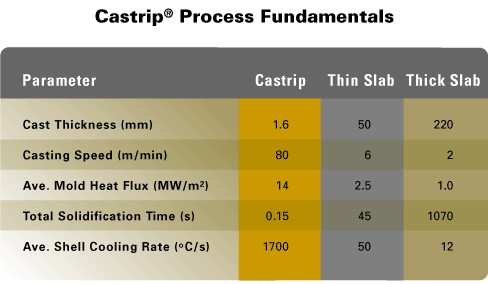
A twin-roll process, much as Bessemer conceived, is already employed by Nucor, a giant American steelmaker. Called Castrip, it is producing steel in two of its plants. A big advantage of twin-roll and belt-casting is compactness. Nucor reckons a Castrip plant needs only 20 hectares (50 acres) and provides a good investment return from the production of only 500,000 tonnes of steel a year. A conventional steel plant, by comparison, may sprawl over 2,000 hectares and need to produce some 4m tonnes a year to turn a profit.
Other firms are licensing Castrip as well. Shagang, a large Chinese steelmaker, is replacing a less energy-efficient plant with the new technology. The numbers look compelling enough to encourage a startup, too: Albion Steel is talking to investors about building a 300m ($370m) Castrip plant in Britain. The plant would be "fed" by a low-cost mini-mill that melts scrap and produces steel for galvanising, mostly for the construction industry, says Tony Pedder, one of Albion's founders. Mr Pedder is the chairman of Sheffield Forgemasters, an engineering company, and a former boss of British Steel (which later became Corus). Britain has a surplus of scrap but imports galvanised steel. The plant would employ only about 250 people; traditional integrated operations need a thousand or so. "We believe in the technology," says Mr Pedder. "In our view it is past the point of being experimental."
Read more


The Castrip process uses up to 90% less energy to process liquid steel into hot rolled steel sheets. In addition, the Castrip process will reduce greenhouse gas emissions by up to 80%. The Castrip(R) technology offers considerable savings in capital outlay, completion and delivery times and energy costs.
In sheet steels, thinner is more valuable. Thickness of as-cast product from the Castrip(R) process is less than conventional hot rolled products. With the single stand in-line hot rolling mill, ultra-thin products of less than 1.0 mm can be produced. The long-term goal is to produce ultra-thin cast strip as thin as 0.7 mm (0.028"). It is interesting to note that as the cast thickness is reduced, the productivity of the process actually increases.
Because the Castrip process operates best when making thin products at high casting speeds, exciting opportunities are now being created for new sheet steel product categories. The potential exists for the Castrip product to be used in many applications that were not previously possible for hot rolled material. Several market segments that could initially benefit include structural decking, purlins and light-gauge steel framing, as well as tubular goods and structural applications such as racking.
Due to its thinness, the Castrip product can also be used as a direct replacement for cold rolled material in many applications. Short term plans include the production of galvanized products directly from the caster without the need for further cold rolling.
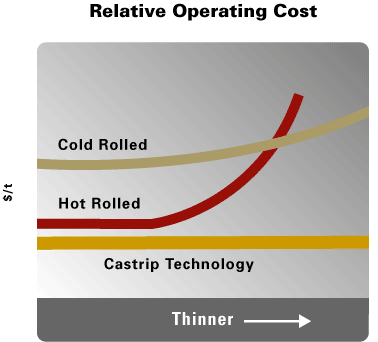
The Castrip(R) process is a major technological breakthrough for producing flat-rolled, carbon and stainless steel sheets at very thin gauges. The process is based on Sir Henry Bessemer's 1857 concept of twin roll casting, which has proven very difficult to bring to commercial reality...until now. Castrip technology allows steel makers to produce thin flat-rolled products in far fewer process steps, saving money on both capital outlay and operating expenses. And by casting steel at or near its final dimensions, tremendous savings of time and energy can be achieved.
Process Fundamentals
The twin roll casting process shown in Figure 1 uses two copper water-cooled, counter-rotating rolls. A refractory core nozzle (not shown) is positioned between the rolls to distribute molten steel into the melt pool. Side dams are positioned at each end of the rolls to contain the melt pool (also not shown).
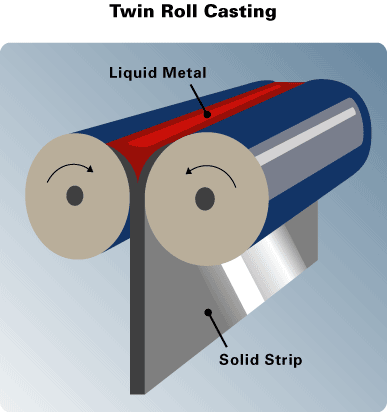
Starting at the first point of contact between the rolls and the molten steel, solidification begins and continues as the rolls rotate downwards. Two individual steel shells are formed, one on each roll. The shells form one continuous sheet when they are brought together at the roll nip or kissing point. This steel strip is guided through pinch rolls and a hot rolling stand, where it is reduced to the desired dimensions, typically between 0.7 and 2.0 mm. (See Figure 2 for a complete diagram of the Castrip process. The typical layout of a Castrip plant is illustrated in Figure 3.) Water-spray cooling reduces the steel from its rolling temperature to a temperature suitable for coiling.
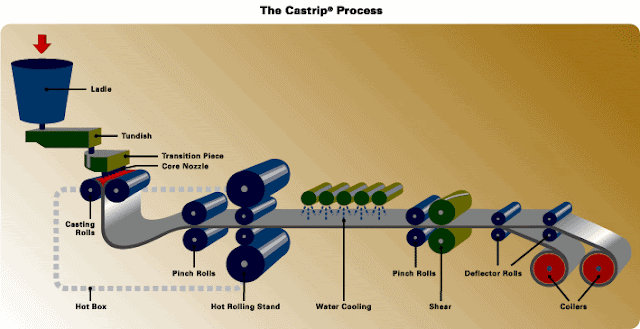
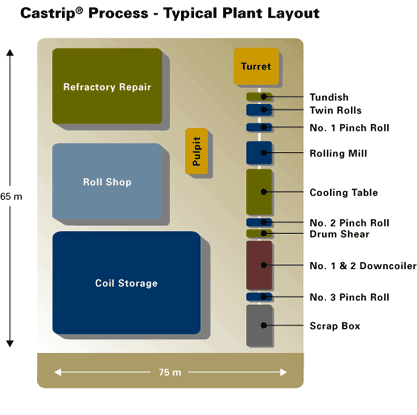
Process-to-Process Comparison
The Castrip(R) process represents a step-change over conventional thin slab casting of steel products in almost every aspect of operations - in fact, most characteristics are an order of magnitude different from comparable values from slab casting. The solidification event is completed in a shorter amount of time, the casting speed is much faster, heat fluxes are tremendously higher and the product is thinner.
Unlike slab casting, the Castrip process does not utilize any form of lubrication between the roll surface and the molten steel. Further, oscillation of the mold is not used and intimate contact is maintained between the solidifying shell and the roll. This allows for greater heat transfer, which dramatically reduces the solidification time to just 0.15 seconds, compared with 1070 seconds for conventional casting.
The new techniques are particularly good for making higher-value, specialist steels, says Claire Davis, a steel expert with the Warwick Manufacturing Group at the University of Warwick in Britain. Ms Davis and her team are developing new high-tech steels especially for belt casting, including advanced low-density steels that are stronger, lighter and more flexible than conventional steel.
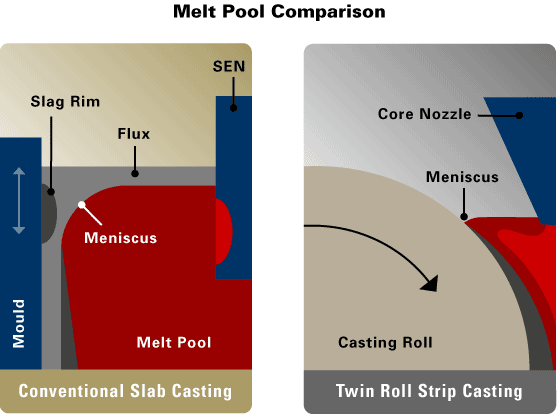
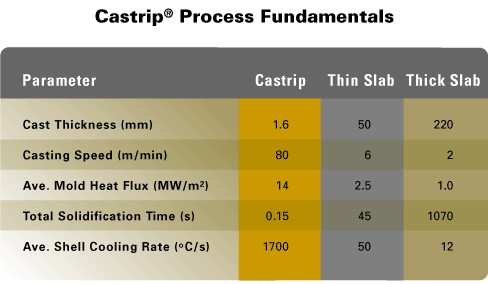
A twin-roll process, much as Bessemer conceived, is already employed by Nucor, a giant American steelmaker. Called Castrip, it is producing steel in two of its plants. A big advantage of twin-roll and belt-casting is compactness. Nucor reckons a Castrip plant needs only 20 hectares (50 acres) and provides a good investment return from the production of only 500,000 tonnes of steel a year. A conventional steel plant, by comparison, may sprawl over 2,000 hectares and need to produce some 4m tonnes a year to turn a profit.
Other firms are licensing Castrip as well. Shagang, a large Chinese steelmaker, is replacing a less energy-efficient plant with the new technology. The numbers look compelling enough to encourage a startup, too: Albion Steel is talking to investors about building a 300m ($370m) Castrip plant in Britain. The plant would be "fed" by a low-cost mini-mill that melts scrap and produces steel for galvanising, mostly for the construction industry, says Tony Pedder, one of Albion's founders. Mr Pedder is the chairman of Sheffield Forgemasters, an engineering company, and a former boss of British Steel (which later became Corus). Britain has a surplus of scrap but imports galvanised steel. The plant would employ only about 250 people; traditional integrated operations need a thousand or so. "We believe in the technology," says Mr Pedder. "In our view it is past the point of being experimental."
Read more